- お役立ち記事
- Comprehensive Explanation of the Assembly Process for Industrial Robots
Comprehensive Explanation of the Assembly Process for Industrial Robots
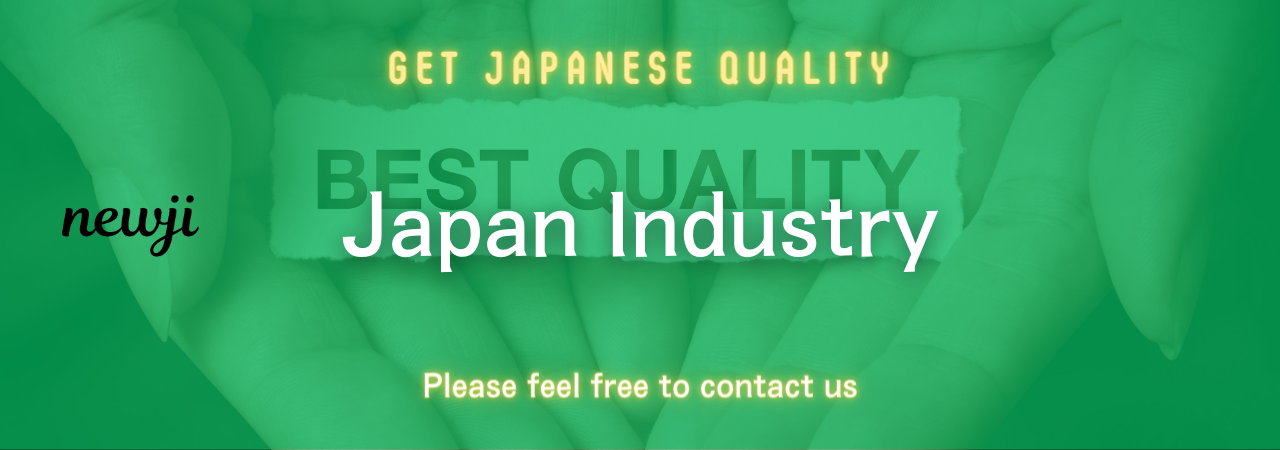
Industrial robots are fascinating machines that can perform a variety of tasks with precision and efficiency.
Understanding how these complex devices are assembled can give us deeper insight into modern manufacturing and engineering.
Let’s take a detailed look at the assembly process for industrial robots.
目次
Planning and Design
The assembly process begins with meticulous planning and design.
Engineers and designers come together to create blueprints and schematics for the robot.
They consider the robot’s intended functions and the environment in which it will operate.
Cutting-edge software tools are employed to model each component in three dimensions.
This virtual prototype allows for optimization of the robot’s design before any physical materials are cut or molded.
Selection of Materials
Once the design is finalized, the next step involves selecting the appropriate materials.
The choice of materials is crucial, as it affects the robot’s performance, durability, and cost.
Common materials include high-strength steel, aluminum alloys, and advanced plastics.
Each material is chosen based on its strength, weight, and resistance to environmental factors like heat and corrosion.
Manufacturing Components
With the design and materials decided, the manufacturing of individual components begins.
Machining Metal Parts
Metal components are crafted using precision machining techniques.
Computer Numerical Control (CNC) machines cut, shape, and drill metal parts to exact specifications.
These machines operate with incredible accuracy, ensuring that each piece fits perfectly with the others.
Molding Plastic Components
Plastic parts are produced through injection molding or 3D printing.
In injection molding, molten plastic is injected into a mold to create the desired shape.
3D printing, on the other hand, builds the part layer by layer from a digital model.
Both methods allow for the creation of complex shapes that would be difficult or impossible to achieve through traditional machining.
Assembly of Subcomponents
Once all individual parts are manufactured, they need to be assembled into larger subcomponents.
This step often involves both manual labor and automated systems.
Base Unit Assembly
The base unit is typically the first subcomponent to be assembled.
It includes the robot’s structural foundation and housing for primary systems.
