- お役立ち記事
- Detailed Planning Techniques for Capital Investment and Financial Planning in Manufacturing
Detailed Planning Techniques for Capital Investment and Financial Planning in Manufacturing
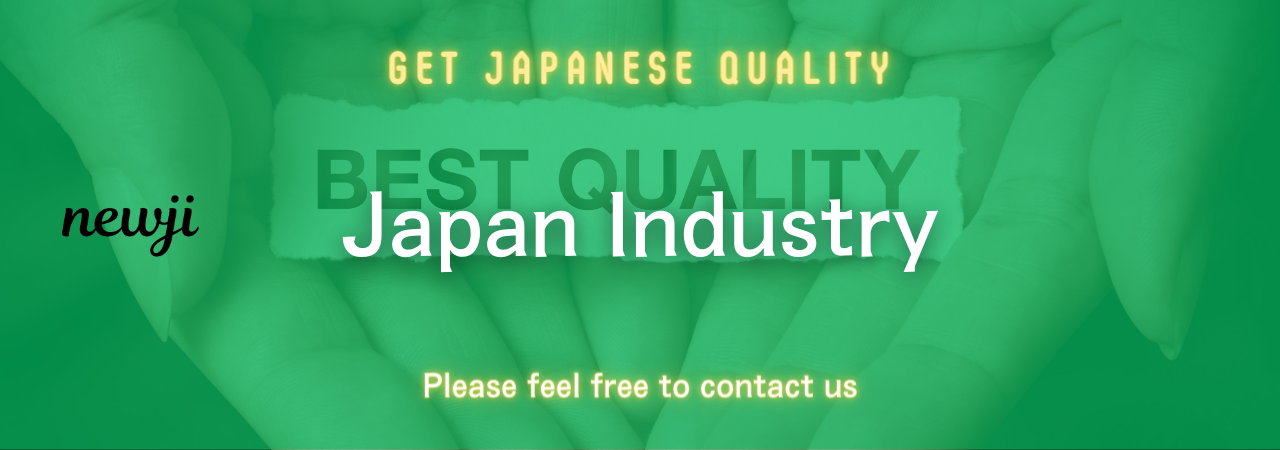
Capital investment and financial planning are crucial for the smooth running of any manufacturing operation.
The above two terms might seem overwhelming at first, but with a well-structured plan, they can be easily managed.
Let’s dive deep into these concepts and explore planning techniques that can significantly benefit your manufacturing business.
目次
Understanding Capital Investment
Capital investment refers to the funds that a manufacturing company allocates to purchase, improve, and maintain physical assets.
These assets can include machinery, buildings, technology, and other long-term resources critical for production.
The Importance of Capital Investment in Manufacturing
Capital investment is vital for manufacturing businesses aiming to enhance production efficiency, upgrade technology, and boost long-term profitability.
Proper investment decisions ensure that the company remains competitive, meets market demands, and can scale operations effectively.
A well-planned capital investment strategy can also reduce operational risks and improve financial stability.
Types of Capital Investments
1. **Equipment and Machinery:** Upgrading to advanced machinery enhances production speed and product quality.
2. **Building and Infrastructure:** Investing in new facilities or upgrading existing ones ensures optimal operational environment.
3. **Technology:** Implementing cutting-edge software and systems can streamline operations and reduce wastage.
Steps to Plan Capital Investments
Identify Business Needs and Goals
The first step in capital investment planning is to identify the needs of the business.
Clearly defining business goals helps in determining the type of investments required.
Do you need new machinery, a larger facility, or advanced software systems?
Understanding your long-term objectives is crucial.
Conduct a Financial Analysis
A thorough financial analysis helps in understanding the current financial position of the company and its capacity to invest.
Evaluate cash flow, existing debts, and profit margins.
This analysis aids in deciding the amount that can be safely allocated for new investments without straining the company’s finances.
Research and Make Informed Decisions
Research the market and consult industry experts before making any investment.
Compare different options, understand the potential return on investment (ROI), and assess risks.
Informed decisions can prevent overspending and ensure the best use of available resources.
