- お役立ち記事
- The difference between On-time Delivery Rate and Production Plan Adherence Rate
The difference between On-time Delivery Rate and Production Plan Adherence Rate
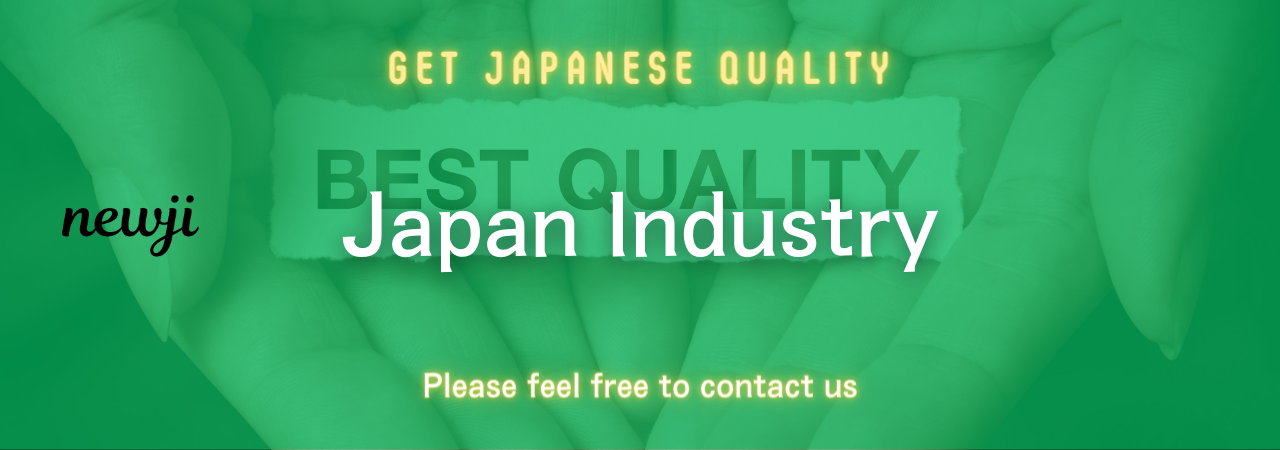
Understanding the metrics that define the efficiency of a manufacturing process is crucial for any business striving for operational excellence.
Two pivotal metrics in this sphere are the On-time Delivery Rate and the Production Plan Adherence Rate.
Though they might seem similar at a glance, they measure different aspects of the production process.
Let’s delve into what each metric stands for and how they differ.
目次
What is On-time Delivery Rate?
The On-time Delivery Rate (OTDR) is a performance metric that measures the percentage of orders delivered on or before the promised due date.
In simple terms, it tells you how often you are able to meet your delivery promises to customers.
This metric is fundamental for evaluating customer satisfaction and the reliability of your supply chain.
To calculate OTDR, use the formula:
On-time Delivery Rate = (Number of Orders Delivered On-Time / Total Number of Orders) * 100
For example, if you delivered 90 out of 100 orders on time, your OTDR would be 90%.
Consequently, a higher OTDR signifies a reliable delivery system that keeps customers happy and builds trust.
What is Production Plan Adherence Rate?
The Production Plan Adherence Rate (PPAR) measures how closely your actual production aligns with your planned production.
It is more of an internal metric that evaluates the efficiency and effectiveness of your production process.
PPAR helps in understanding how well your manufacturing facility follows the production schedules and plans set forth.
It is calculated using the formula:
Production Plan Adherence Rate = (Actual Production Output / Planned Production Output) * 100
For instance, if your planned production for the week was 500 units but you only produced 450 units, your PPAR would be 90%.
In short, a higher PPAR means your production process is running smoothly and efficiently, with minimal disruptions or deviations from the plan.
Key Differences Between On-time Delivery Rate and Production Plan Adherence Rate
While both metrics aim to improve operational performance, they do so from different angles.
Here are the key differences between OTDR and PPAR:
Focus Area
OTDR focuses on the external aspect of delivery and customer satisfaction.
It measures how well you meet committed delivery dates and times.
PPAR, on the other hand, is internally focused.
It evaluates how closely your production aligns with the planned schedule.
Measurement Scope
On-time Delivery Rate is concerned with the end-to-end process, from order receipt to delivery.
It includes various factors such as production time, shipping, and handling.
Conversely, Production Plan Adherence Rate specifically looks at the production phase.
