- お役立ち記事
- Manufacturing Process of Acrylic Tissue Cases and Durability Enhancement
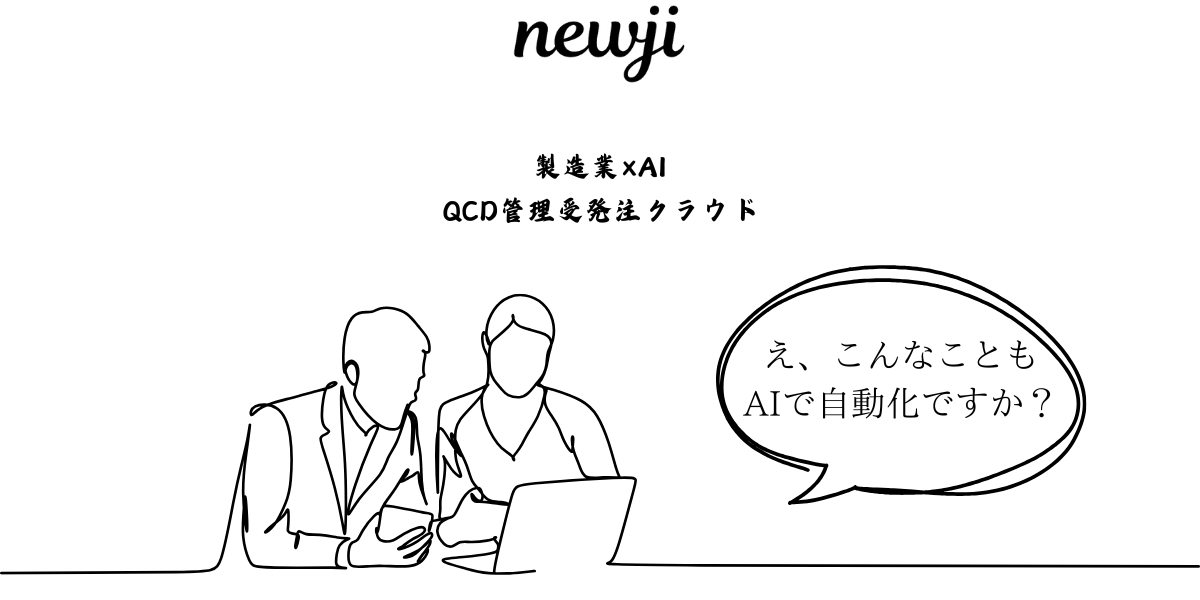
Manufacturing Process of Acrylic Tissue Cases and Durability Enhancement
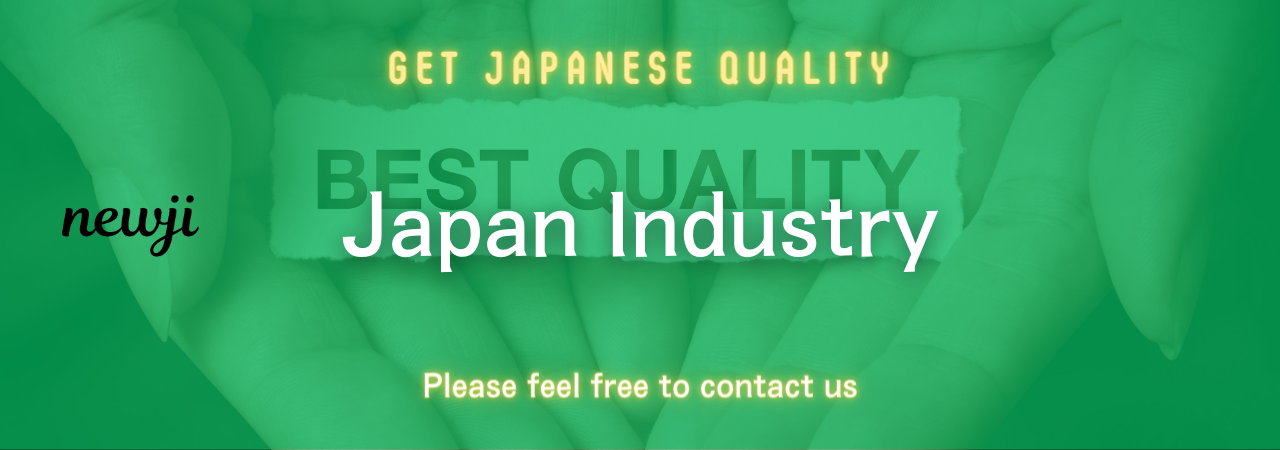
Acrylic tissue cases are a staple in many households and offices due to their sleek, modern look and practical functionality.
Understanding the manufacturing process of these versatile items, as well as how manufacturers ensure their durability, can provide consumers with a better appreciation of these everyday objects.
This article aims to explore both aspects in detail.
目次
Understanding Acrylic Material
What is Acrylic?
Acrylic, also known as polymethyl methacrylate (PMMA), is a transparent thermoplastic often used as a lightweight or shatter-resistant alternative to glass.
