- お役立ち記事
- Revolutionizing Electronics: The Power of 1-Liquid Non-Curing Thermal Conductive Compound in Japanese Manufacturing
Revolutionizing Electronics: The Power of 1-Liquid Non-Curing Thermal Conductive Compound in Japanese Manufacturing
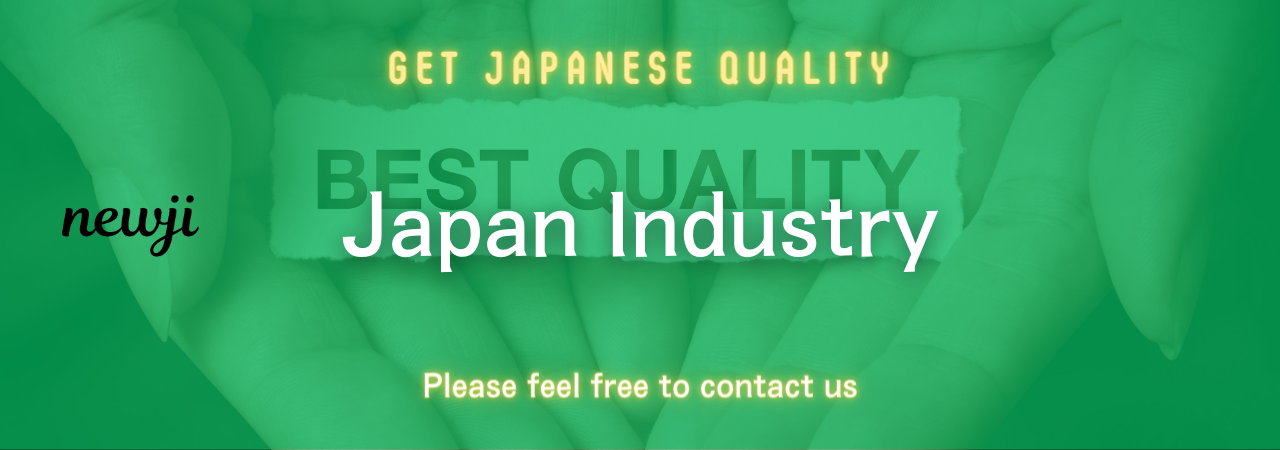
Revolutionizing Electronics: The Power of 1-Liquid Non-Curing Thermal Conductive Compound in Japanese Manufacturing
In the rapidly evolving world of electronics, the need for efficient thermal management solutions has never been more critical. As electronic devices become smaller and more powerful, managing heat effectively is paramount to ensure the longevity and reliability of these products. One groundbreaking solution that has emerged in recent years is the 1-liquid non-curing thermal conductive compound. Japanese manufacturers, known for their precision and innovation, have taken significant strides in utilizing this compound to enhance the performance and efficiency of electronic devices.
目次
Understanding the 1-Liquid Non-Curing Thermal Conductive Compound
To appreciate the revolutionary impact of the 1-liquid non-curing thermal conductive compound, it is essential first to understand what it is and how it functions. This thermal compound is a unique formulation designed to enhance heat transfer between surfaces, such as electronic components and heat sinks. Unlike traditional thermal pastes and adhesives, the 1-liquid non-curing compound remains in a semi-liquid state, providing continuous and consistent thermal conductivity without hardening or deteriorating over time.
Key Characteristics
Several key characteristics distinguish the 1-liquid non-curing thermal conductive compound from other thermal management solutions:
– **High Thermal Conductivity**: This compound exhibits superior thermal conductivity, ensuring efficient heat transfer and dissipation.
– **Non-Curing Nature**: Unlike traditional compounds that cure and harden, this thermal compound maintains its semi-liquid form, allowing for long-term reliability.
– **Low Thermal Resistance**: The compound offers low thermal resistance, minimizing the temperature differential between the heat source and the heat sink.
– **Ease of Application**: Its viscosity and consistency make it easy to apply and reapply, ensuring thorough coverage and optimal thermal performance.
Advantages of Using 1-Liquid Non-Curing Thermal Conductive Compound in Japanese Manufacturing
Japanese manufacturers have embraced the 1-liquid non-curing thermal conductive compound for several compelling reasons. Let’s delve into the key advantages this innovation brings to the table.
