- お役立ち記事
- Improving Energy Efficiency Through Drive Unit Optimization in Extrusion Molding
Improving Energy Efficiency Through Drive Unit Optimization in Extrusion Molding
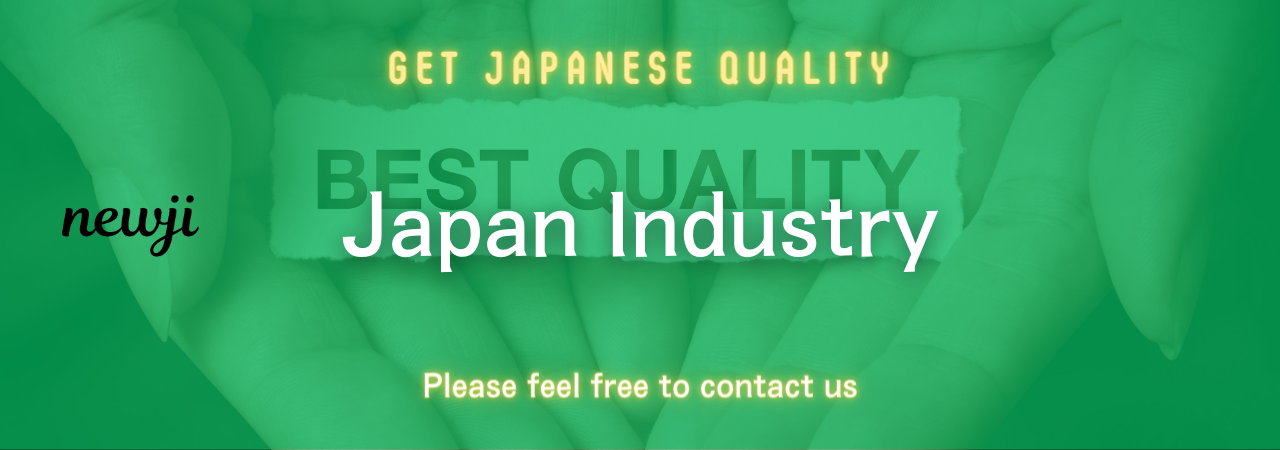
Extrusion molding is a process used to create objects of a fixed cross-sectional profile.
In this process, material is melted and pushed through a die to form the desired shape.
This method is common in industries such as automotive, construction, and packaging.
While extrusion molding is effective, it is often energy-intensive.
Optimizing the drive unit, which powers the extrusion process, can significantly improve energy efficiency.
目次
Understanding Extrusion Molding
Extrusion molding involves several critical components.
A hopper feeds raw material into the extruder.
The material is then melted in a heated barrel.
A screw or plunger pushes the molten material through a die to form the desired shape.
The final product is cooled and cut to length.
Extrusion molding is highly versatile.
It can process a variety of materials, including plastics, metals, and ceramics.
However, the process requires substantial energy to melt the material and maintain the required pressure.
This is where drive unit optimization becomes crucial.
The Role of the Drive Unit
The drive unit is the heart of the extrusion molding process.
It converts electrical energy into mechanical motion to drive the screw or plunger.
Common types of drive units include hydraulic, mechanical, and electric drives.
Each type has its pros and cons, but electric drives are increasingly popular due to their energy efficiency.
Electric drive units are known for their precise control and high efficiency.
They can adjust speed and torque to match the requirements of the extrusion process.
This adaptability makes them ideal for optimizing energy consumption.
Benefits of Drive Unit Optimization
Optimizing the drive unit can offer several benefits:
Energy Savings
Improving the efficiency of the drive unit can lead to significant energy savings.
An optimized drive unit reduces the power needed for the extrusion process.
This can lower operational costs and minimize the environmental impact.
Increased Productivity
A more efficient drive unit can enhance the overall productivity of the extrusion molding process.
By ensuring the drive unit operates at optimal conditions, the entire system can run more smoothly and consistently.
This can lead to higher output rates and better product quality.
Reduced Maintenance Costs
Optimized drive units often experience less wear and tear.
They operate more smoothly and efficiently, reducing the likelihood of mechanical failures.
This can decrease maintenance costs and reduce downtime.
