- お役立ち記事
- Revolutionizing Japanese Manufacturing: The Role of Digital Traceability in Boosting Precision and Efficiency
Revolutionizing Japanese Manufacturing: The Role of Digital Traceability in Boosting Precision and Efficiency
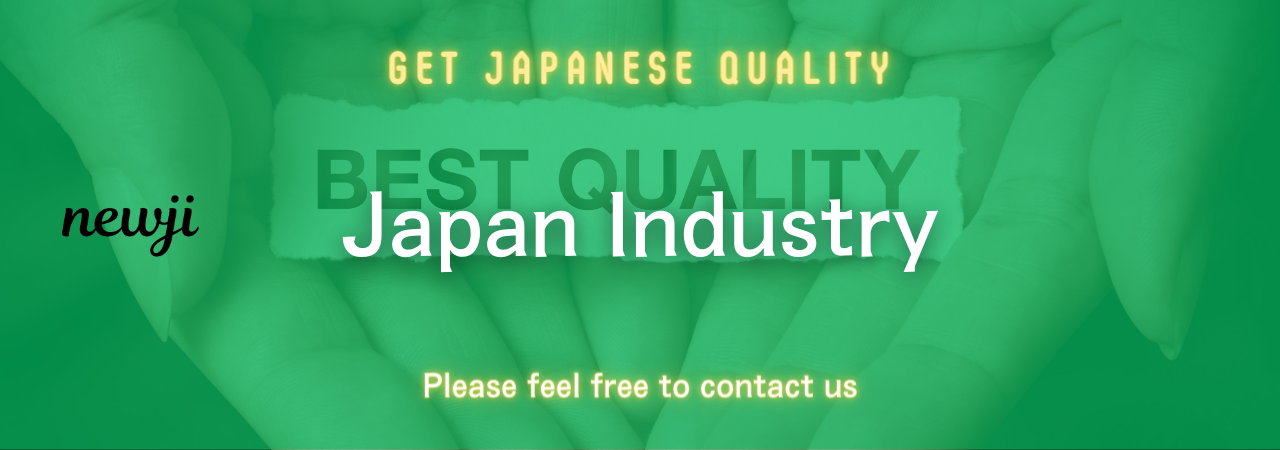
The global shift towards digital transformation is reshaping industries, and manufacturing is no exception. In Japan, renowned for its precision, efficiency, and commitment to quality, digital traceability is emerging as a pivotal tool that could revolutionize manufacturing operations. This article delves into the realms of digital traceability, exploring its impact on Japanese manufacturing, and how it can be harnessed to boost both precision and efficiency.
目次
Understanding Digital Traceability
Digital traceability refers to the capability to track and trace every step of the production process through digital means. By leveraging advanced technologies such as IoT (Internet of Things), blockchain, and big data analytics, manufacturers can achieve unprecedented levels of transparency and accountability in their operations.
The Core Components of Digital Traceability
Digital traceability relies on several key components to function seamlessly:
**1. Data Collection Devices:** Sensors, RFID tags, and barcodes collect real-time data throughout the manufacturing process.
**2. Data Storage and Management:** Cloud-based systems and databases store vast amounts of data securely.
**3. Data Analysis Tools:** Advanced analytics and AI-driven software interpret data to identify patterns and insights.
**4. Communication Networks:** Robust communication networks enable real-time data sharing across the supply chain.
The Importance of Digital Traceability
Digital traceability offers numerous benefits for manufacturing companies:
**Enhanced Quality Control:** Real-time monitoring ensures that any deviations from quality standards are promptly detected and rectified.
**Increased Transparency:** Detailed documentation of each production step fosters accountability and builds trust with customers and stakeholders.
**Efficient Supply Chain Management:** Streamlined processes and accurate data lead to optimized inventory management and reduced lead times.
**Compliance and Risk Management:** Traceability helps in adhering to regulatory requirements and managing recalls efficiently.
Advantages of Digital Traceability in Japanese Manufacturing
The Japanese manufacturing sector, known for its excellence, stands to gain significantly from adopting digital traceability solutions.
Improved Precision and Quality
Precision and quality are the hallmarks of Japanese manufacturing. Digital traceability enhances these aspects by:
**Real-Time Monitoring:** Continuous monitoring allows for immediate intervention when errors are detected, thereby reducing defects and maintaining high-quality standards.
**Root Cause Analysis:** Accurate data collection enables thorough analysis to identify and address the root causes of issues, leading to long-term quality improvements.
**Standardization:** Uniform data collection and analysis processes ensure consistency in quality across different production lines and facilities.
Augmented Efficiency
Efficiency is crucial in manufacturing, and digital traceability offers several avenues to achieve it:
**Streamlined Processes:** Real-time data provides insights into inefficiencies, enabling manufacturers to streamline processes and eliminate bottlenecks.
**Optimized Resource Management:** Accurate tracking of materials and resources helps in precise planning and reduces wastage.
