- お役立ち記事
- Methods to Promote Improvement with Suppliers Through Defective Product Analysis
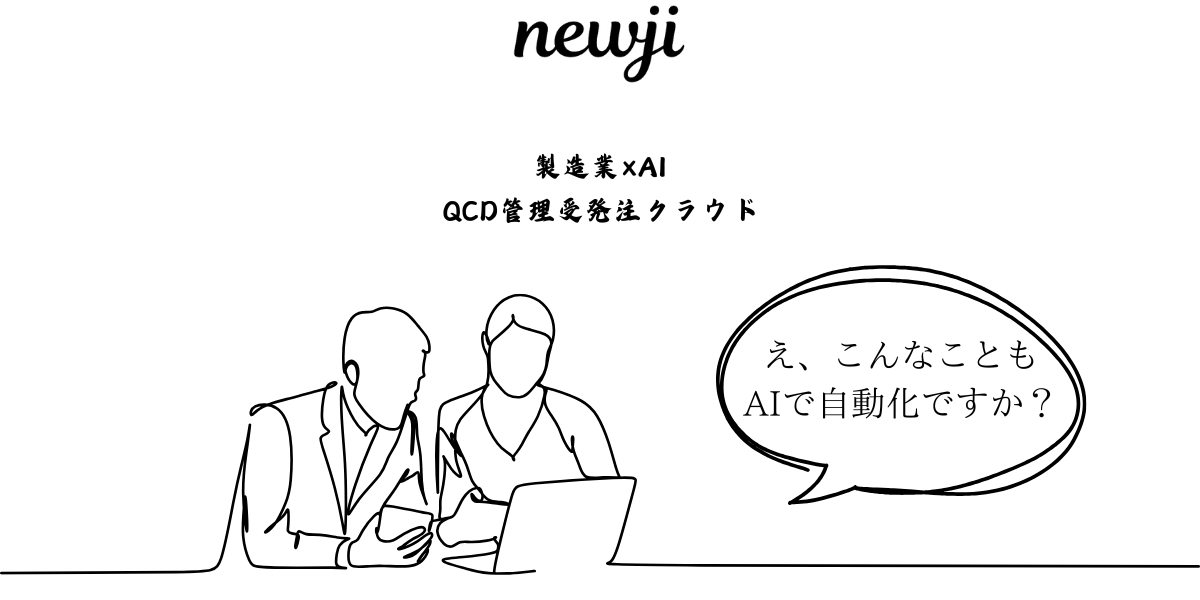
Methods to Promote Improvement with Suppliers Through Defective Product Analysis
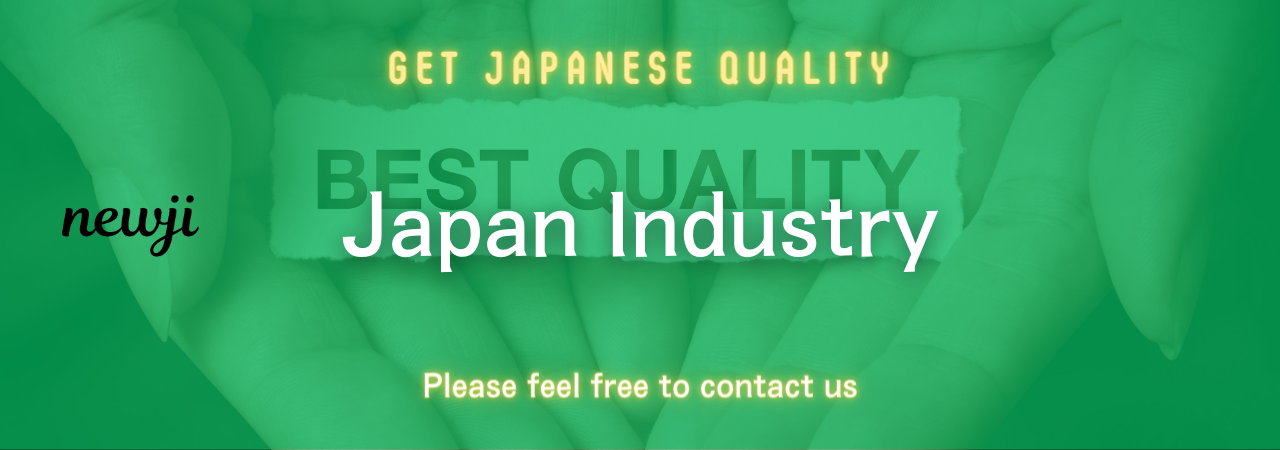
When working with suppliers, ensuring product quality is paramount. If you’re finding defects in the products delivered, it’s essential to have a strategic approach in place to address and correct these issues. Analysis of defective products can act as a critical tool in fostering improvement with suppliers. Here’s a robust approach:
目次
Understanding the Importance of Defective Product Analysis
Defective products can disrupt supply chains, increase costs, and damage business relationships. By conducting a thorough analysis, businesses can identify the root causes of defects and provide actionable insights to their suppliers. This process not only helps in resolving the current issues but also aids in preventing future occurrences.
Establishing a Clear Communication Channel
Transparency with Suppliers
Maintaining open and honest communication with suppliers is fundamentally important. When defects are identified, it’s crucial to communicate these findings promptly and transparently. Suppliers need detailed information about the nature of the defects so they can understand the implications and the required improvements.
