- お役立ち記事
- Understanding “Fill Weight” in Japanese Manufacturing: 「充填重量」は英語で「Fill Weight」になります。
Understanding “Fill Weight” in Japanese Manufacturing: 「充填重量」は英語で「Fill Weight」になります。
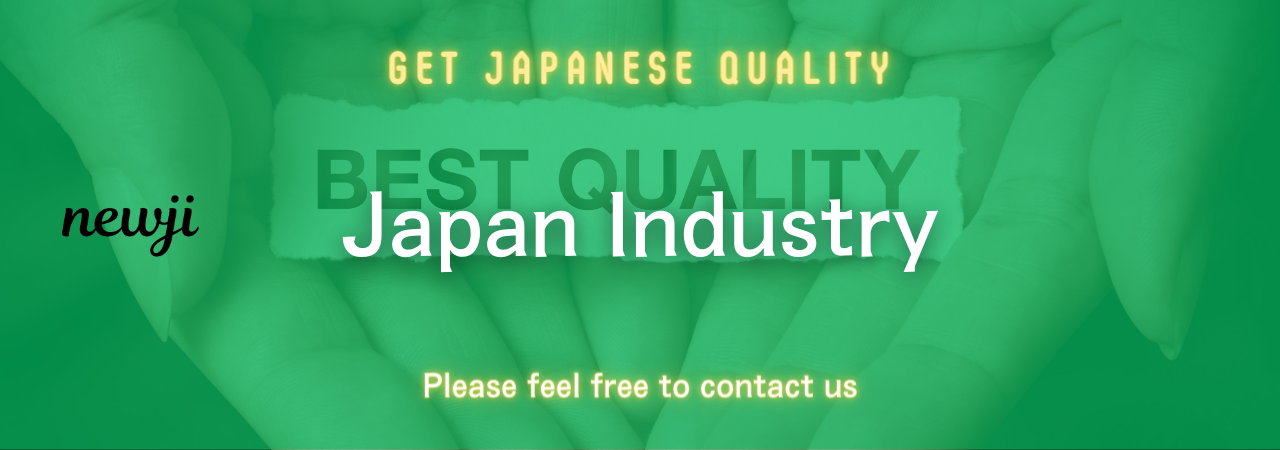
目次
Introduction to Fill Weight
In the world of manufacturing and procurement, particularly when dealing with Japanese suppliers, the term “fill weight” often comes into play. For those new to international procurement or unfamiliar with specific manufacturing terminology, understanding fill weight is essential.
Fill weight, known as 「充填重量」 in Japanese, refers to the amount of product weight filled into a container or package. Recognizing and correctly managing this concept can have substantial implications for quality control, production efficiency, and overall supply chain performance.
Importance of Fill Weight
Quality Control
Maintaining consistent fill weight is crucial for quality control. Variations in fill weight can lead to customer dissatisfaction, deviations from regulations, and increased wastage. For instance, under-filling can result in customer complaints while over-filling can cause product spillage and excess cost.
Cost Management
Accurate fill weight management allows manufacturers to control material costs effectively. Under-filling or over-filling products can lead to significant financial losses over time. Proper equipment calibration and regular monitoring can prevent waste and ensure cost efficiency.
Logistics and Shipping
Fill weight also impacts logistics and shipping. Accurately weighted shipments prevent overloading, reduce transportation costs, and improve delivery efficiency. Moreover, compliance with transportation regulations often mandates accurate weight declarations.
Challenges in Managing Fill Weight
Precise Measurement
Achieving precise fill weight requires high-quality equipment and meticulous calibration. Inaccuracies in scales and measuring devices can lead to substantial variations, affecting the overall consistency and reliability of the product.
Consistency Across Batches
Producing consistent fill weights across different batches can be challenging due to variations in raw materials, production conditions, and operator handling. Ensuring uniformity demands stringent quality control practices and regular process audits.
Regulatory Compliance
Manufacturers must adhere to local and international regulations regarding fill weight. Non-compliance can result in fines, product recalls, and damage to the brand’s reputation. Ensuring compliance requires staying updated on regulations and implementing robust quality assurance measures.
