- お役立ち記事
- The difference between Resolver and Rotary Encoder
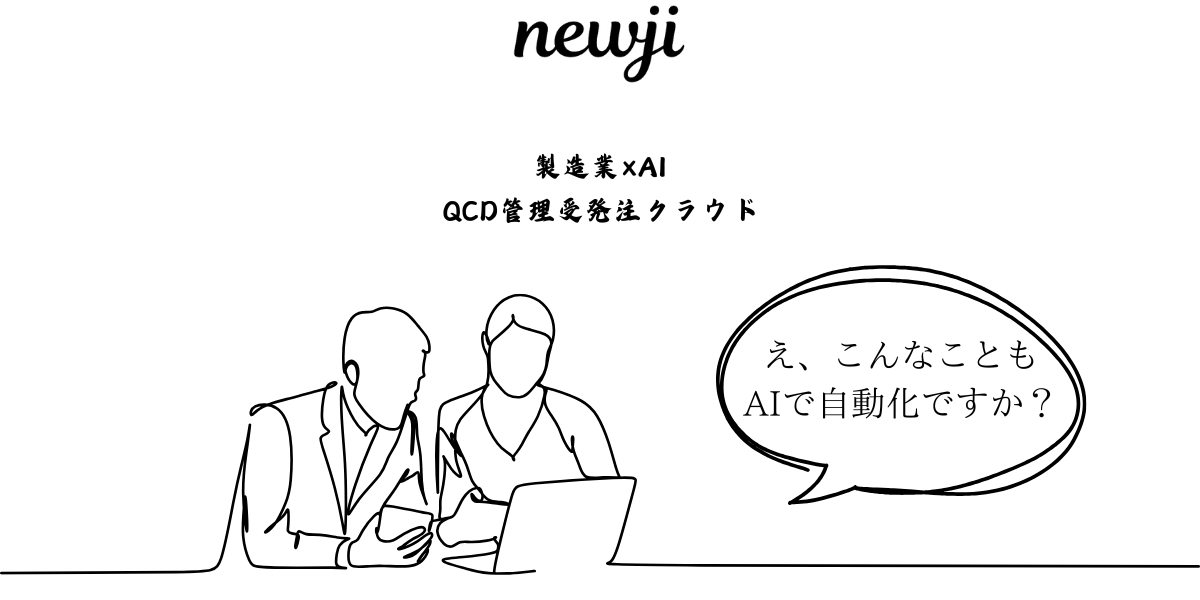
The difference between Resolver and Rotary Encoder
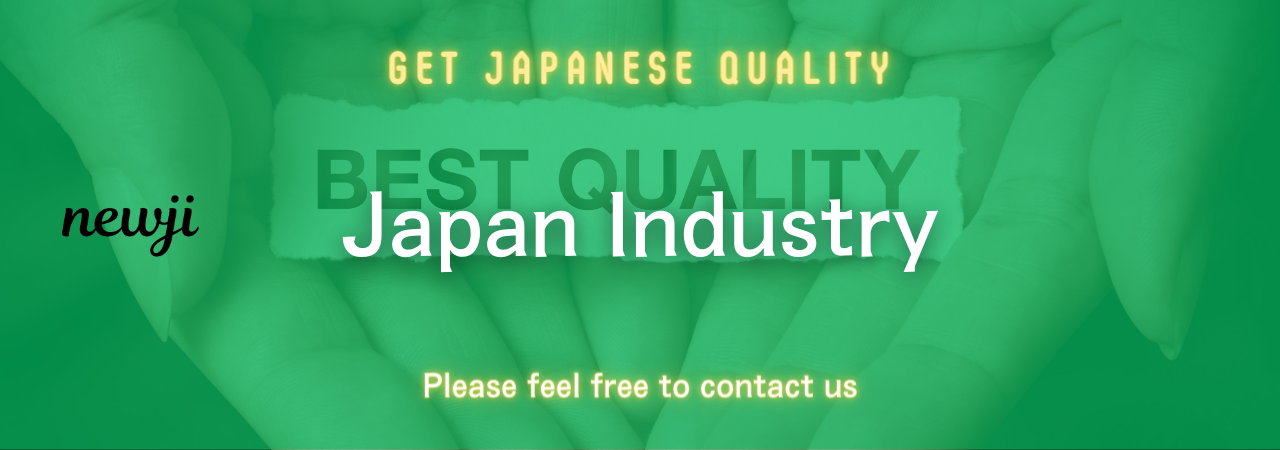
When it comes to measuring the rotation angle or position of a shaft in various industrial applications, two widely used devices are resolvers and rotary encoders.
Both serve a similar purpose, but their operating principles and applications can differ significantly.
Understanding these differences is essential to choose the right component for your specific needs.
