- お役立ち記事
- The difference between Yield Improvement and Defect Reduction
The difference between Yield Improvement and Defect Reduction
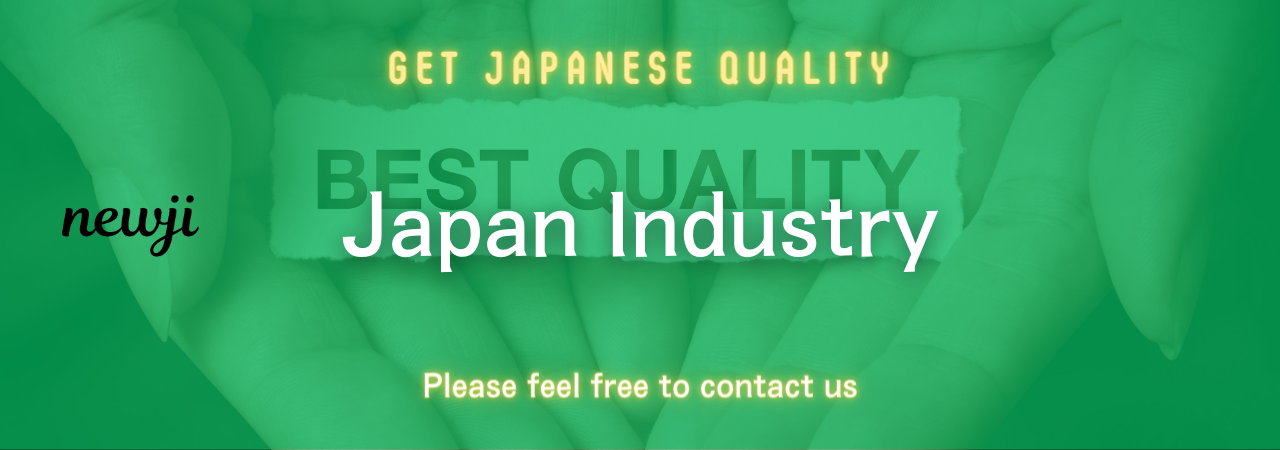
Understanding the principles of yield improvement and defect reduction can significantly impact the efficiency and profitability of manufacturing processes.
Although related, these two concepts have individual approaches and benefits.
In this article, we’ll explore what yield improvement and defect reduction are, how they differ, and why they are crucial for businesses seeking operational excellence.
目次
What is Yield Improvement?
Yield improvement refers to the strategies and actions taken to increase the productivity and efficiency of a manufacturing process.
In simple terms, it is about getting the most out of a given production cycle.
Yield improvement focuses on maximizing the output of good, usable products.
This is particularly crucial in industries where raw materials or components are costly, such as semiconductor manufacturing, pharmaceuticals, and automotive sectors.
Methods of Yield Improvement
Several methods can enhance yield improvement:
Process Optimization
Optimizing the production process involves fine-tuning different aspects, from raw material handling to the final assembly.
By identifying and eliminating inefficiencies, you can produce more units in the same amount of time or with the same amount of resources.
Material Quality
Using high-quality raw materials is essential for yield improvement.
Poor-quality materials often lead to increased wastage and lower output.
Therefore, ensuring that input materials meet stringent quality standards can directly improve yield rates.
Employee Training
Skilled and knowledgeable employees can significantly impact yield.
Properly trained workers are less likely to make mistakes, thus increasing the number of good products produced.
Investing in continuous training can yield long-term benefits.
What is Defect Reduction?
Defect reduction focuses on minimizing the number of defective products generated during a manufacturing process.
While yield improvement looks at overall productivity, defect reduction zeroes in on the quality aspect.
The primary goal is to identify, analyze, and eliminate sources of defects to ensure that the final products meet specific quality standards.
Approaches to Defect Reduction
Several strategies are commonly employed for defect reduction:
Quality Assurance (QA) and Quality Control (QC)
QA and QC are systematic processes put in place to monitor and ensure product quality.
QA focuses on the processes that contribute to the final product, whereas QC involves the actual inspection of the end product.
Both are integral to reducing defects.
Root Cause Analysis
Finding the root cause of defects is crucial for long-term solutions.
