- お役立ち記事
- 製造業DX成功の鍵:FMEAによるリスク管理とプロセス最適化
製造業DX成功の鍵:FMEAによるリスク管理とプロセス最適化
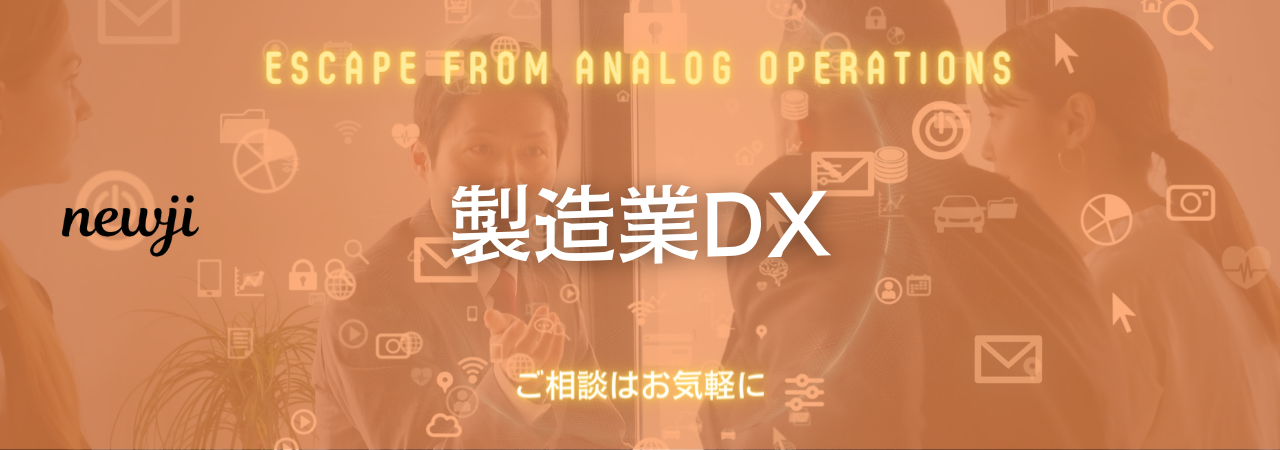
目次
はじめに
製造業は、近年のデジタル化の波により、大きな変革を迎えています。
ディジタル・トランスフォーメーション(DX)は、生産効率の向上、コスト削減、品質改善など、多岐にわたるメリットをもたらします。
その中でも、FMEA(Failure Mode and Effects Analysis:故障モード影響解析)は、リスク管理とプロセス最適化の重要な手段となっています。
この記事では、FMEAの基本原理から具体的な手法、実践的な事例や最新技術動向までを詳しく解説します。
FMEAとは?
FMEAの基本概念
FMEAは、製品やプロセスの設計段階で潜在的な故障モードを特定し、それが発生する原因と影響を分析する手法です。
このアプローチにより、潜在的な問題を事前に予測し、対策を講じることが可能です。
FMEAは将来の問題発生を予測し、未然に防ぐことで、品質の向上とコスト削減に寄与します。
FMEAの種類
FMEAにはいくつかのタイプがあります。
– デザインFMEA(DFMEA):製品設計段階でのリスク管理
– プロセスFMEA(PFMEA):生産プロセスのリスク管理
どちらも重要ですが、特に製造業ではDFMEAとPFMEAの両方を組み合わせたアプローチが効果的です。
FMEAの実施方法
ステップ1:チームの編成
FMEAを成功させるためには、多様な部門から専門家を集めたチームを編成することが重要です。
設計、品質管理、製造、生産管理などの部門から適切なメンバーを選びます。
ステップ2:システムの理解
対象となるシステムやプロセスを詳しく理解し、全体像を把握します。
これは、詳細な分析を行うための基礎となります。
ステップ3:故障モードの特定
各部品やプロセスステップごとに、どのような故障が発生しうるかを洗い出します。
この段階で、できる限り多くの故障モードを特定することが重要です。
ステップ4:影響の評価
特定した故障モードが実際に発生した場合、その影響を評価します。
これには、安全性、機能性、コストなどが含まれます。
ステップ5:発生原因の分析
故障モードが発生する原因を徹底的に分析します。
この作業により、発生頻度を低減させるための具体的な対策が明確になります。
ステップ6:優先順位の設定
リスクの大きさに基づき、優先順位を設定します。
ここでは、RPN(Risk Priority Number:リスク優先度数)を用いることが一般的です。
RPNは、発生の可能性、故障の影響度、発見の難易度の3つの要素を掛け合わせて算出されます。
ステップ7:対策の立案と実施
優先順位に基づき、具体的な対策を立案し、実施します。
この段階では、定期的な見直しとフィードバックが重要です。
FMEA導入のメリットとデメリット
メリット
– **リスクの事前把握**:潜在的な問題を事前に特定し、対策を講じることで、製品やプロセスの安定性が向上します。
– **コスト削減**:問題発生後の修正やリコールを減少させることで、コスト削減が可能です。
– **品質向上**:品質管理の徹底により、製品の信頼性が高まります。
– **チームワークの強化**:多部門からの専門家が参加することで、チームワークが向上します。
