- お役立ち記事
- Manufacturing Process of Electric Screwdrivers and Strengthening Bit Exchange Systems
Manufacturing Process of Electric Screwdrivers and Strengthening Bit Exchange Systems
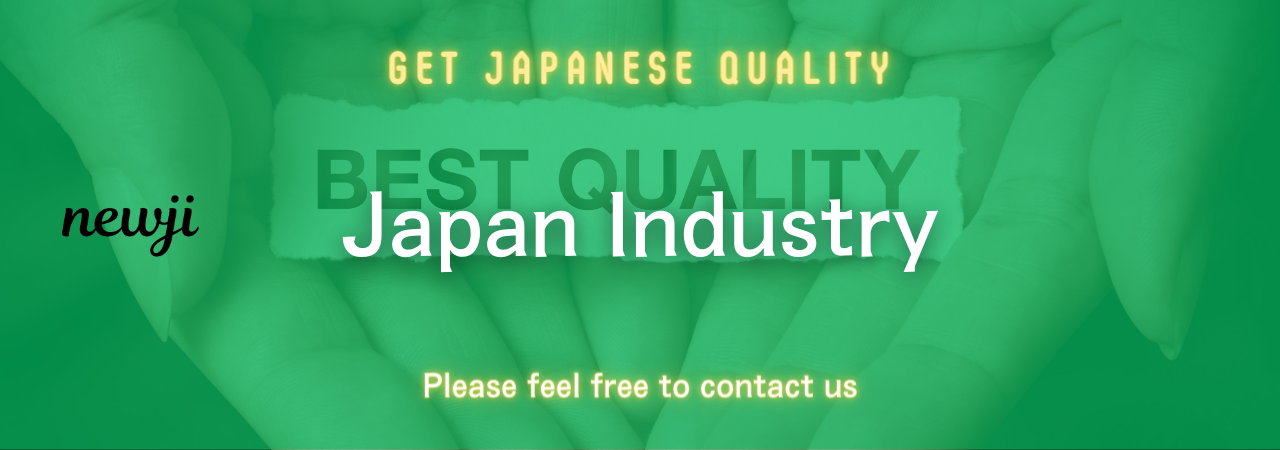
目次
Introduction
Electric screwdrivers, a staple in both DIY projects and professional settings, have revolutionized the way we approach fastening tasks.
Understanding the manufacturing process of these tools and the mechanisms behind bit exchange systems can offer valuable insights, whether you’re a hobbyist or a professional.
We’ll take a deep dive into how these handy tools are made and explore the advancements in bit exchange systems that enhance their functionality and user experience.
The Design Phase
The journey of an electric screwdriver begins in the design phase.
Here, engineers and designers work together to sketch and model the screwdriver, paying close attention to ergonomics, weight distribution, and functionality.
Computer-aided design (CAD) software is often used to create detailed 3D models of each component.
This allows for precise measurements and simulations that can predict how the screwdriver will perform in real-world conditions.
Material Selection
Once the design is finalized, the next step is material selection.
The body of an electric screwdriver is often made from high-impact plastic because it’s lightweight and durable.
Internal components, such as the gear system and the motor, require metals like steel and aluminum for their strength and longevity.
PCBs (Printed Circuit Boards) for the electrical components are usually made from non-conductive materials layered with copper circuits for efficient conductivity.
Component Manufacturing
With the design and materials set, the actual production process begins.
Each component of the electric screwdriver is manufactured separately.
Plastic Molding
The plastic parts, such as the housing, are produced using injection molding.
Plastic granules are heated until they become molten and are then injected into a mold under high pressure.
Once cooled, the plastic hardens into the desired shape.
Metal Fabrication
Metal components like screws, gears, and bearings are produced through a combination of machining, stamping, and casting.
These processes ensure that the metal parts are precise and durable.
Electronic Components
PCBs are fabricated using photolithography, a process that involves layering materials and etching away excess to leave the required circuitry.