Improved Control and Precision
Modern electric drive units provide precise control over the extrusion process.
This control can result in better-quality products with fewer defects.
Precise control also allows for the processing of a wider range of materials and more complex shapes.
Steps to Optimize Drive Units
Conduct an Energy Audit
The first step in optimizing drive units is to conduct an energy audit.
This involves measuring the current energy consumption and identifying areas for improvement.
An energy audit can reveal inefficiencies and highlight opportunities for optimization.
Upgrade to Energy-Efficient Drive Units
One of the most effective ways to optimize energy efficiency is to upgrade to modern, energy-efficient drive units.
Electric drives, in particular, can offer substantial energy savings compared to older technology.
These units are designed to provide high efficiency and precise control.
Implement Advanced Control Systems
Advanced control systems can enhance the performance of drive units.
Variable frequency drives (VFDs) allow for precise control of motor speed and torque.
This can optimize the performance of the extrusion process and reduce energy consumption.
Integrating programmable logic controllers (PLCs) can further enhance control and efficiency.
Regular Maintenance and Monitoring
Regular maintenance is crucial for keeping drive units in optimal condition.
This includes checking for wear and tear, lubricating moving parts, and replacing worn components.
Monitoring the performance of drive units can also help identify issues early and prevent costly downtime.
Case Studies: Successful Drive Unit Optimization
Several companies have successfully optimized their drive units and realized significant benefits.
Case Study 1: The Automotive Industry
A leading automotive manufacturer upgraded their hydraulic drive units to modern electric drives.
This change resulted in a 30% reduction in energy consumption.
The company also reported improved product quality and reduced maintenance costs.
Case Study 2: The Packaging Industry
A packaging company implemented VFDs and advanced control systems in their extrusion molding process.
This optimization led to a 25% increase in productivity and a 20% reduction in energy use.
The company also experienced fewer production stoppages and improved product consistency.
Future Trends in Drive Unit Optimization
The future of drive unit optimization looks promising.
Technological advancements are continuously improving the efficiency and performance of drive units.
Smart Drive Units
Smart drive units equipped with sensors and connectivity features are becoming more common.
These units can monitor their own performance and provide real-time data for optimization.
This can lead to more proactive maintenance and further energy savings.
Integration with IoT and AI
The integration of the Internet of Things (IoT) and Artificial Intelligence (AI) is set to revolutionize drive unit optimization.
IoT devices can collect vast amounts of data from drive units.
AI can analyze this data and provide actionable insights for further optimization.
Conclusion
Optimizing the drive units in extrusion molding processes is a powerful way to improve energy efficiency.
By conducting energy audits, upgrading to energy-efficient drives, and implementing advanced control systems, companies can realize significant energy savings.
Regular maintenance and monitoring are also essential for maintaining optimal performance.
As technology continues to advance, the opportunities for drive unit optimization will only grow, leading to even greater efficiencies and cost savings.
資料ダウンロード
QCD調達購買管理クラウド「newji」は、調達購買部門で必要なQCD管理全てを備えた、現場特化型兼クラウド型の今世紀最高の購買管理システムとなります。
ユーザー登録
調達購買業務の効率化だけでなく、システムを導入することで、コスト削減や製品・資材のステータス可視化のほか、属人化していた購買情報の共有化による内部不正防止や統制にも役立ちます。
NEWJI DX
製造業に特化したデジタルトランスフォーメーション(DX)の実現を目指す請負開発型のコンサルティングサービスです。AI、iPaaS、および先端の技術を駆使して、製造プロセスの効率化、業務効率化、チームワーク強化、コスト削減、品質向上を実現します。このサービスは、製造業の課題を深く理解し、それに対する最適なデジタルソリューションを提供することで、企業が持続的な成長とイノベーションを達成できるようサポートします。
オンライン講座
製造業、主に購買・調達部門にお勤めの方々に向けた情報を配信しております。
新任の方やベテランの方、管理職を対象とした幅広いコンテンツをご用意しております。
お問い合わせ
コストダウンが利益に直結する術だと理解していても、なかなか前に進めることができない状況。そんな時は、newjiのコストダウン自動化機能で大きく利益貢献しよう!
(Β版非公開)