- お役立ち記事
- Challenges and Solutions for SMEs in Lathe Processing
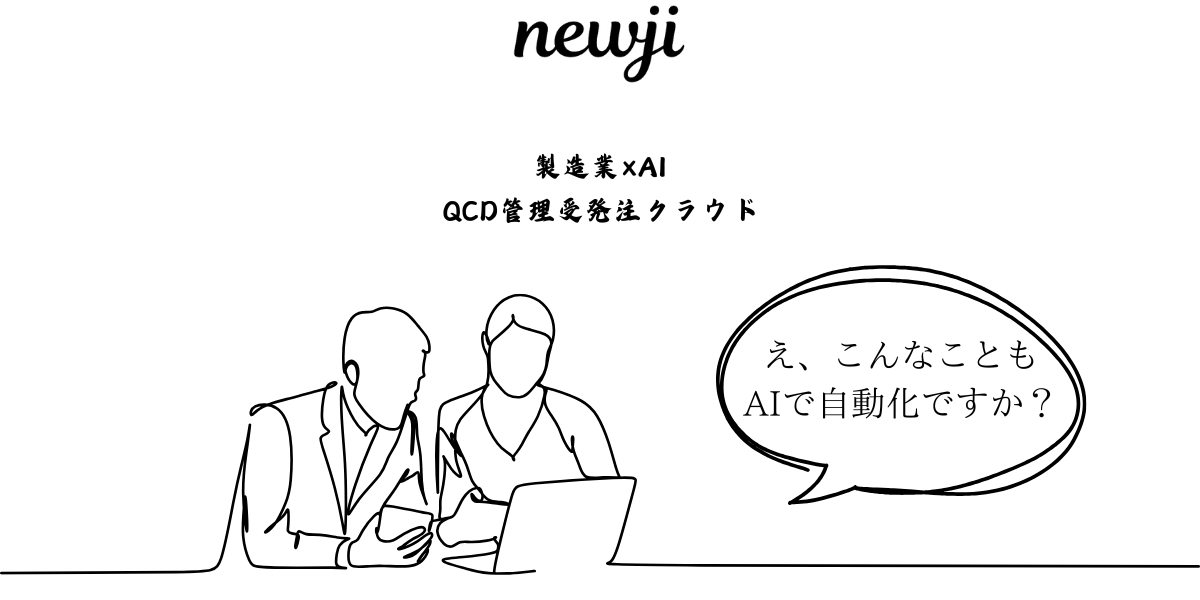
Challenges and Solutions for SMEs in Lathe Processing
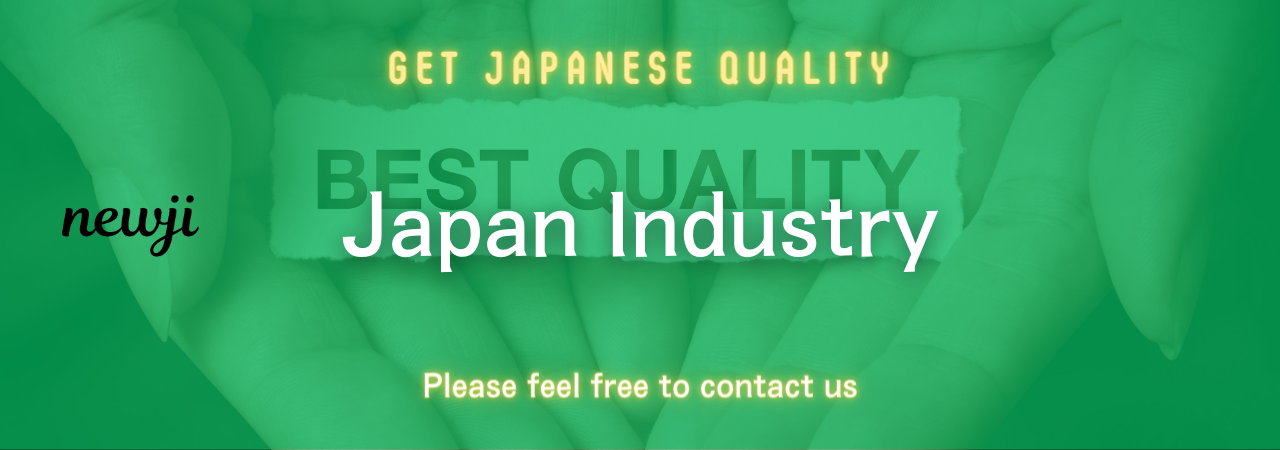
In today’s competitive manufacturing landscape, small and medium-sized enterprises (SMEs) face numerous challenges, especially in the field of lathe processing.
Lathe processing is essential for producing various cylindrical parts used in machinery, automotive industries, and many other sectors.
However, the path to mastering this technique for SMEs can be riddled with obstacles.
This article explores some common challenges SMEs encounter in lathe processing and offers viable solutions to overcome them.
目次
Understanding Lathe Processing
Lathe processing is a machining process involving the rotation of workpieces along their axes to execute operations like cutting, sanding, drilling, and turning.
Although it is a fundamental technique in manufacturing, the complexity and precision required can pose significant difficulties, especially for smaller enterprises.
Understanding these intricacies is the first step towards tackling the issues head-on.
Common Challenges Faced by SMEs in Lathe Processing
Lack of Skilled Labor
One of the most pressing challenges is the shortage of skilled labor.
