- お役立ち記事
- Manufacturing Process of Circuit Breakers and Safety Reinforcement
Manufacturing Process of Circuit Breakers and Safety Reinforcement
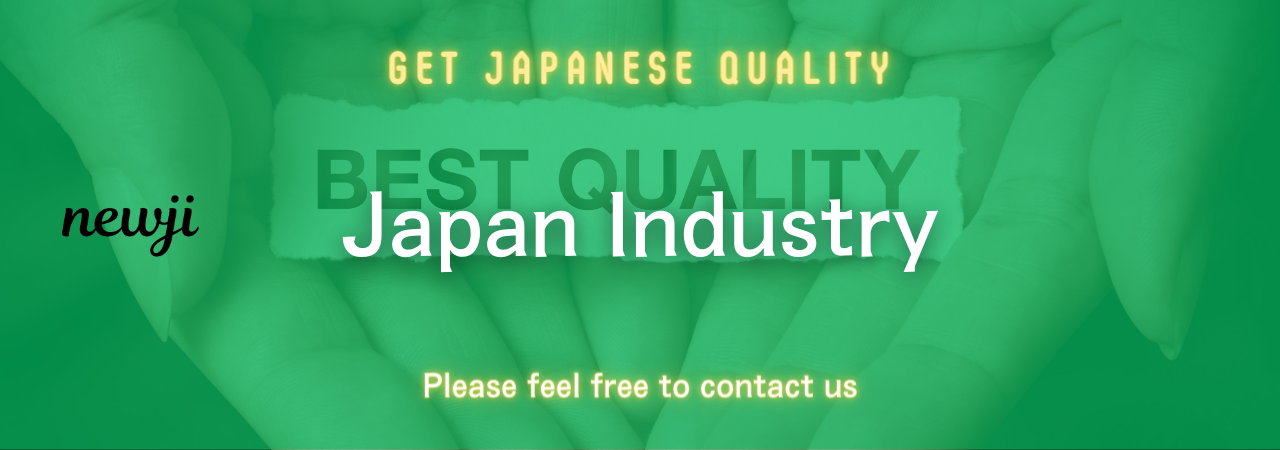
Circuit breakers are essential components in electrical systems, protecting circuits from damage caused by overloads or short circuits.
Understanding the manufacturing process of these devices and how safety is reinforced is crucial for ensuring their reliability and effectiveness.
目次
Materials and Initial Design
The manufacturing process begins with sourcing high-quality raw materials.
The primary materials used in circuit breakers include plastics, metals, and specific alloys.
Copper, for instance, is commonly used for its excellent conductivity, while steel provides structural integrity.
Once the materials are gathered, the initial design phase begins.
Engineers use sophisticated software to create detailed blueprints.
These blueprints outline every aspect of the circuit breaker’s construction, from the housing to the internal components.
Computer-aided design (CAD) systems play a crucial role in this phase, allowing for precise adjustments and optimizations.
Component Manufacturing
Following the design, the manufacturing of individual components commences.
Each component plays a critical role in the functionality of the circuit breaker.
Contact Points
Contact points are responsible for making or breaking the electrical connection.
These parts are typically manufactured using high-grade conductive materials to ensure minimal resistance and maximum durability.
The manufacturing process involves stamping, forming, and plating the contact points to enhance conductivity and resistance to wear.
Housing
The housing, usually made from thermo-set plastics or other insulating materials, serves as the protective shell for the internal components.
Injection molding is a common manufacturing technique used to create robust and precise housing units.
This process ensures that each housing unit meets stringent safety and durability standards.
Trip Mechanism
The trip mechanism is vital for detecting faults and disconnecting the circuit.
This component is often made from a combination of metals and plastics.
Precision machining and assembly are crucial in ensuring the reliability and responsiveness of the trip mechanism.
Assembly
After component manufacturing, the assembly process begins.
This stage requires meticulous attention to detail to ensure all parts fit and function correctly.
Sub-Assembly
In the sub-assembly phase, smaller components are assembled into larger, functional units.
For instance, the contact points, trip mechanisms, and terminals are put together as sub-assemblies.
