- お役立ち記事
- The difference between Wire Cutting and Laser Cutting
The difference between Wire Cutting and Laser Cutting
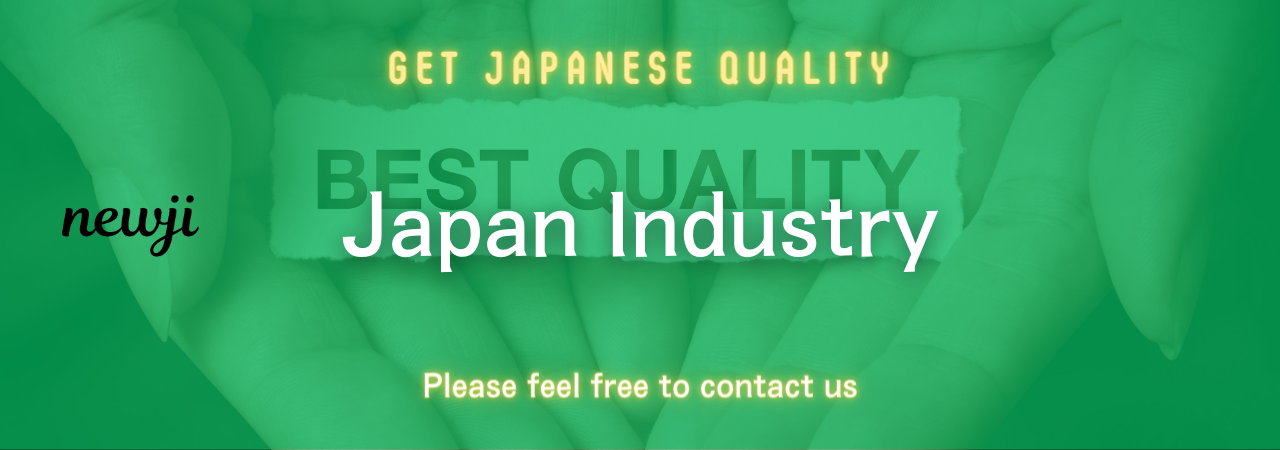
Cutting materials accurately and efficiently is crucial in many industries, from manufacturing to crafting.
Two common methods are wire cutting and laser cutting.
Understanding the differences between these two techniques can help you choose the best method for your specific needs.
目次
What is Wire Cutting?
Wire cutting uses a thin wire to cut through various materials.
This method is also known as wire EDM (Electrical Discharge Machining).
In this process, a thin, electrically charged wire is used to create sparks that erode the material.
The wire moves back and forth, cutting through the material bit by bit.
Wire cutting is often used for hard materials like steel and titanium and is known for its precision.
Advantages of Wire Cutting
Wire cutting is highly accurate.
It can achieve very tight tolerances, making it ideal for parts that need to fit together perfectly.
This method is great for cutting complex shapes and intricate designs.
Wire cutting produces a smooth finish, reducing the need for additional polishing or machining.
It is also versatile, as it can cut through a variety of materials, including metals, ceramics, and even some types of glass.
Disadvantages of Wire Cutting
Wire cutting can be slow, especially for thicker materials.
The process can be costly due to the need for specialized equipment and materials.
It is not suitable for cutting soft or easily deformable materials.
Wire cutting requires a constant supply of electricity, which can be a drawback in areas with unstable power supplies.
What is Laser Cutting?
Laser cutting uses a focused beam of light to cut through materials.
This method involves directing a high-powered laser at the material, which then melts, burns, or vaporizes it.
The laser beam is controlled by a computer, ensuring precise and consistent cuts.
Laser cutting is commonly used for materials like metals, plastics, wood, and textiles.
Advantages of Laser Cutting
Laser cutting is incredibly fast and efficient.
It can cut through materials quickly, making it ideal for high-volume production.
The method provides a high level of precision, allowing for detailed and intricate designs.
Laser cutting produces minimal waste, as the beam is very thin and precise.
This method is versatile, capable of cutting, engraving, and etching various materials.
Disadvantages of Laser Cutting
Laser cutting can be expensive, especially for high-powered lasers and specialized equipment.
It is not suitable for very thick materials, as the laser may not penetrate deeply enough.
