- お役立ち記事
- The difference between Production Efficiency and Operating Efficiency
The difference between Production Efficiency and Operating Efficiency
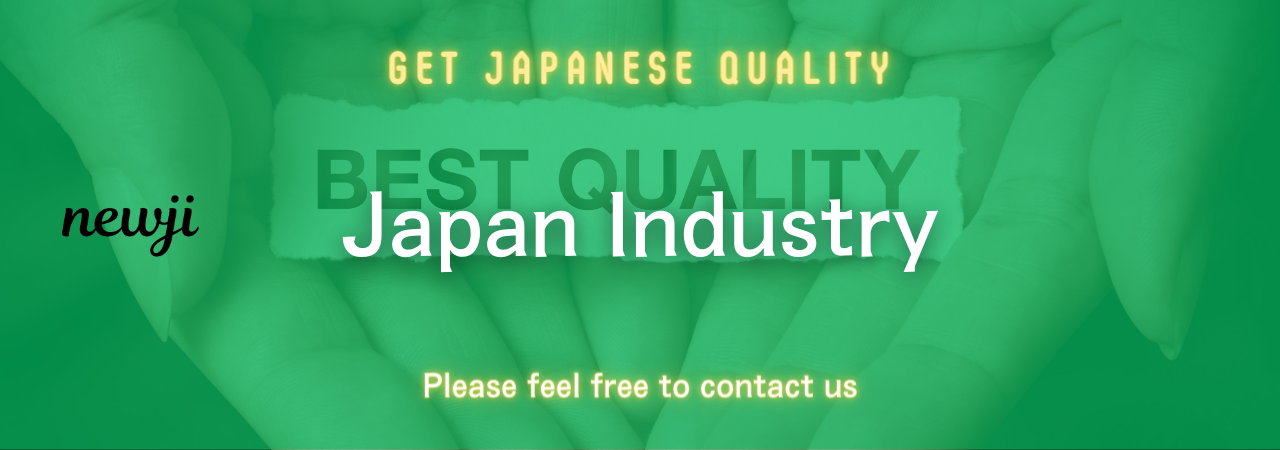
In today’s competitive business environment, understanding various metrics that measure efficiency is crucial for success.
Two important metrics often discussed are production efficiency and operating efficiency.
Although these terms may sound similar, they pertain to different aspects of a business’s performance.
Let’s dive into what each term means and explore the key differences between production efficiency and operating efficiency.
目次
What is Production Efficiency?
Production efficiency measures how well a company turns inputs into outputs during the manufacturing process.
It focuses on minimizing waste and optimizing resources to ensure that the maximum possible quantity of goods is produced using the least amount of resources.
The goal is to make the production process as effective as possible.
Key Components of Production Efficiency
To better understand production efficiency, it’s important to look at some of its key components.
These include:
* **Input Utilization**: This measures how effectively a company uses its raw materials, labor, and equipment to create products.
* **Process Optimization**: This involves evaluating and adjusting the steps in the production process to make them more efficient.
* **Quality Control**: Ensuring that the final products meet certain quality standards is critical for high production efficiency.
How to Measure Production Efficiency
Production efficiency is often measured using the formula:
Production Efficiency = (Actual Output / Maximum Possible Output) x 100.
For example, if a company’s production line can produce 1,000 units per day, but it only produces 900 units, the production efficiency is 90%.
What is Operating Efficiency?
Operating efficiency, on the other hand, takes a broader view of how a business runs as a whole.
It measures the ability of a company to generate income from its operational activities while minimizing costs.
Unlike production efficiency, operating efficiency includes not just the manufacturing process, but also other areas such as marketing, sales, and administration.
Key Components of Operating Efficiency
To get a complete picture of operating efficiency, consider the following components:
* **Revenue Generation**: This looks at how well a company is able to generate sales and revenue from its operations.
* **Cost Management**: It involves minimizing expenses related to all operational activities, not just production.
* **Asset Utilization**: This measures how effectively a company uses its assets, like equipment and facilities, to produce revenue.