It is characterized by its excellent optical clarity, resistance to UV rays, and ability to be formed into various shapes.
Acrylic is a popular choice for making tissue cases because it combines aesthetic appeal with robustness.
Manufacturing Process of Acrylic Tissue Cases
Design and Prototyping
The first step in manufacturing acrylic tissue cases is designing and creating prototypes.
Designers use computer-aided design (CAD) software to create models that will be used to produce the molds.
Prototyping is essential to ensure that the case fits the functional dimensions and meets aesthetic standards.
During this phase, designers can experiment with different shapes, colors, and features.
Molding and Shaping
Once the design is finalized, the next step is to prepare the molds.
These molds are typically made of metal and are precision-engineered to replicate the design accurately.
Acrylic sheets or pellets are then heated to a molten state and injected into the molds using injection molding or cast molding techniques.
The material cools and hardens into the desired shape.
Cutting and Trimming
After the acrylic has cooled and solidified, it is removed from the mold and subjected to cutting and trimming processes.
Excess material is trimmed away, and any rough edges are smoothed out.
Advanced laser-cutting technology is often used to achieve high precision and clean edges.
This ensures that each tissue case is uniform and free from imperfections.
Polishing and Finishing
Polishing and finishing are crucial to achieving the clear, glass-like appearance that acrylic is known for.
The acrylic cases are polished using various methods, including mechanical buffing and chemical treatments, to remove any surface scratches and enhance their transparency.
During this stage, manufacturers may also add any additional features, such as engraved logos or custom designs.
Quality Control
Before the acrylic tissue cases can be packed and shipped out, they undergo a rigorous quality control process.
This involves visual inspections and functional tests to ensure that the cases meet the required standards.
Any defective products are rejected or sent back for rework.
Quality control ensures that customers receive high-quality, durable products.
Enhancing Durability of Acrylic Tissue Cases
Material Selection
One of the most important factors in enhancing the durability of acrylic tissue cases is the selection of high-quality acrylic material.
Premium-grade PMMA is more resistant to cracking, yellowing, and other forms of wear and tear.
Manufacturers often source their acrylic from reputable suppliers to ensure consistency and quality.
UV and Scratch Resistance
Acrylic is naturally resistant to UV rays, but additional treatments can further enhance this property.
UV-resistant coatings can be applied to the surface of the acrylic to protect it from prolonged exposure to sunlight, which can cause degradation and discoloration.
Similarly, scratch-resistant coatings can be added to improve the longevity of the case and maintain its pristine appearance over time.
Reinforced Edges and Corners
Edges and corners are the most vulnerable parts of any acrylic product.
Manufacturers often take extra measures to reinforce these areas to prevent chipping and cracking.
This may involve using thicker acrylic sheets for these parts or incorporating additional structural supports in the design.
Reinforced edges and corners greatly enhance the overall durability of the tissue case.
Anti-Yellowing Agents
Over time, exposure to light and environmental factors can cause acrylic to yellow.
To combat this, manufacturers incorporate anti-yellowing agents into the acrylic during the production process.
These agents help maintain the material’s clear appearance and extend the life of the product.
Regular maintenance, such as cleaning with non-abrasive cloths and mild detergents, also plays a role in preventing yellowing.
Conclusion
The manufacturing process of acrylic tissue cases involves several meticulous steps, from design and prototyping to molding, cutting, and finishing.
Quality control ensures that the final products meet high standards.
Durability is enhanced through material selection, protective coatings, reinforced edges, and anti-yellowing agents.
Understanding these processes helps consumers appreciate the complexity and care involved in creating these functional and aesthetically pleasing items.
With this knowledge, you can make more informed decisions when purchasing acrylic tissue cases and better understand how to care for them to ensure long-lasting use.
資料ダウンロード
QCD調達購買管理クラウド「newji」は、調達購買部門で必要なQCD管理全てを備えた、現場特化型兼クラウド型の今世紀最高の購買管理システムとなります。
ユーザー登録
調達購買業務の効率化だけでなく、システムを導入することで、コスト削減や製品・資材のステータス可視化のほか、属人化していた購買情報の共有化による内部不正防止や統制にも役立ちます。
NEWJI DX
製造業に特化したデジタルトランスフォーメーション(DX)の実現を目指す請負開発型のコンサルティングサービスです。AI、iPaaS、および先端の技術を駆使して、製造プロセスの効率化、業務効率化、チームワーク強化、コスト削減、品質向上を実現します。このサービスは、製造業の課題を深く理解し、それに対する最適なデジタルソリューションを提供することで、企業が持続的な成長とイノベーションを達成できるようサポートします。
オンライン講座
製造業、主に購買・調達部門にお勤めの方々に向けた情報を配信しております。
新任の方やベテランの方、管理職を対象とした幅広いコンテンツをご用意しております。
お問い合わせ
コストダウンが利益に直結する術だと理解していても、なかなか前に進めることができない状況。そんな時は、newjiのコストダウン自動化機能で大きく利益貢献しよう!
(Β版非公開)