- お役立ち記事
- The difference between Poka-yoke and Autonomation
The difference between Poka-yoke and Autonomation
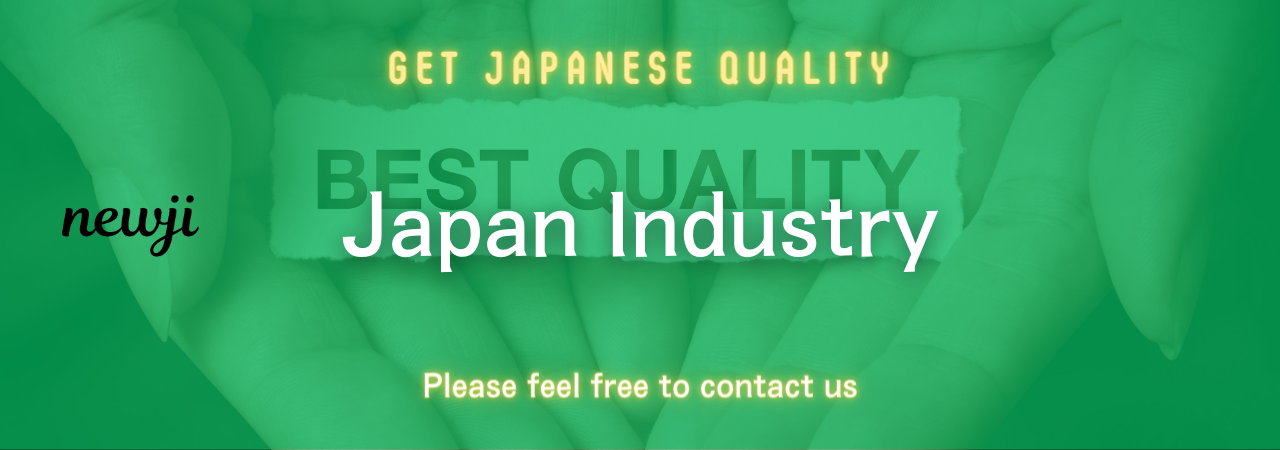
Poka-yoke and autonomation are two powerful concepts in manufacturing that significantly enhance quality and efficiency.
Though they share similar goals, they are distinct in their approaches and applications.
Understanding these differences is crucial for anyone looking to optimize their manufacturing processes.
In this article, we will delve into the essence of poka-yoke and autonomation, comparing their principles, benefits, and implementation strategies.
目次
What is Poka-yoke?
Poka-yoke is a Japanese term that means “mistake-proofing.”
It was coined by Shigeo Shingo while working at Toyota to improve the production process.
The primary goal of poka-yoke is to prevent errors in the manufacturing process by designing mechanisms that make it difficult or impossible to make mistakes.
Principles of Poka-yoke
The core idea behind poka-yoke is to create a fail-safe mechanism that identifies and corrects errors before they result in defects.
There are several principles guiding the implementation of poka-yoke:
1. **Prevention**: A mechanism is set up to prevent mistakes from occurring in the first place.
2. **Detection**: If a mistake does occur, it is detected immediately before it affects the final product.
3. **Response**: Once a mistake is detected, the process is either stopped or the error is corrected automatically.
Examples of Poka-yoke
There are numerous instances where poka-yoke is utilized to enhance manufacturing processes:
1. **Color-coding**: Different parts are color-coded to avoid assembly errors.
2. **Limit switches**: Ensure that components are in the correct position before the machine operates.
3. **Go/No-go gauges**: Ensure the correct dimensions of parts before they proceed in the production process.
What is Autonomation?
Autonomation, also known as “jidoka,” is another crucial concept in manufacturing, particularly in lean production.
Autonomation refers to automation with a human touch. It means equipping machines with the ability to detect when they are operating incorrectly and to stop themselves automatically.
Principles of Autonomation
Autonomation is based on the following principles:
1. **Human-Machine Coordination**: Machines are designed to work in conjunction with human operators.
2. **Self-Monitoring**: Machines can detect irregularities or mistakes during production.
3. **Automatic Stop**: Upon detecting an error, machines stop operation to prevent further issues.
4. **Problem Solving**: Once stopped, the machine alerts the operator to the issue, allowing for an immediate resolution.
Examples of Autonomation
Some common practices of autonomation include:
1. **Sensors**: Machines equipped with sensors to alert operators about defects or malfunctions.
