- お役立ち記事
- Tips for Selecting Blank Processing Suppliers According to Major
Tips for Selecting Blank Processing Suppliers According to Major
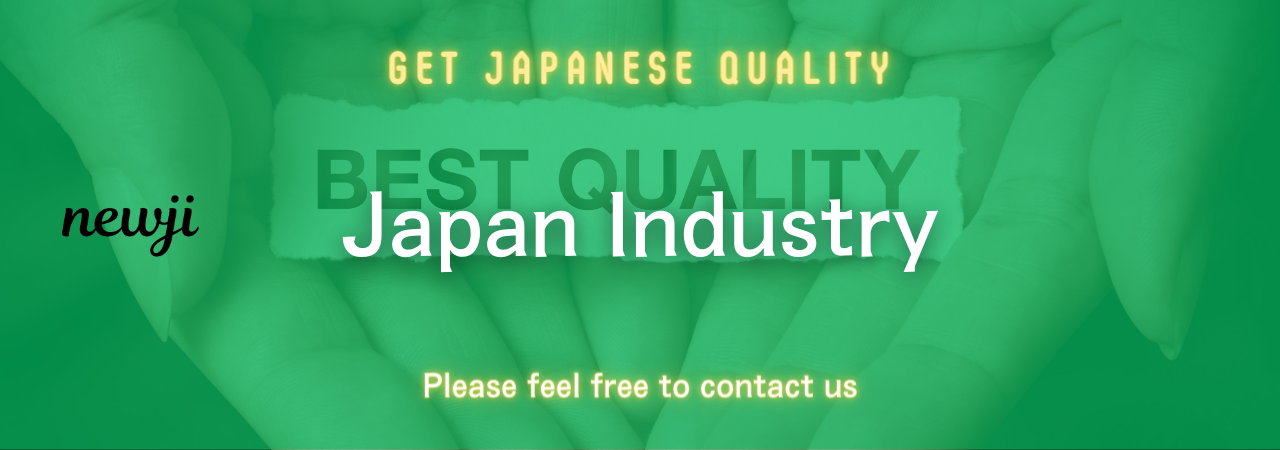
Choosing the right blank processing supplier is crucial for businesses across various industries.
Whether you are in aerospace, automotive, construction, or another sector, selecting a supplier who can meet your specific requirements is vital for ensuring quality, efficiency, and cost-effectiveness.
In this article, we will offer practical tips on how to choose the most suitable blank processing suppliers according to your major industry.
This will help you make informed decisions that align with your business needs.
目次
Understand Your Industry-Specific Needs
The first step in selecting a blank processing supplier is understanding your industry’s specific needs.
Each industry has its own set of standards, specifications, and requirements that must be met.
For example, the aerospace industry often demands high precision and strict adherence to international standards, while the automotive industry may prioritize quick turnaround times and cost efficiency.
Understanding these needs helps in narrowing down potential suppliers who specialize in your industry.
Define the Specifications
To ensure that you select the right supplier, start by defining the specifications of the blank parts you require.
This includes details like dimensions, tolerances, material types, and surface finishes.
Providing detailed specifications upfront can help suppliers offer more accurate quotes and lead to a smoother production process.
Compliance and Certifications
Ensure that the supplier has the necessary certifications and complies with industry standards.
For instance, suppliers catering to the aerospace industry should have AS9100 certification, while those in the automotive sector should be certified with IATF 16949.
Compliance with these standards ensures that the supplier can meet your quality and regulatory requirements.
Evaluate Supplier Capabilities
Once you understand your specific needs, the next step is to evaluate the capabilities of potential suppliers.
This involves assessing their technical skills, machinery, workforce, and general capacity to meet your demands.
Technical Expertise and Machinery
The supplier you choose should have the necessary technical expertise and equipment required for blank processing in your industry.
For instance, precision machining and advanced CNC machines might be essential in the aerospace sector, whereas large-scale stamping presses could be crucial for automotive applications.
Make sure the supplier’s machinery is up-to-date and capable of producing parts to your required specifications.
Workforce Skills
It’s important to consider the skills and experience of the supplier’s workforce.
A skilled workforce can significantly impact the quality and efficiency of the blank processing.
