- お役立ち記事
- Change Management and Its Implementation in Manufacturing
Change Management and Its Implementation in Manufacturing
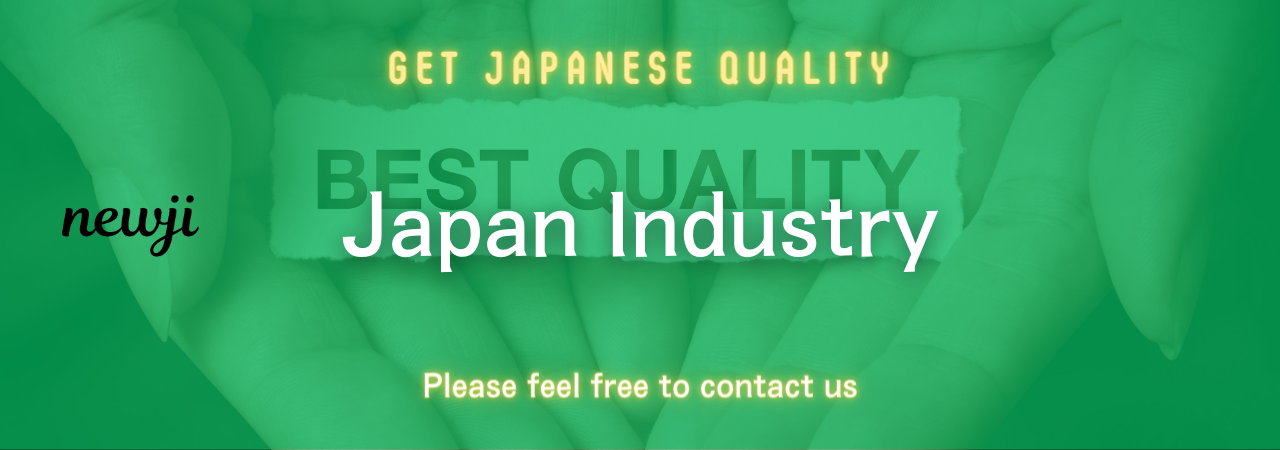
Change management is a crucial process in any industry, but it bears particular significance in manufacturing. Rapid technological advancements, evolving market demands, and increased competition necessitate continuous adaptation. Effective change management ensures that these transitions occur smoothly, minimizing disruption and fostering growth. This article explores the fundamentals of change management in the manufacturing sector and provides insights into its successful implementation.
目次
Understanding Change Management
Change management involves a structured approach to transitioning individuals, teams, and organizations from a current state to a desired future state. It aims to equip people to accept and embrace changes in their current work environment. In a manufacturing context, this may include shifts in production processes, technological upgrades, or organizational restructuring.
Why Change Management is Critical in Manufacturing
The manufacturing industry is characterized by its complexity and rapid pace. Processes are often intricate, involving numerous moving parts and a reliance on both human and technological resources. Any change, therefore, has the potential to create significant disruption if not managed carefully. Effective change management helps mitigate risks, ensuring that the benefits of new initiatives are realized without substantial negative impacts.
Key Elements of Change Management
Several essential components contribute to successful change management in manufacturing:
1. **Clear Vision and Objectives:** It is essential to have a clear understanding of why the change is necessary and what it aims to achieve. This vision must be communicated effectively to all stakeholders.
2. **Stakeholder Engagement:** Engaging all stakeholders, including employees, managers, and external partners, is crucial. Their input and buy-in are vital for the smooth implementation of changes.
3. **Effective Communication:** Regular and transparent communication helps manage expectations and reduces resistance. Stakeholders should be kept informed about the change process, timelines, and any potential impacts.
4. **Training and Support:** Providing adequate training and support ensures that employees are equipped to handle new processes and technologies. This reduces uncertainty and builds confidence.
5. **Monitoring and Feedback:** Continuous monitoring and feedback mechanisms allow for adjustments to be made as needed. This ensures that the change process remains on track and achieves its desired outcomes.
