- お役立ち記事
- Enhancing Quality Management with Poka-Yoke (Foolproofing) in Manufacturing
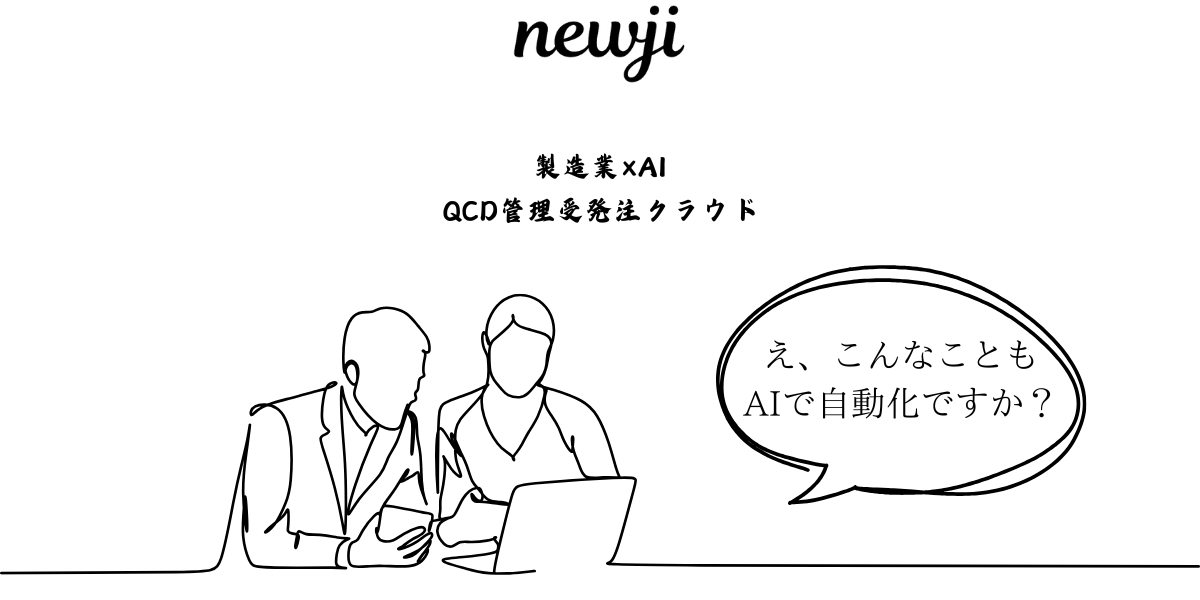
Enhancing Quality Management with Poka-Yoke (Foolproofing) in Manufacturing
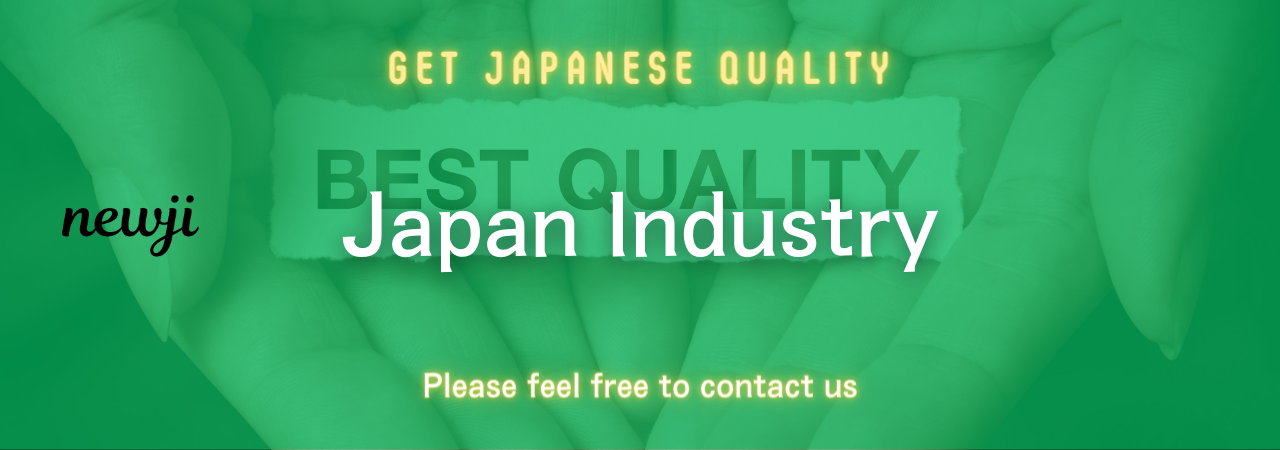
In the fast-paced world of manufacturing, ensuring top-notch product quality is non-negotiable.
One powerful method to achieve this is through Poka-Yoke, or foolproofing.
Originating from Japan, this methodology is designed to prevent errors by making it impossible for them to occur.
Let’s dive deeply into how Poka-Yoke can enhance quality management in manufacturing.
目次
What is Poka-Yoke?
Poka-Yoke, a Japanese term that translates to “mistake-proofing” or “inadvertent error prevention,” is a principle that was introduced by Dr. Shigeo Shingo in the 1960s.
The aim of Poka-Yoke is to eliminate defects by preventing, correcting, or highlighting human errors as they occur.
While mistakes are an inevitable part of any human-driven process, Poka-Yoke seeks to minimize their impact on product quality.
By designing systems and processes to catch errors as they happen, manufacturers can significantly reduce defects, thereby improving overall product quality.
The Importance of Poka-Yoke in Quality Management
In any production environment, maintaining consistent quality is crucial.
Even minor mistakes can lead to significant defects, resulting in substantial financial losses and reputational damage.