Inquire about the training programs that the supplier offers its staff and their experience working with companies in your industry.
Production Capacity
Assess the supplier’s production capacity to ensure they can handle your order volume.
Whether you need a small batch or a large-scale production run, the supplier should be able to accommodate your needs without compromising on quality or deadlines.
Assess Quality Control Procedures
Quality control is a critical aspect of blank processing.
Ensure that the supplier has robust quality control procedures in place to maintain high standards throughout the production process.
Inspection Methods
Inquire about the methods the supplier uses for inspecting blank parts.
They should employ rigorous inspection techniques, such as dimensional checks, surface finish inspections, and material testing, to ensure parts meet your specifications.
Record Keeping and Traceability
Good suppliers maintain detailed records of their production processes.
This includes traceability of materials and components used in the manufacturing of blank parts.
Having a traceability system in place ensures that any issues can be quickly identified and resolved, minimizing disruptions to your supply chain.
Continuous Improvement
Look for suppliers who are committed to continuous improvement.
They should have processes in place to regularly evaluate and enhance their production methods, machinery, and workforce skills.
This commitment to improvement reflects a proactive approach to maintaining high-quality standards.
Consider Cost and Timeliness
Cost and timeliness are key factors in any supply chain decision.
Evaluate the supplier’s pricing and lead times to ensure they align with your business requirements.
Competitive Pricing
While cost should not be the sole factor in your decision, it is important to find a supplier who offers competitive pricing.
Request detailed quotes from potential suppliers and compare them.
Be wary of quotes that are significantly lower than others, as this may indicate a compromise on quality.
Lead Times
Reliable lead times are crucial for ensuring that your production schedule stays on track.
Inquire about the supplier’s typical lead times and their ability to meet urgent orders if necessary.
Consider their location as well, as shipping times can affect overall lead time.
Flexibility
A flexible supplier who can adapt to changes in your order volume or specifications is invaluable.
Assess their ability to scale production up or down and accommodate any last-minute changes.
Check Reviews and References
Before making a final decision, it’s advisable to check reviews and references from other businesses in your industry.
This can provide valuable insights into the supplier’s reliability, quality, and customer service.
Customer Reviews
Look for customer reviews online to gauge the supplier’s reputation.
Platforms like Google Reviews, industry forums, and social media can offer candid feedback from other businesses that have worked with the supplier.
Request References
Ask the supplier to provide references from clients in your industry.
Speaking directly with these references can give you a better idea of the supplier’s performance and reliability.
Final Thoughts
Selecting the right blank processing supplier according to your major industry involves a comprehensive evaluation of your specific needs, supplier capabilities, quality control procedures, cost, timeliness, and customer feedback.
By taking these factors into account, you can make an informed decision that aligns with your business objectives, ensuring that you receive high-quality parts on time and within budget.
This careful selection process ultimately contributes to the success and efficiency of your operations.
資料ダウンロード
QCD調達購買管理クラウド「newji」は、調達購買部門で必要なQCD管理全てを備えた、現場特化型兼クラウド型の今世紀最高の購買管理システムとなります。
ユーザー登録
調達購買業務の効率化だけでなく、システムを導入することで、コスト削減や製品・資材のステータス可視化のほか、属人化していた購買情報の共有化による内部不正防止や統制にも役立ちます。
NEWJI DX
製造業に特化したデジタルトランスフォーメーション(DX)の実現を目指す請負開発型のコンサルティングサービスです。AI、iPaaS、および先端の技術を駆使して、製造プロセスの効率化、業務効率化、チームワーク強化、コスト削減、品質向上を実現します。このサービスは、製造業の課題を深く理解し、それに対する最適なデジタルソリューションを提供することで、企業が持続的な成長とイノベーションを達成できるようサポートします。
オンライン講座
製造業、主に購買・調達部門にお勤めの方々に向けた情報を配信しております。
新任の方やベテランの方、管理職を対象とした幅広いコンテンツをご用意しております。
お問い合わせ
コストダウンが利益に直結する術だと理解していても、なかなか前に進めることができない状況。そんな時は、newjiのコストダウン自動化機能で大きく利益貢献しよう!
(Β版非公開)