- お役立ち記事
- Manufacturing Process of Fans and Assembly Procedures
Manufacturing Process of Fans and Assembly Procedures
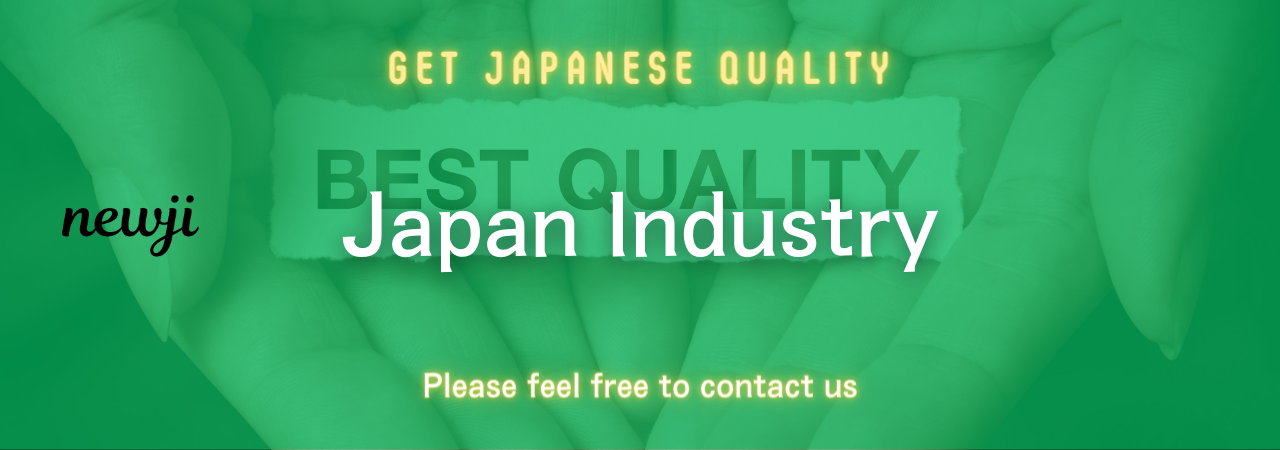
Fans are indispensable appliances that help keep our environments cool and comfortable.
They come in various shapes and sizes, suited for different needs.
To understand how these important devices come into existence, let’s delve into the manufacturing process of fans and their assembly procedures.
目次
Raw Material Selection
The manufacturing process of fans begins with the selection of high-quality raw materials.
Materials such as metals, plastics, and electrical components are sourced from reliable suppliers.
Metals like aluminum or steel are used for fan blades and structural components, while plastics are often employed for the casing and other non-structural parts.
Ensuring the use of premium materials guarantees the durability and efficiency of the final product.
Design and Prototyping
Before mass production begins, engineers and designers work on creating a detailed blueprint of the fan.
This involves deciding on the fan’s size, blade shape, motor specifications, and other important features.
Advanced software is used to create 3D models, allowing designers to visualize the final product and make necessary adjustments.
Once the design is finalized, a prototype is built to test its functionality and performance.
The prototype undergoes rigorous testing to ensure it meets all safety and efficiency standards.
Blade Manufacturing
Fan blades are one of the most crucial components in a fan.
The blade manufacturing process starts with the cutting of metal sheets into the desired shape and size.
This is usually done using high-precision machines to ensure uniformity.
Next, the edges of the blades are polished to reduce any roughness and ensure smooth operation.
For plastic blades, injection molding is the preferred method.
Molten plastic is injected into molds of the desired blade shape, which then cool and harden.
Both metal and plastic blades are subjected to quality checks to ensure they are free from defects.
Motor Manufacturing
The motor is the powerhouse of the fan, responsible for converting electrical energy into mechanical energy to rotate the blades.
The manufacturing process of a motor involves several steps.
First, the stator and rotor, the two main components of a motor, are constructed.
The stator is made by winding copper wires around a core, while the rotor is typically constructed from laminated steel.