Techniques like the 5 Whys, Fishbone diagram, and Failure Mode and Effects Analysis (FMEA) can help identify and eliminate the underlying issues causing defects.
Statistical Process Control (SPC)
SPC uses statistical methods to monitor and control production processes.
By analyzing data gathered during production, businesses can identify unusual performances that may indicate defects are occurring.
This allows for early intervention and minimizes defective outputs.
Key Differences Between Yield Improvement and Defect Reduction
Though both yield improvement and defect reduction aim to enhance production efficiency, they differ significantly in their focus and approach.
Focus Area
Yield improvement is primarily concerned with increasing the overall output of good products by optimizing the entire production process.
Defect reduction, on the other hand, focuses solely on minimizing the number of faulty or defective products.
Measurement Metrics
Yield improvement is usually measured in terms of the percentage of good products versus the total products produced.
Defect reduction is often quantified by the defect rate, which indicates the number of defective items per batch or production cycle.
Impact on Costs
Yield improvement can lead to cost savings through better utilization of resources and increased productivity.
Defect reduction directly affects costs associated with rework, scrap, and customer dissatisfaction due to returns or recalls.
Why Both are Important
Understanding the importance of both yield improvement and defect reduction can drive the adoption of best practices in a manufacturing setup.
Enhanced Product Quality
Balancing both strategies ensures that you not only produce a high quantity of products but also maintain high quality.
Improved product quality can lead to increased customer satisfaction and loyalty.
Operational Efficiency
Combining yield improvement with defect reduction contributes to the overall operational efficiency of a manufacturing process.
Optimizing both quantity and quality helps in achieving a more robust and reliable production system.
Profit Margins
By focusing on both yield improvement and defect reduction, businesses can achieve better profit margins.
Efficient use of resources, less wastage, and fewer returns or recalls contribute to reduced operational costs and increased profitability.
Implementing Both Strategies
Successfully implementing both yield improvement and defect reduction strategies requires a structured approach.
Integrated Quality Management Systems (QMS)
A well-organized QMS can be instrumental in simultaneously addressing yield improvement and defect reduction.
A QMS integrates various quality policies, processes, and resources required to meet customer expectations.
Continuous Monitoring and Feedback
Regularly monitoring production processes and collecting feedback is vital for both yield improvement and defect reduction.
This ongoing assessment enables businesses to make data-driven decisions and implement timely interventions.
Cross-functional Teams
Collaboration between different departments, such as production, quality control, and supply chain, can lead to more effective yield improvement and defect reduction.
Cross-functional teams bring diverse perspectives and expertise to tackle complex problems.
In conclusion, yield improvement and defect reduction are two pivotal aspects of modern manufacturing that, when integrated, can significantly enhance industrial efficiency and profitability.
While yield improvement focuses on maximizing output, defect reduction zeroes in on ensuring the highest quality.
Both strategies contribute to streamlined operations, improved product quality, and better profit margins.
Implementing a balanced approach encompassing both areas can lead to sustained success in a competitive marketplace.
資料ダウンロード
QCD調達購買管理クラウド「newji」は、調達購買部門で必要なQCD管理全てを備えた、現場特化型兼クラウド型の今世紀最高の購買管理システムとなります。
ユーザー登録
調達購買業務の効率化だけでなく、システムを導入することで、コスト削減や製品・資材のステータス可視化のほか、属人化していた購買情報の共有化による内部不正防止や統制にも役立ちます。
NEWJI DX
製造業に特化したデジタルトランスフォーメーション(DX)の実現を目指す請負開発型のコンサルティングサービスです。AI、iPaaS、および先端の技術を駆使して、製造プロセスの効率化、業務効率化、チームワーク強化、コスト削減、品質向上を実現します。このサービスは、製造業の課題を深く理解し、それに対する最適なデジタルソリューションを提供することで、企業が持続的な成長とイノベーションを達成できるようサポートします。
オンライン講座
製造業、主に購買・調達部門にお勤めの方々に向けた情報を配信しております。
新任の方やベテランの方、管理職を対象とした幅広いコンテンツをご用意しております。
お問い合わせ
コストダウンが利益に直結する術だと理解していても、なかなか前に進めることができない状況。そんな時は、newjiのコストダウン自動化機能で大きく利益貢献しよう!
(Β版非公開)