- お役立ち記事
- Manufacturing Process of Pipe Fittings and Pressure Resistance Enhancement
Manufacturing Process of Pipe Fittings and Pressure Resistance Enhancement
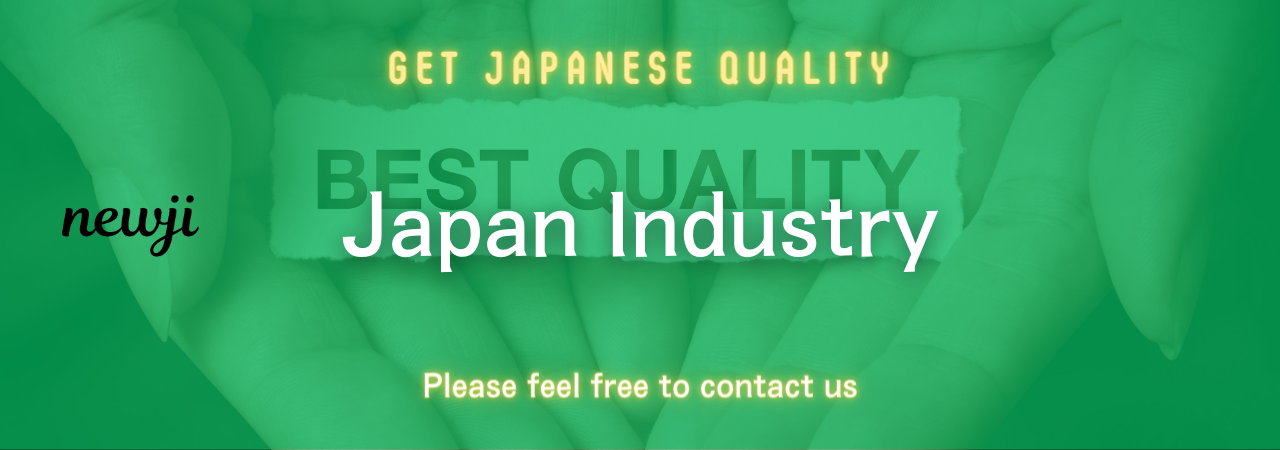
Pipe fittings are crucial components in various plumbing and industrial applications, ensuring smooth fluid flow and connection between different pipeline sections.
Understanding the manufacturing process and how their pressure resistance is enhanced can be beneficial for anyone involved in industries that rely on piping systems.
目次
Introduction to Pipe Fittings
Pipe fittings serve multiple purposes in the plumbing and industrial sectors.
They are designed to connect straight sections of pipe, adapt them to different sizes or shapes, and regulate fluid flow.
Examples include elbows, tees, couplings, and valves.
The manufacturing process of pipe fittings requires precision and adherence to quality standards since poor-quality fittings can lead to system failures and safety hazards.
Materials Used in Manufacturing Pipe Fittings
Various materials are used in the production of pipe fittings, each offering its distinct advantages.
Common materials include:
Steel
Steel pipe fittings are highly durable and can withstand high pressures and temperatures.
They are widely used in industrial applications due to their strength and longevity.
Brass
Brass fittings are known for their corrosion resistance and ease of use.
They are commonly found in plumbing applications.
Plastic
Plastic fittings, such as those made from PVC or CPVC, are lightweight and easy to install.
They are typically used in residential plumbing and low-pressure applications.
Copper
Copper fittings are highly resistant to corrosion and are commonly used in plumbing systems for both hot and cold water supplies.
Manufacturing Process of Pipe Fittings
The manufacturing process of pipe fittings involves several stages to ensure they meet the required specifications and standards.
Step 1: Raw Material Selection and Preparation
The process begins with selecting the appropriate raw material based on the application.
The selected material undergoes quality checks.
It is then cut into the required size and shape.
Step 2: Heating and Forming
The prepared raw material is heated to the required temperature to make it malleable.
Different forming techniques are employed depending on the type of fitting being produced:
– **Forging**: In this method, the heated material is hammered or pressed into the desired shape. Forging enhances the strength of the fitting.
– **Extrusion**: For this method, the material is forced through a die to create long sections that are then cut to the required length.
– **Casting**: This involves pouring molten material into a mold to obtain the desired shape. It is commonly used for complex shapes.
Step 3: Machining
Machining processes, such as drilling, threading, and grooving, are performed to achieve the required dimensions and features.
This step ensures that the fittings can connect pipes securely and function as intended.
Step 4: Surface Treatment
Surface treatment processes such as galvanizing, coating, and painting are applied to protect against corrosion and enhance the fitting’s longevity.
These treatments are essential, especially for fittings used in harsh or corrosive environments.
Step 5: Inspection and Quality Control
Each fitting undergoes rigorous inspection to ensure it meets the required standards.
Non-destructive testing methods, like ultrasonic and radiographic inspection, are used to detect any internal or surface defects.
Step 6: Final Processing and Packaging
After passing quality checks, the fittings undergo final processing, such as cleaning and labeling.
They are then packaged carefully to prevent damage during transportation and storage.
Enhancing Pressure Resistance of Pipe Fittings
Pipe fittings must withstand the systems’ operational pressure to ensure safety and reliability.
Several techniques are used to enhance the pressure resistance of fittings:
Material Selection
Selecting appropriate materials with high tensile strength and corrosion resistance improves the fittings’ ability to withstand high pressures.
Heat Treatment
Heat treatment processes like annealing and quenching enhance the material’s mechanical properties, making fittings more robust and durable.
Welded Joints
For fittings exposed to high pressure, welded joints provide additional strength.
Welding creates a continuous connection, reducing the risk of leaks and failures.
Reinforcement
Reinforcement techniques, like adding ribs or increasing wall thickness, provide additional strength to the fittings.
These reinforcements distribute the stress more evenly, reducing the chances of failure under pressure.
Conclusion
The manufacturing process of pipe fittings involves various stages, from raw material selection to final packaging, to ensure they meet stringent quality standards.
Enhancing the pressure resistance of these fittings through material selection, heat treatment, welded joints, and reinforcement techniques is crucial for their reliability and longevity.
Understanding these processes is essential for industries relying on piping systems, as it helps in selecting the appropriate fittings for specific applications, ultimately ensuring the safety and efficiency of the entire system.
資料ダウンロード
QCD調達購買管理クラウド「newji」は、調達購買部門で必要なQCD管理全てを備えた、現場特化型兼クラウド型の今世紀最高の購買管理システムとなります。
ユーザー登録
調達購買業務の効率化だけでなく、システムを導入することで、コスト削減や製品・資材のステータス可視化のほか、属人化していた購買情報の共有化による内部不正防止や統制にも役立ちます。
NEWJI DX
製造業に特化したデジタルトランスフォーメーション(DX)の実現を目指す請負開発型のコンサルティングサービスです。AI、iPaaS、および先端の技術を駆使して、製造プロセスの効率化、業務効率化、チームワーク強化、コスト削減、品質向上を実現します。このサービスは、製造業の課題を深く理解し、それに対する最適なデジタルソリューションを提供することで、企業が持続的な成長とイノベーションを達成できるようサポートします。
オンライン講座
製造業、主に購買・調達部門にお勤めの方々に向けた情報を配信しております。
新任の方やベテランの方、管理職を対象とした幅広いコンテンツをご用意しております。
お問い合わせ
コストダウンが利益に直結する術だと理解していても、なかなか前に進めることができない状況。そんな時は、newjiのコストダウン自動化機能で大きく利益貢献しよう!
(Β版非公開)