- お役立ち記事
- The Evolution of Monitoring Systems and Use Cases in Manufacturing
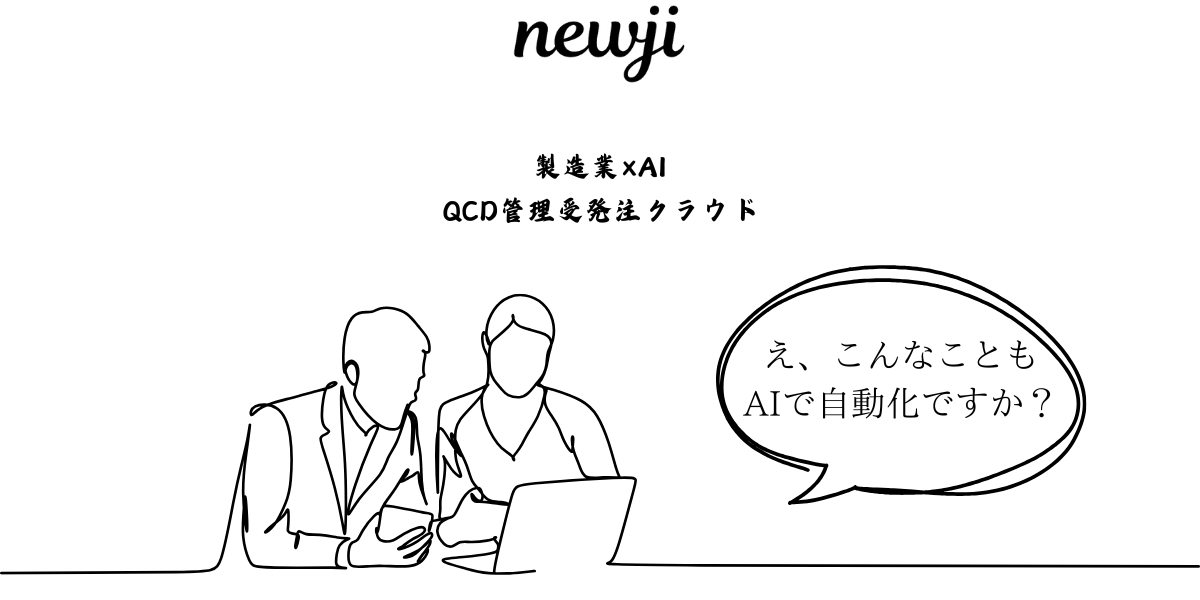
The Evolution of Monitoring Systems and Use Cases in Manufacturing
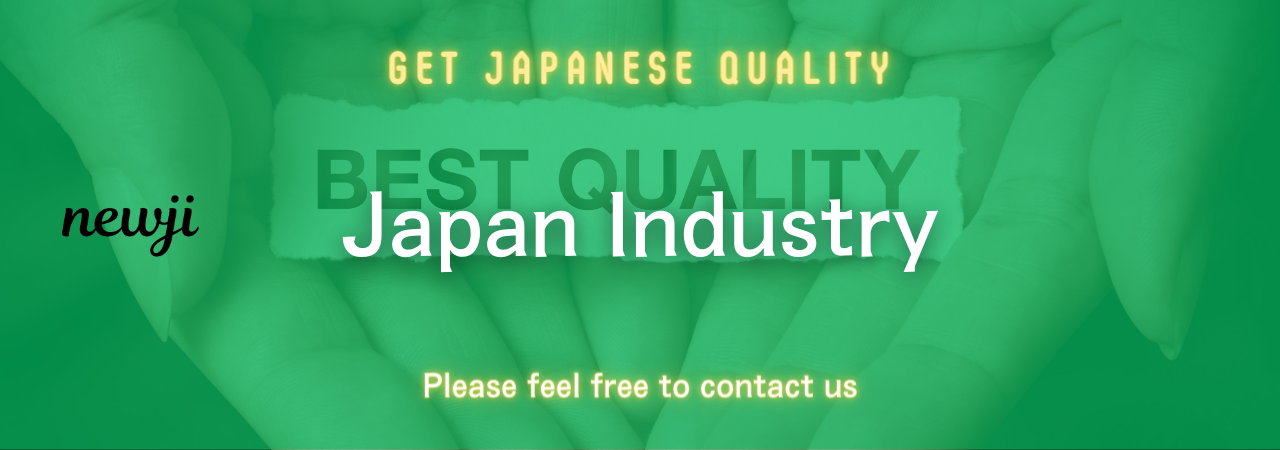
Manufacturing has always been a cornerstone of technological progress and economic growth.
Over the years, the industry has consistently adapted and evolved, embracing cutting-edge innovations to enhance efficiency and effectiveness.
One of the most significant advancements has been in monitoring systems.
These systems have revolutionized the way manufacturers operate, providing detailed insights and real-time data that are crucial for making informed decisions.
目次
What Are Monitoring Systems in Manufacturing?
Monitoring systems in manufacturing are technological solutions designed to track, collect, analyze, and report data from various processes on the production floor.
They cover a wide range of functionalities, from quality control and equipment maintenance to energy consumption and workflow management.
These systems are indispensable for modern manufacturers striving to stay competitive in a fast-paced market.
The Evolution of Monitoring Systems
Early Beginnings
In the early days, monitoring in manufacturing was rudimentary at best.
Factory managers relied on manual checks and periodic inspections to ensure everything was running smoothly.
This approach was labor-intensive and often led to errors and inefficiencies.
Introduction of Basic Automation
With the advent of mechanization and early automation, manufacturers began to use basic monitoring tools.
