- お役立ち記事
- Manufacturing Process of Intake Manifolds and Airflow Improvement
Manufacturing Process of Intake Manifolds and Airflow Improvement
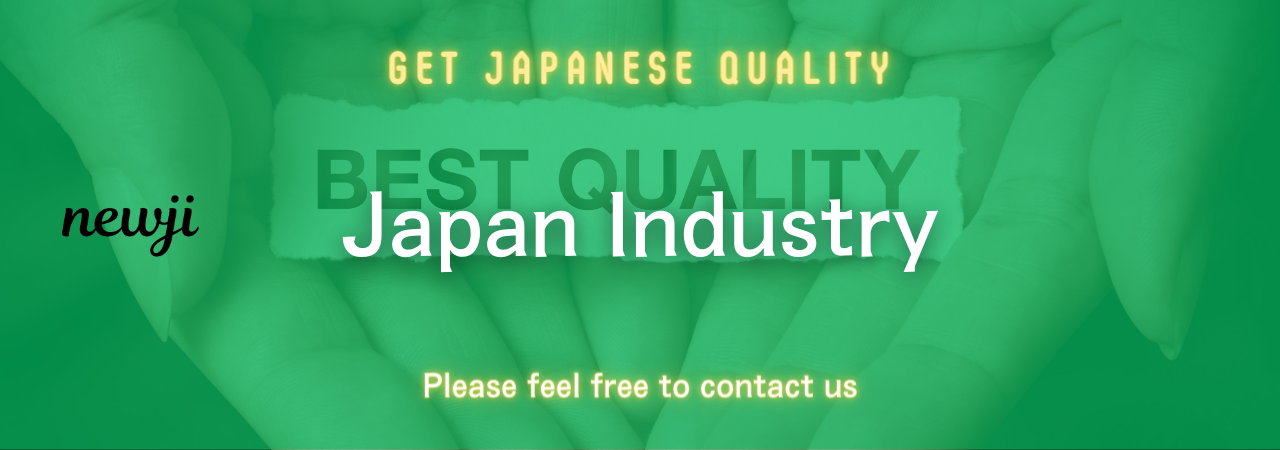
目次
Introduction to Intake Manifolds
An intake manifold is a key part of a vehicle’s engine.
It ensures that air travels smoothly into the engine cylinders for combustion.
The intake manifold plays a crucial role in determining an engine’s performance and efficiency.
Material Selection for Intake Manifolds
The choice of material is essential for manufacturing intake manifolds.
Traditionally, these components were made from cast iron.
However, modern engineering has introduced lightweight materials like aluminum and high-strength plastics.
These materials help improve fuel efficiency by reducing the overall weight of the engine.
Benefits of Aluminum
Aluminum is a popular choice due to its light weight and its ability to withstand high temperatures.
It improves the car’s fuel efficiency and performance.
Aluminum intake manifolds are also less prone to corrosion, ensuring durability and longevity.
Advantages of High-Strength Plastics
High-strength plastics, such as nylon composites, are another excellent option.
They are even lighter than aluminum.
Moreover, they provide better acoustic properties, helping to reduce engine noise.
High-strength plastics are also resistant to the range of chemicals found in a car engine.
Design and Engineering of Intake Manifolds
The design of the intake manifold is critical.
It must ensure that the air is evenly distributed to each cylinder.
Inconsistent air distribution can lead to poor engine performance and increased emissions.
Computer-Aided Design (CAD)
Engineers use Computer-Aided Design (CAD) software to create intake manifold designs.
With CAD, they can model the air intake system and simulate airflow dynamics.
This helps them identify and eliminate inefficiencies before the manufacturing process begins.
Prototype Development
Before full-scale production, a prototype is usually developed.
This prototype undergoes rigorous testing to ensure it performs as expected.
Any flaws or improvements needed are identified during this phase.
This step is crucial for optimizing the design before mass production.
Manufacturing Process
The actual production of intake manifolds involves several steps.
Each step is crucial to ensure the final product meets quality and performance standards.
Molding
For plastic or composite intake manifolds, the first step in the manufacturing process is molding.
A mold is created based on the CAD design.
Molten plastic is injected into this mold to take the shape of the intake manifold.
For metal intake manifolds, casting is the equivalent process.
Machining
Once the raw shape is obtained, it undergoes machining.
Machining helps achieve the precise dimensions and smooth surfaces required for optimal performance.
Computer Numerical Control (CNC) machines are often used for this purpose.
These machines ensure accuracy and consistency in every unit produced.
Assembly and Quality Checks
After machining, the intake manifolds are assembled with any additional components, such as sensors.
Each unit undergoes stringent quality checks to ensure it meets the required standards.
Any defects identified are corrected to ensure only high-quality manifolds make it to the market.
Airflow Improvement Techniques
To enhance the performance of intake manifolds, various techniques are employed to improve airflow.
Efficient airflow ensures better combustion and higher engine performance.
Smoothing the Passageway
One of the simplest techniques is smoothing the passageway of the intake manifold.
A smooth surface reduces air resistance and turbulence, ensuring a steady flow of air into the engine.
Polishing and porting are common methods used to achieve this smooth surface.
Variable Length Intake Manifolds
Variable Length Intake Manifolds (VLIM) are engineered to improve airflow based on engine speed.
They alter the air path lengths to optimize air intake during different engine loads.
At low speeds, a longer path improves torque, while a shorter path enhances performance at higher speeds.
This technology ensures the engine operates efficiently under various conditions.
Turbocharging
Turbocharging is another effective technique to improve airflow.
A turbocharger forces more air into the engine, enhancing combustion.
This results in higher power output and improved efficiency.
While turbocharging is often applied to the engine as a whole, it works in conjunction with the intake manifold to deliver better performance.
Conclusion
The manufacturing process of intake manifolds involves careful selection of materials, precise engineering, and rigorous quality checks.
Airflow improvement techniques play a significant role in enhancing engine performance and efficiency.
By understanding these processes, we can appreciate the importance of intake manifolds in the overall functioning of a vehicle.
資料ダウンロード
QCD調達購買管理クラウド「newji」は、調達購買部門で必要なQCD管理全てを備えた、現場特化型兼クラウド型の今世紀最高の購買管理システムとなります。
ユーザー登録
調達購買業務の効率化だけでなく、システムを導入することで、コスト削減や製品・資材のステータス可視化のほか、属人化していた購買情報の共有化による内部不正防止や統制にも役立ちます。
NEWJI DX
製造業に特化したデジタルトランスフォーメーション(DX)の実現を目指す請負開発型のコンサルティングサービスです。AI、iPaaS、および先端の技術を駆使して、製造プロセスの効率化、業務効率化、チームワーク強化、コスト削減、品質向上を実現します。このサービスは、製造業の課題を深く理解し、それに対する最適なデジタルソリューションを提供することで、企業が持続的な成長とイノベーションを達成できるようサポートします。
オンライン講座
製造業、主に購買・調達部門にお勤めの方々に向けた情報を配信しております。
新任の方やベテランの方、管理職を対象とした幅広いコンテンツをご用意しております。
お問い合わせ
コストダウンが利益に直結する術だと理解していても、なかなか前に進めることができない状況。そんな時は、newjiのコストダウン自動化機能で大きく利益貢献しよう!
(Β版非公開)