- お役立ち記事
- Manual Utilization Techniques to Solve Leadership Shortages and Build Talent Development Systems in Manufacturing Sites
Manual Utilization Techniques to Solve Leadership Shortages and Build Talent Development Systems in Manufacturing Sites
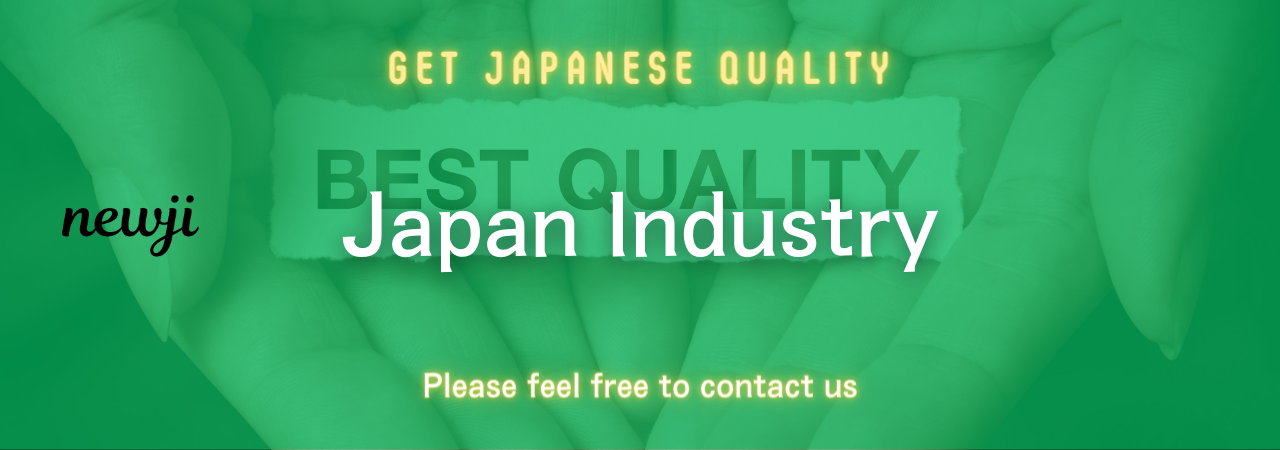
Leadership shortages in manufacturing sites can lead to significant disruptions, hindering productivity and growth.
To address this, it’s essential to cultivate robust talent development systems that can nurture future leaders.
This article delves into manual utilization techniques to solve these challenges effectively.
目次
Understanding the Leadership Shortage
Leadership shortages in manufacturing sites are often a result of an aging workforce.
Many experienced leaders are nearing retirement, leaving a gap that is difficult to fill.
Additionally, the industry is changing rapidly, requiring leaders to possess new skills and adapt quickly.
Understanding these underlying causes is the first step in addressing the shortage.
The Importance of Talent Development
Talent development ensures a steady stream of skilled individuals who can step into leadership roles as needed.
Manufacturing sites require leaders not only with technical expertise but also with strong managerial and interpersonal skills.
By investing in talent development, organizations can build a pipeline of capable leaders ready to tackle future challenges.
Implementing Manual Utilization Techniques
1. Identifying Skill Gaps
The first step in utilizing manual techniques is to identify skill gaps within the current workforce.
This can be accomplished through regular assessments and performance reviews.
By understanding where deficits exist, targeted training programs can be developed to address these needs directly.
2. On-the-Job Training
On-the-job training is a crucial manual technique for developing leaders.
This hands-on approach allows potential leaders to learn in a real-world environment.
Implementing mentorship programs where experienced leaders guide less experienced employees can be highly effective.
3. Cross-Training
Cross-training involves teaching employees how to perform tasks outside their usual responsibilities.
This not only broadens their skill set but also prepares them for leadership roles.
Cross-training can expose employees to different aspects of manufacturing, making them more versatile and capable leaders.
4. Developing Soft Skills
Technical skills are essential, but soft skills such as communication, problem-solving, and team management are just as crucial.
Workshops and seminars focused on these skills can help prepare potential leaders.
Role-playing and scenario-based training can be particularly beneficial in developing these competencies.
5. Setting Clear Goals
Clear, achievable goals are essential for effective talent development.
Setting specific objectives for potential leaders provides direction and motivation.
Regularly reviewing progress toward these goals can help ensure that development remains on track.
Building a Supportive Environment
Creating a supportive environment is vital for effective talent development.
Encouraging open communication and providing regular feedback can help employees feel valued and motivated.
Additionally, recognizing and rewarding progress can boost morale and commitment to development efforts.
The Role of Advanced Technologies
While manual techniques are crucial, integrating advanced technologies can further enhance talent development.
For example, e-learning platforms can provide flexible learning opportunities.
Simulation software can offer realistic practice scenarios, and data analytics can track progress and identify areas for improvement.
1. E-Learning Platforms
E-learning platforms offer a range of courses and resources accessible at any time.
This flexibility allows employees to learn at their own pace, complementing on-the-job training and other manual techniques.
2. Simulation Software
Simulation software can create realistic practice scenarios where employees can apply their skills.
This technology can be particularly beneficial for training in complex or high-risk tasks, providing a safe environment for learning and experimentation.
3. Data Analytics
Data analytics can track employee progress and highlight areas needing improvement.
By analyzing this data, organizations can refine their training programs to better suit the needs of their workforce.
Success Stories in Manufacturing
Numerous manufacturing sites have successfully implemented manual utilization techniques to overcome leadership shortages.
For instance, a leading automotive manufacturer created a comprehensive mentorship program, pairing each new employee with a seasoned mentor.
This initiative not only addressed skill gaps but also fostered a supportive workplace culture.
Another success story comes from an electronics manufacturer that introduced cross-training programs.
By encouraging employees to learn tasks outside their usual roles, they not only built a versatile workforce but also prepared employees for leadership positions.
Conclusion
Addressing leadership shortages in manufacturing requires a multifaceted approach.
By utilizing manual techniques such as on-the-job training, cross-training, and soft skill development, organizations can build a robust talent development system.
Creating a supportive environment and integrating advanced technologies further enhances these efforts.
Through strategic planning and continued investment in talent development, manufacturing sites can ensure they have the leaders needed to drive future success.
資料ダウンロード
QCD調達購買管理クラウド「newji」は、調達購買部門で必要なQCD管理全てを備えた、現場特化型兼クラウド型の今世紀最高の購買管理システムとなります。
ユーザー登録
調達購買業務の効率化だけでなく、システムを導入することで、コスト削減や製品・資材のステータス可視化のほか、属人化していた購買情報の共有化による内部不正防止や統制にも役立ちます。
NEWJI DX
製造業に特化したデジタルトランスフォーメーション(DX)の実現を目指す請負開発型のコンサルティングサービスです。AI、iPaaS、および先端の技術を駆使して、製造プロセスの効率化、業務効率化、チームワーク強化、コスト削減、品質向上を実現します。このサービスは、製造業の課題を深く理解し、それに対する最適なデジタルソリューションを提供することで、企業が持続的な成長とイノベーションを達成できるようサポートします。
オンライン講座
製造業、主に購買・調達部門にお勤めの方々に向けた情報を配信しております。
新任の方やベテランの方、管理職を対象とした幅広いコンテンツをご用意しております。
お問い合わせ
コストダウンが利益に直結する術だと理解していても、なかなか前に進めることができない状況。そんな時は、newjiのコストダウン自動化機能で大きく利益貢献しよう!
(Β版非公開)