- お役立ち記事
- The difference between Laser Processing and Waterjet Processing
The difference between Laser Processing and Waterjet Processing
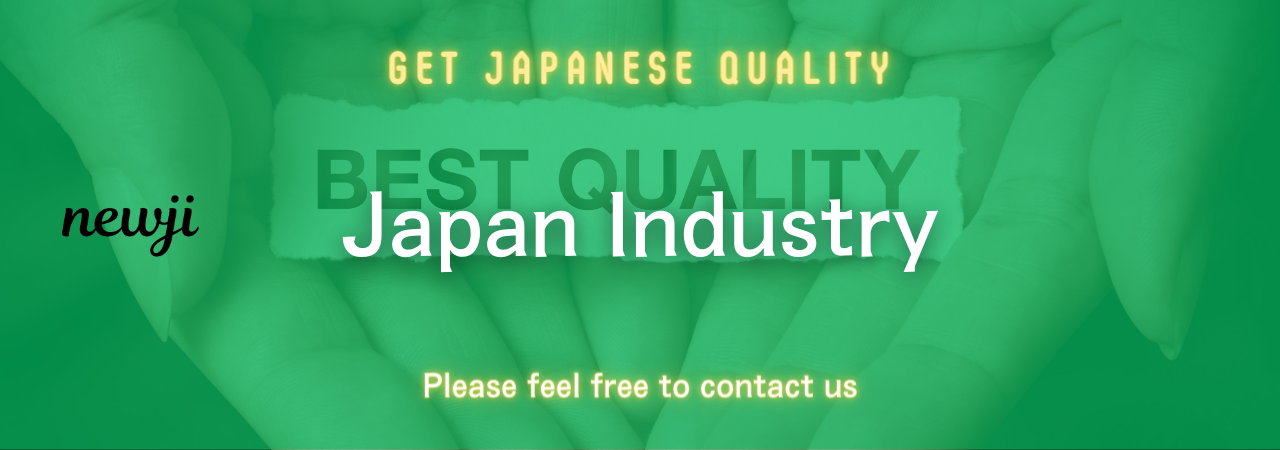
When it comes to cutting and shaping materials, two popular methods stand out: laser processing and waterjet processing.
Both techniques are highly effective but serve different purposes depending on the material and desired outcome.
Understanding these differences can help you choose the right method for your project.
目次
What is Laser Processing?
Laser processing involves focusing a high-powered laser beam onto a material to either cut, engrave, or shape it.
The laser is controlled via computer systems to deliver precise movements and intricate designs.
This method uses heat to vaporize the material at the targeted point, making it an efficient option for delicate and detailed work.
Advantages of Laser Processing
One of the key benefits of laser processing is its high level of precision.
The laser can cut materials with extreme accuracy, producing smooth edges and intricate designs.
Additionally, laser processing can handle a wide variety of materials, including metals, plastics, and even some types of wood.
This versatility makes it a go-to option for many industries.
Another advantage is the speed at which laser processing can be accomplished.
Because the process is controlled by computer systems, production times can be significantly shortened, which is ideal for high-volume projects.
Limitations of Laser Processing
Despite its many advantages, laser processing does have some limitations.
For one, it is not suitable for all materials.
For example, materials that are highly reflective, like certain metals, can be challenging to cut with a laser.
Additionally, because laser processing involves high levels of heat, it can cause thermal distortion or discoloration in some materials.
The initial cost of investing in laser processing equipment can be high, making it less accessible for smaller businesses or hobbyists.
What is Waterjet Processing?
Waterjet processing, also known as waterjet cutting, uses a high-pressure jet of water combined with abrasive materials to cut through various types of materials.
This method does not rely on heat, making it a ‘cold cutting’ process.
Some setups use pure water for cutting, while others incorporate substances like garnet to help slice through tougher materials.
Advantages of Waterjet Processing
One of the primary benefits of waterjet processing is its ability to cut through almost any material, from metal and stone to rubber and foam.
The absence of heat means there is no risk of thermal distortion, making waterjet processing ideal for materials that might be sensitive to high temperatures.
Waterjet processing is also environmentally friendly.
The process does not produce harmful gases or dust, which is beneficial for both the environment and workplace safety.
Additionally, the precision of waterjet cutting allows for highly accurate cuts, even in thick materials.
Limitations of Waterjet Processing
While waterjet processing is highly versatile, it does have its downsides.
The process can be slower than laser processing, making it less ideal for high-volume projects.
Moreover, the quality of the edge finish may not be as smooth as that achieved by laser processing, which could require additional finishing steps.
Another downside is the water and abrasive materials required for the process, which can lead to increased operational costs over time.
Comparing Laser and Waterjet Processing
In terms of precision, laser processing generally has an edge due to its ability to make extremely fine cuts and intricate designs.
However, waterjet processing excels in its capability to cut through a broader range of materials without causing thermal damage.
When it comes to speed, laser processing often wins out, particularly for smaller and more detailed projects.
Waterjet processing, however, is unmatched in its versatility and ability to handle thicker materials.
From a cost perspective, initial investment and operational costs vary for both methods.
While the setup cost for laser processing can be high, the operational costs may be lower in the long run.
On the other hand, waterjet processing equipment might be more affordable initially but can incur higher costs in water and abrasive materials.
Choosing the Right Method for Your Project
The choice between laser and waterjet processing ultimately depends on your specific needs and constraints.
If your project requires high precision and involves materials that are not sensitive to heat, laser processing could be the ideal choice.
However, if you’re working with a wider variety of materials or need to avoid the risk of thermal damage, waterjet processing may be more suitable.
Assess the material, design complexity, project timelines, and budget when making your decision.
Sometimes, combining both methods can offer the best of both worlds, leveraging the strengths of each process for different aspects of the same project.
Conclusion
Both laser and waterjet processing are powerful and precise methods for cutting and shaping materials.
While each has its unique advantages and limitations, understanding these differences can help you make informed decisions for your specific project requirements.
Whether it’s the fine detail of laser cutting or the robustness of waterjet processing, these technologies offer incredible capabilities to bring your designs to life.
資料ダウンロード
QCD調達購買管理クラウド「newji」は、調達購買部門で必要なQCD管理全てを備えた、現場特化型兼クラウド型の今世紀最高の購買管理システムとなります。
ユーザー登録
調達購買業務の効率化だけでなく、システムを導入することで、コスト削減や製品・資材のステータス可視化のほか、属人化していた購買情報の共有化による内部不正防止や統制にも役立ちます。
NEWJI DX
製造業に特化したデジタルトランスフォーメーション(DX)の実現を目指す請負開発型のコンサルティングサービスです。AI、iPaaS、および先端の技術を駆使して、製造プロセスの効率化、業務効率化、チームワーク強化、コスト削減、品質向上を実現します。このサービスは、製造業の課題を深く理解し、それに対する最適なデジタルソリューションを提供することで、企業が持続的な成長とイノベーションを達成できるようサポートします。
オンライン講座
製造業、主に購買・調達部門にお勤めの方々に向けた情報を配信しております。
新任の方やベテランの方、管理職を対象とした幅広いコンテンツをご用意しております。
お問い合わせ
コストダウンが利益に直結する術だと理解していても、なかなか前に進めることができない状況。そんな時は、newjiのコストダウン自動化機能で大きく利益貢献しよう!
(Β版非公開)