- お役立ち記事
- Mastering Grounding: Unpacking Japanese Manufacturing Techniques for Optimal Stability and Efficiency
Mastering Grounding: Unpacking Japanese Manufacturing Techniques for Optimal Stability and Efficiency
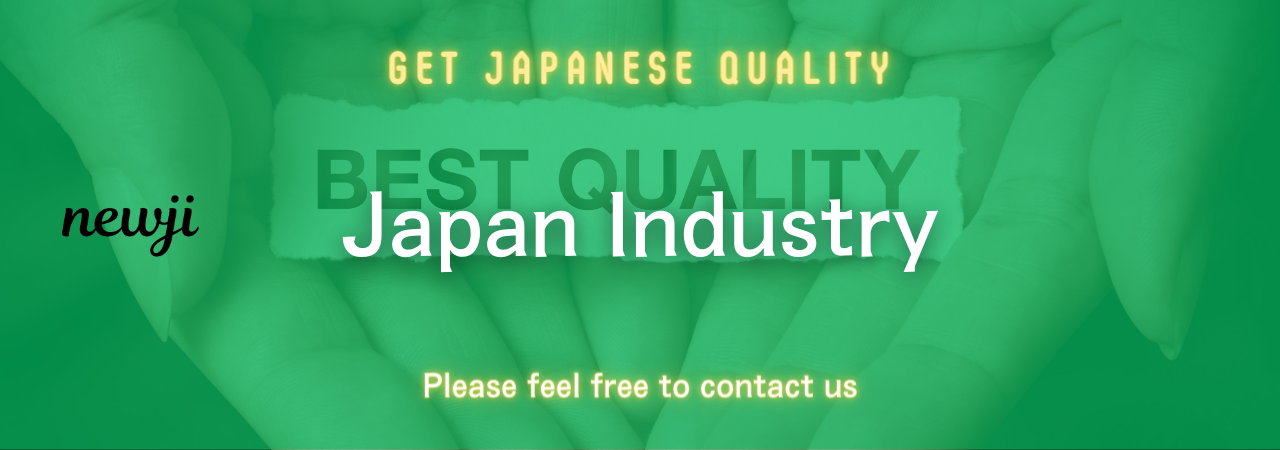
目次
Introduction
Grounding is a fundamental concept in manufacturing, particularly in ensuring the stability and efficiency of production processes. Japanese manufacturing companies have long been revered for their impeccable standards and innovative approaches. Understanding these grounding techniques not only helps in improving operational stability but also brings numerous efficiency gains. This article dives deep into mastering grounding by unpacking Japanese manufacturing techniques and providing practical insights for procurement and purchasing professionals.
Understanding Grounding in Japanese Manufacturing
The Concept of Grounding
Grounding, in the manufacturing context, refers to the processes and practices that stabilize production lines, ensuring minimal disruptions and maximum efficiency. From the precise functionality of machinery to the seamless flow of work, grounding encompasses a wide range of elements.
The Significance of Grounding
Japanese manufacturers place significant emphasis on grounding as it is crucial to maintaining high-quality production standards. Grounding practices reduce downtime, enhance the precision of manufacturing processes, and ensure the consistent quality of output. These practices contribute to Japan’s global reputation for excellence in manufacturing.
Advantages of Japanese Grounding Techniques
Precision and Consistency
Japanese manufacturing techniques are renowned for their precision. Grounding practices ensure that machinery and production lines operate at optimal settings, reducing variations and defects. This results in consistent high-quality products.
Enhanced Efficiency
By minimizing disruptions and ensuring smooth operations, grounding techniques significantly enhance manufacturing efficiency. Lean manufacturing principles, such as Just-In-Time (JIT) production and the Toyota Production System (TPS), are rooted in effective grounding practices.
Reduced Downtime
Proper grounding minimizes the risk of equipment failures and production halts. Regular maintenance and monitoring, key aspects of grounding, ensure that machinery operates smoothly, reducing downtime and boosting productivity.
Cost Savings
With increased efficiency and reduced downtime, grounding practices lead to substantial cost savings. These savings can be reinvested in further improving production processes or expanding business operations.
Challenges and Disadvantages
Initial Investment
Implementing Japanese grounding techniques can involve significant initial investment in training, equipment, and process reengineering. This can be a barrier for small to medium-sized enterprises.
Complexity
Japanese grounding techniques can be complex and require a deep understanding of manufacturing processes. This complexity necessitates specialized training and expertise, which can be time-consuming and costly.
