- お役立ち記事
- Manufacturing Process of Brake Pads and Friction Performance Enhancement
Manufacturing Process of Brake Pads and Friction Performance Enhancement
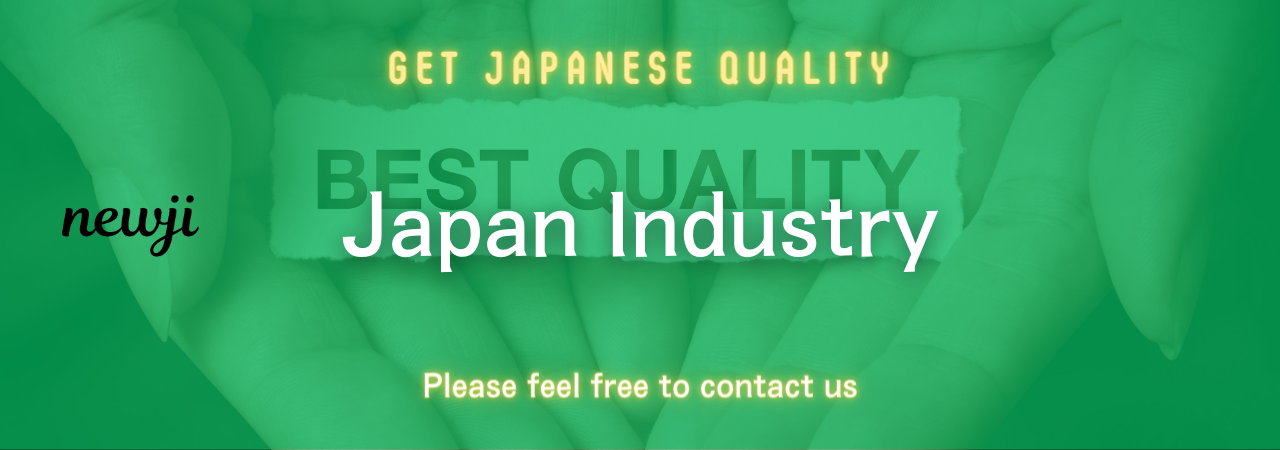
Manufacturing brake pads, crucial for vehicle safety, involves several steps, from raw material selection to final testing.
Understanding this process provides insights into how these components contribute to effective braking.
Moreover, enhancing their friction performance ensures better vehicle control, reducing the risk of accidents.
目次
Raw Material Selection
Choosing the right materials is the first step in manufacturing brake pads.
Commonly used materials include metal fibers, friction modifiers, and binding resins.
Each material contributes distinct properties to the final product.
Metal fibers, for example, provide strength, while friction modifiers improve braking performance.
Mixing and Formulation
Once the materials are selected, they are measured precisely and mixed.
This stage, known as formulation, creates a homogeneous mixture.
The formulation varies depending on the type of brake pad being manufactured, such as organic, semi-metallic, or ceramic pads.
Each type has unique characteristics suited for different applications.
Organic Brake Pads
Organic pads use non-metallic fibers such as rubber, Kevlar, and glass.
They offer quiet operation but wear out faster than other types.
Semi-Metallic Brake Pads
Semi-metallic pads incorporate a mixture of metal fibers, providing a balance between durability and performance.
They are commonly used in high-performance and standard vehicles.
Ceramic Brake Pads
Ceramic pads, composed mainly of ceramic fibers and filler materials, are known for their longevity and minimal dust production.
They are ideal for everyday driving conditions.
Molding Process
After mixing, the compound is placed into molds to form the shape of the brake pads.
The molding process involves high pressure and heat, bonding the materials together.
This step is critical for achieving the desired density and structural integrity of the pads.
Curing and Heat Treatment
Following molding, the pads undergo curing in an oven.
Curing uses high temperatures to solidify the binding resins, ensuring the ingredients stay bonded.
Heat treatment also improves the structural properties of the pads, enhancing their durability.
Backing Plate Preparation
A vital component of brake pads is the backing plate.
Manufactured from steel, it provides the structural support needed during braking.
