- お役立ち記事
- The difference between Material Ordering and Parts Ordering
The difference between Material Ordering and Parts Ordering
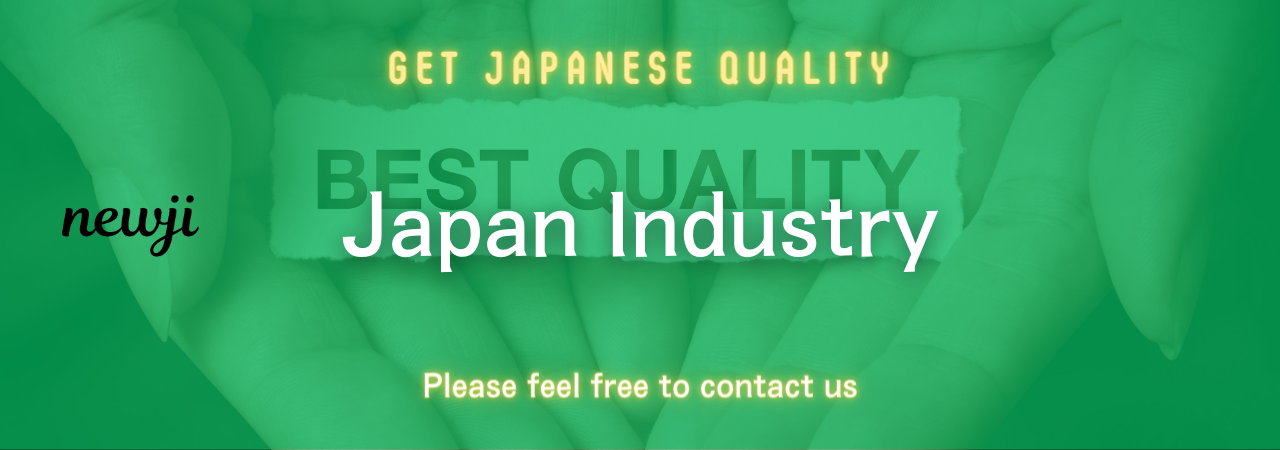
When dealing with production, manufacturing, or even simple DIY projects, you might hear the terms “material ordering” and “parts ordering.” Both are crucial processes that contribute to the completion of a project. However, they serve different purposes and involve distinct steps.
Understanding the difference between these two can greatly improve efficiency and reduce mistakes. Let’s explore the nuances of material ordering and parts ordering and why both are essential for successful project execution.
目次
What is Material Ordering?
Material ordering refers to the process of procuring raw materials required for production or manufacturing activities.
These raw materials are the essential elements that will be transformed into a finished product through various processes such as cutting, welding, assembling, or painting.
For example, if you’re building a wooden table, material ordering would involve getting wood, nails, varnish, and other raw materials needed for the project.
Material ordering ensures that you have all the fundamental substances necessary to start and complete your work.
The Importance of Material Ordering
Material ordering is the backbone of any production cycle.
It ensures the availability of necessary ingredients to kickstart and sustain production activities.
Without the right materials, production can come to a halt, resulting in delays and increased costs.
Proper planning and timely ordering of materials can prevent shortages and overstock situations, thereby optimizing inventory management.
The Steps Involved in Material Ordering
Identify Requirements: First, you need to determine what materials are required for the project. This involves understanding the project scope and specifications.
Sourcing Suppliers: Next, identify potential suppliers who can provide the required materials. Quality, cost, and delivery time are critical factors to consider when choosing suppliers.
Placing Orders: After selecting the supplier, place orders specifying the quantity, quality, and delivery schedule.
Receiving and Inspection: Once materials are delivered, inspect them to ensure they meet the required standards and specifications.
What is Parts Ordering?
Parts ordering, on the other hand, involves procuring individual components or sub-assemblies that make up the final product.
These parts are usually pre-made or pre-manufactured and are not raw materials.
For example, in building a car, parts ordering would involve getting wheels, engine components, seats, bolts, and other pre-made components.
Parts ordering is about obtaining the pieces that will be assembled to create a complete, functional product.
The Importance of Parts Ordering
Parts ordering is crucial for the assembly phase of any project.
