- お役立ち記事
- Manufacturing Process of Smart Cameras for Cars and Improvement in Recording Precision
Manufacturing Process of Smart Cameras for Cars and Improvement in Recording Precision
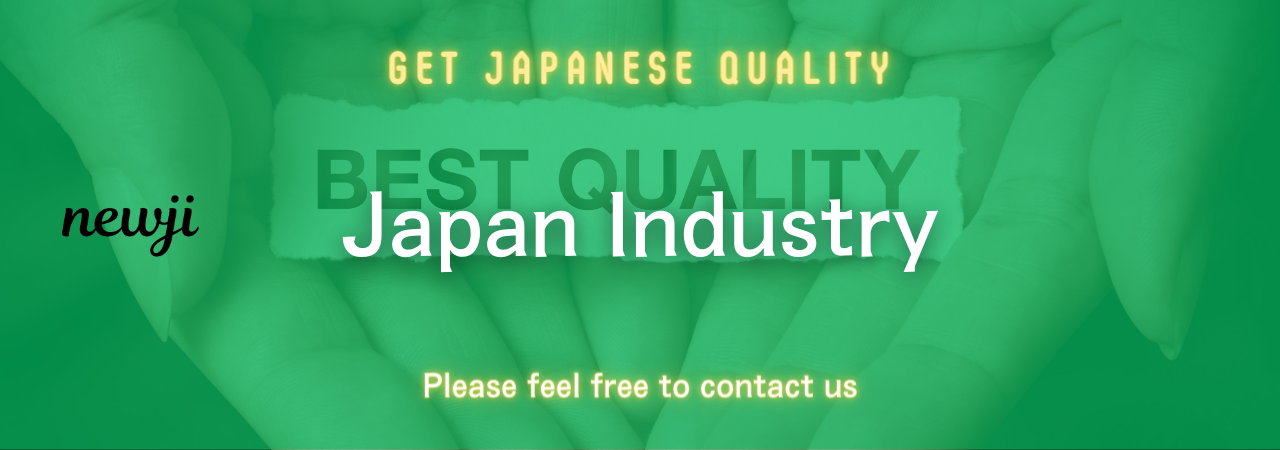
The manufacturing process of smart cameras for cars involves several complex stages, from designing the camera to assembling and testing the final product.
This process ensures that the cameras are capable of delivering high recording precision, which is crucial for their role in enhancing vehicle safety and driver assistance features.
目次
Designing the Camera
The first stage in the manufacturing process of smart cameras for cars is the design phase.
Engineers and designers collaborate to create a camera that meets specific requirements in terms of size, functionality, and performance.
They typically use computer-aided design (CAD) software to develop detailed blueprints and 3D models of the camera.
During this phase, decisions are made about the type of sensors, lenses, and electronic components that will be used in the camera.
Designers also consider the camera’s ability to withstand various environmental conditions, as it will be exposed to factors like temperature fluctuations, dust, and moisture in real-world applications.
Prototyping and Testing
Once the design is finalized, the next step is to create a prototype.
Prototyping involves building a functional version of the camera based on the design specifications.
This prototype is then subjected to a series of tests to evaluate its performance, durability, and reliability.
Testing is a critical part of the process, as it helps identify any potential issues or areas for improvement.
Engineers conduct various tests, including image quality assessments, environmental stress tests, and compatibility checks with other vehicle systems.
Component Manufacturing
With a successful prototype in hand, the manufacturing process moves to the production of individual components.
Key components of a smart camera include the image sensor, lens, circuit board, and housing.
The image sensor is one of the most crucial parts of the camera, as it captures the visual data that will be processed to assist the driver.
Manufacturing image sensors typically involves intricate semiconductor fabrication techniques.
The lens, which focuses light onto the sensor, is usually made from high-quality glass or plastic and requires precise optical engineering.
The circuit board, which houses the camera’s electronic components, is manufactured using advanced printed circuit board (PCB) fabrication methods.