Lathe operations demand highly skilled operators who can handle complex machinery and produce precise components.
Small enterprises often struggle to attract and retain such talent due to competition from larger firms offering better pay packages and benefits.
High Initial Investment
Setting up a comprehensive lathe processing unit involves a substantial financial outlay.
Advanced, computer-numerical-control (CNC) lathes, tooling, and auxiliary equipment can be prohibitively expensive for SMEs.
This high initial investment can be a significant barrier to entry or expansion in this sector.
Maintenance and Downtime
Machinery maintenance is a crucial but often overlooked aspect of lathe processing.
Unexpected breakdowns and the need for regular upkeep can lead to significant downtime.
For SMEs operating on tight schedules and limited budgets, downtime can disrupt workflow and result in missed deadlines and lost revenue.
Quality Control and Consistency
Maintaining high levels of quality control is another hurdle.
The precision required in lathe processing means that even slight deviations can lead to faulty components.
Ensuring consistent quality across batches is challenging, particularly when dealing with intricate parts and varying material types.
Supply Chain Issues
The efficiency of lathe processing is also heavily dependent on the availability and quality of raw materials.
SMEs often experience delays and fluctuations in the supply chain, which can hamper production schedules.
Such inconsistencies can lead to subpar finished products and customer dissatisfaction.
Solutions to Overcome Challenges in Lathe Processing
Investing in Training and Development
One of the most effective ways to address the skills shortage is through investment in training and development.
SMEs can sponsor vocational training programs or collaborate with educational institutions to create a pipeline of skilled labor.
Regular workshops and in-house training sessions can also help existing employees upgrade their skills.
Leveraging Financial Support
To tackle the challenge of high initial investments, SMEs can explore various financial avenues.
Government grants, subsidies, and low-interest loans can significantly ease the financial burden.
Additionally, leasing machinery instead of outright purchasing can provide a more manageable option for small-scale enterprises.
Implementing Preventive Maintenance
Preventive maintenance can minimize downtime and extend the lifespan of machinery.
SMEs should develop a robust maintenance schedule, including frequent inspections and timely replacements of worn-out parts.
Predictive maintenance technologies, such as IoT-enabled sensors, can also help monitor equipment health in real-time, ensuring timely interventions.
Enhancing Quality Control Measures
Strict quality control protocols are essential for maintaining consistency.
Implementing statistical process control (SPC) and using precision measuring instruments can help identify deviations early in the production process.
Automated Inspection systems can further ensure that each component meets the required specifications.
Streamlining the Supply Chain
Building strong relationships with reliable suppliers is key to a smooth supply chain.
SMEs should diversify their supplier base to mitigate risks associated with single-source dependency.
Adopting Just-in-Time (JIT) inventory practices can also help in minimizing waste and ensuring that materials are available when needed, without holding excessive stock.
Future Trends in Lathe Processing for SMEs
Adoption of Automation and Robotics
Automation is set to revolutionize lathe processing, making it more efficient and less dependent on human labor.
Robotic arms and automated feeding systems can handle repetitive tasks, freeing up human operators to focus on more complex aspects.
SMEs adopting these technologies can boost productivity and achieve more consistent output.
Use of Advanced Materials
The shift towards advanced materials like composites and high-strength alloys is another trend shaping lathe processing.
These materials offer superior properties but require specialized machining techniques.
SMEs that invest in the necessary tooling and training can tap into new market segments and enhance their product offerings.
Implementation of Smart Manufacturing
The integration of IoT and AI in manufacturing processes is paving the way for smart factories.
In lathe processing, this could mean real-time monitoring of machine performance, predictive maintenance, and enhanced production analytics.
These technologies can optimize workflow, reduce downtime, and improve overall efficiency.
Conclusion
While SMEs face several challenges in lathe processing, a proactive approach can mitigate many of these issues.
Investing in skills development, leveraging financial support, implementing preventive maintenance, and adopting advanced technologies are all viable strategies.
By addressing these challenges systematically, SMEs can enhance their capabilities, improve quality, and remain competitive in the ever-evolving manufacturing landscape.
資料ダウンロード
QCD調達購買管理クラウド「newji」は、調達購買部門で必要なQCD管理全てを備えた、現場特化型兼クラウド型の今世紀最高の購買管理システムとなります。
ユーザー登録
調達購買業務の効率化だけでなく、システムを導入することで、コスト削減や製品・資材のステータス可視化のほか、属人化していた購買情報の共有化による内部不正防止や統制にも役立ちます。
NEWJI DX
製造業に特化したデジタルトランスフォーメーション(DX)の実現を目指す請負開発型のコンサルティングサービスです。AI、iPaaS、および先端の技術を駆使して、製造プロセスの効率化、業務効率化、チームワーク強化、コスト削減、品質向上を実現します。このサービスは、製造業の課題を深く理解し、それに対する最適なデジタルソリューションを提供することで、企業が持続的な成長とイノベーションを達成できるようサポートします。
オンライン講座
製造業、主に購買・調達部門にお勤めの方々に向けた情報を配信しております。
新任の方やベテランの方、管理職を対象とした幅広いコンテンツをご用意しております。
お問い合わせ
コストダウンが利益に直結する術だと理解していても、なかなか前に進めることができない状況。そんな時は、newjiのコストダウン自動化機能で大きく利益貢献しよう!
(Β版非公開)