- お役立ち記事
- Manufacturing Process of Acrylic Floor Mats and Anti-slip Performance Improvement
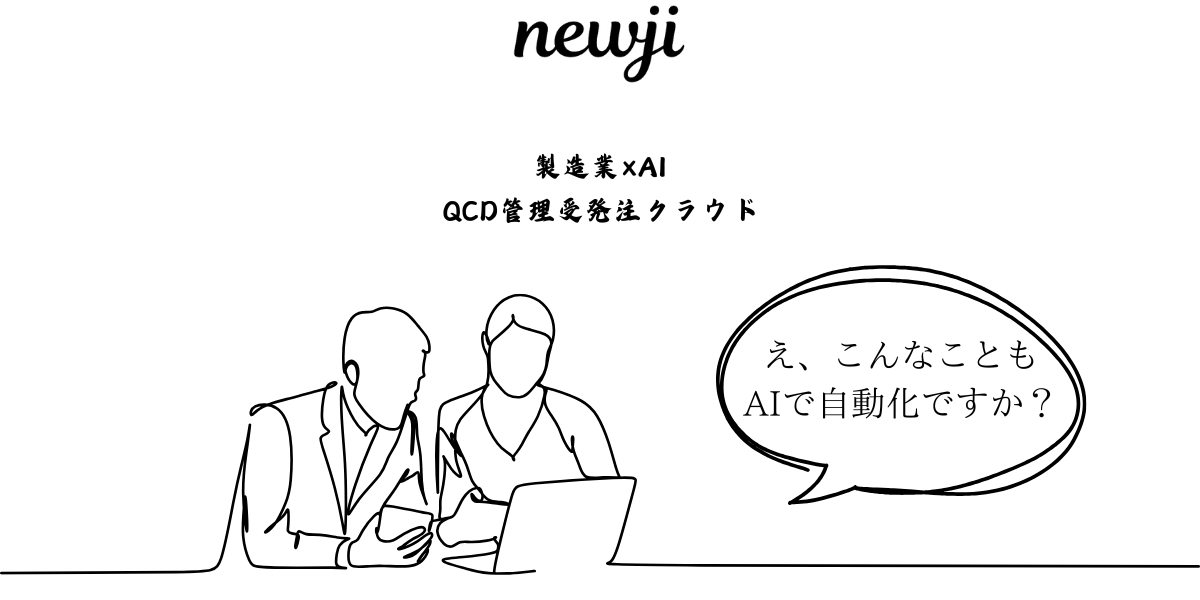
Manufacturing Process of Acrylic Floor Mats and Anti-slip Performance Improvement
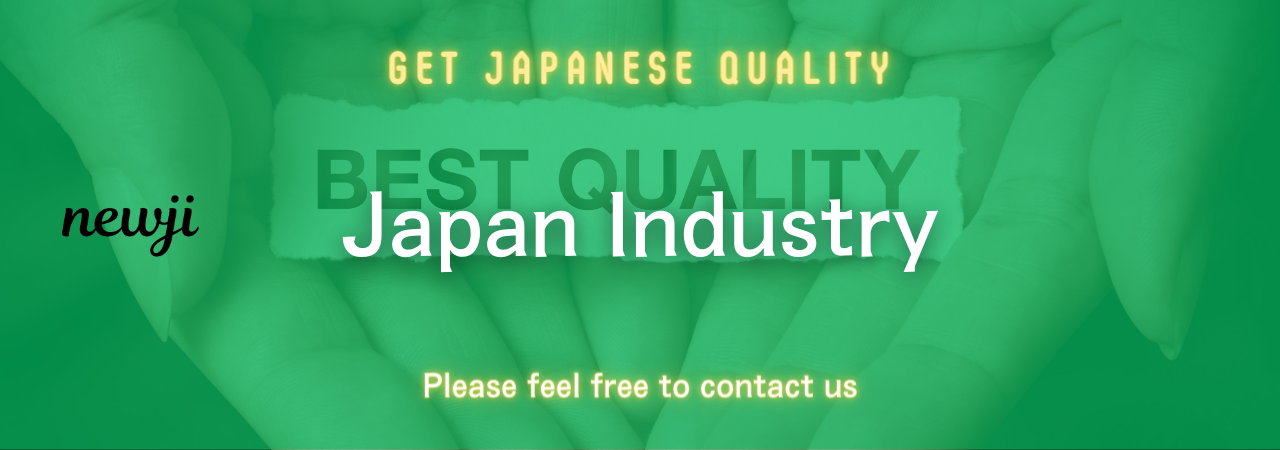
Acrylic floor mats have become an integral part of many households and businesses due to their versatility, durability, and aesthetic appeal.
Their unique construction offers numerous benefits, including anti-slip features that contribute to safety in various environments.
This article will explore the manufacturing process of acrylic floor mats and delve into how their anti-slip performance can be enhanced.
目次
Understanding Acrylic Floor Mats
What Are Acrylic Floor Mats?
Acrylic floor mats are made from synthetic fibers derived from acrylic resin.
These mats are popular because they can be easily customized in terms of color, pattern, and texture to suit different preferences.
They are also known for their resistance to fading and staining, making them a practical choice for both residential and commercial settings.
