- お役立ち記事
- The difference between Manufacturing Cost and Sales Cost
The difference between Manufacturing Cost and Sales Cost
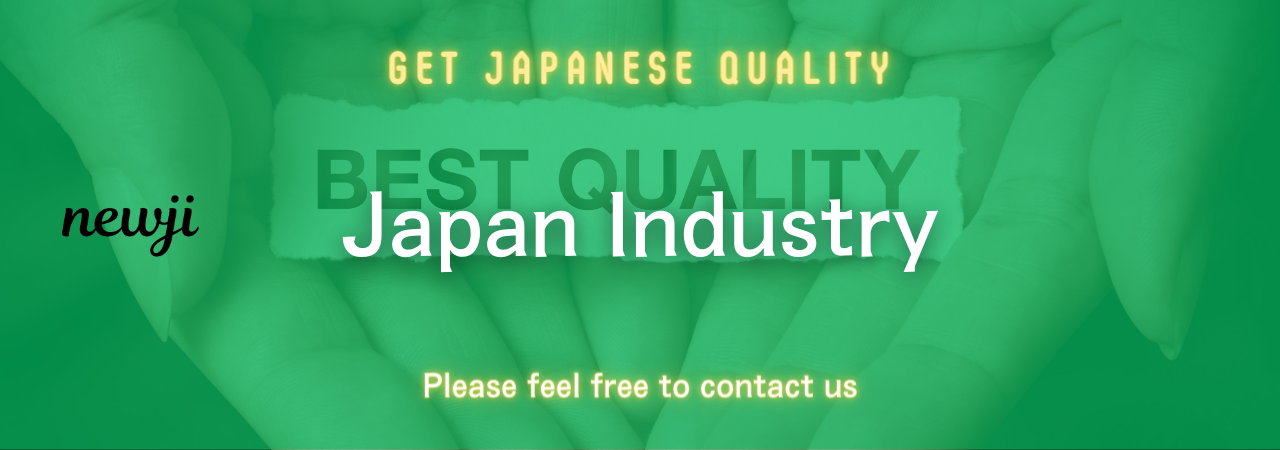
When running a business, understanding various financial aspects is crucial to maintaining profitability and ensuring long-term success.
Among these financial aspects, two important terms frequently pop up: manufacturing cost and sales cost.
Despite their seeming similarity, these two concepts represent different stages of the business process.
Knowing the difference is essential for making informed decisions.
目次
What is Manufacturing Cost?
Manufacturing cost refers to the total expenses incurred in producing a product.
These expenses are usually categorized into three segments: direct materials, direct labor, and manufacturing overhead.
Direct Materials
Direct materials are the raw components used in creating a product.
For example, the wood used to make furniture or the fabric for clothing items falls under this category.
The cost of these materials directly affects the final product’s production cost.
Direct Labor
Direct labor involves the salaries and wages of employees who are directly involved in the manufacturing process.
This includes workers operating machinery, assembling products, or working on the production line.
Their labor costs are directly tied to the number of units produced.
Manufacturing Overhead
Manufacturing overhead consists of indirect costs related to production activities but not directly traceable to a specific product.
Examples include factory rent, equipment depreciation, and utility expenses.
These costs are necessary to keep the production process running smoothly.
What is Sales Cost?
Sales cost, often referred to as the cost of goods sold (COGS), represents the total expenses involved in selling a product.
Unlike manufacturing cost, sales cost includes various factors from manufacturing to the actual sale.
Cost of Goods Sold (COGS)
COGS includes all costs directly associated with the production and sale of goods.
It comprises direct materials, direct labor, and manufacturing overhead. However, it extends further to incorporate expenses directly linked to the sale, such as packaging and freight costs.
Sales and Marketing Expenses
This category includes costs related to promoting and selling the product.
Examples are advertising expenses, sales commissions, and costs associated with marketing campaigns.
While sometimes categorized separately, they are often integrated into overall sales costs for a comprehensive view.