Workers or machines attach the motor, gears, and initial wiring to the base.
This foundation will later support the other robotic elements.
Joint and Arm Assembly
Next, the joints and arms are assembled.
Industrial robots usually have multiple joints that allow for flexible movements.
Each joint is carefully constructed with bearings, motors, and encoders that provide rotational movement.
The arms, which may be made from lightweight yet strong materials like carbon fiber, are then connected to these joints.
Integration of Electronics
No industrial robot can function without a sophisticated electronic system.
The integration of electronics involves installing controllers, sensors, and wiring.
Control System Installation
The control system is essentially the brain of the robot.
It is responsible for receiving instructions, processing data, and sending commands to various parts of the robot.
The control unit is usually housed within the base or another protected area.
Technicians ensure that all connections are secure, and the system is programmed correctly for the robot’s tasks.
Sensor Implementation
Sensors are vital for the robot’s interaction with its environment.
Different types of sensors are installed depending on the robot’s function.
For example, proximity sensors help the robot avoid obstacles, while force sensors enable it to apply the right amount of pressure when gripping objects.
The integration of these sensors allows the robot to perform tasks with accuracy and safety.
Wiring and Cabling
All components need to be interconnected with wiring and cabling.
This step requires precision to ensure reliable communication between parts.
Technicians route wires through channels to protect them from damage and interference.
Special attention is given to cable management, making sure that the wires do not impede the robot’s movements.
Final Assembly and Testing
With subcomponents and electronics assembled, the final assembly and rigorous testing phase begin.
Robot Configuration
During the final assembly, all subcomponents are brought together.
The base, joints, arms, and electronic systems are connected into a single, cohesive unit.
Technicians calibrate the robot, ensuring that all parts are aligned and functioning as intended.
Performance Testing
Testing is a critical part of the assembly process.
The robot undergoes a series of tests to confirm that it performs its intended tasks correctly.
These tests might include motion accuracy checks, speed trials, and response time assessments.
Any issues identified are addressed promptly, and adjustments are made to fine-tune the robot’s performance.
Quality Assurance
In addition to performance tests, quality assurance checks are conducted.
These checks ensure that all components meet industry standards and regulations.
Inspectors look for any defects or deviations from the design specifications.
Only robots that pass these stringent quality checks are approved for deployment.
Conclusion
The assembly process for industrial robots is a complex and highly coordinated effort.
It involves precise planning, advanced manufacturing techniques, skilled labor, and thorough testing.
Understanding this process highlights the incredible engineering and craftsmanship that go into creating these versatile and powerful machines.
Whether for manufacturing, healthcare, or other industries, industrial robots continue to revolutionize the way we work and live.
資料ダウンロード
QCD調達購買管理クラウド「newji」は、調達購買部門で必要なQCD管理全てを備えた、現場特化型兼クラウド型の今世紀最高の購買管理システムとなります。
ユーザー登録
調達購買業務の効率化だけでなく、システムを導入することで、コスト削減や製品・資材のステータス可視化のほか、属人化していた購買情報の共有化による内部不正防止や統制にも役立ちます。
NEWJI DX
製造業に特化したデジタルトランスフォーメーション(DX)の実現を目指す請負開発型のコンサルティングサービスです。AI、iPaaS、および先端の技術を駆使して、製造プロセスの効率化、業務効率化、チームワーク強化、コスト削減、品質向上を実現します。このサービスは、製造業の課題を深く理解し、それに対する最適なデジタルソリューションを提供することで、企業が持続的な成長とイノベーションを達成できるようサポートします。
オンライン講座
製造業、主に購買・調達部門にお勤めの方々に向けた情報を配信しております。
新任の方やベテランの方、管理職を対象とした幅広いコンテンツをご用意しております。
お問い合わせ
コストダウンが利益に直結する術だと理解していても、なかなか前に進めることができない状況。そんな時は、newjiのコストダウン自動化機能で大きく利益貢献しよう!
(Β版非公開)