Prepare a Detailed Plan and Budget
Create a detailed plan outlining the investment strategy, timelines, and expected outcomes.
A well-defined budget should also be included, highlighting the cost of each investment and potential financial returns.
This plan acts as a roadmap for the investment process.
Monitor and Evaluate
After the investment has been made, continuously monitor the performance and evaluate the results.
Comparing actual outcomes with expected outcomes helps in understanding the effectiveness of the investment and making necessary adjustments.
Understanding Financial Planning
Financial planning involves managing the company’s finances to achieve its business goals.
For manufacturing companies, financial planning ensures that funds are effectively allocated and managed to support operations and investments.
The Importance of Financial Planning in Manufacturing
Effective financial planning helps in maintaining cash flow, managing debts, and ensuring sufficient funds for operations and future investments.
It enables companies to plan for uncertainties, such as economic downturns or unexpected costs, thereby reducing financial risks.
Financial planning also provides insights into profitability, helping in making informed strategic decisions.
Key Components of Financial Planning
1. **Budgeting:** Creating a detailed budget helps in managing income and expenses.
2. **Forecasting:** Predicting future financial conditions based on current data aids in proactive planning.
3. **Financial Analysis:** Regular analysis of financial statements to understand the company’s financial health.
4. **Risk Management:** Identifying potential financial risks and creating strategies to mitigate them.
Steps to Develop an Effective Financial Plan
Set Financial Goals
The first step is to set clear and realistic financial goals that align with the company’s overall business objectives.
Whether it’s revenue growth, cost reduction, or capital preservation, having defined goals provides a direction for financial planning.
Analyze Current Financial Position
Understanding the current financial state of the business is crucial.
Review balance sheets, income statements, and cash flow statements to get a clear picture of where the company stands financially.
Identify strengths, weaknesses, opportunities, and threats.
Create a Budget
Develop a comprehensive budget that outlines expected income and expenses.
Consider both short-term and long-term financial needs.
A well-planned budget acts as a financial guide and helps in controlling costs.
Develop Financial Strategies
Formulate strategies to achieve financial goals.
This can include cost-cutting measures, revenue enhancement techniques, and efficient capital allocation.
Ensure that the strategies are flexible enough to adapt to changing market conditions.
Implement and Monitor
Once the financial plan is in place, implement the strategies and continuously monitor the results.
Regularly reviewing financial performance helps in identifying any deviations from the plan and making necessary adjustments.
Review and Adjust
The financial environment is dynamic, and so should be the financial plan.
Regularly reviewing and adjusting the plan based on current financial performance and market conditions is essential for staying on track to achieve financial goals.
Capital investment and financial planning are integral aspects of a successful manufacturing business.
By understanding their importance and following a structured approach, businesses can ensure sustainable growth and financial stability.
Careful planning, continuous monitoring, and timely adjustments are key to effectively managing these critical areas.
資料ダウンロード
QCD調達購買管理クラウド「newji」は、調達購買部門で必要なQCD管理全てを備えた、現場特化型兼クラウド型の今世紀最高の購買管理システムとなります。
ユーザー登録
調達購買業務の効率化だけでなく、システムを導入することで、コスト削減や製品・資材のステータス可視化のほか、属人化していた購買情報の共有化による内部不正防止や統制にも役立ちます。
NEWJI DX
製造業に特化したデジタルトランスフォーメーション(DX)の実現を目指す請負開発型のコンサルティングサービスです。AI、iPaaS、および先端の技術を駆使して、製造プロセスの効率化、業務効率化、チームワーク強化、コスト削減、品質向上を実現します。このサービスは、製造業の課題を深く理解し、それに対する最適なデジタルソリューションを提供することで、企業が持続的な成長とイノベーションを達成できるようサポートします。
オンライン講座
製造業、主に購買・調達部門にお勤めの方々に向けた情報を配信しております。
新任の方やベテランの方、管理職を対象とした幅広いコンテンツをご用意しております。
お問い合わせ
コストダウンが利益に直結する術だと理解していても、なかなか前に進めることができない状況。そんな時は、newjiのコストダウン自動化機能で大きく利益貢献しよう!
(Β版非公開)