2. **Andon Systems**: Visual or audible alert systems that indicate machine status and issues.
3. **Inspection Machines**: Automated machines inspect products during different production stages and halt if defects are found.
Comparing Poka-yoke and Autonomation
While both poka-yoke and autonomation aim to improve quality and efficiency, they do so in different ways.
Here, we compare these two methodologies across various factors.
Objective
Poka-yoke focuses on error prevention and ensuring that mistakes do not occur, while autonomation emphasizes detecting abnormalities in the process and stopping operations to prevent defects.
Implementation
Implementing poka-yoke often involves simple, cost-effective solutions like using color-coding or mechanical fixtures.
Autonomation, on the other hand, requires more sophisticated technology such as sensors and automated feedback systems.
Response to Errors
Poka-yoke typically provides immediate feedback to either prevent errors or correct them before they become defects.
Autonomation detects errors and prompts the machine to stop, thereby minimizing the risk of defects and allowing human intervention.
Benefits of Poka-yoke
Poka-yoke offers a range of benefits for manufacturing processes:
1. **Reduced Defects**: By preventing errors, the likelihood of defects is significantly minimized.
2. **Increased Efficiency**: Production runs more smoothly without interruptions caused by defects.
3. **Lower Costs**: Reducing defects lowers the cost of rework, scrap, and returns.
4. **Higher Quality**: Consistent error prevention leads to higher quality products.
Benefits of Autonomation
Autonomation also brings several advantages to the manufacturing floor:
1. **Early Error Detection**: Mistakes are detected early, minimizing the impact on the final product.
2. **Improved Safety**: Stopping machinery upon detecting faults enhances workplace safety.
3. **Enhanced Problem Solving**: By involving human operators in the problem-solving process, long-term solutions are more likely to be found.
4. **Consistent Production**: Minimizing defects and downtime ensures a consistent production process.
Implementing Poka-yoke and Autonomation
Successful implementation of poka-yoke and autonomation requires careful planning and execution.
Here are some steps to consider:
Assess the Current Process
Begin by analyzing the current production process to identify where errors and defects most commonly occur.
Understand the root causes of these issues.
Design Poka-yoke Solutions
Develop simple, cost-effective mechanisms to prevent errors.
Test these solutions to ensure they effectively prevent mistakes from occurring.
Integrate Autonomation
Incorporate machines with self-monitoring capabilities.
Ensure these machines can halt operations and alert human operators when errors are detected.
Train Operators
Provide training for operators on the new poka-yoke systems and autonomation technologies.
They should understand how to respond to alerts and correct issues promptly.
Monitor and Improve
Regularly monitor the effectiveness of your poka-yoke and autonomation implementations.
Continually refine and improve the processes based on feedback and performance data.
Poka-yoke and autonomation are both valuable strategies in the pursuit of manufacturing excellence.
By understanding their differences and correctly implementing each where appropriate, manufacturers can significantly enhance quality, efficiency, and safety.
These tools, when used together, create a robust system for minimizing errors and ensuring high-quality production, leading to overall operational success.
資料ダウンロード
QCD調達購買管理クラウド「newji」は、調達購買部門で必要なQCD管理全てを備えた、現場特化型兼クラウド型の今世紀最高の購買管理システムとなります。
ユーザー登録
調達購買業務の効率化だけでなく、システムを導入することで、コスト削減や製品・資材のステータス可視化のほか、属人化していた購買情報の共有化による内部不正防止や統制にも役立ちます。
NEWJI DX
製造業に特化したデジタルトランスフォーメーション(DX)の実現を目指す請負開発型のコンサルティングサービスです。AI、iPaaS、および先端の技術を駆使して、製造プロセスの効率化、業務効率化、チームワーク強化、コスト削減、品質向上を実現します。このサービスは、製造業の課題を深く理解し、それに対する最適なデジタルソリューションを提供することで、企業が持続的な成長とイノベーションを達成できるようサポートします。
オンライン講座
製造業、主に購買・調達部門にお勤めの方々に向けた情報を配信しております。
新任の方やベテランの方、管理職を対象とした幅広いコンテンツをご用意しております。
お問い合わせ
コストダウンが利益に直結する術だと理解していても、なかなか前に進めることができない状況。そんな時は、newjiのコストダウン自動化機能で大きく利益貢献しよう!
(Β版非公開)