- お役立ち記事
- Planning for Future Demand with Production Capacity Analysis
Planning for Future Demand with Production Capacity Analysis
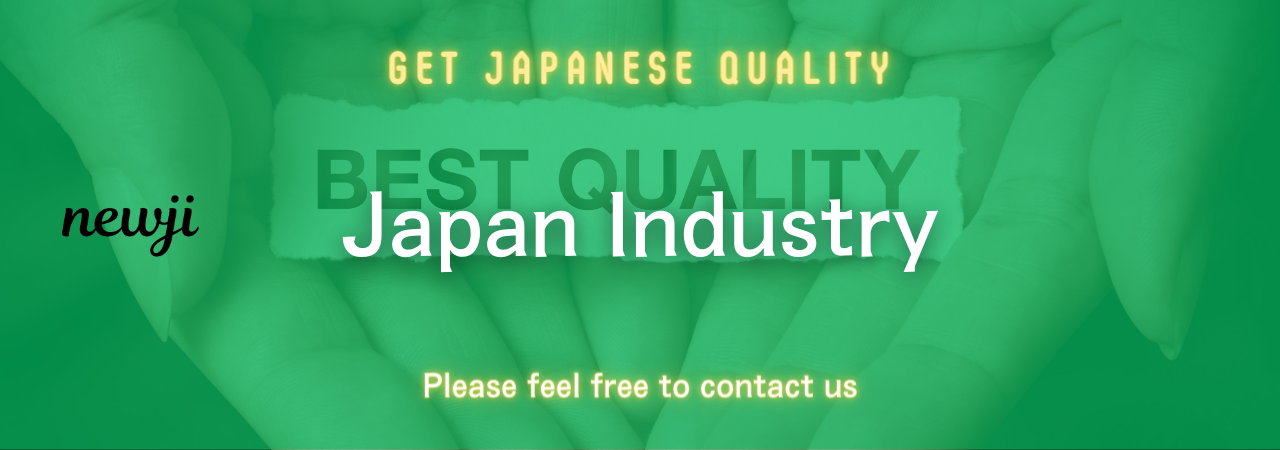
In today’s fast-paced and ever-evolving market, it is crucial for businesses to anticipate future demand efficiently.
Planning for future demand with production capacity analysis is a strategic approach that ensures a company is prepared to meet customer needs without incurring unnecessary costs.
By employing effective analytics and forecasting methods, companies can align their manufacturing capabilities to meet anticipated market demand.
目次
Understanding Production Capacity
Production capacity refers to the maximum output a company can produce within a given period.
It includes the total resources available, such as labor, machinery, and raw materials, that can be utilized to manufacture products.
Understanding your production capacity is the foundation for efficient planning and ensuring that you can meet customer demand.
Types of Production Capacity
There are several types of production capacities that businesses need to consider:
* **Theoretical Capacity:** This is the ideal maximum output possible, assuming no downtime or maintenance issues.
It represents the full utilization of available resources, but it is rarely achievable in real-world scenarios.
* **Practical Capacity:** Practical capacity takes into account scheduled maintenance, breaks, and other predictable downtime.
It provides a more realistic measure of what a production line can achieve.
* **Capacity Utilization:** This measure indicates the extent to which a company is using its production capacity.
It is often expressed as a percentage and helps identify areas where efficiency can be improved.
The Importance of Demand Forecasting
Accurate demand forecasting is critical for effective production planning.
It involves predicting future customer demand for products or services using data, trends, and various forecasting methods.
Without accurate forecasting, a business may either produce too much, leading to excess inventory, or too little, resulting in stockouts and lost sales.
Methods of Demand Forecasting
There are several methods businesses can use for demand forecasting:
* **Qualitative Methods:** These methods rely on expert opinions and market research.
They are useful when historical data is limited or when introducing a new product to the market.
* **Quantitative Methods:** These involve statistical techniques and historical data to predict future demand.
Common quantitative methods include time series analysis, regression analysis, and economic indicators.
* **Combination Methods:** Often, the best approach is to combine qualitative and quantitative methods.
This hybrid approach leverages the strengths of both to create more accurate forecasts.
Tools for Demand Forecasting
Modern technology offers a variety of tools and software to enhance demand forecasting accuracy.
These include:
* **ERP Systems:** Enterprise Resource Planning (ERP) systems integrate various business functions, including demand forecasting, to provide a comprehensive view of operations.
* **Machine Learning:** Advanced algorithms can analyze large datasets to identify patterns and trends, making them powerful tools for demand forecasting.
* **Scenario Analysis:** This involves creating different demand scenarios based on various factors, such as market trends, economic conditions, and competitor actions.