How to Measure Operating Efficiency
Operating efficiency can be quantified using several financial ratios.
One commonly used measure is the Operating Efficiency Ratio, calculated as:
Operating Efficiency Ratio = (Operating Expenses / Revenue) x 100.
For example, if a company’s revenue is $1 million and its operating expenses are $700,000, the Operating Efficiency Ratio is 70%.
Main Differences Between Production Efficiency and Operating Efficiency
After exploring the definitions and components of each type of efficiency, it’s clear that there are several key differences between production efficiency and operating efficiency.
Scope of Measurement
Production efficiency focuses narrowly on the manufacturing process.
It aims to maximize output while minimizing waste and resource use in production activities.
Operating efficiency, however, takes a broader view by evaluating the entire operational performance of a business.
It looks at how well a company converts its overall operational inputs into profitable outputs.
Metrics Used
Production efficiency is often measured in terms of output versus input specifically within the production line.
Common metrics include cycle time, production rates, and defect rates.
Operating efficiency, on the other hand, uses financial ratios like the Operating Efficiency Ratio to measure overall business performance.
These ratios consider not just production costs, but other operational expenses and revenue as well.
Areas of Improvement
Improving production efficiency generally involves optimizing specific production activities.
This could mean improving the quality of raw materials, upgrading machinery, or streamlining the steps in the production process.
Improving operating efficiency involves a more holistic approach.
This could include cost reduction across various departments, better asset utilization, and strategies to increase revenue from sales and services.
Why Both Metrics Matter
Understanding both production efficiency and operating efficiency is vital for a well-rounded view of a business’s performance.
A company might have high production efficiency but poor operating efficiency if it excels in manufacturing but struggles in areas like sales and marketing.
Conversely, strong operating efficiency can sometimes compensate for low production efficiency by generating revenue through other means.
Achieving Balance
The key to sustainable success is to strike a balance between these two types of efficiency.
By focusing on optimizing production processes and maintaining a keen eye on overall operational performance, companies can ensure they’re making the best use of their resources.
Continuous Improvement
Both production efficiency and operating efficiency should be seen as ongoing objectives.
Regularly analyzing and optimizing these metrics can lead to sustained improvements over time, helping a company to remain competitive and profitable in a dynamic market.
Conclusion
While production efficiency and operating efficiency may seem similar, they focus on different aspects of a business’s performance.
Understanding both helps companies optimize their processes and improve their overall operational effectiveness.
By measuring and striving to improve these metrics, businesses can make the most of their resources, boost profitability, and ensure long-term success.
Whether you’re a business owner, manager, or employee, knowing the difference between production efficiency and operating efficiency will enable you to contribute more effectively to your company’s growth and prosperity.
資料ダウンロード
QCD調達購買管理クラウド「newji」は、調達購買部門で必要なQCD管理全てを備えた、現場特化型兼クラウド型の今世紀最高の購買管理システムとなります。
ユーザー登録
調達購買業務の効率化だけでなく、システムを導入することで、コスト削減や製品・資材のステータス可視化のほか、属人化していた購買情報の共有化による内部不正防止や統制にも役立ちます。
NEWJI DX
製造業に特化したデジタルトランスフォーメーション(DX)の実現を目指す請負開発型のコンサルティングサービスです。AI、iPaaS、および先端の技術を駆使して、製造プロセスの効率化、業務効率化、チームワーク強化、コスト削減、品質向上を実現します。このサービスは、製造業の課題を深く理解し、それに対する最適なデジタルソリューションを提供することで、企業が持続的な成長とイノベーションを達成できるようサポートします。
オンライン講座
製造業、主に購買・調達部門にお勤めの方々に向けた情報を配信しております。
新任の方やベテランの方、管理職を対象とした幅広いコンテンツをご用意しております。
お問い合わせ
コストダウンが利益に直結する術だと理解していても、なかなか前に進めることができない状況。そんな時は、newjiのコストダウン自動化機能で大きく利益貢献しよう!
(Β版非公開)