Cultural Adaptation
Japanese manufacturing practices are often deeply rooted in the country’s culture. Adapting these practices to a different cultural context may pose challenges and require careful consideration and customization.
Supplier Negotiation Techniques
Building Strong Relationships
Japanese suppliers place a high value on long-term relationships. Building strong, trust-based relationships with suppliers can lead to better negotiation outcomes and more favorable terms. Regular communication and mutual respect are key components of this approach.
Understanding Supplier Capabilities
Before entering negotiations, thoroughly understand the supplier’s capabilities, strengths, and limitations. This knowledge allows for realistic expectations and more effective negotiation strategies.
Focus on Quality
Japanese suppliers prioritize quality over cost-cutting measures. Emphasize your commitment to quality during negotiations to align with their values and foster a collaborative approach to problem-solving.
Win-Win Solutions
Aim for win-win solutions that benefit both parties. This approach fosters long-term partnerships and encourages suppliers to go the extra mile to meet your requirements.
Documentation and Clarity
Ensure that all agreements and expectations are clearly documented. This prevents misunderstandings and establishes a clear framework for the supplier relationship.
Market Conditions
Economic Stability
Japan’s stable economy provides a reliable foundation for manufacturing operations. The country’s well-developed infrastructure and advanced technology contribute to a conducive environment for industrial activities.
Skilled Workforce
Japan boasts a highly skilled workforce with expertise in precision manufacturing. This skilled labor force ensures the consistent high quality of products and enhances overall production efficiency.
Technological Advancements
Japanese manufacturers are at the forefront of technological advancements. Leveraging cutting-edge technology, such as automation and robotics, further enhances the efficiency and effectiveness of grounding practices.
Environmental Regulations
Japan’s stringent environmental regulations promote sustainable manufacturing practices. These regulations ensure that manufacturing processes are environmentally friendly, aligning with global standards and consumer expectations.
Best Practices in Implementing Japanese Grounding Techniques
Invest in Training
Invest in training programs to ensure that your workforce understands and can effectively implement grounding practices. Continuous learning and development are essential for maintaining high standards.
Adopt Lean Manufacturing Principles
Incorporate lean manufacturing principles, such as JIT and TPS, into your operations. These principles are integral to Japanese grounding techniques and contribute significantly to overall efficiency and stability.
Regular Maintenance
Implement a rigorous maintenance schedule to prevent equipment failures and production disruptions. Regular maintenance ensures that machinery operates at optimal performance levels.
Continuous Improvement
Embrace a culture of continuous improvement (kaizen). Encourage your team to identify areas for improvement and implement changes proactively to enhance overall production processes.
Collaboration and Communication
Foster a collaborative environment where open communication is encouraged. Collaboration between different departments and with suppliers helps identify and address potential issues before they escalate.
Conclusion
Mastering grounding techniques, as exemplified by Japanese manufacturers, is crucial for achieving stability and efficiency in production processes. While initial investments and complexity may pose challenges, the long-term benefits in terms of precision, consistency, and cost savings are significant.
By building strong relationships with suppliers, understanding market conditions, and adopting best practices, procurement and purchasing professionals can leverage Japanese grounding techniques to optimize their manufacturing operations.
資料ダウンロード
QCD調達購買管理クラウド「newji」は、調達購買部門で必要なQCD管理全てを備えた、現場特化型兼クラウド型の今世紀最高の購買管理システムとなります。
ユーザー登録
調達購買業務の効率化だけでなく、システムを導入することで、コスト削減や製品・資材のステータス可視化のほか、属人化していた購買情報の共有化による内部不正防止や統制にも役立ちます。
NEWJI DX
製造業に特化したデジタルトランスフォーメーション(DX)の実現を目指す請負開発型のコンサルティングサービスです。AI、iPaaS、および先端の技術を駆使して、製造プロセスの効率化、業務効率化、チームワーク強化、コスト削減、品質向上を実現します。このサービスは、製造業の課題を深く理解し、それに対する最適なデジタルソリューションを提供することで、企業が持続的な成長とイノベーションを達成できるようサポートします。
オンライン講座
製造業、主に購買・調達部門にお勤めの方々に向けた情報を配信しております。
新任の方やベテランの方、管理職を対象とした幅広いコンテンツをご用意しております。
お問い合わせ
コストダウンが利益に直結する術だと理解していても、なかなか前に進めることができない状況。そんな時は、newjiのコストダウン自動化機能で大きく利益貢献しよう!
(Β版非公開)