- お役立ち記事
- Production Management and Reduction of Inventory and Work-In-Process
Production Management and Reduction of Inventory and Work-In-Process
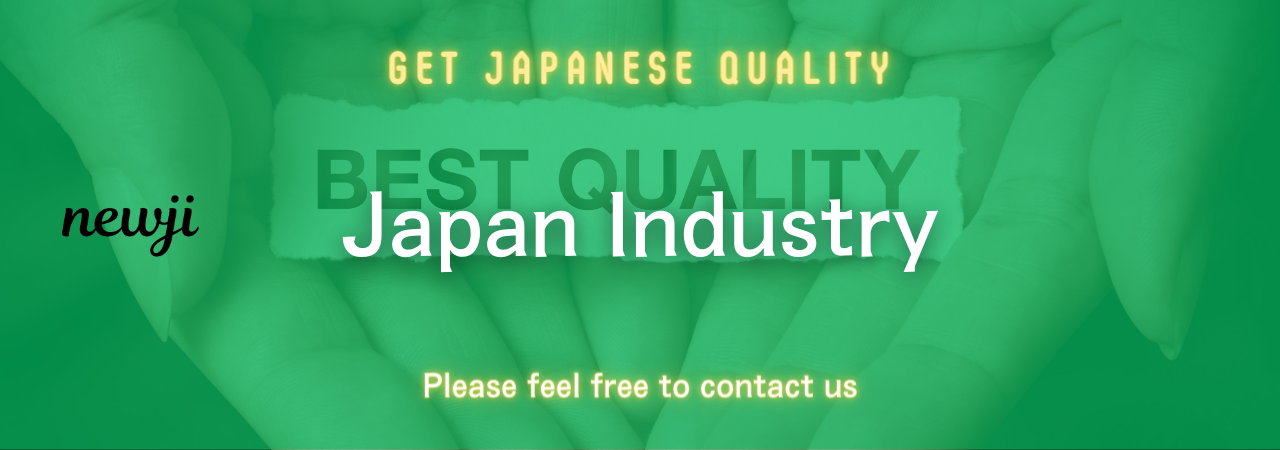
Production management is a critical aspect for any manufacturing business.
It deals with the planning, coordination, and control of production activities to ensure efficient use of resources and timely production of goods.
One of the major concerns in production management is the reduction of inventory and work-in-process (WIP).
This article explores strategies for reducing inventory and WIP, enhancing overall productivity.
目次
Understanding Inventory and Work-In-Process
What is Inventory?
Inventory refers to the raw materials, work-in-progress items, and finished goods that a company holds in stock.
Keeping high levels of inventory can tie up significant sums of money and storage space.
Costs associated with inventory include storage costs, insurance, and potential for obsolescence.
What is Work-In-Process (WIP)?
Work-In-Process (WIP) represents items that are partially completed in the production cycle.
Excessive WIP can lead to inefficiencies and high carrying costs.
It often signals bottlenecks in the production process and can delay the delivery of finished goods to customers.
Importance of Reducing Inventory and WIP
Reducing inventory and WIP is crucial for improving cash flow and increasing the efficiency of operations.
It leads to lower storage costs and reduces the risk of obsolete stock.
Additionally, reducing WIP can minimize lead times and ensure a more streamlined production process.
Cost Reduction
Lowering inventory levels directly decreases storage and holding costs.
In turn, this frees up capital that can be used for other purposes, such as investment in new technology or employee training.
Improved Efficiency
Minimizing WIP ensures that production activities are more synchronized and can significantly reduce lead times.
This allows manufacturers to be more responsive to customer demands and improve overall service levels.
Strategies for Reducing Inventory
There are several effective strategies to reduce inventory in a manufacturing environment.
Implementing these strategies can lead to more efficient production processes and lower costs.
Just-in-Time (JIT) Production
Just-in-Time (JIT) is a production strategy aimed at producing only what is needed, when it is needed.
This approach minimizes holding costs and reduces the risk of overproduction.
JIT requires accurate demand forecasting and strong supplier relationships to be effective.
Demand Forecasting
Accurate demand forecasting is essential for maintaining optimal inventory levels.
By understanding customer demand patterns, businesses can better align their production schedules with market needs.
This reduces the likelihood of excess inventory.
