- お役立ち記事
- Key Process Improvements to Achieve High Precision in Polishing
Key Process Improvements to Achieve High Precision in Polishing
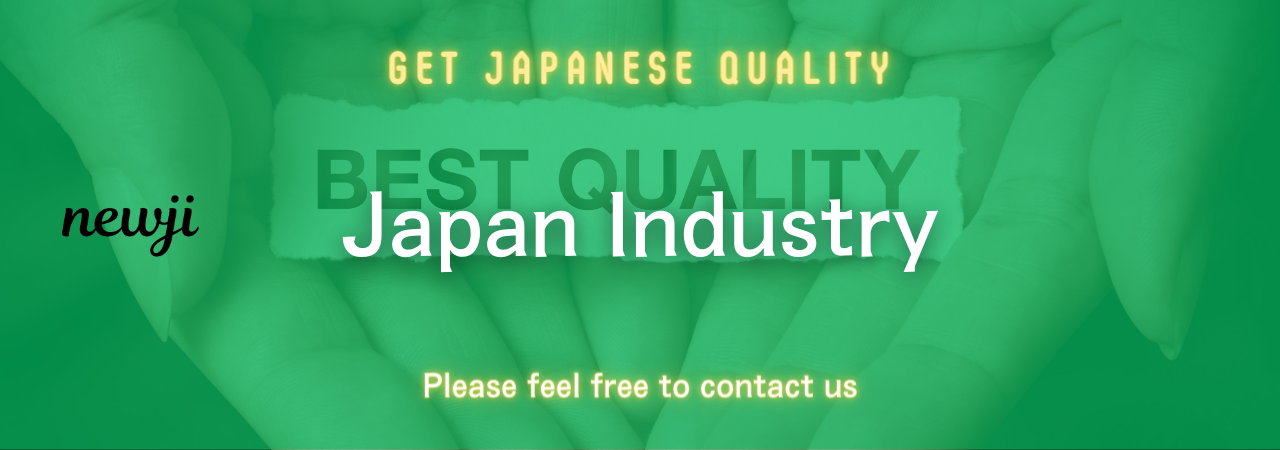
In today’s fast-paced industrial environment, achieving high precision in polishing is crucial for businesses focused on manufacturing and production.
Polishing involves the use of abrasives to create a smooth and shiny surface on various materials like metals, ceramics, and plastics.
Achieving high-precision polishing ensures that the end products meet stringent quality standards, resulting in customer satisfaction and reduced production costs.
目次
Understanding the Basics of Polishing
Polishing is a multi-step process that involves several techniques such as grinding, lapping, and buffing.
Each step must be meticulously executed to achieve the desired results.
Quality abrasives play a significant role in the efficiency of the polishing process.
Different materials require specific types of abrasives to achieve the optimal finish.
Grinding
Grinding is the initial stage in the polishing process.
It involves removing large amounts of material to shape the workpiece.
Coarse abrasives are typically used in this stage to eliminate any irregularities on the surface.
Correct grinding techniques set the foundation for achieving a high-quality finish in the later stages.
Lapping
Lapping follows grinding and uses finer abrasives to achieve a smoother surface.
This stage helps to eliminate the scratches left by grinding, bringing the workpiece closer to its final polished form.
Lapping ensures that the surface is uniform and free of defects.
Buffing
Buffing is the final step in the polishing process.
It involves using a soft cloth and a fine abrasive to achieve a mirror-like finish.
Buffing enhances the surface’s aesthetic appeal and often serves as the final quality check before the product is deemed complete.
Key Process Improvements for High-Precision Polishing
Achieving high precision in polishing requires continual process improvements.
Below are some key areas to focus on for improved polishing results.
Choosing the Right Abrasives
Selecting the appropriate abrasives is crucial for high-precision polishing.
Different materials have varying hardness levels, which necessitates the use of specific abrasives to achieve optimum results.
For instance, diamond abrasives are commonly used for polishing hard materials like ceramics and metals, while softer materials may require silicon carbide or aluminum oxide abrasives.
Optimizing Machine Parameters
The settings on polishing machines play a significant role in determining the final quality of the polished surface.
Parameters such as speed, pressure, and time must be meticulously calibrated.
