- お役立ち記事
- Manufacturing Process of Electric Drills and Motor Assembly
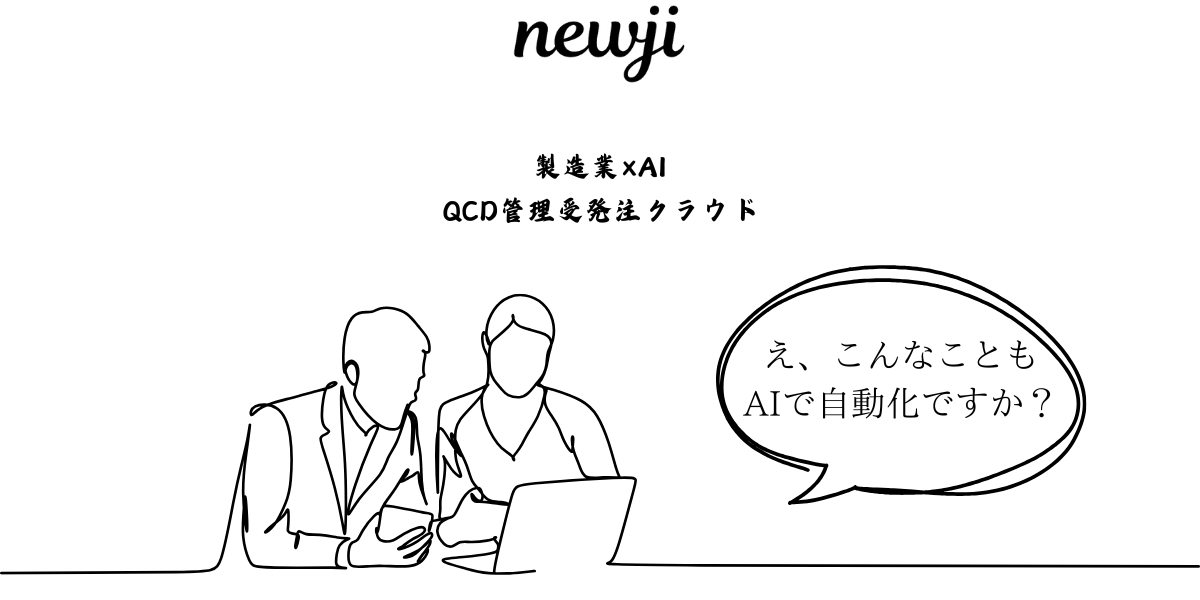
Manufacturing Process of Electric Drills and Motor Assembly
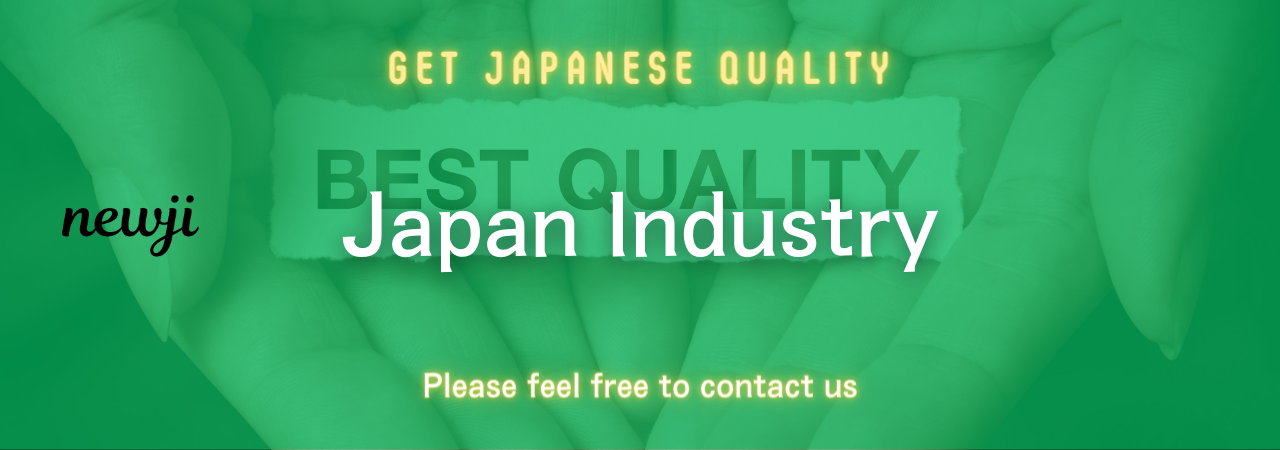
Electric drills are essential tools for both professionals and DIY enthusiasts.
Understanding the manufacturing process of electric drills and their motor assembly can give you a better appreciation of the technology that makes these tools so effective.
目次
Introduction to Electric Drills
An electric drill is a versatile power tool that uses an electric motor to rotate a drill bit, allowing users to bore holes in various materials such as wood, metal, and plastic.
Electric drills come in different models and sizes, catering to a wide range of applications.
From cordless to corded versions, each type has unique components and assemblies that contribute to its functionality.
