- お役立ち記事
- Manufacturing Process of Electric Pens and Improving Pressure Sensitivity
Manufacturing Process of Electric Pens and Improving Pressure Sensitivity
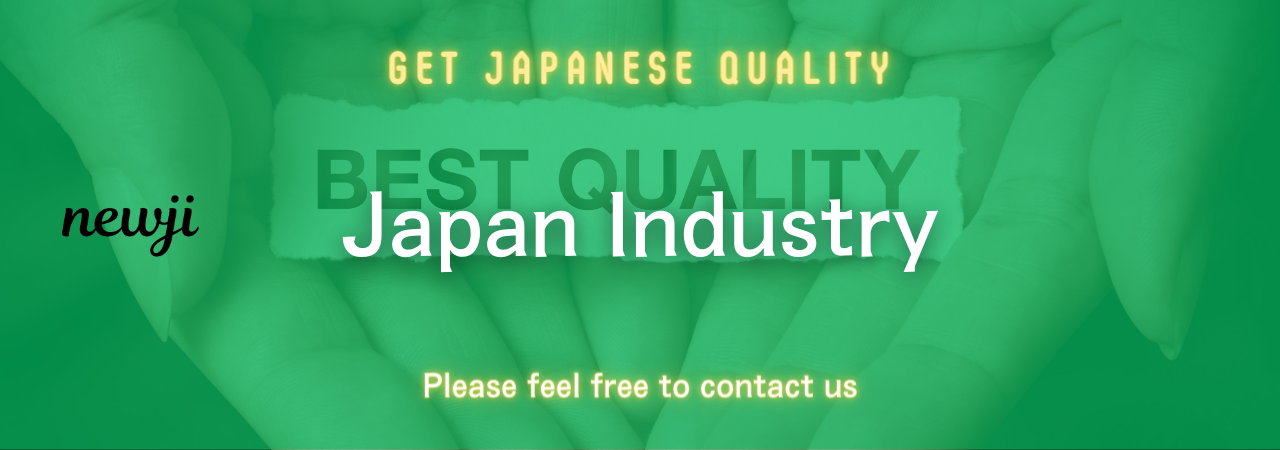
Electric pens, also known as digital pens or styluses, have become essential tools in today’s tech-driven world.
From graphic designers sketching their latest masterpiece to students taking digital notes, these devices have a wide range of applications.
Understanding how electric pens are manufactured and how their pressure sensitivity can be improved is fascinating.
目次
Electric Pen Manufacturing Process
Creating an electric pen involves several detailed steps.
Each stage ensures the device functions correctly and meets industry standards.
Design and Prototyping
The first step in manufacturing an electric pen is designing it.
Engineers and designers collaborate to create blueprints and specifications that outline the pen’s shape, size, and functionality.
Computer-aided design (CAD) software is often used to create detailed 3D models.
Once the design is finalized, prototypes are created.
Prototyping helps identify any potential design flaws or areas for improvement.
This stage often involves creating multiple iterations before arriving at the perfect design.
Component Selection
An electric pen is composed of several crucial components, including the tip, sensors, circuitry, and outer casing.
Selecting the right components is key to ensuring the pen’s optimal performance.
– **Tip:** The tip is typically made from durable and conductive materials.
Different types of tips can be used to accommodate varying levels of pressure sensitivity and precision.
– **Sensors:** Sensors detect the position and pressure applied by the pen.
Various types of sensors, such as capacitive or electromagnetic, may be used based on the pen’s intended application.
– **Circuitry:** The internal circuitry processes signals from the sensors and communicates them to the connected device.
Advanced circuitry can improve the pen’s accuracy and responsiveness.
– **Casing:** The outer casing protects the internal components and provides a comfortable grip for the user.
Materials like plastic or aluminum are commonly used.
Assembly and Testing
Once all the components are selected, the assembly process begins.
This involves integrating the sensors and circuitry into the casing and attaching the tip.
Precision is crucial during this stage to ensure all components are aligned and functioning correctly.
After assembly, each pen undergoes rigorous testing.
This includes checking for functionality, accuracy, and pressure sensitivity.
Pens that pass the tests move on to the next stage, while those that don’t are either reworked or discarded.
Packaging and Quality Control
The final stage is packaging the pens and conducting a quality control check.
Packaging is designed not only to protect the pen during shipping but also to be aesthetically appealing.
Once packaged, another round of quality control ensures that only pens meeting the highest standards reach the consumers.
Improving Pressure Sensitivity
Pressure sensitivity is a critical feature of electric pens.
It allows users to vary the thickness and intensity of their strokes based on how hard they press the pen against a surface.
Improving this sensitivity can significantly enhance the user experience.
Advanced Sensor Technology
Incorporating advanced sensor technology is one of the most effective ways to improve pressure sensitivity.
High-resolution sensors can detect even the slightest variations in pressure, providing a more nuanced response.
Manufacturers are continually developing new sensor technologies to enhance sensitivity and accuracy.
Optimized Firmware
Firmware is the software that controls the hardware functions of the pen.
Optimized firmware can improve the pen’s responsiveness to pressure changes.
This involves fine-tuning the algorithms that process signals from the sensors.
Regular firmware updates can also introduce new features and enhancements.
Material Improvements
Using higher quality materials for the pen’s tip and sensors can also enhance pressure sensitivity.
Materials that offer better conductivity and durability provide more accurate and consistent responses over time.
Innovations in materials science continue to offer new possibilities for improving pen performance.
User Calibration
Many modern electric pens offer user calibration options.
Calibration allows users to adjust the pen’s sensitivity settings to match their personal preferences.
This can result in a more customized and satisfactory user experience.
Feedback Mechanisms
Incorporating feedback mechanisms, such as haptic feedback, can offer users real-time responses to their actions.
Haptic feedback can make the pen feel more like a traditional pen or pencil, providing a more intuitive and pleasant experience.
This technology can also help users understand how much pressure they are applying.
Conclusion
The manufacturing process of electric pens is a complex yet fascinating journey that involves meticulous design, component selection, assembly, and rigorous testing.
Advancements in sensor technology, firmware optimization, material science, user calibration, and feedback mechanisms continually push the boundaries of what these devices can achieve.
As technology continues to evolve, we can expect electric pens to become even more precise and responsive.
Whether you’re a professional artist, student, or casual user, the continual improvements in pressure sensitivity will undoubtedly enhance your digital interactions.
資料ダウンロード
QCD調達購買管理クラウド「newji」は、調達購買部門で必要なQCD管理全てを備えた、現場特化型兼クラウド型の今世紀最高の購買管理システムとなります。
ユーザー登録
調達購買業務の効率化だけでなく、システムを導入することで、コスト削減や製品・資材のステータス可視化のほか、属人化していた購買情報の共有化による内部不正防止や統制にも役立ちます。
NEWJI DX
製造業に特化したデジタルトランスフォーメーション(DX)の実現を目指す請負開発型のコンサルティングサービスです。AI、iPaaS、および先端の技術を駆使して、製造プロセスの効率化、業務効率化、チームワーク強化、コスト削減、品質向上を実現します。このサービスは、製造業の課題を深く理解し、それに対する最適なデジタルソリューションを提供することで、企業が持続的な成長とイノベーションを達成できるようサポートします。
オンライン講座
製造業、主に購買・調達部門にお勤めの方々に向けた情報を配信しております。
新任の方やベテランの方、管理職を対象とした幅広いコンテンツをご用意しております。
お問い合わせ
コストダウンが利益に直結する術だと理解していても、なかなか前に進めることができない状況。そんな時は、newjiのコストダウン自動化機能で大きく利益貢献しよう!
(Β版非公開)