Slow and consistent speeds often yield the best results, as excessive speed can generate heat and cause defects.
Implementing Automation
Automation can greatly enhance the efficiency and consistency of the polishing process.
Automated polishing machines can perform repetitive tasks with high precision, reducing the likelihood of human error.
Robotic arms equipped with advanced sensors can adapt in real-time to variations in the workpiece, ensuring a uniform finish.
Regular Maintenance
Regular maintenance of polishing equipment is essential for achieving consistent results.
Wear and tear on abrasives and machine components can negatively impact the quality of the polished surface.
Scheduled maintenance checks help identify and rectify issues before they affect the production process.
Investing in Training
Skilled operators are invaluable assets in the polishing industry.
Continuous training ensures that operators are well-versed in the latest techniques and technologies.
Investing in employee training programs helps maintain high standards and fosters a culture of continuous improvement.
The Role of Technology in Precision Polishing
Advancements in technology have significantly impacted the precision polishing industry.
Below are some technological innovations that have revolutionized the field.
CNC Machines
Computer Numerical Control (CNC) machines have transformed the polishing process by providing unparalleled precision.
These machines can follow complex patterns and execute tasks with minimal deviations, resulting in a consistently high-quality finish.
Advanced Materials
The development of advanced materials like nanodiamonds has made it possible to achieve ultra-smooth surfaces.
These materials offer superior hardness and durability, making them ideal for high-precision applications.
Software Solutions
Software solutions enable real-time monitoring and control of the polishing process.
Innovative software can analyze data and provide insights into optimizing machine parameters, reducing waste, and enhancing efficiency.
3D Printing
3D printing technology has found applications in creating custom polishing tools and fixtures.
This flexibility allows for precise control over the surface quality and helps in achieving intricate designs and patterns.
Applications of High-Precision Polishing
High-precision polishing is essential in various industries, including aerospace, automotive, medical, and electronics.
Aerospace
In the aerospace industry, components must meet stringent quality and safety standards.
High-precision polishing ensures that parts like turbine blades and engine components have the necessary surface finish to perform under extreme conditions.
Automotive
The automotive sector demands high-quality finishes for both aesthetic and functional purposes.
Polishing interior and exterior car parts to a mirror-like finish enhances visual appeal and overall quality.
Medical
In the medical field, precision-polished instruments and implants are crucial for ensuring patient safety and effective treatment.
Smooth surfaces reduce the risk of contamination and increase the longevity of medical devices.
Electronics
The electronics industry relies on high-precision polishing for components like semiconductors and lenses.
Polishing ensures optimal performance and functionality of these sensitive parts.
Conclusion
Achieving high precision in polishing requires a combination of skilled labor, advanced technology, and continual process improvements.
By focusing on the key areas outlined in this article, businesses can optimize their polishing processes to produce high-quality results consistently.
With the right techniques and tools, high-precision polishing can significantly enhance the quality and performance of finished products.
資料ダウンロード
QCD調達購買管理クラウド「newji」は、調達購買部門で必要なQCD管理全てを備えた、現場特化型兼クラウド型の今世紀最高の購買管理システムとなります。
ユーザー登録
調達購買業務の効率化だけでなく、システムを導入することで、コスト削減や製品・資材のステータス可視化のほか、属人化していた購買情報の共有化による内部不正防止や統制にも役立ちます。
NEWJI DX
製造業に特化したデジタルトランスフォーメーション(DX)の実現を目指す請負開発型のコンサルティングサービスです。AI、iPaaS、および先端の技術を駆使して、製造プロセスの効率化、業務効率化、チームワーク強化、コスト削減、品質向上を実現します。このサービスは、製造業の課題を深く理解し、それに対する最適なデジタルソリューションを提供することで、企業が持続的な成長とイノベーションを達成できるようサポートします。
オンライン講座
製造業、主に購買・調達部門にお勤めの方々に向けた情報を配信しております。
新任の方やベテランの方、管理職を対象とした幅広いコンテンツをご用意しております。
お問い合わせ
コストダウンが利益に直結する術だと理解していても、なかなか前に進めることができない状況。そんな時は、newjiのコストダウン自動化機能で大きく利益貢献しよう!
(Β版非公開)