- お役立ち記事
- Manufacturing Process of Automatic Camera Gimbals and Improvement in Stabilization Technology
Manufacturing Process of Automatic Camera Gimbals and Improvement in Stabilization Technology
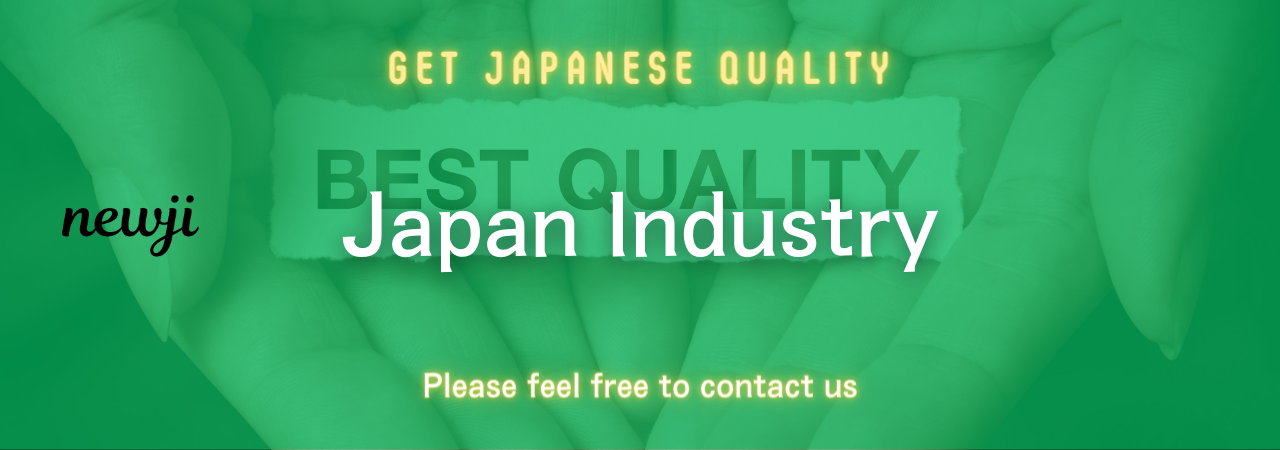
目次
Introduction to Camera Gimbals
Camera gimbals have revolutionized the way we capture images and videos.
They are mechanical devices that help stabilize cameras, ensuring smooth and steady shots, which is crucial, especially during movement.
Over the years, the manufacturing process of these gimbals has evolved significantly, leading to remarkable improvements in stabilization technology.
The Basics of Camera Gimbal Technology
Before delving into the manufacturing process, it’s essential to understand how gimbals work.
A camera gimbal uses motors and sensors to counteract any unwanted movements.
These devices often consist of three axes of rotation, allowing the camera to remain stable regardless of the operator’s movements.
Components of a Camera Gimbal
At its core, a camera gimbal comprises several critical components:
– **Motors**: These are responsible for counteracting the unwanted movements.
Three motors, one for each axis, are typically utilized.
– **Sensors**: These detect the camera’s orientation and measure the amount of movement that needs to be corrected.
– **Controller**: This electronic unit processes the sensor data and controls the motors accordingly.
– **Mechanical Frame**: Provides the physical structure and supports the camera.
Materials and Design
The choice of materials is crucial in manufacturing camera gimbals, as they need to be lightweight yet robust.
Aluminum, carbon fiber, and high-strength plastics are commonly used materials.
Carbon fiber is particularly favored due to its excellent strength-to-weight ratio.
The design process begins with 3D modeling software.
Engineers create detailed blueprints of the gimbal, ensuring that all components fit perfectly and function harmoniously.
Computer-aided design (CAD) software is pivotal in this phase, allowing for the simulation of various stress tests and movement scenarios.
Precision Manufacturing Techniques
Once the design is finalized, the manufacturing process involves several high-precision techniques.
CNC Machining
Computer Numerical Control (CNC) machining is widely used in the production of gimbal parts.
This manufacturing method allows for the creation of highly precise components.
A CNC machine cuts the materials according to the design specifications, ensuring each part meets strict tolerances.
Injection Molding
For plastic components, injection molding is a common technique.
