- お役立ち記事
- The difference between End-face Machining and Flange Machining
The difference between End-face Machining and Flange Machining
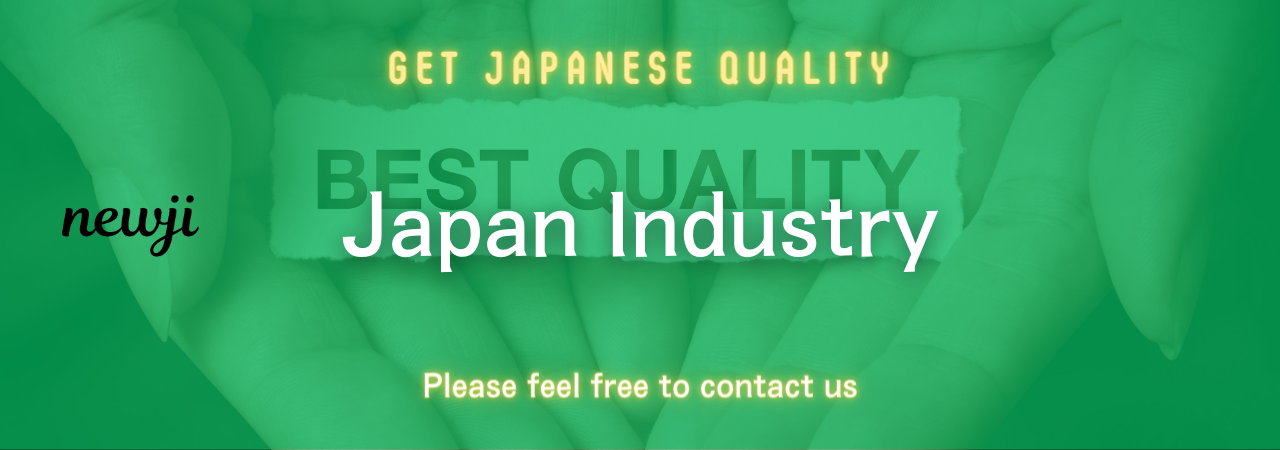
End-face machining and flange machining are critical processes in various manufacturing and engineering sectors.
They both serve essential roles in the production and finishing of components used in machinery, piping systems, and other industrial applications.
While they might seem similar at first glance, they have distinct differences in application, technique, and outcomes.
Understanding these differences can help you choose the right process for your specific needs.
目次
What is End-Face Machining?
End-face machining involves processing the end surfaces of cylindrical or disc-shaped workpieces.
This technique is commonly used in the production of shafts, rotors, and other components where smooth and precise end surfaces are crucial for assembly or functionality.
Often executed on a lathe, the main goal of end-face machining is to create flat, perpendicular end faces with high surface quality.
End-face machining starts with securing the workpiece in a chuck or another type of holder.
The cutting tool is then advanced towards the end surface of the workpiece as it rotates.
By carefully controlling the feed rate and depth of cut, machinists can achieve the desired surface finish and dimensional accuracy.
This process may also involve subsequent steps such as grinding or polishing to meet stringent specifications.
What is Flange Machining?
Flange machining, on the other hand, specifically deals with the processing of flanges—connecting components used to join pipes, valves, pumps, and other equipment in piping systems.
Flanges are vital for ensuring leak-proof and structurally sound connections in various applications, such as oil and gas pipelines, water supply systems, and chemical processing plants.
During flange machining, the focus is on creating precise surfaces, bolt holes, and other features required for seamless connections.
This process involves several steps including facing, drilling, tapping, and sometimes even milling to achieve the desired specifications.
The machining operations are typically carried out on specialized machines, such as flange lathes or CNC machining centers, to ensure high-quality and repeatable results.
Differences in Applications
End-Face Machining Applications
End-face machining is primarily used in industries where the quality and precision of the end surfaces directly impact the performance and longevity of the parts.
For example, in the automotive sector, end-face machining is critical for producing engine components like crankshafts and camshafts.
In the aerospace industry, this technique is used to manufacture parts such as turbine shafts and landing gear components.
Other applications include the production of hydraulic cylinders, electric motor shafts, and various types of industrial rollers.
