- お役立ち記事
- Building Digital Infrastructure to Support the Next Generation of Manufacturing
Building Digital Infrastructure to Support the Next Generation of Manufacturing
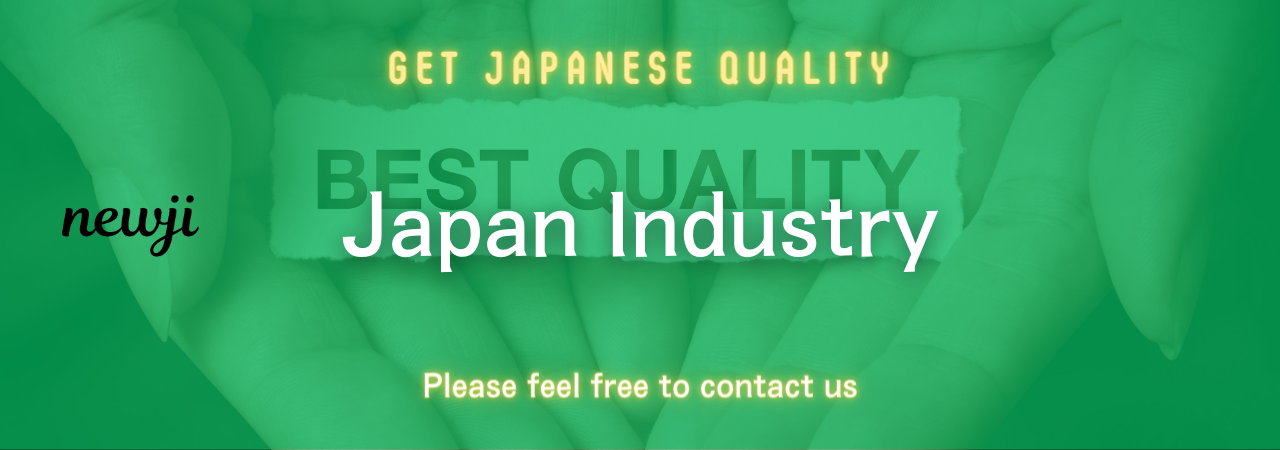
Manufacturing is undergoing a radical transformation, spurred by advances in digital technology.
Traditional methods are being replaced by more efficient, precise, and interconnected systems.
To thrive in this evolving landscape, companies must build robust digital infrastructure to support the next generation of manufacturing.
目次
Understanding Digital Infrastructure
Digital infrastructure encompasses the hardware, software, networks, and data management systems necessary for modern manufacturing.
It includes everything from cloud computing and IoT devices to artificial intelligence (AI) and blockchain technology.
These components work together to create a connected, intelligent ecosystem capable of optimizing manufacturing processes.
Cloud Computing
Cloud computing offers scalable resources and services that can be accessed via the Internet.
By leveraging cloud solutions, manufacturers can store vast amounts of data, run applications, and perform complex computations without needing extensive on-premises equipment.
Cloud computing also provides flexibility, allowing businesses to quickly adapt to changing demands and requirements.
Internet of Things (IoT)
IoT involves embedding sensors and devices into equipment and machinery to collect real-time data.
This data is crucial for monitoring performance, detecting anomalies, and predicting maintenance needs.
By integrating IoT with digital infrastructure, manufacturers can gain insights into their operations, improving efficiency and reducing downtime.
Artificial Intelligence (AI)
AI algorithms analyze large datasets to identify patterns, predict outcomes, and optimize processes.
In manufacturing, AI can improve quality control, automate repetitive tasks, and enhance decision-making.
For instance, AI-driven predictive maintenance solutions can forecast equipment failures before they occur, saving time and costs.
Blockchain Technology
Blockchain offers a secure and transparent way to record transactions and track assets.
In manufacturing, it can be used to ensure the authenticity of materials, track the lifecycle of products, and streamline supply chains.
Blockchain’s decentralized nature reduces the risk of fraud and enhances trust among stakeholders.
Benefits of Digital Infrastructure in Manufacturing
Building a robust digital infrastructure offers numerous advantages for manufacturers.
These benefits include increased efficiency, enhanced collaboration, improved quality control, and greater agility.
Increased Efficiency
Digital infrastructure allows manufacturers to automate repetitive and time-consuming tasks.
Automation not only speeds up production but also minimizes human error.
Additionally, data collected through IoT devices enables real-time monitoring and adjustments, ensuring optimal performance.
Enhanced Collaboration
Digital tools facilitate communication and collaboration across different departments and locations.
Cloud-based platforms enable team members to access and share information seamlessly.