Plastic is melted and injected into pre-designed molds, which are then cooled to form the gimbal parts.
This method is efficient for mass production, ensuring consistent quality.
3D Printing
Additive manufacturing or 3D printing is gaining popularity in the gimbal industry.
It allows for the creation of intricate and custom-designed components that might be challenging to produce using traditional methods.
While not yet prevalent for mass production, 3D printing is invaluable for prototyping.
Assembling the Gimbal
The assembly process is a meticulous operation that requires precision and care.
Initial Assembly
The first step involves assembling the mechanical frame.
Each part is carefully aligned and securely fastened to form the basic structure.
Following this, the motors are installed in their respective positions.
Wiring and Electronics
The next phase involves connecting the electronic components.
Wiring is carefully routed to avoid interference with the gimbal’s movements.
The controller unit is integrated, and connections are tested to ensure they function correctly.
Calibration
Once assembled, the gimbal undergoes a calibration process.
This involves fine-tuning the sensors and controllers to ensure accurate movement compensation.
Calibration is crucial for achieving optimal stability and performance.
Testing and Quality Assurance
Before a camera gimbal reaches the market, it must pass rigorous testing and quality assurance procedures.
Functional Testing
Each gimbal is subjected to a series of functional tests.
These tests assess how well the gimbal stabilizes the camera during various movements.
Different scenarios are simulated, including sudden jerks and smooth pans, to ensure reliable performance.
Durability Testing
Durability tests are conducted to assess the gimbal’s resilience under harsh conditions.
These might include exposure to extreme temperatures, moisture, and physical impacts.
The goal is to ensure that the gimbal can withstand real-world usage scenarios.
Advancements in Stabilization Technology
Recent advancements have significantly enhanced the performance of camera gimbals.
Advanced Algorithms
Modern gimbals employ advanced algorithms to improve stabilization.
These algorithms analyze sensor data in real-time and adjust the motors more precisely.
Machine learning techniques are also being integrated, allowing the gimbal to adapt to the operator’s movements and improve over time.
Enhanced Sensors
The sensors used in modern gimbals are more sophisticated than ever.
Gyroscopes and accelerometers have become more accurate, reducing lag and improving responsiveness.
Some gimbals now include GPS and magnetometer sensors for even better performance.
Power Efficiency
Power efficiency has also seen significant improvements.
Gimbal motors are now more energy-efficient, allowing for longer operating times on a single charge.
Battery technology has advanced, offering lightweight yet high-capacity batteries.
Conclusion
The manufacturing process of automatic camera gimbals is a complex yet fascinating journey from design to production.
Improvements in materials, precision manufacturing techniques, and sophisticated algorithms have all contributed to the advancements in stabilization technology.
As we continue to innovate and refine these processes, the future of camera gimbals looks bright, offering even smoother and more reliable performance for photographers and videographers alike.
資料ダウンロード
QCD調達購買管理クラウド「newji」は、調達購買部門で必要なQCD管理全てを備えた、現場特化型兼クラウド型の今世紀最高の購買管理システムとなります。
ユーザー登録
調達購買業務の効率化だけでなく、システムを導入することで、コスト削減や製品・資材のステータス可視化のほか、属人化していた購買情報の共有化による内部不正防止や統制にも役立ちます。
NEWJI DX
製造業に特化したデジタルトランスフォーメーション(DX)の実現を目指す請負開発型のコンサルティングサービスです。AI、iPaaS、および先端の技術を駆使して、製造プロセスの効率化、業務効率化、チームワーク強化、コスト削減、品質向上を実現します。このサービスは、製造業の課題を深く理解し、それに対する最適なデジタルソリューションを提供することで、企業が持続的な成長とイノベーションを達成できるようサポートします。
オンライン講座
製造業、主に購買・調達部門にお勤めの方々に向けた情報を配信しております。
新任の方やベテランの方、管理職を対象とした幅広いコンテンツをご用意しております。
お問い合わせ
コストダウンが利益に直結する術だと理解していても、なかなか前に進めることができない状況。そんな時は、newjiのコストダウン自動化機能で大きく利益貢献しよう!
(Β版非公開)