This step allows for easier final assembly and quality control checks.
Final Assembly
The final assembly involves integrating all the sub-assemblies into the main housing.
Automated systems and skilled technicians work together to ensure precise alignment and secure fastening.
During this stage, wiring is carefully routed and connected, and moving parts are tested for smooth operation.
Quality Control and Testing
Quality control is a crucial part of the manufacturing process, ensuring that each circuit breaker meets rigorous safety and performance standards.
Visual Inspection
The first step in quality control involves a thorough visual inspection.
Trained inspectors examine each unit for signs of defects or irregularities in materials and workmanship.
Functional Testing
Next, functional testing is performed to verify that the circuit breaker operates as intended.
This includes testing the trip mechanism, continuity, and resistance.
Advanced testing equipment simulates fault conditions to ensure that the circuit breaker reacts appropriately.
Environmental Testing
Circuit breakers are also subjected to environmental testing to verify their durability under various conditions.
This testing includes exposure to extreme temperatures, humidity, and vibrations.
The aim is to confirm that the circuit breakers can withstand the rigors of real-world applications.
Safety Reinforcement
Ensuring the safety of circuit breakers is paramount throughout the manufacturing process.
Several measures are implemented to reinforce safety.
Material Selection
The choice of materials plays a vital role in safety reinforcement.
Only high-quality, certified materials are used to manufacture circuit breakers.
This minimizes the risk of failures and ensures durability.
Redundant Systems
Incorporating redundant systems within the design adds an extra layer of safety.
For instance, multiple trip mechanisms may be included, ensuring that if one fails, another will still protect the circuit.
Continuous Improvement
Manufacturers are committed to continuous improvement in design and production processes.
Regular reviews of performance data and customer feedback help identify areas for enhancement.
This iterative process leads to safer and more reliable products over time.
Packaging and Distribution
Once testing and quality control are completed, the circuit breakers are packaged for distribution.
Protective packaging materials are used to prevent damage during transit.
Clear labeling and documentation ensure that customers receive products that meet their specific requirements.
Installation and Maintenance
Proper installation and maintenance are essential for the long-term safety and functionality of circuit breakers.
Professional Installation
Circuit breakers should be installed by qualified electricians who follow industry standards and guidelines.
Correct installation is crucial for ensuring that the breakers operate effectively and safely.
Regular Maintenance
Routine maintenance checks are necessary to ensure that circuit breakers remain in good working condition.
This includes inspecting for signs of wear, conducting functional tests, and replacing components as needed.
Understanding the manufacturing process of circuit breakers and the measures taken to reinforce safety highlights the importance of precision and quality in the production of these critical electrical components.
By adhering to strict standards and continually striving for improvement, manufacturers ensure that circuit breakers provide reliable protection, safeguarding electrical systems and ultimately saving lives.
資料ダウンロード
QCD調達購買管理クラウド「newji」は、調達購買部門で必要なQCD管理全てを備えた、現場特化型兼クラウド型の今世紀最高の購買管理システムとなります。
ユーザー登録
調達購買業務の効率化だけでなく、システムを導入することで、コスト削減や製品・資材のステータス可視化のほか、属人化していた購買情報の共有化による内部不正防止や統制にも役立ちます。
NEWJI DX
製造業に特化したデジタルトランスフォーメーション(DX)の実現を目指す請負開発型のコンサルティングサービスです。AI、iPaaS、および先端の技術を駆使して、製造プロセスの効率化、業務効率化、チームワーク強化、コスト削減、品質向上を実現します。このサービスは、製造業の課題を深く理解し、それに対する最適なデジタルソリューションを提供することで、企業が持続的な成長とイノベーションを達成できるようサポートします。
オンライン講座
製造業、主に購買・調達部門にお勤めの方々に向けた情報を配信しております。
新任の方やベテランの方、管理職を対象とした幅広いコンテンツをご用意しております。
お問い合わせ
コストダウンが利益に直結する術だと理解していても、なかなか前に進めることができない状況。そんな時は、newjiのコストダウン自動化機能で大きく利益貢献しよう!
(Β版非公開)