Feedback Mechanisms
Create structured feedback mechanisms. This could include regular meetings, reports, and real-time updates. Use these platforms to share the analysis of defective products and collaboratively develop improvement plans. Consistent feedback ensures suppliers remain aware of performance metrics and areas needing attention.
Utilizing Data for Accurate Analysis
Collecting Detailed Defect Data
To identify and rectify defects, gathering comprehensive data is essential. Document every aspect of the defective products, including the type of defect, its frequency, and the potential impact on the end product. Use a standardized format to collect this data, ensuring consistency and reliability.
Analyzing Patterns and Root Causes
With detailed data in hand, employ statistical tools and techniques to analyze patterns. Look for recurring issues and identify any common factors that might be contributing to these defects. Root cause analysis methods, such as the Fishbone Diagram and 5 Whys, can be particularly effective in pinpointing underlying issues.
Implementing Corrective Actions
Collaborative Problem-Solving
Work closely with your suppliers to develop and implement corrective actions. This collaborative approach fosters a sense of partnership and shared responsibility. Brainstorm potential solutions together, considering both immediate fixes and long-term strategies. Ensure your suppliers are fully involved in this process and understand the rationale behind each action.
Monitoring and Evaluation
Once corrective actions are in place, it’s vital to monitor their effectiveness. Set clear metrics to evaluate whether the implemented solutions are delivering the desired improvements. Regularly review these metrics with your suppliers to ensure ongoing progress and to make any necessary adjustments.
Training and Support
Providing Necessary Resources
In some cases, defects might stem from a lack of resources or expertise at the supplier’s end. Providing necessary training and support can be incredibly beneficial. Organize workshops, share best practices, and offer technical assistance to help suppliers enhance their processes and eliminate defects.
Encouraging Continuous Improvement
Promote a culture of continuous improvement among your suppliers. Encourage them to regularly assess their processes, invest in quality control measures, and innovate to prevent defects. Recognizing and rewarding suppliers who show significant improvement can also motivate others to strive for excellence.
Building Strong Relationships with Suppliers
Trust and Collaboration
Strong relationships built on trust and collaboration are essential for successful supplier management. When suppliers feel valued and trusted, they are more likely to commit to quality improvements. Regularly engage with your suppliers, not only when issues arise but also to share successes and future goals.
Shared Goals and Objectives
Aligning on shared goals and objectives is another important aspect. Make sure your suppliers understand your quality standards and expectations. Work together to set mutual targets for improvement and establish a shared vision for success. This alignment fosters a sense of partnership and mutual accountability.
Utilizing Technology for Better Management
Quality Management Systems (QMS)
Implementing a robust Quality Management System (QMS) can streamline the process of analyzing defects and managing supplier performance. QMS platforms offer tools for tracking defect data, managing corrective actions, and ensuring compliance with quality standards. They also facilitate better communication and collaboration between you and your suppliers.
Supply Chain Management Tools
Use advanced supply chain management tools to enhance oversight and control. These tools can provide real-time visibility into the supply chain, helping you detect defects early and manage supplier performance more effectively. Leveraging technology can significantly reduce the occurrence of defects and boost overall supply chain efficiency.
The Role of Audits and Inspections
Regular Audits
Conduct regular audits of your suppliers’ facilities and processes. These audits can uncover potential issues before they lead to defects. Ensure that your audits are comprehensive and cover critical aspects such as production processes, quality control measures, and compliance with standards.
Unannounced Inspections
In addition to scheduled audits, consider unannounced inspections. These inspections provide a more accurate picture of the daily operations at your suppliers’ facilities. They can be particularly effective in identifying hidden issues and ensuring that quality standards are consistently maintained.
Conclusion: The Path to Quality Improvement
Addressing defective products through thorough analysis and collaboration with suppliers is a strategic approach to quality improvement. By establishing clear communication channels, utilizing detailed data, implementing corrective actions, providing support and training, and building strong relationships, businesses can work with suppliers to achieve higher quality standards. Leveraging technology and conducting regular audits further enhances this process, ensuring that defects are minimized and quality is optimized.
The journey to supplier improvement is ongoing and requires commitment from both parties. By fostering a culture of continuous improvement and collaboration, businesses can not only rectify current defects but also prevent future issues, leading to a more efficient and reliable supply chain.
資料ダウンロード
QCD調達購買管理クラウド「newji」は、調達購買部門で必要なQCD管理全てを備えた、現場特化型兼クラウド型の今世紀最高の購買管理システムとなります。
ユーザー登録
調達購買業務の効率化だけでなく、システムを導入することで、コスト削減や製品・資材のステータス可視化のほか、属人化していた購買情報の共有化による内部不正防止や統制にも役立ちます。
NEWJI DX
製造業に特化したデジタルトランスフォーメーション(DX)の実現を目指す請負開発型のコンサルティングサービスです。AI、iPaaS、および先端の技術を駆使して、製造プロセスの効率化、業務効率化、チームワーク強化、コスト削減、品質向上を実現します。このサービスは、製造業の課題を深く理解し、それに対する最適なデジタルソリューションを提供することで、企業が持続的な成長とイノベーションを達成できるようサポートします。
オンライン講座
製造業、主に購買・調達部門にお勤めの方々に向けた情報を配信しております。
新任の方やベテランの方、管理職を対象とした幅広いコンテンツをご用意しております。
お問い合わせ
コストダウンが利益に直結する術だと理解していても、なかなか前に進めることができない状況。そんな時は、newjiのコストダウン自動化機能で大きく利益貢献しよう!
(Β版非公開)