Some materials, like reflective metals, can be challenging to cut with a laser.
There is a risk of burns or fire if the equipment is not properly managed.
Comparing Wire Cutting and Laser Cutting
When choosing between wire cutting and laser cutting, it is important to consider the specific requirements of your project.
Here, we will compare the two methods based on several factors.
Accuracy and Precision
Both wire cutting and laser cutting offer high levels of accuracy and precision.
However, wire cutting is often considered more precise, especially for tight tolerances and intricate designs.
Laser cutting, while precise, may struggle with very small details or complex shapes.
Speed
Laser cutting is generally faster than wire cutting, making it more suitable for high-volume production.
Wire cutting, on the other hand, can be time-consuming, particularly for thicker materials.
Cost
Both methods can be costly, but the expenses come from different sources.
Wire cutting requires specialized equipment and materials, which can be expensive.
Laser cutting, while also requiring specialized equipment, tends to be more efficient and may offer cost savings in high-volume production.
Materials
Wire cutting is best suited for hard materials like metals and ceramics.
Laser cutting, on the other hand, is versatile and can cut through a wider range of materials, including metals, plastics, wood, and textiles.
However, very thick materials can pose a challenge for laser cutting.
Finish Quality
Wire cutting produces a smooth finish, often eliminating the need for further polishing.
Laser cutting can leave a slightly rougher edge, depending on the material and the settings used.
In some cases, additional finishing may be required.
Applications of Wire Cutting
Wire cutting is commonly used in industries where precision is paramount.
Here are a few examples of its applications:
– **Tool and Die Making:** Creating precise tools and dies for manufacturing processes.
– **Aerospace:** Producing intricate and high-precision parts for aircraft and spacecraft.
– **Medical Devices:** Manufacturing precise components for medical equipment and implants.
– **Automotive:** Cutting complex shapes for engine components and other critical parts.
Applications of Laser Cutting
Laser cutting is widely used across various industries due to its versatility and speed.
Some common applications include:
– **Manufacturing:** Cutting and engraving parts for various products.
– **Art and Design:** Creating intricate designs in materials like paper, wood, and acrylic.
– **Signage:** Producing custom signs with detailed engravings and cutouts.
– **Jewelry:** Crafting intricate and delicate pieces of jewelry.
Making the Right Choice
Both wire cutting and laser cutting offer unique advantages and are suited for different applications.
To make the right choice for your project, consider the following factors:
– **Material Type:** Determine whether your material is hard or soft, thick or thin.
– **Precision Requirements:** Assess the level of detail and accuracy needed for your design.
– **Production Volume:** Consider whether you need a method that is fast and efficient for high-volume production.
– **Cost Constraints:** Evaluate the costs associated with each method and choose the one that fits your budget.
By carefully considering these factors, you can choose the most suitable cutting method for your needs.
Whether you opt for the precision of wire cutting or the versatility of laser cutting, you can achieve high-quality results for your project.
資料ダウンロード
QCD調達購買管理クラウド「newji」は、調達購買部門で必要なQCD管理全てを備えた、現場特化型兼クラウド型の今世紀最高の購買管理システムとなります。
ユーザー登録
調達購買業務の効率化だけでなく、システムを導入することで、コスト削減や製品・資材のステータス可視化のほか、属人化していた購買情報の共有化による内部不正防止や統制にも役立ちます。
NEWJI DX
製造業に特化したデジタルトランスフォーメーション(DX)の実現を目指す請負開発型のコンサルティングサービスです。AI、iPaaS、および先端の技術を駆使して、製造プロセスの効率化、業務効率化、チームワーク強化、コスト削減、品質向上を実現します。このサービスは、製造業の課題を深く理解し、それに対する最適なデジタルソリューションを提供することで、企業が持続的な成長とイノベーションを達成できるようサポートします。
オンライン講座
製造業、主に購買・調達部門にお勤めの方々に向けた情報を配信しております。
新任の方やベテランの方、管理職を対象とした幅広いコンテンツをご用意しております。
お問い合わせ
コストダウンが利益に直結する術だと理解していても、なかなか前に進めることができない状況。そんな時は、newjiのコストダウン自動化機能で大きく利益貢献しよう!
(Β版非公開)