The camera housing, which protects the internal components, is molded from durable materials like plastic or metal.
Assembly
After all the components have been manufactured, the next stage is assembly.
During the assembly process, the various parts of the camera are carefully put together to form the complete unit.
Automated assembly lines are often used to ensure high precision and consistency in the assembly process.
Robotic arms and other automated tools handle delicate tasks such as placing the image sensor onto the circuit board and aligning the lens with the sensor.
Calibration and Testing
Following assembly, each camera undergoes a rigorous calibration process.
Calibration involves adjusting the camera to ensure optimal performance and accuracy in its recordings.
This step is essential for achieving high recording precision.
During calibration, engineers fine-tune the camera’s settings, such as focus adjustments and sensor alignment.
The camera is also tested under various lighting conditions and scenarios to verify its performance.
Quality Control
Quality control is an ongoing process throughout the manufacturing of smart cameras.
At each stage of production, inspections and tests are conducted to ensure that the components and assembled units meet predefined quality standards.
Quality control measures include visual inspections, automated testing systems, and functional tests to check for defects or inconsistencies.
Any units that fail to meet the required standards are either reworked or rejected.
Software Integration
A smart camera’s functionality is largely dependent on the software that processes the captured images and data.
Software integration is a critical phase that involves loading the camera with firmware and software algorithms that enable its intelligent features.
The software is designed to process image data in real-time, allowing the camera to recognize objects, detect lane markings, and assist with driver safety features.
Developers rigorously test the software to ensure it operates correctly and efficiently.
Final Testing and Packaging
Before the smart cameras are shipped to customers, they undergo final testing to ensure they operate as expected in real-world conditions.
This includes performance tests, compatibility checks, and exhaustive functionality assessments.
Once the cameras pass final testing, they are packaged with care to protect them during transit.
Packaging often includes protective materials, user manuals, and installation guides to assist customers with setting up and using their new cameras.
Continual Improvement
Manufacturers of smart cameras for cars are continually seeking ways to improve their products’ precision and performance.
Advancements in technology, such as better image sensors and more sophisticated software algorithms, contribute to ongoing improvements in recording precision.
Manufacturers also gather feedback from users and conduct post-market surveillance to identify any areas where their cameras can be enhanced.
This commitment to continual improvement ensures that smart cameras keep pace with the evolving demands of the automotive industry.
In conclusion, the manufacturing process of smart cameras for cars is a multifaceted operation that involves careful design, precise component manufacturing, meticulous assembly, and thorough testing.
Each stage plays a crucial role in ensuring that the cameras deliver the high recording precision necessary for their role in modern vehicles.
As technology advances, these cameras continue to evolve, offering even greater accuracy and enhanced capabilities for driver assistance and safety.
資料ダウンロード
QCD調達購買管理クラウド「newji」は、調達購買部門で必要なQCD管理全てを備えた、現場特化型兼クラウド型の今世紀最高の購買管理システムとなります。
ユーザー登録
調達購買業務の効率化だけでなく、システムを導入することで、コスト削減や製品・資材のステータス可視化のほか、属人化していた購買情報の共有化による内部不正防止や統制にも役立ちます。
NEWJI DX
製造業に特化したデジタルトランスフォーメーション(DX)の実現を目指す請負開発型のコンサルティングサービスです。AI、iPaaS、および先端の技術を駆使して、製造プロセスの効率化、業務効率化、チームワーク強化、コスト削減、品質向上を実現します。このサービスは、製造業の課題を深く理解し、それに対する最適なデジタルソリューションを提供することで、企業が持続的な成長とイノベーションを達成できるようサポートします。
オンライン講座
製造業、主に購買・調達部門にお勤めの方々に向けた情報を配信しております。
新任の方やベテランの方、管理職を対象とした幅広いコンテンツをご用意しております。
お問い合わせ
コストダウンが利益に直結する術だと理解していても、なかなか前に進めることができない状況。そんな時は、newjiのコストダウン自動化機能で大きく利益貢献しよう!
(Β版非公開)