- お役立ち記事
- Customization and Flexibility: Achieving Demand-Driven Manufacturing
Customization and Flexibility: Achieving Demand-Driven Manufacturing
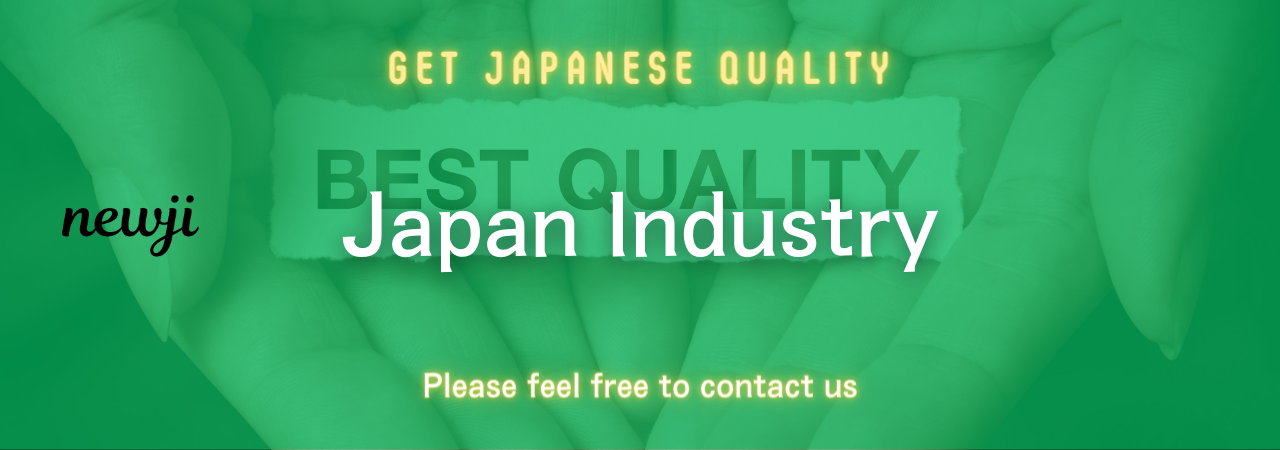
In today’s fast-paced market, manufacturers must adapt quickly to changing demands.
Demand-driven manufacturing is the key to staying competitive.
It allows companies to respond swiftly to customer needs, optimize production processes, and reduce waste.
Customization and flexibility play a crucial role in achieving a demand-driven manufacturing environment.
目次
Understanding Demand-Driven Manufacturing
Demand-driven manufacturing is a strategy that aligns production processes with actual customer demand.
Instead of producing goods based on forecasts, manufacturers produce items as they are needed.
This approach minimizes inventory, reduces costs, and enhances customer satisfaction.
To implement demand-driven manufacturing, companies need to be agile and responsive.
They must have the ability to scale production up or down based on real-time data.
This requires advanced planning systems, robust supply chain management, and the flexibility to customize products to meet specific customer requirements.
The Importance of Customization
Customization is a significant component of demand-driven manufacturing.
Customers today expect products that cater to their unique needs and preferences.
Offering customized solutions sets a company apart from its competitors and adds value to its offerings.
Customization in manufacturing can range from simple modifications to fully bespoke products.
In both cases, the goal is to meet the customer’s exact specifications without compromising quality or efficiency.
The Role of Technology in Customization
Advanced technologies play a pivotal role in enabling customization.
Digital tools like CAD (Computer-Aided Design) and CAM (Computer-Aided Manufacturing) systems allow engineers to design and produce customized products with precision.
3D printing, also known as additive manufacturing, offers incredible flexibility in creating prototypes and final products.
This technology allows for rapid changes and iterations, making it perfect for customization.
Benefits of Customization
Customization offers numerous benefits in a demand-driven manufacturing environment.
Firstly, it enhances customer loyalty by providing products that meet specific needs.
When customers feel valued and heard, they are more likely to return and recommend the brand to others.
Secondly, customization can lead to higher profit margins.
Customers are often willing to pay a premium for products that cater to their unique preferences.
By offering customized solutions, manufacturers can justify higher prices and increase their revenue.
Lastly, customization helps in reducing waste.
Producing items based on actual demand means less overproduction and inventory.
This results in efficient use of resources and a smaller environmental footprint.
The Need for Flexibility
Flexibility is just as important as customization in a demand-driven manufacturing setup.
Manufacturers must be able to adapt to changing market conditions, customer preferences, and production challenges.
Flexibility ensures that the production process can handle variations without significant disruptions.