Enhanced Thermal Management
One of the primary benefits of this compound is its ability to significantly enhance thermal management in electronic devices. Efficient heat dissipation is crucial for preventing overheating and ensuring the longevity of electronic components. The high thermal conductivity of the 1-liquid non-curing compound ensures that heat is transferred away from critical components swiftly and effectively.
Improved Reliability and Longevity
Traditional thermal compounds that cure and harden over time can degrade and lose their effectiveness. This degradation can lead to increased thermal resistance and compromised thermal management. In contrast, the non-curing nature of the 1-liquid compound ensures consistent performance over extended periods. This reliability translates to longer-lasting electronic devices with fewer failures and maintenance issues.
Simplified Application and Reapplication
The ease of application and reapplication is another significant advantage. Manufacturers can apply the compound with precision and ease, ensuring optimal coverage and thermal contact. Additionally, if components need to be replaced or reassembled, the compound’s non-curing nature allows for easy removal and reapplication without the risk of damaging parts.
Environmental and Cost Benefits
Traditional thermal management solutions often involve curing agents and materials that can pose environmental risks. The 1-liquid non-curing compound is formulated to be environmentally friendly, reducing the impact on manufacturing ecosystems. Moreover, its reliability and longevity can lead to cost savings in terms of reduced maintenance and fewer component replacements over the lifespan of electronic devices.
Challenges and Considerations in Implementing 1-Liquid Non-Curing Thermal Conductive Compound
As with any technological advancement, the adoption of the 1-liquid non-curing thermal conductive compound comes with its own set of challenges and considerations.
Compatibility with Existing Processes
One of the initial hurdles manufacturers may face is ensuring compatibility with existing manufacturing processes. Integrating this new compound into established workflows may require adjustments in application techniques, equipment, and quality control protocols. However, with careful planning and collaboration with suppliers, these challenges can be effectively addressed.
Quality Control and Consistency
Maintaining consistent quality and performance of the thermal compound is crucial to achieving the desired thermal management outcomes. Manufacturers need to establish robust quality control measures to ensure that the compound meets stringent standards. Collaborating closely with suppliers to monitor production and testing processes can help maintain consistency and reliability.
Market Competition and Differentiation
As more manufacturers recognize the benefits of the 1-liquid non-curing thermal conductive compound, the market landscape is likely to become more competitive. To stay ahead, manufacturers must focus on differentiating their products through innovation, superior quality, and effective marketing strategies. Building a strong reputation for reliability and performance can help secure a competitive edge.
Best Practices for Leveraging 1-Liquid Non-Curing Thermal Conductive Compound
To maximize the benefits of the 1-liquid non-curing thermal conductive compound, manufacturers can follow several best practices based on practical insights and field experience.
Collaborate with Trusted Suppliers
Establishing strong partnerships with reputable suppliers is essential. Suppliers with expertise in thermal management solutions can provide valuable guidance on selecting the right compound, optimizing application techniques, and ensuring consistent quality. Regular communication and collaboration with suppliers can also help address any challenges that arise during implementation.
Invest in Training and Education
Proper training and education for personnel involved in applying and handling the thermal compound are critical. Ensuring that employees understand the unique properties and benefits of the 1-liquid non-curing compound will lead to more accurate and effective application. Training programs can cover application techniques, quality control measures, and troubleshooting procedures.
Implement Robust Testing and Quality Control
Implementing rigorous testing and quality control protocols is essential to maintain the performance and reliability of the thermal compound. Regular testing can help identify any deviations from desired thermal conductivity and thermal resistance levels. Additionally, monitoring the compound’s performance over time can provide insights into its long-term effectiveness.
Optimize Application Techniques
To achieve optimal thermal performance, manufacturers should focus on refining application techniques. Ensuring even and thorough coverage of the compound on contact surfaces is crucial for minimizing thermal resistance. Manufacturers can experiment with different application methods, such as stencil printing or automated dispensing, to determine the most effective approach for their specific products.