Flange Machining Applications
Flange machining is indispensable for industries that rely on robust and reliable piping systems.
The oil and gas sector is a prime example where flange machining ensures the integrity of pipe connections in high-pressure environments.
In water treatment plants, flanges machined to precise standards are crucial for leak-proof connections.
The chemical processing industry also benefits from accurately machined flanges to ensure safe and efficient transport of hazardous materials.
Additionally, flange machining is essential in HVAC systems, shipbuilding, and industrial machinery.
Differences in Techniques
End-Face Machining Techniques
The primary technique used in end-face machining is turning.
The workpiece is rotated on a lathe while a cutting tool shapes the end face.
Depending on the material and required surface finish, additional processes like grinding or polishing may be applied.
CNC lathes are often used for complex and high-precision end-face machining tasks, providing consistency and speed.
Flange Machining Techniques
Flange machining involves various processes to achieve the needed precision and functionality.
Facing ensures that the flange face is flat and perpendicular to the pipe axis.
Drilling and tapping create the holes needed for bolting flanges together.
In some cases, milling may be used to form slots or other specific features.
The use of CNC machines is prevalent in flange machining as well, ensuring high accuracy and repeatability.
Material Considerations
Materials in End-Face Machining
The materials commonly used in end-face machining include metals like steel, aluminum, and titanium.
These materials require specific cutting tools and parameters to achieve optimal results.
Advanced ceramics and composites are also machined using this technique, especially in industries like aerospace and medical device manufacturing where high strength and low weight are crucial.
Materials in Flange Machining
Flange machining typically deals with materials like carbon steel, stainless steel, and various alloys.
These materials need to be tough and resistant to corrosion, especially in applications exposed to harsh environments.
Copper, bronze, and PVC are also used in flange manufacturing, depending on the application’s requirements.
The Importance of Precision
Precision is a critical factor in both end-face machining and flange machining.
In end-face machining, precision ensures that components fit together perfectly, leading to improved performance and longevity.
For example, an imprecisely machined shaft end can result in misalignment, vibration, and premature wear in machinery.
In flange machining, precision is crucial for leak prevention and structural integrity.
Improperly machined flanges can lead to connection failures, leaks, and potentially catastrophic consequences in systems carrying hazardous materials.
Choosing the Right Machining Process
Selecting between end-face machining and flange machining depends on the specific requirements of your project.
If you need to create precise end surfaces for rotational components, end-face machining is the way to go.
Conversely, if your project involves creating or modifying connections in piping systems, flange machining is essential.
Understanding the material properties, required precision, and application context can further guide your decision.
In many cases, consulting with a machining expert or engineer can help you make the best choice, ensuring that your components are manufactured to the highest standards.
End-face machining and flange machining are both vital but distinct processes in the world of manufacturing.
By understanding their differences and applications, you can make informed decisions that enhance the quality and performance of your products and systems.
資料ダウンロード
QCD調達購買管理クラウド「newji」は、調達購買部門で必要なQCD管理全てを備えた、現場特化型兼クラウド型の今世紀最高の購買管理システムとなります。
ユーザー登録
調達購買業務の効率化だけでなく、システムを導入することで、コスト削減や製品・資材のステータス可視化のほか、属人化していた購買情報の共有化による内部不正防止や統制にも役立ちます。
NEWJI DX
製造業に特化したデジタルトランスフォーメーション(DX)の実現を目指す請負開発型のコンサルティングサービスです。AI、iPaaS、および先端の技術を駆使して、製造プロセスの効率化、業務効率化、チームワーク強化、コスト削減、品質向上を実現します。このサービスは、製造業の課題を深く理解し、それに対する最適なデジタルソリューションを提供することで、企業が持続的な成長とイノベーションを達成できるようサポートします。
オンライン講座
製造業、主に購買・調達部門にお勤めの方々に向けた情報を配信しております。
新任の方やベテランの方、管理職を対象とした幅広いコンテンツをご用意しております。
お問い合わせ
コストダウンが利益に直結する術だと理解していても、なかなか前に進めることができない状況。そんな時は、newjiのコストダウン自動化機能で大きく利益貢献しよう!
(Β版非公開)