Flexible manufacturing systems (FMS) are designed to accommodate changes in product design, production volume, and process flow.
These systems leverage automation, robotics, and real-time data to quickly adjust to new requirements.
Implementing Flexible Manufacturing Systems
Implementing a flexible manufacturing system requires thorough planning and investment in technology.
Here are some key steps to consider:
1. **Assessment and Planning**: Evaluate current production capabilities and identify areas that need improvement.
Develop a roadmap for integrating flexibility into the manufacturing process.
2. **Technology Integration**: Invest in advanced machinery and software that support flexibility.
Robotic arms, CNC machines, and IoT (Internet of Things) devices can enhance automation and real-time decision-making.
3. **Workforce Training**: Train employees to work with flexible systems and adapt to new technologies.
A skilled workforce is essential for maximizing the benefits of a flexible manufacturing environment.
4. **Supply Chain Collaboration**: Collaborate with suppliers to ensure they can provide materials and components quickly and efficiently.
A flexible supply chain is crucial for maintaining production agility.
Advantages of Flexibility
The advantages of flexibility in manufacturing are manifold.
Firstly, it allows manufacturers to respond swiftly to market changes.
If a particular product becomes popular, production can be ramped up to meet demand.
Conversely, if demand drops, production can be scaled back to avoid overproduction.
Secondly, flexibility supports product innovation.
Manufacturers can experiment with new designs, materials, and processes without significant downtime or cost.
This leads to faster time-to-market and a competitive edge in the industry.
Lastly, flexibility enhances overall operational efficiency.
By reducing downtime and optimizing resource usage, manufacturers can achieve higher productivity and lower operational costs.
Combining Customization and Flexibility
The true power of demand-driven manufacturing lies in combining customization and flexibility.
Together, they create a responsive, efficient, and customer-centric production environment.
Manufacturers can deliver personalized products at scale, respond to market trends, and optimize their operations.
Case Study: A Successful Implementation
Let’s look at an example of a company that successfully implemented demand-driven manufacturing.
XYZ Electronics, a leading manufacturer of consumer electronics, faced challenges with inventory management and customer satisfaction.
By adopting a demand-driven approach, they transformed their production process.
First, they invested in advanced manufacturing technologies and data analytics.
This allowed them to monitor real-time demand and adjust production accordingly.
They implemented flexible manufacturing systems that could handle different product configurations and volumes.
Next, they focused on customization.
Customers could personalize their electronic devices by choosing from various features, colors, and designs.
XYZ Electronics used 3D printing to create prototypes and small batches quickly.
This way, they tested and refined custom designs before mass production.
The results were remarkable.
Customer satisfaction soared as individuals received products tailored to their preferences.
Inventory levels decreased, leading to significant cost savings.
XYZ Electronics also gained a reputation for innovation and responsiveness, attracting new customers and increasing market share.
Conclusion
Customization and flexibility are the cornerstones of demand-driven manufacturing.
By tailoring products to customer needs and adapting swiftly to market changes, manufacturers can achieve higher efficiency, reduced costs, and enhanced customer satisfaction.
Investing in advanced technologies, training the workforce, and collaborating with suppliers are essential steps toward achieving a demand-driven manufacturing environment.
Embracing customization and flexibility will not only improve operational efficiency but also provide a competitive edge in today’s dynamic market.
資料ダウンロード
QCD調達購買管理クラウド「newji」は、調達購買部門で必要なQCD管理全てを備えた、現場特化型兼クラウド型の今世紀最高の購買管理システムとなります。
ユーザー登録
調達購買業務の効率化だけでなく、システムを導入することで、コスト削減や製品・資材のステータス可視化のほか、属人化していた購買情報の共有化による内部不正防止や統制にも役立ちます。
NEWJI DX
製造業に特化したデジタルトランスフォーメーション(DX)の実現を目指す請負開発型のコンサルティングサービスです。AI、iPaaS、および先端の技術を駆使して、製造プロセスの効率化、業務効率化、チームワーク強化、コスト削減、品質向上を実現します。このサービスは、製造業の課題を深く理解し、それに対する最適なデジタルソリューションを提供することで、企業が持続的な成長とイノベーションを達成できるようサポートします。
オンライン講座
製造業、主に購買・調達部門にお勤めの方々に向けた情報を配信しております。
新任の方やベテランの方、管理職を対象とした幅広いコンテンツをご用意しております。
お問い合わせ
コストダウンが利益に直結する術だと理解していても、なかなか前に進めることができない状況。そんな時は、newjiのコストダウン自動化機能で大きく利益貢献しよう!
(Β版非公開)