- お役立ち記事
- Equipment Selection for Successful TPM (Total Productive Maintenance)
Equipment Selection for Successful TPM (Total Productive Maintenance)
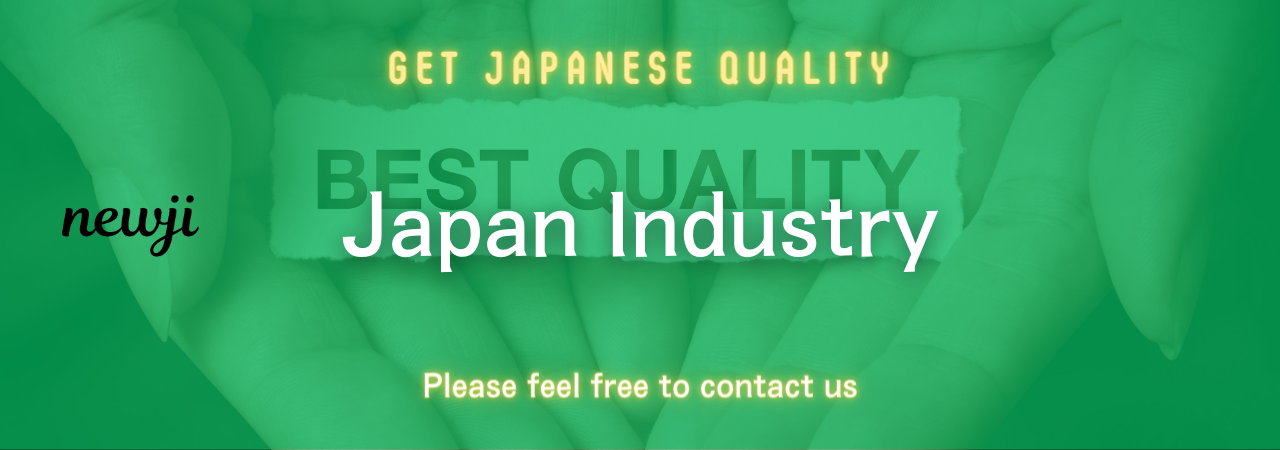
Total Productive Maintenance (TPM) is a comprehensive approach to equipment maintenance that aims to achieve perfect production without accidents, defects, or breakdowns.
Successful implementation of TPM requires the selection of appropriate equipment, which plays a pivotal role in ensuring the overall success of this maintenance strategy.
In this article, we will explore the key elements involved in equipment selection for TPM, and why they are crucial.
We will also offer tips for making the best possible choices for your organization.
目次
Understanding TPM and Its Goals
TPM is a proactive maintenance approach that involves all employees, from operators to management, in maintaining equipment.
The primary objectives of TPM are to improve equipment effectiveness, ensure smooth production processes, reduce downtime, and enhance overall workplace safety.
To achieve these goals, having the right equipment is essential.
Equipment Reliability and Durability
One of the most important factors to consider in TPM is the reliability and durability of the equipment.
Selecting highly reliable and durable machinery ensures that equipment breakdowns are minimized.
Frequent breakdowns not only disrupt production but also incur high repair costs and maintenance time.
When selecting equipment, look for machines known for their longevity and dependability.
Evaluating past performance data and customer reviews can provide valuable insights into the reliability of potential equipment purchases.
Ease of Maintenance
Ease of maintenance is another critical criterion for equipment selection in TPM.
Choosing equipment that is easy to maintain can significantly reduce downtime and increase productivity.
Equipment that allows straightforward access to critical components for inspection, repair, and replacement is ideal.
In addition, user-friendly maintenance manuals and digital interfaces that provide real-time data on equipment health can facilitate maintenance tasks and troubleshooting.
When analyzing equipment, consider the time and effort required to perform routine maintenance tasks.
Compatibility with Existing Systems
The new equipment must be compatible with your existing systems and processes.
Integration challenges can create bottlenecks and negatively impact productivity.
Before making a purchase, assess whether the new equipment can seamlessly integrate with your current production line and systems.
Also, verify that it supports the materials and inputs used in your production processes.
Consult with equipment vendors and conduct compatibility tests to ensure a smooth transition.
Energy Efficiency and Environmental Impact
With increasing emphasis on sustainable practices, the energy efficiency and environmental impact of equipment are vital considerations.
Opt for equipment that consumes less energy and has a minimal environmental footprint.
Energy-efficient machinery not only reduces operational costs but also aligns with green initiatives and regulatory requirements.
When selecting equipment, review its energy consumption ratings and environmental certifications.
Operator Involvement and Skill Levels
Operator involvement is one of the pillars of TPM, emphasizing the importance of selecting equipment that matches the skill levels of your workforce.
Complex machinery that requires specialized training may not be ideal for achieving TPM goals.