Best Practices for Managing Fill Weight
Regular Calibration
Regular calibration of weighing and filling equipment ensures accuracy. Monitoring and adjusting the equipment periodically prevent discrepancies and maintain compliance with specified weight requirements.
Automated Systems
Implementing automated filling systems can enhance precision and consistency. Automated systems reduce human error, maintain uniform fill weights, and increase overall production efficiency.
Training and SOPs
Providing thorough training to operators on fill weight procedures and establishing standard operating procedures (SOPs) enhance accuracy. Training should focus on equipment handling, quality checks, and troubleshooting.
Technology Integration
Integrating advanced technologies, such as IoT and AI, can optimize fill weight management. IoT devices monitor real-time data, while AI analyzes trends and predicts potential deviations, allowing proactive measures to maintain accuracy.
Negotiating with Japanese Suppliers
Understanding Cultural Nuances
When negotiating with Japanese suppliers, understanding cultural nuances is key. Japanese business culture values respect, patience, and meticulousness. Building a relationship based on trust and mutual respect can lead to more successful negotiations.
Clear Communication
Clearly communicating your fill weight requirements and expectations is crucial. Provide detailed specifications, including tolerances and quality standards. This clarity helps avoid misunderstandings and ensures the supplier meets your standards.
Long-Term Relationships
Japanese suppliers often prefer long-term relationships over one-off transactions. Demonstrating your commitment to a long-term partnership can encourage suppliers to invest in meeting your specific requirements, including accurate fill weight management.
Regular Audits
Conducting regular audits and visits to the supplier’s facilities helps ensure compliance with fill weight standards. These audits provide opportunities to address any issues promptly and maintain consistent quality.
Market Conditions Influencing Fill Weight
Material Costs
Fluctuating material costs can impact fill weight management. Higher costs may result in suppliers reducing fill weights to cut expenses. Understanding market conditions and establishing clear agreements with suppliers can mitigate such risks.
Technological Advancements
Advancements in technology continually influence fill weight management practices. Staying updated on new equipment, software, and methodologies can provide competitive advantages and improve fill weight accuracy.
Regulatory Changes
Changes in local and international regulations can affect fill weight requirements. Keeping abreast of regulatory developments ensures compliance and prevents potential disruptions.
Conclusion
Understanding and effectively managing fill weight in Japanese manufacturing is critical for quality control, cost management, and overall operational efficiency. By implementing best practices, utilizing advanced technologies, and fostering strong supplier relationships, manufacturers can ensure consistent and accurate fill weights.
Navigating the complexities of fill weight management with Japanese suppliers requires cultural sensitivity, clear communication, and a commitment to long-term relationships. Embracing these strategies will not only enhance product quality but also strengthen your position in the competitive manufacturing landscape.
資料ダウンロード
QCD調達購買管理クラウド「newji」は、調達購買部門で必要なQCD管理全てを備えた、現場特化型兼クラウド型の今世紀最高の購買管理システムとなります。
ユーザー登録
調達購買業務の効率化だけでなく、システムを導入することで、コスト削減や製品・資材のステータス可視化のほか、属人化していた購買情報の共有化による内部不正防止や統制にも役立ちます。
NEWJI DX
製造業に特化したデジタルトランスフォーメーション(DX)の実現を目指す請負開発型のコンサルティングサービスです。AI、iPaaS、および先端の技術を駆使して、製造プロセスの効率化、業務効率化、チームワーク強化、コスト削減、品質向上を実現します。このサービスは、製造業の課題を深く理解し、それに対する最適なデジタルソリューションを提供することで、企業が持続的な成長とイノベーションを達成できるようサポートします。
オンライン講座
製造業、主に購買・調達部門にお勤めの方々に向けた情報を配信しております。
新任の方やベテランの方、管理職を対象とした幅広いコンテンツをご用意しております。
お問い合わせ
コストダウンが利益に直結する術だと理解していても、なかなか前に進めることができない状況。そんな時は、newjiのコストダウン自動化機能で大きく利益貢献しよう!
(Β版非公開)