These components are then assembled along with other parts, such as bearings and enclosures.
The motor undergoes rigorous testing to ensure it operates efficiently and reliably.
Assembly Line Production
Once all the individual components are ready, they move on to the assembly line for final assembly.
An assembly line is a step-by-step process where each worker or machine performs a specific task.
The casing of the fan is assembled first, followed by the installation of the motor.
The blades are then attached to the motor, ensuring they are securely fastened.
Electrical wiring is connected, and any control panels or switches are installed.
Automation plays a significant role in modern manufacturing, with robots and automated systems used to perform tasks with high precision and speed.
Quality Control and Testing
After assembly, each fan undergoes thorough quality control checks.
This includes visual inspections to look for any defects, as well as functional tests to ensure the fan operates as intended.
Various parameters such as blade balance, motor efficiency, and noise levels are measured.
Fans are subjected to stress tests to ensure they can withstand prolonged use without issues.
Only those units that pass all quality control checks are approved for packaging.
Packaging and Shipping
Once the fans have passed quality control, they move on to the packaging stage.
Each fan is carefully packed in a box with protective materials to prevent damage during transportation.
User manuals, warranty cards, and any necessary accessories are included in the packaging.
The boxes are then sealed, labeled, and stacked onto pallets for shipping.
Distribution channels are planned to ensure the fans reach retailers and customers in the shortest time possible.
Efficient logistics and warehousing systems play a crucial role in this process.
Automation and Innovation
Technology and innovation continually influence the manufacturing process of fans.
Automation has significantly improved the efficiency and precision of manufacturing.
Advanced robotics, automated quality control systems, and smart manufacturing techniques ensure that fans are produced at a consistent high quality.
Innovation in materials science has led to the development of more efficient and durable components.
For example, the use of lightweight, high-strength materials ensures better performance and longevity.
Energy-efficient motors and smart control systems contribute to reduced energy consumption and enhanced user convenience.
Environmental Considerations
Sustainable manufacturing processes are increasingly prioritized in the production of fans.
Manufacturers are adopting environmentally friendly practices, such as recycling and waste reduction.
Energy-efficient production methods minimize the carbon footprint.
Eco-friendly materials are favored, and efforts are made to reduce harmful emissions during manufacturing.
Consumers are also becoming more environmentally conscious, preferring products that are sustainably produced and energy-efficient.
Manufacturers often highlight their green credentials to appeal to this growing market segment.
Understanding the manufacturing process and assembly procedures of fans provides valuable insights into how these essential appliances are created.
From raw material selection and design to assembly and quality control, each step is crucial in producing a high-quality fan.
Advancements in technology and a focus on sustainability ensure that fans not only perform well but also contribute to a greener planet.
資料ダウンロード
QCD調達購買管理クラウド「newji」は、調達購買部門で必要なQCD管理全てを備えた、現場特化型兼クラウド型の今世紀最高の購買管理システムとなります。
ユーザー登録
調達購買業務の効率化だけでなく、システムを導入することで、コスト削減や製品・資材のステータス可視化のほか、属人化していた購買情報の共有化による内部不正防止や統制にも役立ちます。
NEWJI DX
製造業に特化したデジタルトランスフォーメーション(DX)の実現を目指す請負開発型のコンサルティングサービスです。AI、iPaaS、および先端の技術を駆使して、製造プロセスの効率化、業務効率化、チームワーク強化、コスト削減、品質向上を実現します。このサービスは、製造業の課題を深く理解し、それに対する最適なデジタルソリューションを提供することで、企業が持続的な成長とイノベーションを達成できるようサポートします。
オンライン講座
製造業、主に購買・調達部門にお勤めの方々に向けた情報を配信しております。
新任の方やベテランの方、管理職を対象とした幅広いコンテンツをご用意しております。
お問い合わせ
コストダウンが利益に直結する術だと理解していても、なかなか前に進めることができない状況。そんな時は、newjiのコストダウン自動化機能で大きく利益貢献しよう!
(Β版非公開)