Distribution Costs
Distribution costs involve expenses related to getting the product to the customer.
This includes shipping, handling, and logistics costs.
These costs are essential in delivering the product but do not directly pertain to its production.
The Key Differences
While manufacturing cost and sales cost might appear to overlap, they address different aspects of a business process.
Understanding their differences can clarify your company’s financial health.
Scope of Costs
Manufacturing cost is limited to the expenses involved in producing a product.
It ends when the product is finished and ready for sale.
In contrast, sales cost encompasses a broader range of expenses, spanning from production to the moment a customer buys the product.
It includes manufacturing costs and adds marketing, distribution, and sales-related expenses.
Implications for Pricing
Determining a product’s price often begins with calculating the manufacturing cost.
Companies typically mark up this cost to ensure profitability. However, to set competitive prices, businesses must also consider sales costs.
If you only account for manufacturing costs, there’s a risk of underpricing your products, leading to potential losses.
Incorporating sales costs ensures a more holistic approach to pricing, safeguarding your profit margins.
Impact on Financial Statements
Manufacturing costs primarily impact the cost of inventory on the balance sheet.
These costs accumulate in the inventory account until the products are sold.
Sales costs, including COGS, show up on the income statement.
They directly affect the profit margins and indicate how efficiently a company converts resources into income.
Why Understanding the Difference Matters
Grasping the distinction between manufacturing and sales costs provides significant advantages.
It allows business owners to make well-informed financial decisions, set appropriate pricing strategies, and effectively allocate resources.
Improved Cost Control
By breaking down costs into respective categories, you can better manage and control your expenses.
Knowing the exact manufacturing cost helps identify inefficiencies in the production process.
Similarly, understanding sales costs enables you to optimize marketing and distribution efforts.
Enhanced Financial Planning
Clear knowledge of manufacturing and sales costs aids in accurate budgeting and financial forecasting.
This ensures that you set realistic financial goals and allocate resources effectively.
Such planning is essential for sustaining growth and competing in the market.
Informed Pricing Strategy
Incorporating both manufacturing and sales costs into your pricing strategy ensures that all expenses are covered.
This approach prevents underpricing and safeguards your revenue, ensuring the financial stability of your business.
Conclusion
While manufacturing cost and sales cost are intertwined, they address different facets of the business process.
Manufacturing cost focuses on the expenses associated with creating a product, while sales cost spans from production to final sale.
Understanding this distinction is crucial for effective financial management, accurate pricing, and sustainable profitability.
By recognizing and accurately calculating these costs, business owners can make more informed decisions, ensuring the long-term success of their ventures.
資料ダウンロード
QCD調達購買管理クラウド「newji」は、調達購買部門で必要なQCD管理全てを備えた、現場特化型兼クラウド型の今世紀最高の購買管理システムとなります。
ユーザー登録
調達購買業務の効率化だけでなく、システムを導入することで、コスト削減や製品・資材のステータス可視化のほか、属人化していた購買情報の共有化による内部不正防止や統制にも役立ちます。
NEWJI DX
製造業に特化したデジタルトランスフォーメーション(DX)の実現を目指す請負開発型のコンサルティングサービスです。AI、iPaaS、および先端の技術を駆使して、製造プロセスの効率化、業務効率化、チームワーク強化、コスト削減、品質向上を実現します。このサービスは、製造業の課題を深く理解し、それに対する最適なデジタルソリューションを提供することで、企業が持続的な成長とイノベーションを達成できるようサポートします。
オンライン講座
製造業、主に購買・調達部門にお勤めの方々に向けた情報を配信しております。
新任の方やベテランの方、管理職を対象とした幅広いコンテンツをご用意しております。
お問い合わせ
コストダウンが利益に直結する術だと理解していても、なかなか前に進めることができない状況。そんな時は、newjiのコストダウン自動化機能で大きく利益貢献しよう!
(Β版非公開)