目次
Understanding Resolver
Resolvers are analog devices that convert the angular position of a rotating shaft to an analog electrical signal.
They work on the principle of electromagnetic induction.
Resolvers consist of a stator with one primary winding and two secondary windings, typically placed 90 degrees apart.
The rotor is attached to the rotating shaft and induces a varying voltage in the secondary windings as it rotates.
The ratio of these induced voltages corresponds to the angle of rotation.
Advantages of Resolvers
Resolvers are known for their robustness and reliability, especially in harsh environments.
They can operate at high temperatures and are resistant to dust, dirt, and moisture.
They also offer continuous rotation without mechanical stops, making them ideal for applications requiring precise and uninterrupted angle measurements.
Resolvers provide absolute position feedback, meaning they can detect the precise angular position of the shaft from the moment they are powered on, eliminating the need for initialization or homing procedures.
Understanding Rotary Encoders
Rotary encoders, on the other hand, are digital devices used to convert the angular position or motion of a shaft into a digital signal.
There are two main types of rotary encoders: absolute encoders and incremental encoders.
Absolute Encoders
Absolute encoders provide a unique digital code for each angle of the shaft.
Even when the power is turned off, they retain the precise position of the shaft.
This makes them useful in applications where knowing the exact position after a power loss is critical.
Incremental Encoders
Incremental encoders generate a series of pulses as the shaft rotates.
The number of pulses per revolution (PPR) helps determine the angular position.
Unlike absolute encoders, incremental encoders do not retain position information after power loss, so they may require a homing procedure upon restart.
Advantages of Rotary Encoders
Rotary encoders offer high precision and resolution, making them suitable for applications where fine angular measurements are required.
They are typically smaller and lighter than resolvers, making them easier to integrate into compact systems.
Rotary encoders are also faster in terms of data acquisition and can provide high-speed feedback for dynamic applications.
Comparing the Two Devices
Output Signal
Resolvers provide an analog output signal, while rotary encoders provide a digital signal.
Depending on your system’s requirements, one type of output may be more beneficial than the other.
Environment and Durability
Resolvers are more robust and can withstand harsher environmental conditions than rotary encoders.
If your application is in a demanding environment, a resolver may be the better choice.
Precision and Resolution
While both devices can offer high precision, rotary encoders generally provide higher resolution, making them better suited for applications requiring detailed measurements.
Initialization and Homing
Resolvers offer absolute position feedback without needing initialization.
In contrast, incremental encoders may require homing procedures upon power-up, adding complexity to your system.
Applications of Resolvers and Rotary Encoders
Resolvers
Resolvers are common in aerospace and military applications due to their robustness and reliability.
They are also used in industrial automation and robotics, where precise angle measurement in harsh conditions is crucial.
Rotary Encoders
Rotary encoders find applications in various fields, including CNC machinery, medical devices, and robotics.
Their high resolution and precision make them ideal for tasks requiring detailed position feedback.
Absolute encoders are specifically useful in applications where the exact position data after power loss is critical.
Incremental encoders are often used in applications where continuous movement detection is necessary, such as in conveyor systems and elevator controls.
Choosing the Right Device
Selecting between a resolver and a rotary encoder depends on several factors including the operating environment, required precision, and application-specific needs.
If your application involves harsh conditions or requires absolute position feedback, a resolver could be the ideal choice.
Conversely, if high resolution and fast data acquisition are paramount, especially in less demanding environments, a rotary encoder might be more suitable.
Ultimately, understanding the key differences and applications of each device will help you make an informed decision, ensuring optimal performance and reliability in your system.
資料ダウンロード
QCD調達購買管理クラウド「newji」は、調達購買部門で必要なQCD管理全てを備えた、現場特化型兼クラウド型の今世紀最高の購買管理システムとなります。
ユーザー登録
調達購買業務の効率化だけでなく、システムを導入することで、コスト削減や製品・資材のステータス可視化のほか、属人化していた購買情報の共有化による内部不正防止や統制にも役立ちます。
NEWJI DX
製造業に特化したデジタルトランスフォーメーション(DX)の実現を目指す請負開発型のコンサルティングサービスです。AI、iPaaS、および先端の技術を駆使して、製造プロセスの効率化、業務効率化、チームワーク強化、コスト削減、品質向上を実現します。このサービスは、製造業の課題を深く理解し、それに対する最適なデジタルソリューションを提供することで、企業が持続的な成長とイノベーションを達成できるようサポートします。
オンライン講座
製造業、主に購買・調達部門にお勤めの方々に向けた情報を配信しております。
新任の方やベテランの方、管理職を対象とした幅広いコンテンツをご用意しております。
お問い合わせ
コストダウンが利益に直結する術だと理解していても、なかなか前に進めることができない状況。そんな時は、newjiのコストダウン自動化機能で大きく利益貢献しよう!
(Β版非公開)