On the other hand, equipment that is too simplistic may not meet production demands.
Striking a balance by choosing equipment that is user-friendly yet efficient is crucial.
Providing adequate training and support to operators will ensure that they can effectively use the equipment and contribute to its maintenance.
Training and Support
Training is an essential component for successful equipment operation and maintenance.
When selecting equipment, consider the vendor’s training and support services.
A vendor who offers comprehensive training programs and ongoing support can greatly enhance the effectiveness of your TPM efforts.
Look for vendors who provide on-site training, online resources, and responsive customer support.
This ensures that your team is well-equipped to handle the new machinery and resolve any issues promptly.
Involvement in Selection Process
Involving operators in the equipment selection process can provide valuable insights and promote acceptance of new machinery.
Operators who work with the equipment daily can offer practical perspectives on what features are essential and which equipment best suits their needs.
Engage them in equipment demos, trials, and discussions with vendors to gather feedback.
This collaborative approach fosters a sense of ownership and responsibility among employees, enhancing their commitment to TPM.
Cost Considerations and ROI
While cost is a significant factor in equipment selection, it should not be the sole determinant.
Focus on the total cost of ownership (TCO), which includes the purchase price, operating costs, maintenance expenses, and potential downtime costs.
Investing in high-quality, reliable equipment may have a higher upfront cost but can result in substantial long-term savings through reduced maintenance and downtime.
Calculate the return on investment (ROI) by considering the equipment’s lifespan, productivity gains, and cost savings.
Making informed decisions based on TCO and ROI ensures a cost-effective approach to equipment selection.
Long-Term Viability and Scalability
Consider the long-term viability and scalability of the equipment.
As your organization grows and production demands increase, the equipment should be able to scale accordingly.
Choose equipment that offers upgrade options and can adapt to future technological advancements.
Vendors who provide ongoing updates and enhancements to their equipment can be beneficial in keeping your machinery up-to-date with the latest industry standards.
Choosing the Right Vendor
The selection of the right vendor is as crucial as choosing the right equipment.
A reputable vendor with a proven track record can be a valuable partner in your TPM journey.
Evaluate vendors based on their industry experience, customer reviews, and the range of products they offer.
Inquire about their service and support capabilities, including spare parts availability, response time, and maintenance services.
A strong vendor relationship ensures that you have access to reliable equipment and support, enhancing your TPM implementation.
Vendor Reputation and Experience
Research the vendor’s reputation and experience within the industry.
Companies with a long history of delivering high-quality equipment and exceptional customer service are more likely to meet your expectations.
Consider their client testimonials, case studies, and any awards or certifications they have received.
A reputable vendor will be transparent about their successes and challenges, providing you with a clear understanding of their capabilities.
Service Contracts and Guarantees
Review the service contracts and guarantees offered by the vendor.
Service contracts should outline the terms of maintenance, repairs, and support services.
Ensure that the vendor provides guarantees or warranties that protect your investment and cover potential defects or issues.
Understand the terms and conditions of these contracts to avoid any unforeseen costs or complications.
In conclusion, selecting the right equipment for successful TPM is a multifaceted process that involves careful consideration of reliability, maintenance ease, compatibility, energy efficiency, operator involvement, cost, and vendor relationships.
By prioritizing these elements, you can make informed decisions that enhance equipment effectiveness, minimize downtime, and support a productive and safe working environment.
Implementing TPM with the right equipment paves the way for continuous improvement and operational excellence.
資料ダウンロード
QCD調達購買管理クラウド「newji」は、調達購買部門で必要なQCD管理全てを備えた、現場特化型兼クラウド型の今世紀最高の購買管理システムとなります。
ユーザー登録
調達購買業務の効率化だけでなく、システムを導入することで、コスト削減や製品・資材のステータス可視化のほか、属人化していた購買情報の共有化による内部不正防止や統制にも役立ちます。
NEWJI DX
製造業に特化したデジタルトランスフォーメーション(DX)の実現を目指す請負開発型のコンサルティングサービスです。AI、iPaaS、および先端の技術を駆使して、製造プロセスの効率化、業務効率化、チームワーク強化、コスト削減、品質向上を実現します。このサービスは、製造業の課題を深く理解し、それに対する最適なデジタルソリューションを提供することで、企業が持続的な成長とイノベーションを達成できるようサポートします。
オンライン講座
製造業、主に購買・調達部門にお勤めの方々に向けた情報を配信しております。
新任の方やベテランの方、管理職を対象とした幅広いコンテンツをご用意しております。
お問い合わせ
コストダウンが利益に直結する術だと理解していても、なかなか前に進めることができない状況。そんな時は、newjiのコストダウン自動化機能で大きく利益貢献しよう!
(Β版非公開)