- お役立ち記事
- Tools and Management Methods to Optimize Inventory
Tools and Management Methods to Optimize Inventory
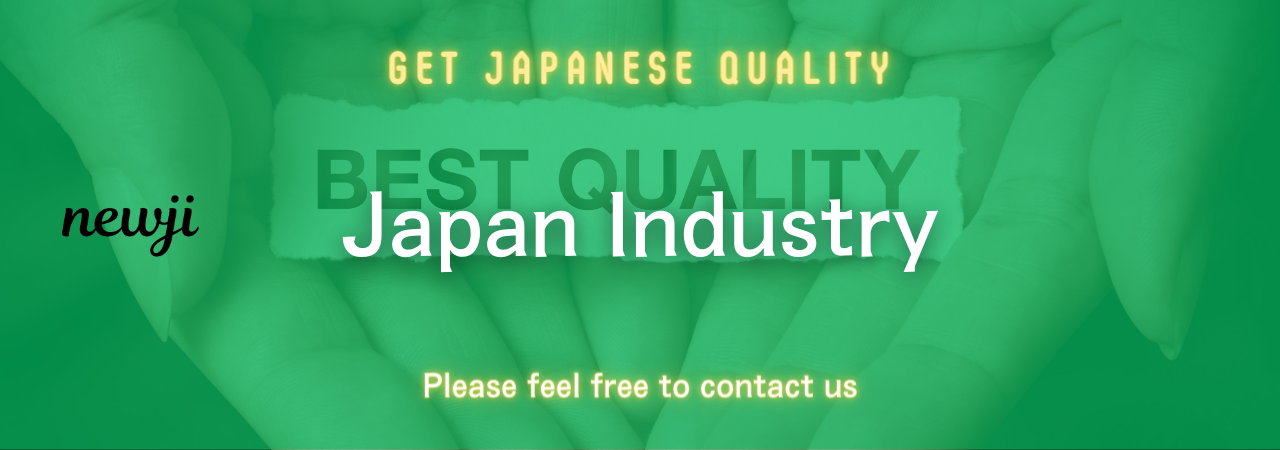
Inventory management is an essential aspect of running a business that deals with physical products.
Effective inventory management ensures that a company maintains the perfect balance of stock available, reducing wasted resources, increasing profitability, and satisfying customer demands.
Let’s explore some tools and management methods to help optimize inventory.
目次
Understanding the Significance of Inventory Management
Proper inventory management is crucial for several reasons.
A well-maintained inventory helps avoid stockouts, overstocking, and order delays which can impact customer satisfaction negatively.
Businesses that fail to manage their inventory accurately often face increased costs, lost sales, and reduced customer loyalty.
Effective inventory control leads to better demand forecasting, improved cash flow, and swifter decision-making.
It creates a streamlined operation, benefiting both customers and the business’ bottom line.
Essential Tools for Optimizing Inventory
In today’s technology-driven world, many tools can assist in making inventory management more effective.
Implementing these tools can save time, reduce errors, and improve accuracy.
Inventory Management Software (IMS)
IMS is a comprehensive tool designed to automate various inventory-related tasks.
These systems offer real-time tracking, stock level alerts, and seamless integration with sales channels.
Popular IMS options include TradeGecko, QuickBooks Commerce, and Cin7.
Such software helps businesses keep track of their stock levels, orders, sales, and deliveries in one centralized system.
Barcode Systems
Barcode systems streamline the process of tracking inventory by using scannable codes on products.
It reduces human error and speeds up inventory counting processes.
With a barcode scanner and corresponding software, businesses can monitor inventory movement accurately, ensuring products are correctly logged and updated in real-time.
Radio Frequency Identification (RFID)
RFID technology uses electromagnetic fields to automatically identify and track tags attached to objects.
RFID tags store a wide range of information about the product, allowing for quicker and more accurate inventory tracking compared to traditional methods.
This technology is especially beneficial for companies with large inventories and frequent stock movements.
Demand Forecasting Tools
Accurate demand forecasting is vital for maintaining optimal inventory levels.