Here’s why implementing Poka-Yoke is essential for quality management:
Reducing Defects and Waste
One of the primary benefits of Poka-Yoke is that it helps reduce the number of defects and waste.
Mistake-proofing mechanisms prevent errors from occurring in the production process.
This leads to fewer defective products, which in turn reduces material waste and saves costs related to rework and scrap.
Enhancing Employee Morale and Productivity
When employees are constantly dealing with errors and rework, it can negatively impact their morale.
Poka-Yoke systems simplify tasks and processes, making it easier for employees to perform their duties without mistakes.
This boosts their confidence and productivity, leading to a more efficient and satisfied workforce.
Improving Customer Satisfaction
Consistently high-quality products are crucial for maintaining customer satisfaction and loyalty.
By preventing errors through Poka-Yoke, manufacturers can ensure their products meet the highest standards of quality.
This leads to happier customers and can provide a significant competitive advantage.
How to Implement Poka-Yoke in Manufacturing
Implementing Poka-Yoke effectively requires a strategic approach.
Here are some steps to follow:
Identify Common Errors
The first step is to identify common errors that occur during the manufacturing process.
This can be achieved by reviewing historical data, conducting root cause analysis, and seeking feedback from employees on the shop floor.
Analyze Processes
Once the common errors have been identified, analyze the processes where these errors occur.
Look for potential points of failure and brainstorm ways to modify the processes to prevent these errors from happening.
Design Poka-Yoke Mechanisms
Next, design Poka-Yoke mechanisms tailored to the specific errors identified.
These mechanisms can be physical changes to equipment or tools, modifications of standard operating procedures, or even simple alerts or warnings that notify workers when an error is about to occur.
Test and Implement
Before rolling out the Poka-Yoke mechanisms across the entire production line, test them on a small scale.
Evaluate their effectiveness and make adjustments as needed.
Once refined, implement the mechanisms throughout the production process.
Train Employees
Ensure that all employees are well-trained on the new Poka-Yoke mechanisms.
Educate them on how these mechanisms work and their role in maintaining high product quality.
Encourage workers to provide feedback for continuous improvement.
Monitor and Improve
Even after successful implementation, continuous monitoring is crucial.
Keep an eye on the performance of Poka-Yoke mechanisms and make ongoing improvements as necessary.
Regularly review error rates and adjust strategies to ensure optimal performance.
Examples of Poka-Yoke in Action
To better understand how Poka-Yoke can be practically applied, let’s look at a few real-world examples:
Color-Coded Assembly
In electronics manufacturing, components are color-coded to ensure they are placed in the correct locations on a circuit board.
Different colors correspond to different sections of the board, making it easy for workers to identify where each component belongs.
This simple visual cue prevents assembly errors and ensures proper placement.
Go / No-Go Gauges
Go / No-Go gauges are a common Poka-Yoke tool used in various manufacturing industries.
These gauges have two test endpoints: one that allows the part to fit (Go) and one that does not (No-Go).
If a component fits in the Go side but not in the No-Go side, it meets the required specifications.
If the component fails either test, it is rejected, ensuring only correctly sized parts proceed.
Assembly Jigs
Assembly jigs are custom tools designed to hold and align parts during the assembly process.
They ensure that parts are positioned correctly, and can even prevent the next step of the process from occurring if parts are misaligned.
This prevents assembly errors and enhances overall product quality.
The Future of Poka-Yoke in Manufacturing
As manufacturing continues to evolve with new technologies and methodologies, Poka-Yoke will remain a fundamental principle for ensuring product quality.
Integrating Poka-Yoke with advanced technologies such as automation, artificial intelligence (AI), and the Internet of Things (IoT) can take mistake-proofing to the next level.
For instance, AI-powered cameras and sensors can detect errors in real-time and automatically halt the production process or provide instant feedback to workers.
IoT devices can monitor equipment performance and alert operators to potential issues before they become problematic.
By leveraging these advanced technologies, manufacturers can create more robust Poka-Yoke systems, further reducing error rates and enhancing product quality.
In conclusion, Poka-Yoke is an invaluable tool in the quest for superior quality management in manufacturing.
By preventing errors before they occur or catching them immediately, manufacturers can significantly reduce defects, improve efficiency, boost employee morale, and enhance customer satisfaction.
As the industry continues to innovate, integrating Poka-Yoke with cutting-edge technologies will ensure that product quality remains uncompromised.
資料ダウンロード
QCD調達購買管理クラウド「newji」は、調達購買部門で必要なQCD管理全てを備えた、現場特化型兼クラウド型の今世紀最高の購買管理システムとなります。
ユーザー登録
調達購買業務の効率化だけでなく、システムを導入することで、コスト削減や製品・資材のステータス可視化のほか、属人化していた購買情報の共有化による内部不正防止や統制にも役立ちます。
NEWJI DX
製造業に特化したデジタルトランスフォーメーション(DX)の実現を目指す請負開発型のコンサルティングサービスです。AI、iPaaS、および先端の技術を駆使して、製造プロセスの効率化、業務効率化、チームワーク強化、コスト削減、品質向上を実現します。このサービスは、製造業の課題を深く理解し、それに対する最適なデジタルソリューションを提供することで、企業が持続的な成長とイノベーションを達成できるようサポートします。
オンライン講座
製造業、主に購買・調達部門にお勤めの方々に向けた情報を配信しております。
新任の方やベテランの方、管理職を対象とした幅広いコンテンツをご用意しております。
お問い合わせ
コストダウンが利益に直結する術だと理解していても、なかなか前に進めることができない状況。そんな時は、newjiのコストダウン自動化機能で大きく利益貢献しよう!
(Β版非公開)