It helps businesses prepare for potential changes in demand.
Aligning Production Capacity with Demand
Once demand forecasting is done, the next step is to align production capacity with the anticipated demand.
This involves several strategies and techniques to ensure optimal resource utilization.
Capacity Planning
Capacity planning is the process of determining the production capacity needed to meet changing demands.
It can be divided into three main types:
* **Long-term Planning:** Focuses on capacity adjustments that take a year or more to implement.
It includes decisions related to plant expansions, acquiring new machinery, and workforce training.
* **Medium-term Planning:** Covers a period of 6 to 18 months.
It involves scheduling maintenance, managing seasonal demand fluctuations, and optimizing production processes.
* **Short-term Planning:** Deals with daily or weekly adjustments in production schedules to respond to immediate demand changes.
It includes managing workforce shifts, machine allocations, and inventory control.
Flexibility in Production
Having a flexible production system is vital for responding to unforeseen changes in demand.
Flexibility can be achieved through:
* **Modular Production Lines:** These allow quick reconfiguration of production lines to accommodate different products or variations.
* **Cross-trained Workforce:** Employees trained to perform multiple tasks can be reassigned as needed to manage demand fluctuations.
* **Supplier Relationships:** Strong relationships with suppliers ensure quick access to raw materials and components, reducing lead times.
Inventory Management
Proper inventory management ensures that a company has the right amount of stock to meet demand without overproducing.
Key strategies include:
* **Just-in-Time (JIT):** This approach minimizes inventory by producing goods only when they are needed, reducing carrying costs and waste.
* **Safety Stock:** Keeping a small buffer of extra inventory helps prevent stockouts during unexpected demand surges.
* **ABC Analysis:** This technique categorizes inventory into three groups (A, B, C) based on their importance, allowing more focus on critical items.
Continuous Improvement and Monitoring
Effective demand planning and capacity analysis require continuous improvement and monitoring.
Regularly reviewing performance metrics and making necessary adjustments ensure that production remains aligned with demand.
Key Performance Indicators (KPIs)
Monitoring KPIs helps assess the effectiveness of your demand planning and capacity strategies.
Important KPIs include:
* **Production Efficiency:** Measures how well production resources are being utilized.
High efficiency indicates optimal resource use.
* **Demand Forecast Accuracy:** Compares predicted demand to actual sales.
High accuracy reduces the risk of overproduction or stockouts.
* **Lead Time:** The time taken to fulfill an order from the moment it is placed.
Shorter lead times improve customer satisfaction.
Feedback Loops
Establishing feedback loops allows for continuous learning and improvement.
Collecting data on production performance, customer feedback, and market trends helps refine forecasting models and production strategies.
Regularly conducting post-mortem analyses of past demand forecasts enhances future forecasting accuracy.
Understanding the reasons for discrepancies between forecasted and actual demand helps identify areas for improvement.
Conclusion
Planning for future demand with production capacity analysis is essential for any business aiming to stay competitive in today’s market.
By understanding production capacity, accurately forecasting demand, and aligning resources accordingly, companies can meet customer needs efficiently.
Continuous monitoring and improvement of these processes ensure long-term success and growth.
Investing in the right tools and strategies for demand planning and capacity analysis not only reduces costs but also enhances customer satisfaction and loyalty.
In a dynamic market, staying ahead with proactive planning is the key to sustained success.
資料ダウンロード
QCD調達購買管理クラウド「newji」は、調達購買部門で必要なQCD管理全てを備えた、現場特化型兼クラウド型の今世紀最高の購買管理システムとなります。
ユーザー登録
調達購買業務の効率化だけでなく、システムを導入することで、コスト削減や製品・資材のステータス可視化のほか、属人化していた購買情報の共有化による内部不正防止や統制にも役立ちます。
NEWJI DX
製造業に特化したデジタルトランスフォーメーション(DX)の実現を目指す請負開発型のコンサルティングサービスです。AI、iPaaS、および先端の技術を駆使して、製造プロセスの効率化、業務効率化、チームワーク強化、コスト削減、品質向上を実現します。このサービスは、製造業の課題を深く理解し、それに対する最適なデジタルソリューションを提供することで、企業が持続的な成長とイノベーションを達成できるようサポートします。
オンライン講座
製造業、主に購買・調達部門にお勤めの方々に向けた情報を配信しております。
新任の方やベテランの方、管理職を対象とした幅広いコンテンツをご用意しております。
お問い合わせ
コストダウンが利益に直結する術だと理解していても、なかなか前に進めることができない状況。そんな時は、newjiのコストダウン自動化機能で大きく利益貢献しよう!
(Β版非公開)