It ensures that all the individual components are available when needed, allowing for smooth and uninterrupted assembly processes.
Timely ordering and receiving of parts can significantly reduce downtime and increase operational efficiency. Accurate parts ordering also helps in maintaining quality control and meeting project deadlines.
The Steps Involved in Parts Ordering
Identify Required Parts: Just like material ordering, this begins with identifying the specific parts needed for the project, often listed in a Bill of Materials (BOM).
Find Reliable Suppliers: Seek out suppliers who can provide high-quality parts at competitive prices. Supplier reliability and part quality are crucial aspects to evaluate.
Order Placement: Place orders specifying the required part numbers, quantities, and delivery schedules.
Receiving and Quality Check: Upon delivery, inspect the parts to ensure they meet the necessary specifications and quality standards.
Key Differences Between Material Ordering and Parts Ordering
Nature of Items
The primary difference lies in what is being ordered.
Material ordering focuses on acquiring raw materials, such as metals, plastics, chemicals, and other basic substances.
In contrast, parts ordering is about procuring pre-manufactured components and assemblies.
Stage of Production
Material ordering is typically associated with the initial stages of production, where raw materials are transformed into intermediate or finished products.
Parts ordering, however, is linked to later stages, where pre-made components are assembled to form the final product.
Supplier Type
Suppliers for material ordering are generally manufacturers or distributors of raw materials.
In contrast, parts ordering requires suppliers who specialize in providing pre-made components, often original equipment manufacturers (OEMs) or aftermarket suppliers.
Inventory Management
Both material and parts ordering require effective inventory management, but they differ in complexity.
Material inventory management involves handling bulk quantities and various types of raw materials, whereas parts inventory management deals with numerous individual components, each with specific part numbers and specifications.
How to Balance Material and Parts Ordering
Balancing material and parts ordering is essential for smooth project execution. Here’s how to achieve this balance:
Effective Planning
Proper planning ensures accurate forecasting of both material and parts requirements.
Using project management tools and software can help track material and part needs, ensuring timely procurement.
Supplier Collaboration
Build strong relationships with suppliers for both materials and parts.
Good communication and collaboration can lead to better pricing, timely deliveries, and improved quality.
Inventory Monitoring
Regularly monitor inventory levels for both materials and parts.
Implement inventory management systems to avoid overstocking or running out of essential items.
Just-In-Time Ordering
Adopt Just-In-Time (JIT) ordering strategies to reduce excess inventory and storage costs.
JIT ensures that materials and parts arrive exactly when needed, minimizing waste and improving efficiency.
Understanding the differences between material ordering and parts ordering can greatly enhance the efficiency of your projects.
Both play vital roles, and their importance cannot be overstated.
By mastering both processes, you can ensure that your projects run smoothly and are completed on time and within budget.
So, the next time you embark on a project, remember the distinct yet complementary roles that material ordering and parts ordering play.
資料ダウンロード
QCD調達購買管理クラウド「newji」は、調達購買部門で必要なQCD管理全てを備えた、現場特化型兼クラウド型の今世紀最高の購買管理システムとなります。
ユーザー登録
調達購買業務の効率化だけでなく、システムを導入することで、コスト削減や製品・資材のステータス可視化のほか、属人化していた購買情報の共有化による内部不正防止や統制にも役立ちます。
NEWJI DX
製造業に特化したデジタルトランスフォーメーション(DX)の実現を目指す請負開発型のコンサルティングサービスです。AI、iPaaS、および先端の技術を駆使して、製造プロセスの効率化、業務効率化、チームワーク強化、コスト削減、品質向上を実現します。このサービスは、製造業の課題を深く理解し、それに対する最適なデジタルソリューションを提供することで、企業が持続的な成長とイノベーションを達成できるようサポートします。
オンライン講座
製造業、主に購買・調達部門にお勤めの方々に向けた情報を配信しております。
新任の方やベテランの方、管理職を対象とした幅広いコンテンツをご用意しております。
お問い合わせ
コストダウンが利益に直結する術だと理解していても、なかなか前に進めることができない状況。そんな時は、newjiのコストダウン自動化機能で大きく利益貢献しよう!
(Β版非公開)