Why Choose Acrylic Mats Over Other Materials?
Acrylic mats are preferred over other types of floor mats for several reasons:
– **Durability:** Acrylic fibers are strong and can withstand heavy foot traffic.
– **Easy Maintenance:** They are easy to clean and maintain.
– **Aesthetic Appeal:** With numerous design options, they can match any decor.
– **Anti-Slip Properties:** Properly manufactured acrylic mats can offer excellent grip, reducing the risk of slips and falls.
The Manufacturing Process of Acrylic Floor Mats
Step 1: Acrylic Fiber Production
The first step in the manufacturing process involves producing acrylic fibers.
Acrylic resin, derived from petroleum, is processed to form a viscous solution.
This solution is then pushed through a device called a spinneret, which has tiny holes, to create filaments.
These filaments are coagulated in a bath and then stretched to enhance their strength and elasticity.
Step 2: Spinning and Weaving
After producing the acrylic fibers, the next step is spinning them into yarn.
This yarn can then be woven or knitted to form the base material of the floor mat.
Various weaving techniques, such as tufting or braiding, can be employed to achieve the desired texture and appearance of the mat.
Step 3: Dyeing and Finishing
Once the acrylic yarn is ready, it undergoes a dyeing process to achieve the required color.
High-quality dyes are used to ensure the colors are vibrant and resistant to fading.
After dyeing, the mat material is treated with various chemicals to enhance its properties, such as stain resistance and UV protection.
Step 4: Adding the Anti-Slip Backing
This is a crucial step in the manufacturing process that directly impacts the safety and functionality of the mat.
The anti-slip backing is usually made from materials like rubber or latex, which provide excellent grip on different flooring surfaces.
This backing is applied to the underside of the mat using adhesives or through thermal bonding techniques.
Step 5: Cutting and Shaping
After completing the backing application, the mat is cut and shaped into the desired size and form.
Advanced machinery ensures precise cutting, enabling the production of mats in various shapes, such as rectangles, circles, and custom designs.
Each piece is checked for quality to ensure it meets the required standards before packaging.
Enhancing Anti-Slip Performance
Improved Backing Materials
One of the most effective ways to enhance the anti-slip performance of acrylic floor mats is by improving the materials used for the backing.
Innovations in material science have led to the development of high-friction compounds that provide superior grip.
Some manufacturers use a combination of rubber and silicone to achieve a non-slip surface that remains effective even in wet conditions.
Textured Surfaces
The design of the mat’s surface can also influence its slip resistance.
By incorporating textured patterns or raised elements on the surface, the friction between the mat and the foot is increased.
These textures can range from simple ridges to intricate designs that enhance both the aesthetic and functional properties of the mat.
Adhesive Solutions
In addition to traditional backing materials, adhesive solutions can be used to improve the grip of acrylic floor mats.
Some products feature peel-and-stick adhesive strips that secure the mat to the floor.
These adhesives are designed to withstand regular use and can be easily removed or replaced when necessary.
Maintenance Tips for Optimal Performance
To maintain the anti-slip properties of acrylic floor mats, regular maintenance is essential.
Dust and debris can accumulate on the surface and reduce the mat’s grip.
Cleaning the mat with mild soap and water and ensuring it is completely dry before use can help preserve its effectiveness.
It is also advisable to periodically check the condition of the anti-slip backing and replace the mat if significant wear or damage is observed.
Conclusion
The manufacturing process of acrylic floor mats involves several intricate steps, from producing the acrylic fibers to applying the anti-slip backing.
These steps ensure that the final product is durable, aesthetically pleasing, and safe for use in various environments.
By focusing on materials, surface textures, and maintenance, the anti-slip performance of acrylic floor mats can be significantly improved, providing greater safety and peace of mind for users.
Whether for a home, office, or commercial space, investing in high-quality acrylic floor mats is a practical choice that combines functionality and style.
資料ダウンロード
QCD調達購買管理クラウド「newji」は、調達購買部門で必要なQCD管理全てを備えた、現場特化型兼クラウド型の今世紀最高の購買管理システムとなります。
ユーザー登録
調達購買業務の効率化だけでなく、システムを導入することで、コスト削減や製品・資材のステータス可視化のほか、属人化していた購買情報の共有化による内部不正防止や統制にも役立ちます。
NEWJI DX
製造業に特化したデジタルトランスフォーメーション(DX)の実現を目指す請負開発型のコンサルティングサービスです。AI、iPaaS、および先端の技術を駆使して、製造プロセスの効率化、業務効率化、チームワーク強化、コスト削減、品質向上を実現します。このサービスは、製造業の課題を深く理解し、それに対する最適なデジタルソリューションを提供することで、企業が持続的な成長とイノベーションを達成できるようサポートします。
オンライン講座
製造業、主に購買・調達部門にお勤めの方々に向けた情報を配信しております。
新任の方やベテランの方、管理職を対象とした幅広いコンテンツをご用意しております。
お問い合わせ
コストダウンが利益に直結する術だと理解していても、なかなか前に進めることができない状況。そんな時は、newjiのコストダウン自動化機能で大きく利益貢献しよう!
(Β版非公開)