- お役立ち記事
- Toward the Realization of Smart Factories
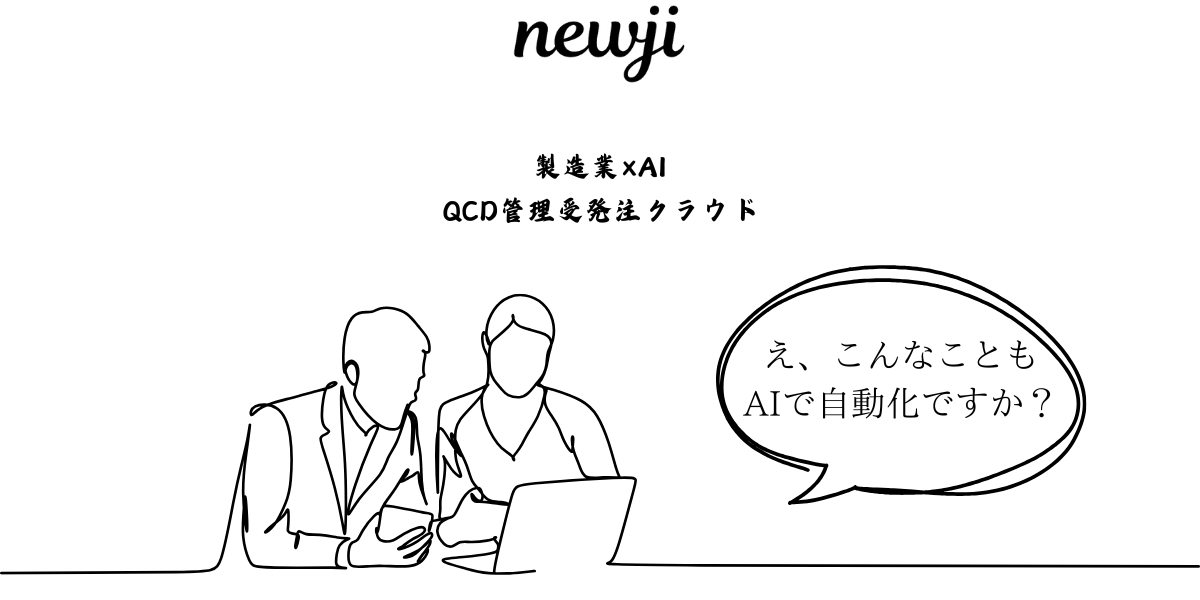
Toward the Realization of Smart Factories
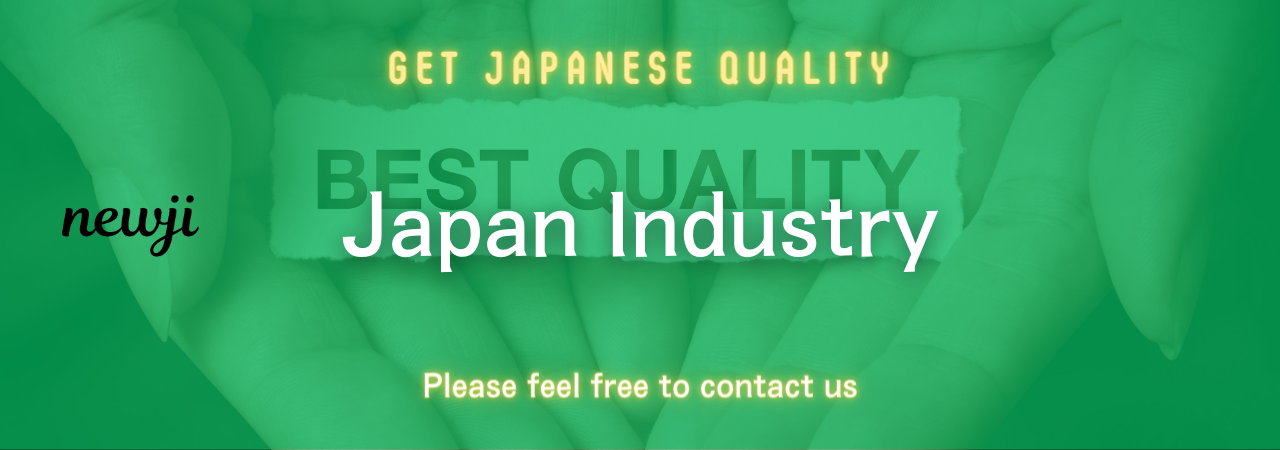
目次
Introduction to Smart Factories
In today’s rapidly evolving technological landscape, the concept of smart factories has become a pivotal topic of discussion.
Smart factories, also referred to as Industry 4.0, integrate cutting-edge technologies to enhance manufacturing processes, boost efficiency, and reduce costs.
These advanced manufacturing setups rely heavily on automation, data exchange, and the Internet of Things (IoT) to create a highly efficient production environment.
What Are Smart Factories?
Smart factories are an evolution of traditional manufacturing plants.
They employ a variety of digital technologies like artificial intelligence (AI), robotics, and machine learning to streamline production processes.
By leveraging these technologies, smart factories can optimize resources, predict equipment failures, and adapt to changing demands in real-time.
At the core of smart factories is the ability to connect machines, systems, and humans in a seamless network.
This interconnected system allows for more dynamic and flexible production lines, capable of adjusting to new tasks with minimal downtime.
