- お役立ち記事
- Manufacturing Process of Burners and Combustion Efficiency Enhancement
Manufacturing Process of Burners and Combustion Efficiency Enhancement
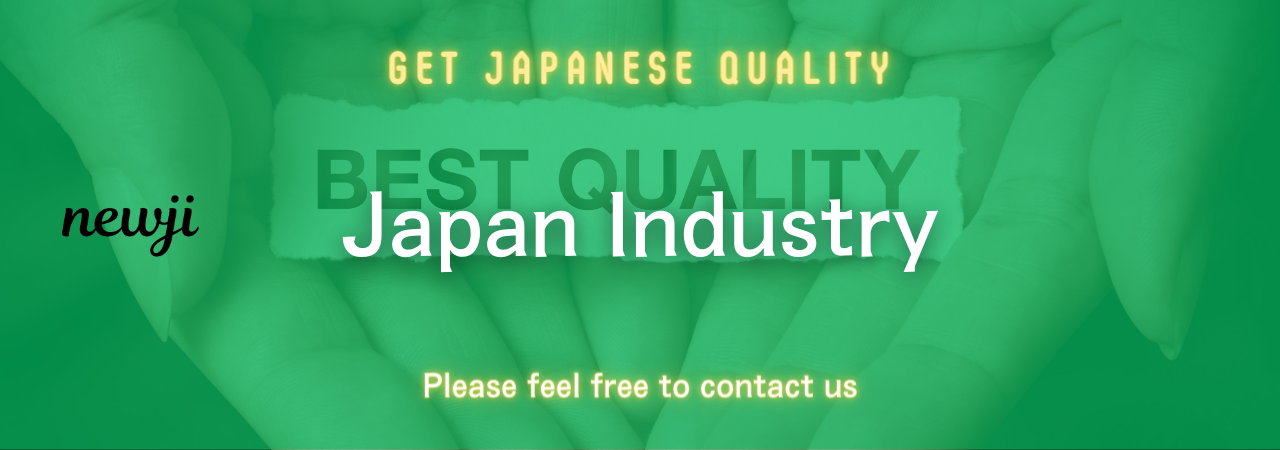
Burners play a crucial role in various industrial processes, including in heating systems, boilers, and furnaces.
Manufacturing burners requires a meticulous process to ensure they operate efficiently and safely.
Combustion efficiency enhancement is also vital for reducing energy consumption and minimizing emissions.
Let’s explore the manufacturing process of burners and the methods used to enhance combustion efficiency.
目次
Material Selection for Burners
Choosing the Right Metals and Alloys
The first step in manufacturing burners is selecting suitable materials.
High-temperature applications require materials resistant to heat and corrosion.
Common materials used include stainless steel, cast iron, and specialized alloys.
Stainless steel is favored for its durability and resistance to oxidation.
Cast iron is known for its excellent heat retention and ability to withstand high temperatures.
Specialized alloys, such as Inconel, are used in extreme conditions due to their superior resistance to thermal fatigue.
Importance of Material Quality
The quality of the materials chosen can significantly impact the performance and lifespan of the burner.
Therefore, manufacturers must work with reputable suppliers and perform rigorous quality checks.
Materials should be certified to meet industry standards and specifications.
Any compromise on material quality can lead to premature failure or inefficient combustion.
Design and Engineering
Creating Efficient Burner Designs
The design phase is critical to the manufacturing process.
Engineers use advanced software to create burner designs that maximize combustion efficiency.
Key factors considered include the shape of the burner, the size of the combustion chamber, and the distribution of air and fuel.
Computer-aided design (CAD) software allows for precise modeling and simulation, ensuring optimal performance.
Innovative Features for Better Combustion
Modern burner designs often incorporate innovative features to enhance combustion.
For example, swirl stabilizers are used to mix air and fuel more effectively, resulting in complete combustion.
Preheated air systems can improve efficiency by reducing the energy required to reach combustion temperatures.
Additionally, some designs include sensors and controls that monitor and adjust the combustion process in real-time.
Manufacturing Process
Fabrication and Assembly
Once the design is finalized, the manufacturing process begins with fabrication.