デメリット
– **コストと時間のコスト**:FMEAの実施には多くのリソースが必要であり、初期段階ではコストと時間がかかります。
– **依存性**:FMEAが完璧でない場合、過信すると他のリスク管理手法を軽視しがちです。
最新の技術動向
AIと機械学習の活用
AIと機械学習を活用したFMEAの自動化が進んでいます。
これにより、大量のデータを迅速に分析し、潜在的なリスクをより正確に予測することが可能です。
IoTデバイスの導入
IoTデバイスを用いたリアルタイムモニタリングは、FMEAの精度をさらに高めます。
センサーから集められるデータを活用し、早期に異常を検知することができます。
クラウドベースのFMEAツール
クラウドベースのFMEAツールは、多拠点での共同作業やデータの一元管理を実現します。
これにより、グローバルなFMEA実施が容易になります。
実践的な事例
自動車産業での成功事例
自動車産業では、FMEAを駆使して多数の部品やシステムのリスク管理を行っています。
例えば、ある自動車メーカーでは、新しいエンジン設計においてFMEAを行い、リスクを大幅に減少させました。
この取り組みにより、製品リコールの削減と品質の向上が達成されています。
エレクトロニクス産業での成功事例
エレクトロニクス産業でも、FMEAは広く導入されています。
ある企業では、新型スマートフォンのプロセスFMEAを実施し、製造段階での故障原因を特定しました。
これにより、製品の信頼性を向上させるとともに、製造コストの削減にも成功しています。
まとめ
FMEAは、製造業のリスク管理とプロセス最適化に欠かせない手法です。
その効果的な実施には、多部門からの専門家の協力と、詳細な分析が必要です。
また、最新の技術を活用することで、より高い精度と効率を実現できます。
組織が持つ潜在的な課題に対して積極的に取り組むことで、製品の品質向上やコスト削減が可能となり、競争力の向上に繋がります。
製造業DXの成功を目指すためには、FMEAの適切な導入と活用が鍵となります。
資料ダウンロード
QCD調達購買管理クラウド「newji」は、調達購買部門で必要なQCD管理全てを備えた、現場特化型兼クラウド型の今世紀最高の購買管理システムとなります。
ユーザー登録
調達購買業務の効率化だけでなく、システムを導入することで、コスト削減や製品・資材のステータス可視化のほか、属人化していた購買情報の共有化による内部不正防止や統制にも役立ちます。
NEWJI DX
製造業に特化したデジタルトランスフォーメーション(DX)の実現を目指す請負開発型のコンサルティングサービスです。AI、iPaaS、および先端の技術を駆使して、製造プロセスの効率化、業務効率化、チームワーク強化、コスト削減、品質向上を実現します。このサービスは、製造業の課題を深く理解し、それに対する最適なデジタルソリューションを提供することで、企業が持続的な成長とイノベーションを達成できるようサポートします。
オンライン講座
製造業、主に購買・調達部門にお勤めの方々に向けた情報を配信しております。
新任の方やベテランの方、管理職を対象とした幅広いコンテンツをご用意しております。
お問い合わせ
コストダウンが利益に直結する術だと理解していても、なかなか前に進めることができない状況。そんな時は、newjiのコストダウン自動化機能で大きく利益貢献しよう!
(Β版非公開)