The backing plate is cleaned, treated with an adhesive solution, and sometimes coated with insulation.
This ensures it bonds effectively with the friction material during the curing process.
Bonding the Backing Plate
The cured friction material is bonded to the backing plate using high-pressure machinery.
This process guarantees the pads can withstand high temperatures and stress during braking.
Securely bonded friction material and backing plate ensure safety and performance.
Finishing and Quality Control
The next step involves finishing the brake pads, including grinding, chamfering, and slotting.
These processes shape the pads and improve their fit and function in braking systems.
The pads are also painted or coated to prevent rust and corrosion.
Grinding
Grinding ensures the pads have a smooth, even surface, critical for consistent braking performance.
Accurate grinding ensures the pads fit well in the caliper.
Chamfering and Slotting
Chamfering involves creating beveled edges on the pads, reducing noise during braking.
Slotting cuts grooves into the pad surface to enhance heat dissipation and prevent cracking.
Performance Testing
Quality control includes rigorous testing of the brake pads.
Tests include friction performance, wear resistance, and thermal stability.
These tests ensure the pads meet safety standards and perform well under various conditions.
Friction Performance Testing
Friction performance testing evaluates the pads’ ability to generate adequate friction at different temperatures and speeds.
Consistent friction coefficient under various conditions indicates reliable brake pads.
Wear Resistance Testing
Wear resistance testing measures the pads’ longevity.
Pads that withstand prolonged use and retain their performance are considered high-quality.
Friction Performance Enhancement Techniques
Enhancing friction performance is key to developing high-quality brake pads.
Several techniques and additives improve the friction characteristics of brake pads.
Friction Modifiers
Friction modifiers are additives that enhance the friction properties of brake pads.
Materials such as graphite, metal oxides, and carbon fibers can be added to the mix to improve performance.
Surface Treatments
Surface treatments such as scorching and thermal conditioning prepare the pads for immediate performance.
These treatments improve the initial friction characteristics and reduce the bedding-in period.
Structural Reinforcements
Adding structural reinforcements, like metal shims, can reduce noise and vibration, resulting in a quieter ride.
These reinforcements also enhance the pads’ overall stability.
Environmental Considerations
Modern brake pad manufacturing also considers environmental impacts.
Using eco-friendly materials and reducing harmful emissions during production are key focus areas.
Manufacturers strive to balance performance with environmental responsibility.
Conclusion
The comprehensive process of manufacturing brake pads ensures they meet stringent safety and performance standards.
From selecting the raw materials to the final performance tests, each step is meticulously carried out.
Enhancing friction performance through innovative techniques ensures that brake pads not only stop vehicles effectively but also contribute to a smoother, quieter ride.
Understanding these processes highlights the complexities and importance of brake pad manufacturing, ultimately contributing to safer and more reliable transportation.
資料ダウンロード
QCD調達購買管理クラウド「newji」は、調達購買部門で必要なQCD管理全てを備えた、現場特化型兼クラウド型の今世紀最高の購買管理システムとなります。
ユーザー登録
調達購買業務の効率化だけでなく、システムを導入することで、コスト削減や製品・資材のステータス可視化のほか、属人化していた購買情報の共有化による内部不正防止や統制にも役立ちます。
NEWJI DX
製造業に特化したデジタルトランスフォーメーション(DX)の実現を目指す請負開発型のコンサルティングサービスです。AI、iPaaS、および先端の技術を駆使して、製造プロセスの効率化、業務効率化、チームワーク強化、コスト削減、品質向上を実現します。このサービスは、製造業の課題を深く理解し、それに対する最適なデジタルソリューションを提供することで、企業が持続的な成長とイノベーションを達成できるようサポートします。
オンライン講座
製造業、主に購買・調達部門にお勤めの方々に向けた情報を配信しております。
新任の方やベテランの方、管理職を対象とした幅広いコンテンツをご用意しております。
お問い合わせ
コストダウンが利益に直結する術だと理解していても、なかなか前に進めることができない状況。そんな時は、newjiのコストダウン自動化機能で大きく利益貢献しよう!
(Β版非公開)