- お役立ち記事
- Secrets to Improving Part Performance with Heat Treatment Technologies
Secrets to Improving Part Performance with Heat Treatment Technologies
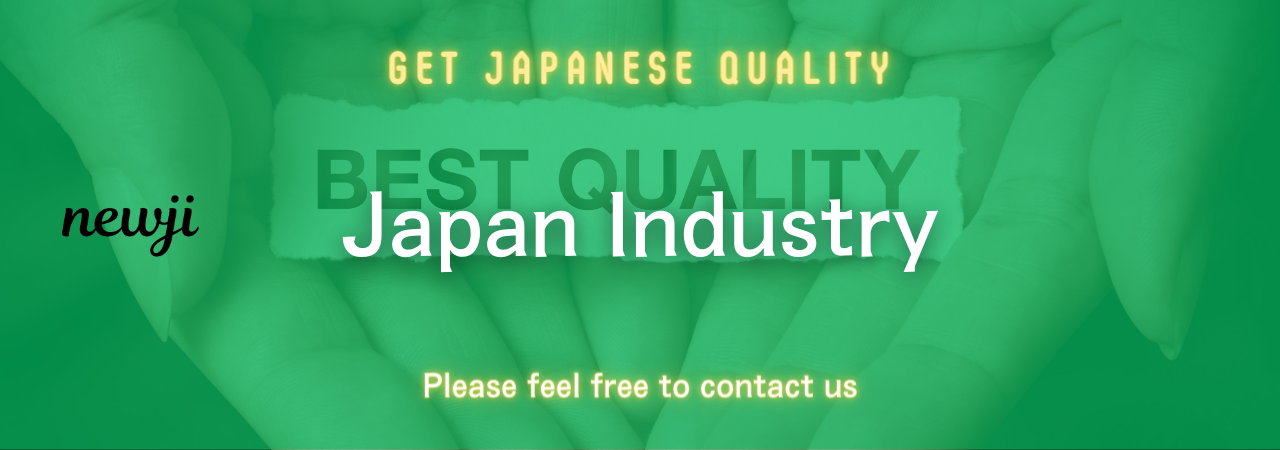
Heat treatment is an essential process in manufacturing to enhance the performance and durability of parts. This process involves heating and cooling metals in a controlled manner to alter their physical and sometimes chemical properties. By using various heat treatment technologies, manufacturers can significantly improve the characteristics of metal components, making them more suitable for their intended applications.
目次
Understanding Heat Treatment
What is Heat Treatment?
Heat treatment is a series of controlled heating and cooling operations applied to metals to change their structure.
These changes affect the metal’s physical properties, such as hardness, strength, toughness, and ductility.
By adjusting the heating and cooling temperatures, along with the rate at which these changes occur, engineers can tailor metal properties to meet specific requirements.
The Importance of Heat Treatment
Heat treatment is crucial in many industries, including automotive, aerospace, construction, and manufacturing.
Properly treated metals perform better under high stress and prolonged use, thereby extending the life of machine parts and structural components.
This process reduces wear and tear, minimizing the frequency of maintenance and replacement, and thus saving costs.
Common Heat Treatment Techniques
Annealing
Annealing involves heating a metal to a specific temperature, holding it at that temperature for a given period, and then cooling it down slowly.
This process primarily aims to reduce hardness, improve machinability, and relieve internal stresses in the metal.
Annealing is commonly used for metals like steel, aluminum, and copper.
Quenching
Quenching involves rapidly cooling a heated metal to lock in a hard, brittle structure.
This technique usually incorporates water, oil, or another cooling medium to quickly bring down the temperature of the metal.
Quenching is often used to increase the hardness and strength of steel and other alloys.
Tempering
Tempering follows quenching to reduce brittleness while maintaining hardness.
In this process, the quenched metal is heated to a temperature below its critical point and then allowed to cool naturally.
This method increases the toughness of the metal and is especially vital for tools and blades that need a balance of hardness and flexibility.
Normalizing
Normalizing involves heating the metal to a specific temperature and then allowing it to cool in the air.
This technique refines the grain structure of the metal, making it more uniform and improving its mechanical properties.