Capacitors, resistors, and other small components are soldered onto the PCB.
Assembly Line
The assembly of an electric screwdriver typically takes place on an assembly line.
This is where all the individual components are brought together.
Motor Installation
The motor, a crucial component, is fitted into its designated space within the housing.
The motor’s wiring is then connected to the PCB to ensure electrical functionality.
Gear System Setup
The gear system, which helps convert the motor’s speed into torque, is carefully assembled and installed.
Proper alignment is critical to ensure smooth operation.
Housing and Handle Attachment
Once the internal components are in place, the plastic housing is snapped or screwed together.
The handle, designed for ergonomic gripping, is also attached at this stage.
Quality Control
Before an electric screwdriver reaches consumers, it must pass through several quality control checks.
These inspections ensure that each unit is up to standard and free from manufacturing defects.
Functionality Testing
Each unit is tested to ensure it operates correctly.
This includes running the motor, checking the torque settings, and ensuring the bit holder works as intended.
Durability Testing
Durability tests subject the screwdriver to conditions it might face during its lifetime, such as drops, vibrations, and prolonged use.
Any unit that fails these tests is either fixed or scrapped.
Packaging and Distribution
After quality control, the electric screwdrivers are packaged.
This typically involves placing the tool in a fitted box along with its charger, instruction manual, and a set of bits.
Once packaged, the screwdrivers are shipped to retailers and distributors.
Innovations in Bit Exchange Systems
One of the most significant advancements in electric screwdriver technology is the bit exchange system.
These systems allow users to quickly and easily change the screwdriver bits, enhancing the tool’s versatility.
Quick-Change Systems
Modern electric screwdrivers often feature quick-change systems that allow users to swap bits with a simple pull-and-insert mechanism.
This eliminates the need for additional tools and speeds up the workflow.
Magnetic Bit Holders
Some screwdrivers use magnetic bit holders that use strong magnets to keep the bit securely in place.
This not only makes it easier to change bits but also ensures they don’t fall out during use.
Universal Bit Adapters
Innovations have also led to the creation of universal bit adapters that can accommodate various bit types and sizes.
This means you can use the same screwdriver for a wider range of tasks, making it even more versatile.
Conclusion
Understanding the manufacturing process of electric screwdrivers and the advancements in bit exchange systems offers valuable insights into the engineering and innovation behind these tools.
From the initial design phase to the final quality control, each step is crucial in creating a reliable, efficient, and user-friendly tool.
As technology continues to advance, we can expect even more improvements in the functionality and versatility of electric screwdrivers.
資料ダウンロード
QCD調達購買管理クラウド「newji」は、調達購買部門で必要なQCD管理全てを備えた、現場特化型兼クラウド型の今世紀最高の購買管理システムとなります。
ユーザー登録
調達購買業務の効率化だけでなく、システムを導入することで、コスト削減や製品・資材のステータス可視化のほか、属人化していた購買情報の共有化による内部不正防止や統制にも役立ちます。
NEWJI DX
製造業に特化したデジタルトランスフォーメーション(DX)の実現を目指す請負開発型のコンサルティングサービスです。AI、iPaaS、および先端の技術を駆使して、製造プロセスの効率化、業務効率化、チームワーク強化、コスト削減、品質向上を実現します。このサービスは、製造業の課題を深く理解し、それに対する最適なデジタルソリューションを提供することで、企業が持続的な成長とイノベーションを達成できるようサポートします。
オンライン講座
製造業、主に購買・調達部門にお勤めの方々に向けた情報を配信しております。
新任の方やベテランの方、管理職を対象とした幅広いコンテンツをご用意しております。
お問い合わせ
コストダウンが利益に直結する術だと理解していても、なかなか前に進めることができない状況。そんな時は、newjiのコストダウン自動化機能で大きく利益貢献しよう!
(Β版非公開)