Vendor-Managed Inventory (VMI)
Vendor-Managed Inventory (VMI) involves suppliers taking responsibility for managing and replenishing inventory.
This can result in more accurate inventory levels and reduces the administrative burden on the manufacturer.
VMI also enhances collaboration and strengthens supplier relationships.
ABC Analysis
ABC analysis categorizes inventory into three groups: A, B, and C.
‘A’ items are high-value products with low sales frequency, ‘B’ items are moderate-value products with moderate sales frequency, and ‘C’ items are low-value products with high sales frequency.
By focusing on ‘A’ items, businesses can optimize inventory levels and reduce carrying costs.
Strategies for Reducing Work-In-Process
Reducing WIP can significantly improve the efficiency of the production process.
Implementing these strategies can help streamline operations and minimize production delays.
Lean Manufacturing
Lean manufacturing focuses on eliminating waste from the production process.
By identifying and removing non-value-added activities, companies can reduce WIP and improve overall efficiency.
This approach also emphasizes continuous improvement and employee involvement.
Implementing Kanban
Kanban is a visual production scheduling system that helps manage workflow and control WIP.
It utilizes cards or signals to indicate when production should start or stop.
Kanban ensures that work is only started when there is demand, preventing overproduction and reducing WIP.
Optimizing Production Scheduling
Effective production scheduling ensures that resources are used efficiently and that production bottlenecks are minimized.
This can be achieved through advanced scheduling software or by implementing priority rules that dictate the sequence of production activities.
Optimization leads to lower WIP and faster lead times.
Reducing Setup Times
Long setup times can lead to high levels of WIP as machines sit idle waiting for setup to be completed.
By implementing techniques such as Single-Minute Exchange of Die (SMED), companies can drastically reduce setup times.
This allows for smaller batch sizes and reduces the need for maintaining high levels of WIP.
Tackling Common Challenges
Despite the benefits, reducing inventory and WIP can present several challenges.
Being aware of these challenges allows businesses to develop strategies to overcome them.
Resistance to Change
Employees and management may resist changes in production processes.
To overcome this, it’s essential to communicate the benefits of new strategies and involve employees in the implementation process.
Training sessions and continuous feedback can also foster a culture of continuous improvement.
Supply Chain Disruptions
Supply chain disruptions can lead to difficulties in maintaining optimal inventory levels.
Building strong relationships with suppliers and having contingency plans in place can help mitigate these risks.
Diversifying the supplier base can also provide an additional level of security.
Data Accuracy
Inaccurate data can lead to poor decision-making and inefficiencies.
Implementing robust inventory management systems and regular audits can ensure data accuracy.
Investing in technology such as RFID and barcoding can also provide real-time insights into inventory levels.
Conclusion
Effective production management hinges on reducing inventory and WIP.
By incorporating strategies such as JIT, lean manufacturing, and accurate demand forecasting, companies can achieve significant cost savings and enhance overall efficiency.
While challenges exist, proactive planning and continuous improvement can help overcome these obstacles.
Ultimately, focusing on reducing inventory and WIP leads to a more agile and responsive manufacturing operation.
資料ダウンロード
QCD調達購買管理クラウド「newji」は、調達購買部門で必要なQCD管理全てを備えた、現場特化型兼クラウド型の今世紀最高の購買管理システムとなります。
ユーザー登録
調達購買業務の効率化だけでなく、システムを導入することで、コスト削減や製品・資材のステータス可視化のほか、属人化していた購買情報の共有化による内部不正防止や統制にも役立ちます。
NEWJI DX
製造業に特化したデジタルトランスフォーメーション(DX)の実現を目指す請負開発型のコンサルティングサービスです。AI、iPaaS、および先端の技術を駆使して、製造プロセスの効率化、業務効率化、チームワーク強化、コスト削減、品質向上を実現します。このサービスは、製造業の課題を深く理解し、それに対する最適なデジタルソリューションを提供することで、企業が持続的な成長とイノベーションを達成できるようサポートします。
オンライン講座
製造業、主に購買・調達部門にお勤めの方々に向けた情報を配信しております。
新任の方やベテランの方、管理職を対象とした幅広いコンテンツをご用意しております。
お問い合わせ
コストダウンが利益に直結する術だと理解していても、なかなか前に進めることができない状況。そんな時は、newjiのコストダウン自動化機能で大きく利益貢献しよう!
(Β版非公開)