Normalizing is especially beneficial for ferrous metals like steel.
Benefits of Heat Treatment on Part Performance
Enhanced Strength
Heat treatment significantly improves the strength of metal parts, allowing them to withstand higher loads and stress.
By optimizing the internal structure, heat-treated metals are less likely to deform or break under extreme conditions.
Improved Hardness
Increased hardness is another significant advantage of heat treatment.
Stronger, harder metals exhibit greater resistance to wear and tear, making them ideal for cutting tools, gears, and other high-stress applications.
Better Flexibility
Certain heat treatment processes, such as tempering, can enhance the flexibility of metals while maintaining their strength and hardness.
This balance is crucial for applications that require components to absorb impact without cracking.
Stress Relief
Heat treatment can also relieve internal stresses that develop during the manufacturing process.
These stresses can cause metal parts to warp or crack over time.
By relieving these stresses, heat treatment helps maintain the dimensional stability and integrity of the parts.
Increased Durability
Overall, the various benefits of heat treatment culminate in increased durability and longevity of metal components.
This extension of part life translates to cost savings in maintenance and replacement, as well as improved reliability in critical applications.
Advanced Heat Treatment Methods
Case Hardening
Case hardening, or surface hardening, involves hardening the metal’s surface while maintaining a softer, ductile core.
Methods like carburizing, nitriding, and cyaniding introduce additional elements such as carbon or nitrogen to the surface.
This results in a wear-resistant exterior and a tough interior, ideal for components like gears and shafts.
Induction Hardening
Induction hardening uses electromagnetic induction to heat the metal rapidly, followed by immediate quenching.
This localized heating focuses on specific areas that require hardening, making it energy-efficient and suitable for precision parts.
Vacuum Heat Treatment
Vacuum heat treatment occurs in a vacuum-sealed chamber, minimizing oxidation and contamination.
This method produces clean, oxide-free surfaces and is especially useful for high-precision components in aerospace and medical fields.
Choosing the Right Heat Treatment Process
Material Type
The type of material being treated significantly influences the choice of heat treatment method.
For example, steel can undergo almost all heat treatment processes, while aluminum typically only benefits from processes like annealing and aging.
End-Use Application
The intended application also dictates the heat treatment process.
Parts exposed to high-stress environments may require hardening and tempering, whereas components needing high dimensional stability might benefit from annealing and normalizing.
Cost and Efficiency
While heat treatment offers numerous benefits, the costs associated with different processes can vary.
Manufacturers must weigh the cost of the heat treatment against the performance improvements to determine the most cost-effective solution.
Conclusion
Heat treatment technologies play a crucial role in improving part performance across various industries.
Understanding the key techniques and their benefits allows manufacturers to optimize their processes and produce stronger, more durable components.
By selecting the right heat treatment method based on material type, application, and cost considerations, businesses can ensure their products meet the highest standards of performance and reliability.
資料ダウンロード
QCD調達購買管理クラウド「newji」は、調達購買部門で必要なQCD管理全てを備えた、現場特化型兼クラウド型の今世紀最高の購買管理システムとなります。
ユーザー登録
調達購買業務の効率化だけでなく、システムを導入することで、コスト削減や製品・資材のステータス可視化のほか、属人化していた購買情報の共有化による内部不正防止や統制にも役立ちます。
NEWJI DX
製造業に特化したデジタルトランスフォーメーション(DX)の実現を目指す請負開発型のコンサルティングサービスです。AI、iPaaS、および先端の技術を駆使して、製造プロセスの効率化、業務効率化、チームワーク強化、コスト削減、品質向上を実現します。このサービスは、製造業の課題を深く理解し、それに対する最適なデジタルソリューションを提供することで、企業が持続的な成長とイノベーションを達成できるようサポートします。
オンライン講座
製造業、主に購買・調達部門にお勤めの方々に向けた情報を配信しております。
新任の方やベテランの方、管理職を対象とした幅広いコンテンツをご用意しております。
お問い合わせ
コストダウンが利益に直結する術だと理解していても、なかなか前に進めることができない状況。そんな時は、newjiのコストダウン自動化機能で大きく利益貢献しよう!
(Β版非公開)