**Reduced Downtime:** Predictive maintenance and timely interventions minimize equipment breakdowns and downtime.
Enhanced Supplier Collaboration
Effective supplier collaboration is essential for a seamless supply chain. Digital traceability facilitates this by:
**Transparent Communication:** Real-time data sharing fosters transparent communication between manufacturers and suppliers.
**Improved Accountability:** Detailed records hold suppliers accountable for the quality of materials and components provided.
**Enhanced Negotiations:** Accurate data enables manufacturers to negotiate better terms based on performance metrics and historical data.
Challenges and Considerations in Implementing Digital Traceability
While digital traceability offers numerous benefits, its implementation comes with certain challenges and considerations.
Initial Investment
Implementing digital traceability requires a significant initial investment in terms of hardware, software, and infrastructure. Manufacturers need to carefully evaluate the return on investment (ROI) to justify the expenditure.
Data Security and Privacy
With the surge in data collection, ensuring the security and privacy of sensitive information becomes paramount. Manufacturers must implement robust cybersecurity measures to protect data from breaches and unauthorized access.
Integration with Existing Systems
Integrating digital traceability solutions with existing legacy systems can be complex. A thorough assessment and careful planning are crucial to ensure seamless integration and interoperability.
Change Management
Adopting digital traceability necessitates a shift in mindset and processes. Manufacturers must invest in training and change management initiatives to ensure smooth adoption and buy-in from employees.
Best Practices for Implementing Digital Traceability
To successfully implement digital traceability, manufacturers should follow best practices tailored to their unique needs and operations.
Conduct a Thorough Needs Assessment
Analyze your production processes and identify key areas where digital traceability can add value. This helps in selecting the right tools and technologies that align with your goals.
Choose the Right Technology
Select technologies that are scalable, flexible, and compatible with your existing systems. Consider factors like ease of use, real-time capabilities, and integration support.
Engage Stakeholders Early
Involve key stakeholders, including suppliers, customers, and employees, from the outset. Their input and buy-in are crucial for successful implementation and adoption.
Develop a Robust Implementation Plan
Create a comprehensive implementation plan outlining timelines, responsibilities, and milestones. This ensures a structured approach and minimizes disruptions to ongoing operations.
Invest in Training and Support
Provide extensive training to employees to familiarize them with new technologies and processes. Continuous support ensures smooth transitions and maximizes the benefits of digital traceability.
The Future of Digital Traceability in Japanese Manufacturing
The adoption of digital traceability in Japanese manufacturing is not just a trend but a transformative shift that promises to redefine industry standards.
Integration with Industry 4.0
Digital traceability is a critical component of Industry 4.0, characterized by smart factories and autonomous production systems. Its integration with IoT, AI, and machine learning will create fully interconnected and intelligent manufacturing environments.
Enhanced Customer Experience
As consumers demand more transparency and quality assurance, digital traceability will play a significant role in meeting these expectations. It provides verifiable proof of quality and origins, enhancing brand trust and loyalty.
Sustainability and Circular Economy
Digital traceability supports sustainable practices by enabling better resource management, reducing waste, and facilitating recycling initiatives. It aligns with global efforts towards a circular economy, where products are designed for longevity and recyclability.
Global Competitiveness
In an increasingly competitive global market, adopting digital traceability will give Japanese manufacturers a strategic edge. It ensures adherence to international quality standards and enhances the reputation of Japanese products worldwide.
Conclusion
Digital traceability is set to revolutionize Japanese manufacturing by enhancing precision, efficiency, and transparency across the production process. While challenges exist, the benefits far outweigh them, making it a worthwhile investment for forward-thinking manufacturers. By embracing digital traceability, Japanese manufacturers can uphold their legacy of excellence and remain competitive in the global market. The future of manufacturing lies in the seamless integration of digital technologies, and Japan is poised to lead the way.
資料ダウンロード
QCD調達購買管理クラウド「newji」は、調達購買部門で必要なQCD管理全てを備えた、現場特化型兼クラウド型の今世紀最高の購買管理システムとなります。
ユーザー登録
調達購買業務の効率化だけでなく、システムを導入することで、コスト削減や製品・資材のステータス可視化のほか、属人化していた購買情報の共有化による内部不正防止や統制にも役立ちます。
NEWJI DX
製造業に特化したデジタルトランスフォーメーション(DX)の実現を目指す請負開発型のコンサルティングサービスです。AI、iPaaS、および先端の技術を駆使して、製造プロセスの効率化、業務効率化、チームワーク強化、コスト削減、品質向上を実現します。このサービスは、製造業の課題を深く理解し、それに対する最適なデジタルソリューションを提供することで、企業が持続的な成長とイノベーションを達成できるようサポートします。
オンライン講座
製造業、主に購買・調達部門にお勤めの方々に向けた情報を配信しております。
新任の方やベテランの方、管理職を対象とした幅広いコンテンツをご用意しております。
お問い合わせ
コストダウンが利益に直結する術だと理解していても、なかなか前に進めることができない状況。そんな時は、newjiのコストダウン自動化機能で大きく利益貢献しよう!
(Β版非公開)