Steps to Implement Change Management in Manufacturing
Implementing change management in a manufacturing setting involves several structured steps:
1. Assess the Need for Change
Before any change can be implemented, it is essential to assess its necessity. This involves identifying the drivers of change, such as new market trends, technological advancements, or internal process inefficiencies. A thorough analysis helps in understanding the potential benefits and risks associated with the change.
2. Develop a Change Management Plan
A detailed change management plan outlines the steps required to achieve the desired transformation. This includes setting clear objectives, defining roles and responsibilities, and establishing timelines. The plan should also address potential challenges and outline strategies to overcome them.
3. Communicate the Change
Effective communication is vital for successful change management. Communicate the reasons for the change, the benefits it will bring, and how it will be implemented. Use multiple channels to reach all stakeholders and ensure that the message is consistent and clear.
4. Train and Support Employees
Training is a critical component of change management. Provide employees with the necessary skills and knowledge to adapt to new processes or technologies. Offer continuous support to address any concerns or challenges that may arise during the transition period.
5. Implement the Change
With a solid plan in place, the next step is to implement the change. This should be done in a phased manner to minimize disruptions. Monitor the implementation closely to ensure that it is proceeding as planned.
6. Monitor and Evaluate
After the change has been implemented, it is essential to monitor its impact. Collect feedback from stakeholders and evaluate the outcomes against the set objectives. Use this information to make necessary adjustments and improve future change management initiatives.
Challenges in Change Management
Change management in manufacturing is not without its challenges. Some common obstacles include:
Resistance to Change
Employees may resist change due to fear of the unknown, lack of understanding, or perceived negative impacts on their jobs. Addressing these concerns through effective communication and support is crucial.
Complexity of Processes
Manufacturing processes are often complex and interdependent. Changes in one area can have ripple effects on others. Thorough planning and careful execution are necessary to manage these complexities.
Resource Constraints
Implementing change requires resources, including time, money, and personnel. Resource constraints can hinder the change process. Prioritizing and efficiently allocating resources is essential.
Best Practices for Successful Change Management
To increase the likelihood of successful change management in manufacturing, consider the following best practices:
Involve Employees Early On
Involving employees in the change process from the outset can help reduce resistance and increase buy-in. Their insights and feedback can also provide valuable input for the change plan.
Maintain Flexibility
While having a detailed plan is important, it is equally crucial to remain flexible. Be prepared to adapt the plan as needed based on feedback and changing circumstances.
Focus on Continuous Improvement
Change management should not be a one-time event. Promote a culture of continuous improvement where change is embraced as a part of everyday operations. This helps organizations stay competitive and responsive to market demands.
Conclusion
Change management is essential for the success and growth of manufacturing organizations. By understanding the need for change, developing a robust plan, and effectively engaging all stakeholders, manufacturers can navigate the complexities of change with minimal disruption. Despite the challenges, adopting best practices and fostering a culture of continuous improvement can lead to long-term benefits and a more resilient organization.
資料ダウンロード
QCD調達購買管理クラウド「newji」は、調達購買部門で必要なQCD管理全てを備えた、現場特化型兼クラウド型の今世紀最高の購買管理システムとなります。
ユーザー登録
調達購買業務の効率化だけでなく、システムを導入することで、コスト削減や製品・資材のステータス可視化のほか、属人化していた購買情報の共有化による内部不正防止や統制にも役立ちます。
NEWJI DX
製造業に特化したデジタルトランスフォーメーション(DX)の実現を目指す請負開発型のコンサルティングサービスです。AI、iPaaS、および先端の技術を駆使して、製造プロセスの効率化、業務効率化、チームワーク強化、コスト削減、品質向上を実現します。このサービスは、製造業の課題を深く理解し、それに対する最適なデジタルソリューションを提供することで、企業が持続的な成長とイノベーションを達成できるようサポートします。
オンライン講座
製造業、主に購買・調達部門にお勤めの方々に向けた情報を配信しております。
新任の方やベテランの方、管理職を対象とした幅広いコンテンツをご用意しております。
お問い合わせ
コストダウンが利益に直結する術だと理解していても、なかなか前に進めることができない状況。そんな時は、newjiのコストダウン自動化機能で大きく利益貢献しよう!
(Β版非公開)