- お役立ち記事
- Explaining the Workflow of CNC Machining for Metal Part Manufacturing
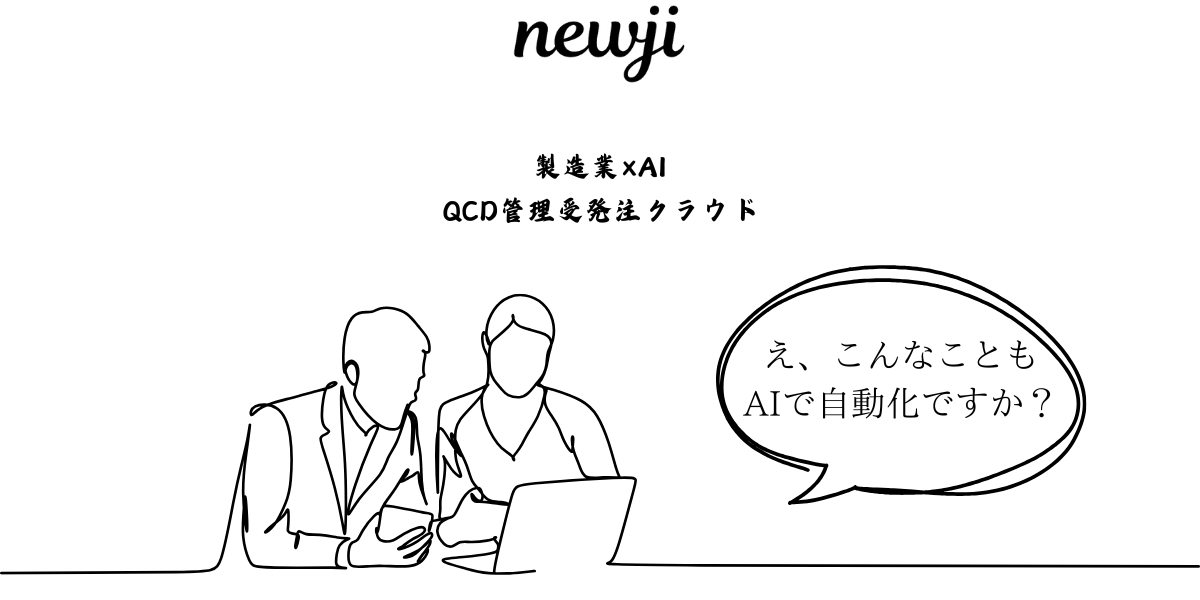
Explaining the Workflow of CNC Machining for Metal Part Manufacturing
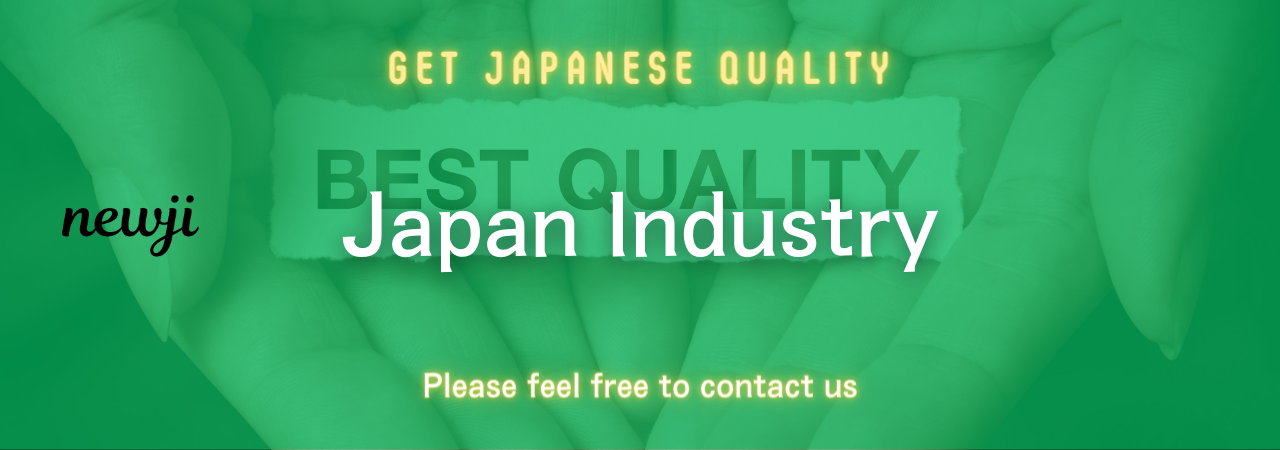
Computer Numerical Control (CNC) machining is a fascinating method used in metal part manufacturing.
By using computers to control machinery, CNC machining achieves highly precise, efficient, and repeatable production.
Let’s dive deep into the intricacies of this process and explore its workflow.
目次
What is CNC Machining?
CNC machining is a manufacturing process where pre-programmed computer software dictates the movement of factory tools and machinery.
This control over complex machinery allows for intricate operations to be executed with pinpoint accuracy.
The equipment can include grinders, lathes, mills, and routers, which are essential in crafting various metal parts.
Importance of CNC Machining in Manufacturing
Before discussing the workflow, it’s essential to understand why CNC machining is so crucial.
The automation provided by CNC machinery minimizes human error, optimizing labor and reducing waste.
This results in consistent and high-quality products, ensuring that every piece meets stringent specifications.
Step-by-Step Workflow of CNC Machining
The CNC machining process follows a defined workflow, beginning with design and ending with the finished product.