Tools like NetStock, GMDH Streamline, and Forecast Pro analyze historical data to predict future demand.
These tools help businesses plan their inventory needs better, reducing the risks of overstocking or stockouts.
With better demand forecasting, companies can anticipate market trends and adjust their stock levels accordingly.
Automated Reordering Systems
Automated reordering systems use algorithms and predefined rules to reorder stock whenever levels drop below a certain threshold.
These systems ensure that businesses never run out of essential products.
By automating the reordering process, companies can save time and reduce the administrative burden on employees.
Effective Inventory Management Methods
Besides implementing tools, certain inventory management methods can significantly improve the efficiency and accuracy of inventory control.
ABC Analysis
ABC Analysis categorizes inventory into three categories based on importance:
Category A: High-value items with low sales frequency.
Category B: Moderate value items with moderate sales frequency.
Category C: Low-value items with high sales frequency.
By focusing on A-category items, businesses can prioritize their resources and attention on the most critical stock, optimizing overall inventory levels.
Just-in-Time (JIT) Inventory
JIT inventory management involves maintaining minimal stock and ordering products only when needed.
This method reduces carrying costs and minimizes the chances of overstocking.
However, it requires accurate demand forecasting and strong vendor relationships to ensure timely delivery.
Economic Order Quantity (EOQ)
EOQ is a formula used to determine the optimal order quantity that minimizes total inventory holding costs and ordering costs.
By calculating the EOQ, businesses can balance ordering and holding costs, leading to more efficient inventory management.
Safety Stock
Safety stock refers to a buffer inventory kept to prevent stockouts caused by unforeseen demand fluctuations or supply chain disruptions.
Having safety stock ensures that businesses can fulfill customer orders even in unexpected situations, maintaining high service levels and customer satisfaction.
Cycle Counting
Cycle counting is a method of regularly counting a small subset of inventory, rather than performing a full inventory count.
This method improves accuracy, reduces disruption to operations, and helps identify and correct discrepancies promptly.
By continuously updating inventory records, businesses can maintain more accurate stock levels.
Conclusion
Optimizing inventory involves a combination of using the right tools and implementing effective management methods.
By leveraging technology such as inventory management software, barcode systems, RFID, and demand forecasting tools, along with strategic methods like ABC analysis, JIT, EOQ, safety stock, and cycle counting, businesses can achieve greater accuracy and efficiency in maintaining their inventory.
Proper inventory management not only enhances operational efficiency but also boosts customer satisfaction and profitability.
Investing time and resources to optimize inventory is a strategic move that pays off significantly in the long run.
Adopting the right tools and practices is essential for a business to thrive in a competitive market and meet the ever-evolving demands of its customers.
資料ダウンロード
QCD調達購買管理クラウド「newji」は、調達購買部門で必要なQCD管理全てを備えた、現場特化型兼クラウド型の今世紀最高の購買管理システムとなります。
ユーザー登録
調達購買業務の効率化だけでなく、システムを導入することで、コスト削減や製品・資材のステータス可視化のほか、属人化していた購買情報の共有化による内部不正防止や統制にも役立ちます。
NEWJI DX
製造業に特化したデジタルトランスフォーメーション(DX)の実現を目指す請負開発型のコンサルティングサービスです。AI、iPaaS、および先端の技術を駆使して、製造プロセスの効率化、業務効率化、チームワーク強化、コスト削減、品質向上を実現します。このサービスは、製造業の課題を深く理解し、それに対する最適なデジタルソリューションを提供することで、企業が持続的な成長とイノベーションを達成できるようサポートします。
オンライン講座
製造業、主に購買・調達部門にお勤めの方々に向けた情報を配信しております。
新任の方やベテランの方、管理職を対象とした幅広いコンテンツをご用意しております。
お問い合わせ
コストダウンが利益に直結する術だと理解していても、なかなか前に進めることができない状況。そんな時は、newjiのコストダウン自動化機能で大きく利益貢献しよう!
(Β版非公開)