- お役立ち記事
- Manufacturing Process of Electric Whistles and Improving Volume Control Functionality
Manufacturing Process of Electric Whistles and Improving Volume Control Functionality
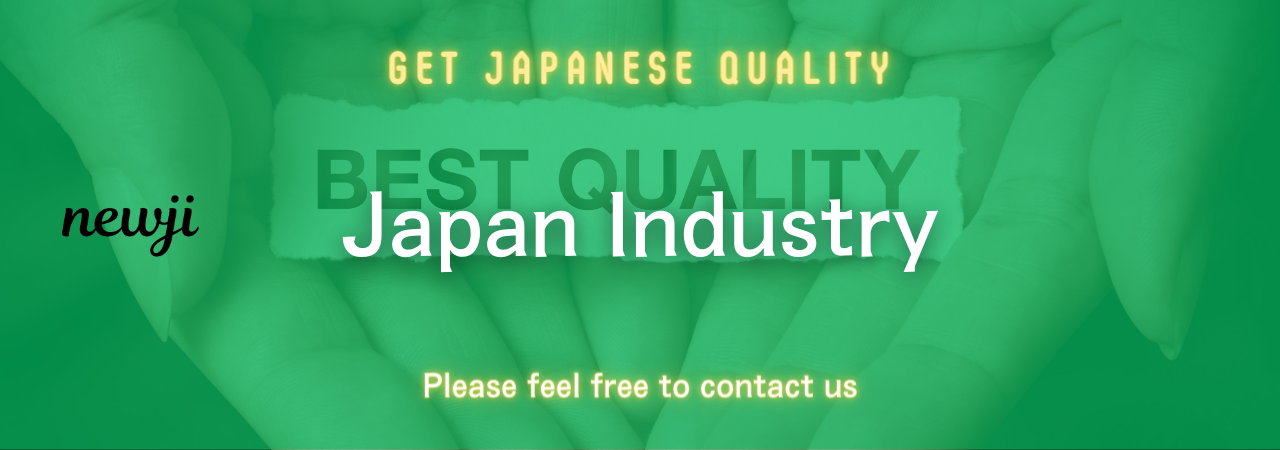
Electric whistles have become vital tools in various fields, serving as indispensable devices for referees, coaches, and trainers, among others.
Traditionally, whistles relied on manual blowing, but technological advancements have ushered in the era of electric whistles, which offer numerous benefits including hygiene and consistency in sound.
In this article, we will walk you through the manufacturing process of electric whistles and explore the innovative approaches to improving their volume control functionality.
目次
Understanding the Basics of Electric Whistles
Unlike traditional whistles, electric whistles generate sound electronically.
They typically consist of a small, battery-powered device that, when activated, produces a high-pitched noise similar to that of a traditional whistle.
The main components of an electric whistle include the casing, speaker, circuitry, and power source.
With the basics out of the way, let’s dive deeper into how these devices are made.
The Manufacturing Process
Step 1: Design and Prototyping
The manufacturing journey begins with the design and prototyping phase.
Engineers and designers collaborate to create a 3D model of the electric whistle.
In this stage, considerations such as size, shape, and ergonomic factors are assessed.
Special attention is given to ensure the design facilitates ease of use while maintaining practicality.
Once a satisfactory design is achieved, a prototype is developed using 3D printing or other rapid prototyping methods.
Step 2: Selection of Materials
Choosing the right materials is crucial for durability and performance.
The outer casing of the electric whistle is generally made from high-quality, impact-resistant plastic or aluminum.
The internal components, including the speaker and circuitry, require materials that can withstand repeated use and environmental factors.
Experts carefully select these materials to ensure the final product meets rigorous quality standards.
Step 3: Assembly of Internal Components
The assembly process begins with the production of small-scale electronic circuit boards.
Microprocessors, capacitors, resistors, and other necessary components are soldered onto these boards.
These circuits control the sound generation and volume of the whistle.
Next, the miniature speaker, which will produce the whistle’s sound, is attached.
The power source, usually a small lithium-ion or alkaline battery, is then connected to the circuitry.
Step 4: Casing Assembly
Once the internal components are assembled, they are encapsulated within the outer casing.
This casing is often designed to be water-resistant and durable, ensuring the whistle can function under various conditions.
Manufacturers use precision moulds to create uniform casing units, which are then inspected for defects before encapsulating the internal components.
