- お役立ち記事
- The difference between Yield Rate and Defect Rate
The difference between Yield Rate and Defect Rate
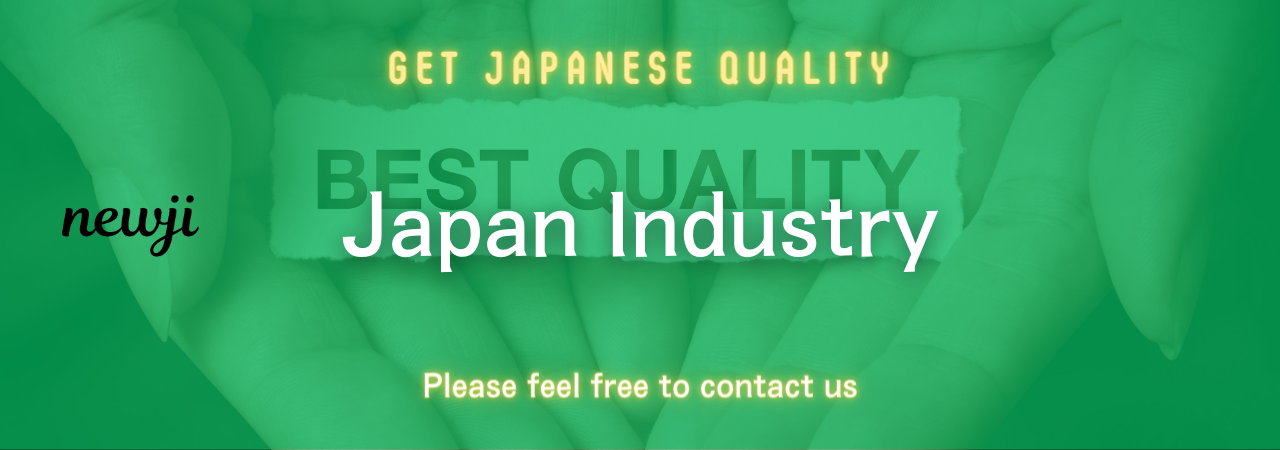
Understanding the intricacies of production processes can often be confusing, especially when it comes to evaluating efficiency and quality.
Two key metrics that manufacturers frequently refer to are the Yield Rate and the Defect Rate.
Although they are related, they serve different purposes and offer distinct insights into the production line.
目次
What is Yield Rate?
The Yield Rate is a metric that measures the efficiency of a production process.
It represents the percentage of finished products that meet the quality standards out of the total number of products produced.
In simpler terms, it tells you how many items are made correctly the first time without needing any rework.
For instance, if a factory produces 1,000 units in a day and 950 of those units meet the quality standards, the Yield Rate would be 95%.
A high Yield Rate generally indicates a well-optimized and efficient production process.
It means that most of the materials, labor, and time invested result in products that are ready for sale or use.
Importance of Yield Rate
Understanding the Yield Rate is crucial for several reasons.
Firstly, a high Yield Rate contributes to lower production costs.
Fewer defective products mean less wastage of materials and time.
Secondly, it improves customer satisfaction.
Products that meet quality standards are less likely to be returned or complained about, ensuring a better customer experience.
Lastly, it is a strong indicator of operational efficiency and can highlight areas within the production process that require improvement.
What is Defect Rate?
The Defect Rate, on the other hand, measures the percentage of defective products in a batch of manufactured items.
It is essentially the inverse of the Yield Rate.
If the Yield Rate tells you what percentage of products are good, the Defect Rate tells you what percentage are not up to standard.
For example, if 950 out of 1,000 units meet the quality standards, then 50 units do not, resulting in a Defect Rate of 5%.
Importance of Defect Rate
Just like the Yield Rate, understanding the Defect Rate is essential for manufacturers.
A high Defect Rate can have several adverse effects.
Firstly, it increases production costs.
More defective products mean more materials wasted and more time spent on rework or repairs.
Secondly, it can severely impact customer satisfaction.
Products that do not meet quality standards are liable to be returned, damaging the brand’s reputation.
Lastly, a high Defect Rate can be a red flag that indicates underlying problems within the production process, such as machinery issues or inadequate worker training.
How They Work Together
The Yield Rate and the Defect Rate are two sides of the same coin.
They provide a comprehensive overview of the production line’s efficiency and quality.
While the Yield Rate focuses on the successful production of good units, the Defect Rate helps identify areas for improvement and cost-saving opportunities.
When both metrics are monitored together, manufacturers can gain valuable insights that can lead to more informed decision-making.
Balancing Yield and Defect Rates
Any attempt to improve the Yield Rate usually comes with a corresponding reduction in the Defect Rate, and vice versa.
However, it’s important to understand that eliminating defects entirely might not be cost-effective.
Some level of defects is often acceptable and expected in a real-world production environment.
The goal should be to find a balance where the Yield Rate is maximized while keeping the Defect Rate as low as reasonably possible without incurring excessive costs.
Real-world Applications
Various industries use Yield and Defect Rates to improve their production efficiency and product quality.
In the semiconductor industry, for instance, these metrics are crucial due to the highly specialized and precise nature of the manufacturing process.
In the automotive industry, understanding these rates can help in creating reliable and long-lasting vehicles.
Food and beverage companies also rely on these metrics to ensure that their products are safe and meet the established quality standards.
Practical Steps to Improve Yield and Reduce Defects
Several practical steps can be taken to improve Yield and reduce Defect Rates.
One effective method is to implement rigorous quality control checks at various stages of the production process.
This not only helps in catching defects early but also provides data that can be used to identify and rectify the root cause of issues.
Another approach is to invest in worker training.
Well-trained employees are less likely to make mistakes, thereby improving the overall Yield Rate.
Upgrading machinery and technology can also contribute to more efficient production and lower Defect Rates.
Conclusion
Understanding the difference between Yield Rate and Defect Rate is essential for anyone involved in manufacturing or production.
While both metrics provide valuable insights, they serve different purposes.
The Yield Rate helps assess efficiency, whereas the Defect Rate highlights potential issues in the production process.
By monitoring and balancing these rates, manufacturers can optimize their operations, reduce costs, and improve customer satisfaction.
Whether you’re in the automotive, semiconductor, or food and beverage industry, grasping these concepts can significantly impact your bottom line.
資料ダウンロード
QCD調達購買管理クラウド「newji」は、調達購買部門で必要なQCD管理全てを備えた、現場特化型兼クラウド型の今世紀最高の購買管理システムとなります。
ユーザー登録
調達購買業務の効率化だけでなく、システムを導入することで、コスト削減や製品・資材のステータス可視化のほか、属人化していた購買情報の共有化による内部不正防止や統制にも役立ちます。
NEWJI DX
製造業に特化したデジタルトランスフォーメーション(DX)の実現を目指す請負開発型のコンサルティングサービスです。AI、iPaaS、および先端の技術を駆使して、製造プロセスの効率化、業務効率化、チームワーク強化、コスト削減、品質向上を実現します。このサービスは、製造業の課題を深く理解し、それに対する最適なデジタルソリューションを提供することで、企業が持続的な成長とイノベーションを達成できるようサポートします。
オンライン講座
製造業、主に購買・調達部門にお勤めの方々に向けた情報を配信しております。
新任の方やベテランの方、管理職を対象とした幅広いコンテンツをご用意しております。
お問い合わせ
コストダウンが利益に直結する術だと理解していても、なかなか前に進めることができない状況。そんな時は、newjiのコストダウン自動化機能で大きく利益貢献しよう!
(Β版非公開)