Case Studies: Successful Implementation in Japanese Manufacturing
Examining real-world case studies of successful implementation can provide valuable insights into the practical benefits and challenges associated with the 1-liquid non-curing thermal conductive compound.
Case Study 1: Thermal Management in High-Performance Computing
A leading Japanese manufacturer of high-performance computing systems faced challenges related to overheating and thermal management. By adopting the 1-liquid non-curing thermal conductive compound, the manufacturer achieved significant improvements in heat dissipation and component reliability. The compound’s consistent performance over time reduced the risk of thermal-related failures, enhancing the overall performance of the computing systems.
Case Study 2: Enhanced Reliability in Automotive Electronics
In the automotive industry, electronic components must withstand harsh conditions and extreme temperatures. A Japanese automotive electronics manufacturer integrated the 1-liquid non-curing thermal conductive compound into their production processes. The compound’s ability to maintain its thermal conductivity without curing made it an ideal solution for ensuring reliable thermal management in critical automotive applications. This implementation resulted in improved reliability and longevity of electronic components, reducing the risk of failures in demanding environments.
The Future of Thermal Management in Electronics
The 1-liquid non-curing thermal conductive compound represents a significant advancement in thermal management technology, but it is only one piece of the puzzle. As electronic devices continue to evolve, ongoing research and innovation in thermal management solutions will be crucial to meet the growing demands of the industry.
Integration with Emerging Technologies
Emerging technologies such as artificial intelligence, the Internet of Things (IoT), and 5G connectivity will place even greater demands on thermal management. Manufacturers must explore how the 1-liquid non-curing compound can be integrated with these technologies to ensure optimal performance and reliability. Collaborative research and development efforts with academia and industry partners can drive innovation in this area.
Sustainable Practices and Materials
Sustainability is becoming an increasingly important consideration in manufacturing. Future developments in thermal management solutions should prioritize environmentally friendly materials and processes. Manufacturers can explore sustainable alternatives to existing compounds and work towards reducing the environmental impact of their products.
Conclusion
The 1-liquid non-curing thermal conductive compound has emerged as a game-changer in the field of thermal management for electronic devices. Japanese manufacturers, renowned for their precision and innovation, have led the way in harnessing the power of this compound to enhance the performance and reliability of their products.
By understanding the key characteristics, advantages, and challenges associated with this compound, manufacturers can implement best practices to optimize its use. Real-world case studies demonstrate the tangible benefits of adopting the 1-liquid non-curing thermal conductive compound in various industries.
As the electronics industry continues to advance, ongoing research and innovation will be essential to address the evolving thermal management needs. By embracing sustainable practices and collaborating with trusted suppliers and industry partners, manufacturers can stay at the forefront of this revolution in thermal management technology.
The future of electronics holds tremendous promise, and the 1-liquid non-curing thermal conductive compound will undoubtedly play a pivotal role in shaping that future, ensuring that electronic devices remain efficient, reliable, and sustainable for years to come.
資料ダウンロード
QCD調達購買管理クラウド「newji」は、調達購買部門で必要なQCD管理全てを備えた、現場特化型兼クラウド型の今世紀最高の購買管理システムとなります。
ユーザー登録
調達購買業務の効率化だけでなく、システムを導入することで、コスト削減や製品・資材のステータス可視化のほか、属人化していた購買情報の共有化による内部不正防止や統制にも役立ちます。
NEWJI DX
製造業に特化したデジタルトランスフォーメーション(DX)の実現を目指す請負開発型のコンサルティングサービスです。AI、iPaaS、および先端の技術を駆使して、製造プロセスの効率化、業務効率化、チームワーク強化、コスト削減、品質向上を実現します。このサービスは、製造業の課題を深く理解し、それに対する最適なデジタルソリューションを提供することで、企業が持続的な成長とイノベーションを達成できるようサポートします。
オンライン講座
製造業、主に購買・調達部門にお勤めの方々に向けた情報を配信しております。
新任の方やベテランの方、管理職を対象とした幅広いコンテンツをご用意しております。
お問い合わせ
コストダウンが利益に直結する術だと理解していても、なかなか前に進めることができない状況。そんな時は、newjiのコストダウン自動化機能で大きく利益貢献しよう!
(Β版非公開)