Step 1: Designing the CAD Model
The first step is creating a detailed design of the part using Computer-Aided Design (CAD) software.
Engineers convert ideas into digital models, showing every intricate detail and dimension of the intended part.
This 3D rendering helps in visualizing and perfecting the design before any physical manufacturing begins.
Step 2: Converting CAD to CNC Program
Once the design is finalized, the CAD model needs to be converted into a CNC-compatible format, usually through CAM (Computer-Aided Manufacturing) software.
The CAM software translates the CAD model into numerical codes and instructions.
These codes dictate the machine’s movements, specifying paths, speeds, and tools.
Step 3: Preparing the CNC Machine
Next, the CNC setup phase begins.
Technicians prepare the CNC machine by selecting the appropriate clamps, fixtures, and cutting tools based on the project requirements.
They also insert the raw material, typically in the form of metal blocks or bars, into the machine.
Step 4: Executing the Machining Process
Once the machine is set up and calibrated, the CNC program is loaded.
Operators then initiate the machining process, allowing the CNC machine to carve out the metal part from the raw material.
This can involve multiple operations like drilling, cutting, milling, and grinding.
The combination of movements and tool changes ensures that the final product meets the design specifications.
Step 5: Monitoring and Quality Control
Throughout the machining process, continuous monitoring is vital.
Operators watch the procedure and make necessary adjustments in real-time to ensure accuracy.
Once machining is complete, a rigorous inspection process follows.
Parts are measured against the original design using precise tools like calipers and coordinate measuring machines (CMM).
Any deviations or defects are corrected immediately to maintain high standards.
Step 6: Post-Processing and Finishing
After the primary machining steps, additional post-processing tasks might be necessary.
These could include deburring, polishing, and surface treatments to enhance the part’s appearance and functionality.
Post-processing ensures the final product is not only precise but also ready for its intended application.
Different Types of CNC Machines
Understanding the types of CNC machines is pivotal in appreciating their diverse applications in metal part manufacturing.
CNC Milling Machines
CNC milling machines are perhaps the most versatile.
They utilize rotary cutters to remove material from a workpiece.
These machines can move along multiple axes, allowing for complex geometries to be achieved.
CNC Lathes
CNC lathes rotate the workpiece against fixed cutting tools.
This setup is ideal for producing symmetrical parts like shafts and cylinders.
It offers high precision in turning operations.
CNC Routers
Though commonly associated with woodworking, CNC routers are also used in metalworking.
These machines follow a similar operational principle to CNC mills, aiding in the cutting and carving of metals.
Other Specialized CNC Machines
Further specialized CNC machinery includes CNC plasma cutters and CNC laser cutters.
These machines use focused energy beams to cut through metals, offering incredible accuracy and speed.
Advantages and Applications of CNC Machining
The benefits of CNC machining are vast, making it indispensable in various industries.
Advantages
The automation reduces labor costs and minimizes manual errors.
The repeatability ensures consistent quality in large production runs.
Flexibility allows for quick changes in designs or materials, adapting to different production needs.
Applications
CNC machining finds applications across multiple industries.
The automotive industry relies on it for engine parts and components.
The aerospace sector uses it for producing high-precision, lightweight parts.
Medical device manufacturers depend on it for complex surgical tools and implants.
Even the electronics industry utilizes CNC machining for housing and internal components.
The Future of CNC Machining
CNC technology continues to evolve, integrating advancements such as AI, IoT, and more sophisticated software.
Smart Manufacturing
With the advent of IoT, machines can now communicate seamlessly, optimizing the entire production line.
Predictive maintenance is becoming a reality, reducing downtime and improving efficiency.
Advanced Materials
The capability to machine advanced materials like composites, ceramics, and high-strength alloys will expand the applications even further.
Enhanced Precision
Ongoing technological improvements are expected to push precision levels to nano-scales, enhancing the quality and performance of manufactured parts.
Understanding the workflow of CNC machining reveals the intricate dance between design, machinery, and technology.
This process has transformed manufacturing, driving efficiency, precision, and innovation forward.
Whether you’re in engineering, manufacturing, or simply curious, appreciating CNC machining can open doors to understanding modern manufacturing’s future.
資料ダウンロード
QCD調達購買管理クラウド「newji」は、調達購買部門で必要なQCD管理全てを備えた、現場特化型兼クラウド型の今世紀最高の購買管理システムとなります。
ユーザー登録
調達購買業務の効率化だけでなく、システムを導入することで、コスト削減や製品・資材のステータス可視化のほか、属人化していた購買情報の共有化による内部不正防止や統制にも役立ちます。
NEWJI DX
製造業に特化したデジタルトランスフォーメーション(DX)の実現を目指す請負開発型のコンサルティングサービスです。AI、iPaaS、および先端の技術を駆使して、製造プロセスの効率化、業務効率化、チームワーク強化、コスト削減、品質向上を実現します。このサービスは、製造業の課題を深く理解し、それに対する最適なデジタルソリューションを提供することで、企業が持続的な成長とイノベーションを達成できるようサポートします。
オンライン講座
製造業、主に購買・調達部門にお勤めの方々に向けた情報を配信しております。
新任の方やベテランの方、管理職を対象とした幅広いコンテンツをご用意しております。
お問い合わせ
コストダウンが利益に直結する術だと理解していても、なかなか前に進めることができない状況。そんな時は、newjiのコストダウン自動化機能で大きく利益貢献しよう!
(Β版非公開)