This interconnectedness promotes synchronized efforts, leading to more cohesive and productive operations.
Improved Quality Control
Advanced analytics and AI algorithms can swiftly identify defects and deviations in the manufacturing process.
Early detection allows for immediate corrective actions, reducing waste and ensuring consistent product quality.
Quality control processes become more proactive, rather than reactive, driving higher customer satisfaction.
Greater Agility
A well-built digital infrastructure enables manufacturers to quickly adapt to market demands and changes.
Scalable resources, flexible production lines, and data-driven insights empower businesses to pivot and innovate swiftly.
This agility is critical in staying competitive in a rapidly changing industry.
Challenges in Implementing Digital Infrastructure
While the benefits are compelling, building digital infrastructure comes with its own set of challenges.
Costs, cybersecurity, and skill gaps are among the main hurdles manufacturers face.
Initial Costs
The initial investment in digital infrastructure can be significant.
Purchasing new equipment, upgrading existing systems, and training staff require substantial capital.
However, these costs are often offset by the long-term gains in efficiency, productivity, and profitability.
Cybersecurity Risks
As manufacturing becomes more connected, it also becomes more vulnerable to cyber threats.
Protecting sensitive data and intellectual property is crucial.
Manufacturers need to implement robust cybersecurity measures, regularly update systems, and educate employees about best practices to mitigate risks.
Skill Gaps
The transition to digital manufacturing requires a workforce skilled in new technologies.
Current employees may need reskilling or upskilling to handle advanced tools and processes.
Investing in training and development programs is essential to bridge these skill gaps and maximize the potential of digital infrastructure.
Steps to Building Digital Infrastructure
Implementing digital infrastructure requires a strategic approach.
Manufacturers should follow a series of steps to ensure a smooth transition.
Assess Current Capabilities
The first step is to evaluate the existing infrastructure and identify areas needing improvement.
Understanding the current state helps in setting realistic goals and benchmarks for future developments.
Create a Roadmap
Develop a comprehensive roadmap outlining the steps needed to build digital infrastructure.
This plan should include timelines, resource allocation, and key milestones.
A clear roadmap ensures all stakeholders are aligned and aware of their roles in the transition.
Invest in Technology
Based on the roadmap, invest in the necessary technologies and tools.
This may involve purchasing new equipment, adopting cloud solutions, or integrating IoT devices.
Prioritize technologies that offer scalability and flexibility to adapt to future needs.
Train the Workforce
Equip your team with the skills required to operate and manage new systems.
Offer regular training sessions, workshops, and online courses.
Encourage continuous learning to keep pace with evolving technologies and industry trends.
Monitor and Optimize
After implementation, continuously monitor the digital infrastructure’s performance.
Collect feedback, analyze data, and make adjustments as needed.
Regular maintenance and updates ensure the infrastructure remains efficient and secure.
Conclusion
Building a digital infrastructure is essential for supporting the next generation of manufacturing.
By embracing technologies like cloud computing, IoT, AI, and blockchain, manufacturers can revolutionize their operations.
The benefits of increased efficiency, enhanced collaboration, improved quality control, and greater agility make the investment worthwhile.
Despite challenges such as initial costs, cybersecurity risks, and skill gaps, a strategic approach can facilitate a seamless transition.
Manufacturers that prioritize digital infrastructure today will be better positioned to thrive in the competitive landscape of tomorrow.
資料ダウンロード
QCD調達購買管理クラウド「newji」は、調達購買部門で必要なQCD管理全てを備えた、現場特化型兼クラウド型の今世紀最高の購買管理システムとなります。
ユーザー登録
調達購買業務の効率化だけでなく、システムを導入することで、コスト削減や製品・資材のステータス可視化のほか、属人化していた購買情報の共有化による内部不正防止や統制にも役立ちます。
NEWJI DX
製造業に特化したデジタルトランスフォーメーション(DX)の実現を目指す請負開発型のコンサルティングサービスです。AI、iPaaS、および先端の技術を駆使して、製造プロセスの効率化、業務効率化、チームワーク強化、コスト削減、品質向上を実現します。このサービスは、製造業の課題を深く理解し、それに対する最適なデジタルソリューションを提供することで、企業が持続的な成長とイノベーションを達成できるようサポートします。
オンライン講座
製造業、主に購買・調達部門にお勤めの方々に向けた情報を配信しております。
新任の方やベテランの方、管理職を対象とした幅広いコンテンツをご用意しております。
お問い合わせ
コストダウンが利益に直結する術だと理解していても、なかなか前に進めることができない状況。そんな時は、newjiのコストダウン自動化機能で大きく利益貢献しよう!
(Β版非公開)