Simple sensors and control systems were introduced, which could report on basic metrics like temperature, pressure, and machine speed.
These early systems laid the groundwork for more sophisticated solutions.
The Digital Revolution
The introduction of digital technology marked a significant turning point.
Microprocessors and software systems allowed for more complex data collection and analysis.
Manufacturing Execution Systems (MES) became prevalent, offering more advanced monitoring capabilities.
These systems could collect data from various sources, integrate it, and provide actionable insights.
The Rise of IoT and Industry 4.0
The Internet of Things (IoT) and the Industry 4.0 revolution have transformed manufacturing monitoring systems.
Connected devices, sensor networks, and cloud computing have made it possible to track and analyze vast amounts of data in real-time.
Predictive maintenance, quality assurance, and energy management have reached new levels of sophistication.
Key Components of Modern Monitoring Systems
Sensors and Data Acquisition
Sensors are the eyes and ears of a monitoring system.
They collect data from various points in the manufacturing process.
This data can include temperature, vibration, pressure, humidity, and more.
Sophisticated data acquisition systems then aggregate this information and make it available for analysis.
Data Storage and Processing
Once collected, data needs to be stored appropriately.
In modern systems, this often involves cloud-based solutions that offer scalability and flexibility.
Advanced algorithms and artificial intelligence (AI) are used to process this data, identifying trends, anomalies, and opportunities for improvement.
Real-time Analytics and Reporting
Real-time analytics are crucial for immediate decision-making.
Advanced monitoring systems provide dashboards and visualizations that present data in an easily understandable format.
These tools enable personnel to react promptly to any issues that arise and make data-driven decisions.
Integration with Other Systems
Modern monitoring systems are not standalone solutions.
They often integrate with other enterprise systems, such as ERP (Enterprise Resource Planning), SCM (Supply Chain Management), and CRM (Customer Relationship Management).
This integration ensures that data flows seamlessly across the organization, facilitating comprehensive insights and strategies.
Use Cases in Manufacturing
Predictive Maintenance
Predictive maintenance is one of the most impactful applications of modern monitoring systems.
By continuously analyzing machine performance data, these systems can predict when a piece of equipment is likely to fail.
This allows maintenance to be scheduled proactively, reducing downtime and saving costs.
Quality Control
Maintaining high quality is essential in manufacturing.
Monitoring systems track various parameters that affect product quality in real time.
If any metrics deviate from the acceptable range, the system alerts the personnel, enabling immediate corrective action.
This reduces the risk of producing defective products and enhances overall quality control.
Energy Management
Energy consumption is a significant concern in manufacturing.
Modern monitoring systems can track and analyze energy use across different processes.
This makes it possible to identify inefficiencies and optimize energy consumption, leading to both cost savings and environmental benefits.
Supply Chain Optimization
The smooth operation of a manufacturing facility depends on efficient supply chain management.
Advanced monitoring systems integrate with supply chain solutions, providing real-time data on inventory levels, delivery times, and supplier performance.
This enables better planning and coordination, ensuring that materials are available when needed without overstocking.
Workforce Management
Human resources are a critical component of manufacturing.
Monitoring systems can track workforce productivity, attendance, and even safety compliance.
This data helps management allocate resources more effectively, leading to better overall performance.
The Future of Monitoring Systems in Manufacturing
AI and Machine Learning
Artificial intelligence and machine learning technologies are set to play a significant role in the future of manufacturing monitoring systems.
These technologies can analyze complex data sets far more efficiently than humans, providing deeper insights and more accurate predictions.
Edge Computing
Edge computing involves processing data closer to where it is generated rather than relying on centralized cloud servers.
This reduces latency and allows for faster decision-making, which is crucial in a fast-paced manufacturing environment.
Blockchain for Traceability
Blockchain technology offers a transparent and immutable way to track products from raw materials to finished goods.
Integrating blockchain with monitoring systems enhances traceability and accountability, which is particularly beneficial in industries requiring stringent quality and compliance standards.
Monitoring systems have come a long way since their inception.
From simple manual inspections to advanced IoT-enabled solutions, they have continually evolved to meet the needs of modern manufacturers.
As technology continues to advance, we can expect these systems to become even more sophisticated, driving further improvements in efficiency, quality, and overall performance.
資料ダウンロード
QCD調達購買管理クラウド「newji」は、調達購買部門で必要なQCD管理全てを備えた、現場特化型兼クラウド型の今世紀最高の購買管理システムとなります。
ユーザー登録
調達購買業務の効率化だけでなく、システムを導入することで、コスト削減や製品・資材のステータス可視化のほか、属人化していた購買情報の共有化による内部不正防止や統制にも役立ちます。
NEWJI DX
製造業に特化したデジタルトランスフォーメーション(DX)の実現を目指す請負開発型のコンサルティングサービスです。AI、iPaaS、および先端の技術を駆使して、製造プロセスの効率化、業務効率化、チームワーク強化、コスト削減、品質向上を実現します。このサービスは、製造業の課題を深く理解し、それに対する最適なデジタルソリューションを提供することで、企業が持続的な成長とイノベーションを達成できるようサポートします。
オンライン講座
製造業、主に購買・調達部門にお勤めの方々に向けた情報を配信しております。
新任の方やベテランの方、管理職を対象とした幅広いコンテンツをご用意しております。
お問い合わせ
コストダウンが利益に直結する術だと理解していても、なかなか前に進めることができない状況。そんな時は、newjiのコストダウン自動化機能で大きく利益貢献しよう!
(Β版非公開)