Benefits of Smart Factories
Enhanced Efficiency
One of the most significant advantages of smart factories is their ability to enhance operational efficiency.
Automated systems can operate continuously without the need for breaks, thus increasing production rates.
Moreover, these systems can optimize the use of raw materials, reducing waste and saving costs.
Improved Quality Control
Smart factories employ advanced monitoring systems to ensure that products meet high-quality standards.
Sensors and cameras can detect defects early in the production process, allowing for immediate corrections.
This level of quality control helps in reducing the rate of defective products, thereby improving overall product quality.
Predictive Maintenance
Predictive maintenance uses AI and machine learning to forecast equipment failures before they occur.
By analyzing data from sensors placed on machinery, smart factories can predict when a piece of equipment is likely to fail.
This proactive approach prevents costly downtime and extends the lifespan of machines.
Flexibility and Adaptability
Traditional factories often struggle to adapt to new production demands quickly.
In contrast, smart factories are designed to be highly flexible.
Automated systems can be reprogrammed to handle different tasks, allowing manufacturers to respond swiftly to market changes or new product lines.
Key Technologies Powering Smart Factories
Internet of Things (IoT)
The IoT is at the heart of smart factories, providing the means to connect various devices and systems.
Sensors, machines, and other equipment communicate with each other through IoT, enabling real-time data exchange and process automation.
Artificial Intelligence (AI) and Machine Learning
AI and machine learning play crucial roles in smart factories by analyzing vast amounts of data generated during production.
These technologies can identify patterns and trends, enabling predictive maintenance, optimizing production schedules, and improving overall efficiency.
Robotics and Automation
Robotics and automation are fundamental components of smart factories.
Automated robots can perform repetitive tasks with high precision, reducing the need for manual labor and minimizing human error.
These robots can also work in hazardous environments, improving workplace safety.
Big Data and Analytics
Smart factories generate enormous amounts of data, often referred to as big data.
Advanced analytics tools can process this data to gain insights into production performance, identify bottlenecks, and make data-driven decisions.
These insights are invaluable for optimizing operations and maintaining a competitive edge.
Challenges in Implementing Smart Factories
High Initial Costs
The transition to a smart factory requires significant investment in new technologies and infrastructure.
This can be a barrier, especially for small and medium-sized enterprises (SMEs) with limited budgets.
However, the long-term benefits often outweigh the initial costs.
Data Security Concerns
With the increasing reliance on digital technologies, data security becomes a critical concern.
Smart factories must implement robust cybersecurity measures to protect sensitive information and prevent potential cyberattacks.
Skilled Workforce
The successful operation of a smart factory depends on a skilled workforce that can manage and maintain advanced systems.
Companies may need to invest in training programs to upskill their employees or hire new talent with expertise in emerging technologies.
Steps to Realize Smart Factories
Assessment and Planning
The journey towards a smart factory begins with a comprehensive assessment of the current production setup.
Identifying areas that can benefit from automation and digitalization is crucial.
Planning should involve setting clear objectives and timelines for implementation.
Investment in Technology
Investing in the right technologies is essential.
Manufacturers should collaborate with technology providers to source suitable equipment and software.
Pilot programs can test new systems on a smaller scale before full deployment.
Employee Training
A well-trained workforce is vital for the success of a smart factory.
Companies should offer ongoing training and development opportunities to ensure that employees are proficient in using new technologies.
This investment in human capital can significantly enhance productivity and innovation.
Continuous Improvement
Smart factories are not a one-time implementation.
Continuous improvement is key to maintaining efficiency and staying competitive.
Regularly reviewing performance metrics, adopting new advancements, and refining processes will ensure long-term success.
Conclusion
The realization of smart factories represents a transformative shift in the manufacturing industry.
By leveraging advanced technologies like IoT, AI, and robotics, manufacturers can achieve unprecedented levels of efficiency, quality, and flexibility.
While challenges such as high initial costs and data security must be addressed, the potential benefits make the pursuit of smart factories worthwhile.
With careful planning, investment, and ongoing improvement, the vision of fully automated, intelligent manufacturing plants can become a reality.
資料ダウンロード
QCD調達購買管理クラウド「newji」は、調達購買部門で必要なQCD管理全てを備えた、現場特化型兼クラウド型の今世紀最高の購買管理システムとなります。
ユーザー登録
調達購買業務の効率化だけでなく、システムを導入することで、コスト削減や製品・資材のステータス可視化のほか、属人化していた購買情報の共有化による内部不正防止や統制にも役立ちます。
NEWJI DX
製造業に特化したデジタルトランスフォーメーション(DX)の実現を目指す請負開発型のコンサルティングサービスです。AI、iPaaS、および先端の技術を駆使して、製造プロセスの効率化、業務効率化、チームワーク強化、コスト削減、品質向上を実現します。このサービスは、製造業の課題を深く理解し、それに対する最適なデジタルソリューションを提供することで、企業が持続的な成長とイノベーションを達成できるようサポートします。
オンライン講座
製造業、主に購買・調達部門にお勤めの方々に向けた情報を配信しております。
新任の方やベテランの方、管理職を対象とした幅広いコンテンツをご用意しております。
お問い合わせ
コストダウンが利益に直結する術だと理解していても、なかなか前に進めることができない状況。そんな時は、newjiのコストダウン自動化機能で大きく利益貢献しよう!
(Β版非公開)