It evaluates how well the manufacturing process adheres to the production plan.
Objective
The primary objective of OTDR is to ensure customer satisfaction by delivering goods as promised.
A high OTDR rate indicates dependable and timely deliveries.
PPAR’s main objective is to streamline the manufacturing process to adhere closely to the production schedule.
A high PPAR indicates fewer disruptions, efficient resource utilization, and effective production planning.
Impact on Supply Chain
A high OTDR positively impacts the entire supply chain, from raw material suppliers to end customers.
It builds credibility and trust among customers and partners alike.
A high PPAR influences mainly the internal stakeholders and processes.
It ensures that the manufacturing unit is operating efficiently but does not directly affect the delivery promises to the customer.
Why Both Metrics are Essential
Achieving a high OTDR without a solid PPAR is akin to promising the moon and falling short on delivery.
To ensure consistent and reliable operations, both metrics need to be optimized.
Customer Satisfaction
A high On-time Delivery Rate ensures that customers receive their orders as promised.
It builds loyal customer relationships and opens the door for repeat business.
However, to maintain a high OTDR, it’s essential to have a robust production process.
This is where PPAR comes into play.
Operational Efficiency
A high Production Plan Adherence Rate ensures that your manufacturing units are operating efficiently and effectively.
This, in turn, supports achieving a high On-time Delivery Rate.
The better your production process, the more likely you are to meet delivery commitments.
Improving Both Metrics
To excel in both OTDR and PPAR, businesses need to adopt a comprehensive approach.
Here are some strategies:
Efficient Planning
Robust production planning is the cornerstone.
Ensure that your production schedules are realistic and achievable.
Use advanced planning systems to predict and mitigate any potential disruptions.
Automation and Technology
Leveraging automation and modern technologies can significantly enhance both metrics.
Use data analytics to identify bottlenecks and inefficiencies in the production process.
Employ tracking systems to monitor deliveries and ensure they are on time.
Quality Control
Maintaining high-quality standards is essential.
Defective products can derail the production process and lead to delayed deliveries.
Implement stringent quality control measures to ensure smooth operations.
Cross-functional Collaboration
Ensure that different departments, from production to shipping, are working in unison.
Foster a culture of collaboration and continuous improvement.
Regularly review performance against these metrics and identify areas for improvement.
Inventory Management
Effective inventory management ensures that the necessary materials are available when needed.
Avoid stockouts and overstocking by employing inventory management software.
This helps in smooth production runs and timely deliveries.
Conclusion
Both On-time Delivery Rate and Production Plan Adherence Rate are integral metrics that contribute to the overall efficiency and success of a business.
While OTDR focuses on customer satisfaction and delivery reliability, PPAR emphasizes internal production efficiency.
Understanding and optimizing both metrics can lead to a well-rounded, efficient, and customer-friendly operation.
By focusing on efficient planning, leveraging technology, maintaining quality, fostering collaboration, and managing inventory effectively, businesses can excel in both areas.
In the end, the harmony between these two metrics is what drives sustained operational success.
資料ダウンロード
QCD調達購買管理クラウド「newji」は、調達購買部門で必要なQCD管理全てを備えた、現場特化型兼クラウド型の今世紀最高の購買管理システムとなります。
ユーザー登録
調達購買業務の効率化だけでなく、システムを導入することで、コスト削減や製品・資材のステータス可視化のほか、属人化していた購買情報の共有化による内部不正防止や統制にも役立ちます。
NEWJI DX
製造業に特化したデジタルトランスフォーメーション(DX)の実現を目指す請負開発型のコンサルティングサービスです。AI、iPaaS、および先端の技術を駆使して、製造プロセスの効率化、業務効率化、チームワーク強化、コスト削減、品質向上を実現します。このサービスは、製造業の課題を深く理解し、それに対する最適なデジタルソリューションを提供することで、企業が持続的な成長とイノベーションを達成できるようサポートします。
オンライン講座
製造業、主に購買・調達部門にお勤めの方々に向けた情報を配信しております。
新任の方やベテランの方、管理職を対象とした幅広いコンテンツをご用意しております。
お問い合わせ
コストダウンが利益に直結する術だと理解していても、なかなか前に進めることができない状況。そんな時は、newjiのコストダウン自動化機能で大きく利益貢献しよう!
(Β版非公開)