The final assembly step involves securing the casing with screws or snap-fits to ensure robustness.
Step 5: Quality Control and Testing
Quality control is paramount to ensuring the final product meets expected standards.
Each assembled electric whistle undergoes a series of stringent tests, including sound output, battery life, and durability tests.
Some manufacturers also perform drop tests to ensure the device can withstand everyday wear and tear.
Any unit failing these tests is either reworked or discarded to maintain high-quality output.
Improving Volume Control Functionality
One of the most critical aspects of electric whistles is their volume control functionality.
Users often need the ability to adjust the sound level to suit different environments and purposes.
This section explores the technological innovations aimed at enhancing volume control.
Incorporating Multi-Level Volume Settings
One effective method to improve volume control is incorporating multi-level volume settings.
By equipping electric whistles with selectable volume levels, users can easily switch between low, medium, and high sound outputs.
Advanced circuit designs enable this functionality, often allowing for smooth transitions between volume levels without affecting sound quality.
Using Digital Signal Processing (DSP)
Digital Signal Processing (DSP) is another cutting-edge technology that has revolutionized volume control in electronic devices.
By integrating DSP chips into electric whistles, manufacturers can offer users precise control over sound output.
DSP enhances the clarity and consistency of the whistle’s sound, even at lower volume levels, by digitally manipulating the signal.
This ensures the whistle performs optimally in varied environments, from quiet indoor settings to noisy sports arenas.
Application of Feedback Systems
Feedback systems can significantly improve volume control by continuously monitoring the sound output and making real-time adjustments.
Such systems employ microphones and sensors to gauge the environmental noise level and adjust the whistle’s volume accordingly.
This automated approach ensures the whistle maintains optimum volume, enhancing user efficiency and reducing the need for manual adjustments.
Innovating Power Management Systems
Effective power management plays a crucial role in sustaining volume control.
Innovative battery management systems can optimize power usage, ensuring consistent volume output over prolonged periods.
Some electric whistles now come with rechargeable batteries and low-power alert features, significantly enhancing the user experience by ensuring the device remains reliably operational.
The Future of Electric Whistles
As technology continues to evolve, the future of electric whistles looks promising.
Emerging trends such as Bluetooth connectivity and smart integration could bring about new functionalities.
Imagine a whistle that connects wirelessly to your smartphone or smartwatch, allowing you to track usage, adjust settings, or even use voice commands.
Another exciting development is the potential integration of Artificial Intelligence (AI) to offer adaptive sound control based on real-time data analysis.
The possibilities are endless, and these innovations would redefine the user experience, making electric whistles even more indispensable.
The manufacturing process of electric whistles is both intricate and fascinating, showcasing the seamless integration of design and technology.
From selecting the right materials to implementing advanced volume control mechanisms, every step is crucial to producing a high-quality, reliable device.
As we look to the future, ongoing advancements promise to make electric whistles even more versatile and user-friendly.
These developments ensure that electric whistles will continue to be a valuable tool across multiple fields, enhancing both functionality and user experience.
資料ダウンロード
QCD調達購買管理クラウド「newji」は、調達購買部門で必要なQCD管理全てを備えた、現場特化型兼クラウド型の今世紀最高の購買管理システムとなります。
ユーザー登録
調達購買業務の効率化だけでなく、システムを導入することで、コスト削減や製品・資材のステータス可視化のほか、属人化していた購買情報の共有化による内部不正防止や統制にも役立ちます。
NEWJI DX
製造業に特化したデジタルトランスフォーメーション(DX)の実現を目指す請負開発型のコンサルティングサービスです。AI、iPaaS、および先端の技術を駆使して、製造プロセスの効率化、業務効率化、チームワーク強化、コスト削減、品質向上を実現します。このサービスは、製造業の課題を深く理解し、それに対する最適なデジタルソリューションを提供することで、企業が持続的な成長とイノベーションを達成できるようサポートします。
オンライン講座
製造業、主に購買・調達部門にお勤めの方々に向けた情報を配信しております。
新任の方やベテランの方、管理職を対象とした幅広いコンテンツをご用意しております。
お問い合わせ
コストダウンが利益に直結する術だと理解していても、なかなか前に進めることができない状況。そんな時は、newjiのコストダウン自動化機能で大きく利益貢献しよう!
(Β版非公開)