This involves cutting, shaping, and welding the chosen materials to form the burner components.
Advanced techniques, such as laser cutting and automated welding, ensure precision and consistency.
After fabrication, the components are assembled to create the finished burner.
Quality Control and Testing
Quality control is an essential part of the manufacturing process.
Each burner undergoes rigorous testing to ensure it meets performance and safety standards.
Tests include checking for leaks, verifying combustion efficiency, and ensuring proper functionality of all controls.
Burners that pass these tests are then cleaned, painted, and prepared for shipment.
Combustion Efficiency Enhancement
Proper Air-to-Fuel Ratio
One of the most effective ways to enhance combustion efficiency is by maintaining the correct air-to-fuel ratio.
Burners must mix air and fuel in precise proportions to achieve complete combustion.
Too much or too little air can lead to inefficient combustion and increased emissions.
Modern burners often include automated controls that monitor and adjust the air-to-fuel ratio in real-time.
Regular Maintenance and Upgrades
Regular maintenance is crucial for maintaining combustion efficiency.
This includes cleaning burner components, inspecting for wear and tear, and calibrating controls.
Upgrading to newer, more efficient burners can also result in significant energy savings and reduced emissions.
Manufacturers offer retrofit solutions that allow older burners to be updated with the latest technology.
Using Advanced Technology
Technological advancements have greatly improved combustion efficiency.
For example, combustion analyzers can provide real-time data on burner performance, allowing for immediate adjustments.
Flue gas recirculation systems can reduce emissions by recirculating exhaust gases back into the combustion process.
Incorporating these technologies can lead to more efficient and environmentally friendly burner operation.
Environmental Impact
Reducing Emissions
Improving combustion efficiency not only saves energy but also reduces harmful emissions.
Efficient burners produce fewer pollutants, such as carbon monoxide (CO) and nitrogen oxides (NOx).
This contributes to cleaner air and helps industries comply with environmental regulations.
Manufacturers are continually developing new technologies to further reduce emissions and improve efficiency.
Energy Conservation
Enhanced combustion efficiency directly translates to energy conservation.
More efficient burners require less fuel, resulting in lower operational costs.
This is particularly important for industries that rely heavily on heating and combustion processes.
By investing in efficient burners, companies can achieve significant cost savings while also supporting sustainability initiatives.
Conclusion
The manufacturing process of burners involves careful material selection, innovative design, precise fabrication, and rigorous quality control.
Enhancing combustion efficiency is essential for reducing energy consumption and minimizing emissions.
By maintaining the proper air-to-fuel ratio, performing regular maintenance, and utilizing advanced technologies, manufacturers can create burners that operate efficiently and sustainably.
Improving combustion efficiency not only benefits the environment but also offers significant economic advantages for industries relying on burners.
資料ダウンロード
QCD調達購買管理クラウド「newji」は、調達購買部門で必要なQCD管理全てを備えた、現場特化型兼クラウド型の今世紀最高の購買管理システムとなります。
ユーザー登録
調達購買業務の効率化だけでなく、システムを導入することで、コスト削減や製品・資材のステータス可視化のほか、属人化していた購買情報の共有化による内部不正防止や統制にも役立ちます。
NEWJI DX
製造業に特化したデジタルトランスフォーメーション(DX)の実現を目指す請負開発型のコンサルティングサービスです。AI、iPaaS、および先端の技術を駆使して、製造プロセスの効率化、業務効率化、チームワーク強化、コスト削減、品質向上を実現します。このサービスは、製造業の課題を深く理解し、それに対する最適なデジタルソリューションを提供することで、企業が持続的な成長とイノベーションを達成できるようサポートします。
オンライン講座
製造業、主に購買・調達部門にお勤めの方々に向けた情報を配信しております。
新任の方やベテランの方、管理職を対象とした幅広いコンテンツをご用意しております。
お問い合わせ
コストダウンが利益に直結する術だと理解していても、なかなか前に進めることができない状況。そんな時は、newjiのコストダウン自動化機能で大きく利益貢献しよう!
(Β版非公開)