Design and Planning
Conceptualization and Design
Every electric drill starts with a design phase where engineers and designers conceptualize the product.
They consider factors like ergonomics, power, weight, and durability to design a drill that meets user needs.
Computer-Aided Design (CAD) software is often employed to create detailed blueprints of the drill and its components.
These blueprints include dimensions, materials, and specifications for each component.
Prototyping
Once the design is finalized, a prototype is created to test the functionality and ergonomics of the drill.
Prototyping involves producing a few units and subjecting them to rigorous tests to identify any shortcomings.
These tests help ensure the drill meets safety standards and performance benchmarks.
Based on the prototype testing, necessary modifications are made before advancing to full-scale production.
Manufacturing the Components
Plastic and Metal Parts
The outer casing of the electric drill is typically made from durable plastic.
This casing not only houses the internal components but also protects them from dust and damage.
The plastic parts are manufactured using injection molding.
Molten plastic is injected into a mold where it cools and hardens into the desired shape.
Metal parts, such as gears and shafts, are produced through processes like casting, forging, and machining.
Machining involves cutting and shaping the metal to precise dimensions.
High-quality steel and aluminum are often used for their strength and durability.
Motor Assembly
The electric motor is the heart of the drill and is manufactured separately before being assembled into the drill.
Electric motors for drills are typically either brushed motors or brushless motors.
Brushed Motor Assembly
Brushed motors consist of several key components: the stator, rotor, commutator, and brushes.
The stator is a stationary part that provides a magnetic field.
The rotor, which rotates, is made up of coils of wire that carry an electric current.
The commutator and brushes work together to switch the direction of the current, causing the rotor to spin.
During assembly, the stator is first wound with copper wire to create the electromagnetic field.
The rotor is then fitted with the commutator, and the entire assembly is aligned and balanced.
Brushes are attached to ensure they maintain contact with the commutator.
The assembled motor is tested to ensure it operates smoothly and efficiently.
Brushless Motor Assembly
Brushless motors, on the other hand, utilize electronic controllers instead of brushes and commutators.
They are generally more efficient and have a longer lifespan compared to brushed motors.
The stator in a brushless motor is typically made of laminated steel and is wound with copper wire.
Permanent magnets are attached to the rotor.
An electronic controller regulates the current flow to the motor, ensuring smooth operation.
Assembling the Electric Drill
Combining the Components
With all the individual components manufactured and tested, the assembly process begins.
The first step involves installing the motor into the plastic casing.
The motor is securely fastened, and electrical connections are made.
Next, the gears and transmission system are assembled.
These components transfer the motor’s rotational energy to the drill bit.
The transmission system often includes a clutch mechanism, allowing users to adjust the torque settings of the drill.
Wiring and Controls
The wiring and control components, including the trigger switch and speed control, are then installed.
The wiring must be carefully routed and secured to prevent any interference with moving parts.
The trigger switch is connected to the motor, allowing users to control the drill’s speed and rotation.
Final Assembly and Testing
Once all components are in place, the outer casing is closed and secured with screws.
The assembled drill undergoes a series of quality control tests to ensure it meets all specifications.
These tests include checking the drill’s speed, torque, and overall functionality.
Packaging and Distribution
After passing the quality control tests, the drills are cleaned and prepared for packaging.
Each drill is packed along with its accessories, such as drill bits, chargers (for cordless models), and user manuals.
The packaged drills are then distributed to retailers and customers.
Understanding the manufacturing process of electric drills and their motor assembly highlights the precision and complexity involved in creating these essential tools.
From design and prototyping to component manufacturing and final assembly, each step is crucial to producing a high-quality electric drill.
Whether you’re a professional contractor or a DIY enthusiast, knowing what goes into making your drill can give you a greater appreciation for its capabilities and reliability.
資料ダウンロード
QCD調達購買管理クラウド「newji」は、調達購買部門で必要なQCD管理全てを備えた、現場特化型兼クラウド型の今世紀最高の購買管理システムとなります。
ユーザー登録
調達購買業務の効率化だけでなく、システムを導入することで、コスト削減や製品・資材のステータス可視化のほか、属人化していた購買情報の共有化による内部不正防止や統制にも役立ちます。
NEWJI DX
製造業に特化したデジタルトランスフォーメーション(DX)の実現を目指す請負開発型のコンサルティングサービスです。AI、iPaaS、および先端の技術を駆使して、製造プロセスの効率化、業務効率化、チームワーク強化、コスト削減、品質向上を実現します。このサービスは、製造業の課題を深く理解し、それに対する最適なデジタルソリューションを提供することで、企業が持続的な成長とイノベーションを達成できるようサポートします。
オンライン講座
製造業、主に購買・調達部門にお勤めの方々に向けた情報を配信しております。
新任の方やベテランの方、管理職を対象とした幅広いコンテンツをご用意しております。
お問い合わせ
コストダウンが利益に直結する術だと理解していても、なかなか前に進めることができない状況。そんな時は、newjiのコストダウン自動化機能で大きく利益貢献しよう!
(Β版非公開)